Electrical Discharge Machining of Al2O3 Using Copper Tape and TiO2 Powder-Mixed Water Medium
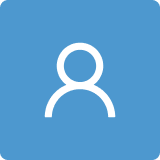
Round 1
Reviewer 1 Report
Summary of review No. technologies-2020817
Electrical Discharge Machining of Al2O3 using Copper-tape and TiO2 Powder-Mixed Water Medium
No. technologies-2020817
This paper investigated the machining characteristics of Al2O3 using assisting copper-tape and adding TiO2 powder into dielectric medium in wire electrical discharge machining (WEDM). The machining performance was evaluated by calculating the material removal rate with relation to the pulse frequency and TiO2 powder concentration. However, machining non-conductive materials with WEDM process is interesting and attracts industrial applications. The machining characteristics should be explored more comprehensive to establish a practice implementation.
After going through the above paper, my general comment and opinion is that the paper should be revised intensively to attain the required for publication in an archival journal.
The following is the list of detailed comments with respect to the paper:
l In Table 2, the reasons that did not explore the effects of discharge current on machining characteristics should be explained, since the current is important factor in WEDM.
l In Table 5, the reasons that authors did not use an identical (or narrow range) diameter TiO2 powder in WEDM process should be explained in the text.
l Figure 8 should be revised; it is difficult to realize the information with regard to Figure 8.
l In page 3, “…would acquire conductive properties (Figure 2d)”. Please check it carefully.
l Please check that the Reference No.87 has been cited in the text.
l In Conclusions Section, “.. increased electrical conductivity up to the level of conductive materials in the presence of heat (more than 1,000° C); semiconductive properties of the powder at normal temperatures (n-type with the band gap Eg = 3.0 eV for rutile”. It is not suitable revealed in Conclusions.
Author Response
Response to Reviewer 1 Comments
Dear reviewer,
Thank you so much for your kind evaluation of our work. We do agree with all your proposals and comments and have modified the manuscript according to them.
We hope that the manuscript will be suitable for publishing in Technologies and will attract many potential readers of the journal with your comments. The introduced corrections in the text of the manuscript are marked yellow.
Kind regards,
Authors.
Reviewer comments
Point 1: In Table 2, the reasons that did not explore the effects of discharge current on machining characteristics should be explained, since the current is important factor in WEDM.
Response 1: Thank you for pointing it out. This is a fair remark. The influence of the current and voltage has been known in electrical discharge machining for decades, and we have researched it in the previously published works for a wide range of materials in correlation with other factors and purposes of the study [1-6]. The main dependence is shown in [3] (more understandably shown in the attached file).
As can be seen, voltage and operational current are in inverse proportion. The previously conducted work with alumina showed that the optimal value of the operational current is 15 A. During the study, it was decided to concentrate research more on EDM factors such as pulse frequency and concentration of the powder in the fluid to make it more straightforward for readers who have experience with EDM and understand the dependencies between the main factors. However, we agree that we should have mentioned it in the text of the manuscript the relevant passage is added:
“The previously conducted work with alumina showed that the optimal value of the operational current is 15 A. During the study, it was decided to limit the research area to EDM factors such as pulse frequency, and concentration of the powder in the fluid to make it more straightforward since the main correlation between current, operational voltage and character of the obtained wells on the surface or material removal rate is known and understandable [86]."
References
- Grigoriev, S.N.; Volosova, M.A.; Okunkova, A.A.; Fedorov, S.V.; Hamdy, K.; Podrabinnik, P.A. Sub-Microstructure of Surface and Subsurface Layers after Electrical Discharge Machining Structural Materials in Water. Metals2021, 11, 1040.
- Grigoriev, S.N.; Volosova, M.A.; Okunkova, A.A.; Fedorov, S.V.; Hamdy, K.; Podrabinnik, P.A. Elemental and Thermochemical Analyses of Materials after Electrical Discharge Machining in Water: Focus on Ni and Zn. Materials2021, 14, 3189.
- Grigoriev, S.N.; Volosova, M.A.; Okunkova, A.A.; Fedorov, S.V.; Hamdy, K.; Podrabinnik, P.A.; Pivkin, P.M.; Kozochkin, M.P.; Porvatov, A.N. Wire Tool Electrode Behavior and Wear under Discharge Pulses. Technologies2020, 8, 49.
- Grigoriev, S.N.; Volosova, M.A.; Okunkova, A.A.; Fedorov, S.V.; Hamdy, K.; Podrabinnik, P.A.; Pivkin, P.M.; Kozochkin, M.P.; Porvatov, A.N. Electrical Discharge Machining of Oxide Nanocomposite: Nanomodification of Surface and Subsurface Layers. Manuf. Mater. Process. 2020, 4, 96.
