Kinetic Analysis of Isothermal and Non-Isothermal Reduction of Iron Ore Fines in Hydrogen Atmosphere
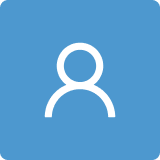
Round 1
Reviewer 1 Report
Authors performed detailed kinetics study of the reduction of iron ore in hydrogen atmosphere in isothermal and non-isothermal conditions. Overall the results in the manuscript are practically important, the methods used are justified. The manuscript fully meets the aims and scope of the journal. I suggest to accept the manuscript for the publication after some minor revisions and clarifications are made:
1. In Table 1 authors presents chemical composition of the iron ore. What does "TFe" mean? What method was used to get chemical composition? Fig. 1 shows XRD pattern of the iron ore and only Fe2O3 is detected, so, what is the origin of other phases in table 1?
2. p. 8, 184-185 claims that dense iron layer hinders the diffusion of the reducing gas. Do you expect that hydrogen is diffused in the volume of the Fe, reacts with oxygen with the formation of water and water is diffused backwards toward the surface? Why don't you think that oxygen is diffused towards the surface due to the chemical potential difference between bulk and surface, where it reacts with hydrogen?
3. Fig.5a. What is the origin of peak at an initial stage at 950C? Can the reduction stages (Fe2O3 -> Fe3O4 -> FeO -> Fe) be identified based on these data?
4. Fig.5b. Authors have chosen the points of reaction rates at different temperatures. However, since these results were got from isothermal reduction data, it is not clear how these points were chosen? Please show them on fig.5a, if possible.
5. p. 9, 214-216 claims that at 1100C there is a "clear boundary" between metallic iron particles and slag. I can't see this boundary on the SEM figure. Can it be indicated with arrows?
6. p. 9, 223-224. Authors mentioned the results for CO reduction, however I could not find them in the manuscript.
Author Response
Please see the attachment.
Author Response File: Author Response.pdf
Reviewer 2 Report
The author needs to state how isothermal experiments are carried out and how it is different from non-isothermal experiments. In fact, all practical reactions are non-isothermal due to the existing temperature gradient in the object. The isothermal reaction may be considered a benchmark. However, it is important to state how such an isothermal condition is achieved.
Why are non-isothermal experiments carried out up to 1000oC while isothermal experiments are carried out up to 1100oC?
What was the heating rate of the furnace for isothermal experiments?
Author Response
Please see the attachment.
Author Response File: Author Response.pdf
Round 2
Reviewer 2 Report
One query still remains unanswered. Do the authors assume no temperature gradient in the body of mass? If so, it needs to be mentioned with justification. Otherwise, isothermal experiment is not truly isothermal.
Author Response
Please see the attachment.
Author Response File: Author Response.pdf