Performance Analysis of New One-Piece Iron Roughneck and Its Spinning Mechanism
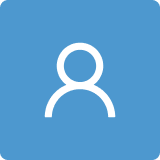
Round 1
Reviewer 1 Report
Comments and Suggestions for AuthorsDear Authors,
The article submitted for review is interesting and extensive. The designed device is described. Basic design calculations and simplified vibration simulations are performed. The article states that innovative design solutions are proposed, increasing this work's value. However, I have a few comments, which I include below.
1. The title of chapter 1 should be written in capital letters.
2. The article lacks references to patent descriptions. I propose expanding Chapter 1 to include references to patent descriptions concerning the issues presented in the article and citing these patents in the article. Several patents belong to geological drilling companies with extensive experience in this area.
3. Was the design solution described in the article the subject of a patent? If so, this should be written about and cited in the references.
4. Was the device shown in Figure 1 made, for example, as a prototype? If it was made, it is worth showing a photo of it.
5. Formula (2) – line 239 – does not contribute anything to the article's content, because the angle q is not analyzed as a variable in the further part of the article.
6. Line 243 - should be "Nm" instead of N.m". Please explain on what basis the value T = 2400 Nm was adopted. Why was this value adopted and not another?
7. Formula (4) – line 244 – there is no need to specify the force value with an accuracy of 0.01 N. With such large forces, it does not matter. A description with an accuracy of one N is sufficient.
8. Line 265 – Instead of "elastomer" it is better to write "elastic". It's about a model of a perfectly elastic body.
9. Caption under Figure 11: instead of "elastomer" it is better to write "elastic".
10. Line 295 – it says "Posinesque solution". I think it means "Boussinesq solution".
11. Line 298 – the words “elastomers” were used. Elastomers are polymers that are classified as viscoelastic bodies. In this case, the use of Hertz’s formulas would be questionable. The spinning buckle roller would be made of metal, so it would be better to use the phrase “elastic element” or "elastic elements"
12. Line 305 – please provide literature reference.
13. Figures 17 ÷ 21 - Please enlarge the font in these figures (if possible), because after printing the text is difficult to read.
14. The simulation results indicate the occurrence of large vibrations. Large amplitudes of force values ​​in a short time. This was not written about in the conclusions. This may result from the adopted overly simplified vibration model. Perhaps a different conclusion should be drawn and damping elements should be used in the structure.
Best Regards,
Reviewer.
Author Response
Please see the attachment.
Author Response File: Author Response.pdf
Reviewer 2 Report
Comments and Suggestions for AuthorsThe manuscript with the title “Performance analysis of new one-piece iron roughneck and its spinning mechanism” presents the design and performance analysis of an integrated iron roughneck, focusing on its clamp body structure and spinning mechanism. It investigates the working characteristics and structural form of the spin buckle roller through theoretical and simulation studies, including contact and rolling friction theories. The study validates the theoretical findings and the design's effectiveness through a dynamics simulation, confirming the performance and structure rationality of the spin buckle mechanism. The topic is important and relevant.
However, the manuscript also has some limitations and weaknesses that need to be addressed and improved. Here are some specific recommendations and suggestions for each section of the manuscript:
Introduction
1. The authors need to expand the introduction section by including a more detailed review of the relevant literature. This will help establish the context and justify the research.
2. The authors did not identify a research gap, based on sufficient and relevant literature in their introduction section to justify the purpose and significance of their research. Including key references and explicitly stating the research gap would enhance its comprehensiveness.
Structural design and theoretical analysis
3. The caption for Figure 1 is missing the respective number for the first component “column; 2. clamp body; 3. base; 4. extension mechanism.”.
4. The simulation methods subsection lacks a detailed description and does not mention the specific software used. The authors should provide a detailed description of the simulation methods, including the software and tools used.
5. The authors should include a section or subsection with a description of the methods used to validate the simulation results.
The manuscript needs major revision before it can be considered for publication. The authors need to address all the recommendations and suggestions mentioned above to improve their manuscript.
Author Response
Please see the attachment.
Author Response File: Author Response.pdf
Reviewer 3 Report
Comments and Suggestions for Authors1. The proposed floating mechanism focuses on reducing friction through the axial movement of the spin buckle roller. However, it may not adequately account for variations in load or impact that occur in real drilling environments. There may be a lack of comprehensive validation under diverse actual working conditions.
2.The results obtained from ADAMS software simulations may not directly translate to real-world performance. Simulations are based on ideal conditions, which might not fully reflect the unexpected variables and issues that can arise in actual operational environments.
3.The new integrated clamp body structure and the double hydraulic cylinder parallel clamping structure may enhance performance but also increase overall structural complexity. This added complexity can lead to higher maintenance costs and potential maintenance issues, which might not have been fully considered.
4.While the wear and durability of the spin buckle roller have been theoretically analyzed and simulated, the actual long-term durability under continuous use might not be fully addressed. Additional wear tests and material selection considerations are needed to ensure the rollers perform well over extended periods.
5.The improved performance of the proposed iron roughneck system is positive, but there is a lack of discussion on cost-effectiveness. It is important to analyze how the new design compares to existing systems in terms of cost efficiency, including initial investment and maintenance costs.
Author Response
Please see the attachment.
Author Response File: Author Response.pdf
Round 2
Reviewer 1 Report
Comments and Suggestions for AuthorsDear Authors,
Thank you for reading my comments and making corrections. I will be recommending this article for publication.
Kind Regards
Reviewer
Reviewer 2 Report
Comments and Suggestions for AuthorsI recommend the article be published in its present form.