- Grigoriev, S.N.; Kozochkin, M.P.; Porvatov, A.N.; Volosova, M.A.; Okunkova, A.A. Electrical discharge machining of ceramic nanocomposites: Sublimation phenomena and adaptive control. Heliyon 2019, 5, e02629.
- Melnik, A.; Kozochkin, M.P.; Porvatov, A.N.; Okunkova, A.A. On adaptive control for electrical discharge machining using vibroacoustic emission. Technologies 2018, 6, 96.
Point 2: In Table 5, the reasons that authors did not use an identical (or narrow range) diameter TiO2 powder in WEDM process should be explained in the text.
Response 2: Thank you for pointing it out. It was mentioned at the end of subsection 2.3 (marked yellow in the text, page 8):
“It should be noted that the smallest size of suspended particles led to the highest rate of volumetric material removal and the lowest wear of the primary tool electrode [88-92].”
However, we have added also a relevant sentence about sieving stage that was not mentioned before:
“Initial TiOâ‚‚ powder was sifted using an analytical sieving machine AS200 basic (Retsch, Dusseldorf, Germany) with a test sieve (10 µm by ISO 3310-1).”
Another reason for using 10 µm granules is the narrow range of the discharge gap: for the conductive materials, it is about 170-200 µm [2,3]; for materials with the threshold conductivity, it is 48-50 µm [4,5]. In this case, the electrical conductivity and the discharge gap are in direct proportion [1]. The relevant passage is added.
Point 3: Figure 8 should be revised; it is difficult to realize the information with regard to Figure 8.
Response 3: Thank you, we agree that Figure 8 looks superfluous. Table 7 duplicates the data on formed kerfs in a more understandable form. The figure was removed.
Point 4: In page 3, “…would acquire conductive properties (Figure 2d)”. Please check it carefully.
Response 4: Thank you for this remark. It is revised in the text.
Point 5: Please check that the Reference No.87 has been cited in the text.
Response 5: Thank you; it is corrected in the text.
Point 6: In Conclusions Section, “.. increased electrical conductivity up to the level of conductive materials in the presence of heat (more than 1,000° C); semiconductive properties of the powder at normal temperatures (n-type with the band gap Eg = 3.0 eV for rutile”. It is not suitable revealed in Conclusions.
Response 6: Thank you; it is corrected in the conclusions.
Author Response File: Author Response.pdf
Reviewer 2 Report
The work has great scientific potential. Many different studies by other authors are cited. Nevertheless, the vast majority of them concern Russian research and possibly Far East researchers. It misses research from the European area as well as from America. Moreover, often authors do not use subscripts in formulas, but only a smaller font. The drawings are legible, the analysis of the literature is thorough. The study was carried out in a proper way, the results were discussed correctly and supported by research. The article has been written very carefully, in accordance with the art of writing scientific articles. Authors should use bigger space between text and figures or tables (e.g. table 1, table 2 etc.). In general, the article presents in a collective manner many results also of other authors, constituting a valuable source of information related to this EDM method.
Author Response
Reviewer comments
Dear reviewer,
Thank you so much for your kind evaluation of our work. We agree with all your proposals and comments and have modified the manuscript accordingly.
We hope the manuscript will be suitable for publishing in Technologies and attract many potential journal readers with your comments. The introduced corrections in the text of the manuscript are marked green.
Kind regards,
Authors.
Reviewer comments
Point 1: The work has great scientific potential. Many different studies by other authors are cited. Nevertheless, the vast majority of them concern Russian research and possibly Far East researchers. It misses research from the European area as well as from America.
Response 1: Thank you for pointing it out. This is a fair remark. We agree that only a few research groups have advanced in this research domain. Most of them are concentrated in the East. After the first proposal of the electroerosive method for dielectric materials by a group of Soviet authors [1], it was developed by researchers from Japan for two decades [2-4]. There are known research groups from Austria [5], Malaysia [6], Turkey [7], at least 4 groups in China [8-10], two groups in Russia (Moscow, MSUT Stankin, and Perm [11]), and recently from Kazakhstan [12]. Even fewer researchers are working with alumina. Most of the published papers do not have systematic character and can be characterized as episodes probably related to the works in the frames of the relevant grants. We would honestly add that many publications from the countries of other regions known for their mechanical engineering productions, such as South Africa and Brazil, also remain insufficient.
We have added a few works from other countries to satisfy the reviewer.
- Lukashenko, S.V.; Kovtun, A.V.; Dashuk, P.N.; Sokolov, B.N. The Method of Electrical Discharge Machining of Dielectrics. Patent 1,542,715, 10 December 1986.
- Mohri, N. EDM of Advanced Ceramics - From Finish Machining to Machining Insulating Ceramics. VDI Berichte 1996 (1276), 289-296.
- Muttamara, A., Fukuzawa, Y., Mohri, N., Tani, T. Effects of structural orientation on EDM properties of sapphire. Materials Transactions 2004, 45(7), 2486-2488.
- Hanaoka, D.; Fukuzawa, Y.; Yamashita, K. Research of large-area electrical discharge machining for insulating Si3N4 ceramics with the assisting electrode method. Advanced Materials Research 2014, 939, 76-83.
- Schubert, ; Zeidler, H.; Kühn, R.; Hackert-Oschätzchen, M.; Flemmig, S.; Treffkorn, N. Investigation of Ablation Behaviour in Micro-EDM of Nonconductive Ceramic Composites ATZ and Si₃Nâ‚„-TiN. Proc. CIRP 2016, 42, 727–732.
- Moudood, M.A.; Sabur, A.; Ali, M.Y.; Jaafar, I.H. Effect of Peak Current on Material Removal Rate for Electrical Discharge Machining of Non-Conductive Al2O3 Adv. Mater. Res. 2014, 845, 730–734.
- Kucukturk, G.; Cogun, C. A New Method for Machining of Electrically Nonconductive Workpieces Using Electric Discharge Machining Technique. Sci. Technol. 2010, 14, 189–207.
- Liu, Y.H.; Li, X.P.; Ji, R.J.; Yu, L. L.; Zhang, H.F.; Li, Q.Y. Effect of technological parameter on the process performance for electric discharge milling of insulating Alâ‚‚O₃ ceramic. Mater. Process. Technol. 2008, 208, 245–250.
- Lin, Y.-J.; Lin, Y.-C.; Wang, A.-C.; Wang, D.A.; Chow, H.M. Machining characteristics of EDM for non-conductive ceramics using adherent copper foils. In Advanced Materials Research, Materials Processing Technologies, Proceedings of the International Conference on Advances in Materials and Manufacturing Processes, Shenzhen, China, 6–8 November 2010; Jiang, Z.Y., Liu, X.H., Bu, J.L., Eds.; Trans Tech Publications Ltd.: Durnten-Zurich, Switzerland, 2010; doi:10.4028/www.scientific.net/AMR.154-155.794.
- Li, X.; Liu, Y.; Yu, L.; Ji, R. Effects of electrical parameters on electrical discharge grinding of non-conductive engineering ceramics. IET Conference Publications 2006, (524), 1306-1309.
- Ablyaz, T.R.; Shlykov, E.S.; Muratov, K.R. The Use of Electrode Tools Obtained by Selective Laser Melting to Create Textured Surfaces. Materials2022, 15, 4885.
- Rashid, A.; Bilal, A.; Liu, C.; Jahan, M.P.; Talamona, D.; Perveen, A. Effect of Conductive Coatings on Micro-Electro-Discharge Machinability of Aluminum Nitride Ceramic Using On-Machine-Fabricated Microelectrodes. Materials 2019, 12, 3316.
Point 2: Moreover, often authors do not use subscripts in formulas, but only a smaller font.
Response 2: Thank you for your comment. We have used the standard low-indexing tools in Word:
- (Ctrl+=) – uses a standard symbol in low index Al2O3 => Al2O3, which we have used in the title; it does not look natural but helps in search engine
and
- (Alt+X) – introduces a special symbol in a low index, Alâ‚‚O₃, looks better but does not help in the search engine as a separate symbol
We have tried to keep the standard symbol (Ctrl+=) in the title and the special symbol (Alt+X) in the manuscript's text. Another option is to replace Al2O3 in the title with “alumina”.
We would be happy to revise it as the reviewer wish if it’s critical for a visual impression.
Point 3: The drawings are legible, the analysis of the literature is thorough. The study was carried out in a proper way, the results were discussed correctly and supported by research. The article has been written very carefully, in accordance with the art of writing scientific articles. Authors should use bigger space between text and figures or tables (e.g. table 1, table 2 etc.). In general, the article presents in a collective manner many results also of other authors, constituting a valuable source of information related to this EDM method.
Response 3: Thank you so much for your kind comment and evaluation. We made the space between text, figures, and tables bigger.
Author Response File: Author Response.pdf