A Novel Robotic-Vision-Based Defect Inspection System for Bracket Weldments in a Cloud–Edge Coordination Environment
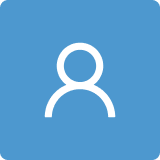
Round 1
Reviewer 1 Report
Line 17: Datasets with 3586 qualified images. Why do you limit the dataset size? Justify
Line 20 and 21: rewrite the statement.
Line 84 : First Letter of the full form should be capitalized. CMOS/LED/NMS/IoU
How you have decided epochs size?
Discussion on related work is so much limited. need to increase. Only ref 29 to 38 is discussed.
Detailed about IoT is missing.
A flow chart for the program is required in the proposed work.
How do you utilize cloud computing in the proposed work?
The capitalized first word in full form.
Need to improve the sequence of the verb in some sentences to convey your interpretation.
Author Response
Please see the attachment.
Author Response File: Author Response.docx
Reviewer 2 Report
Review comments:
The manuscript titled “A Novel Robotic Vision-based Defects Inspection System for Bracket Weldments in Cloud-edge Coordination Environment”, is the good attempt for automatic defect identification for the products under consideration.
The research address the questions of defect detection for Bracket Weldments in Cloud-edge during the production of items (automotive bracket parts). It is important topic and original.
The authors proposed the system under cloud-edge computing environment wherein edge devices are mainly composed of the Raspberry Pi-powered board and the edge gateway. To realize fast response of defects inspection, the Raspberry Pi-powered board is equipped with the computational resource as the edge server and connected to the CMOS industrial camera.
The authors should consider the fast identification of defects using Raspberry Pi. The main focus was for defect inspection and classification of brackets in the automobile, furthermore, different types of datasets can be tested.
The conclusions are consistent with the evidence and arguments presented and do they address the main question posed. The references are appropriate. Appropriate tables and figures are considered in this manuscript.
Author Response
Please see the attachment.
Author Response File: Author Response.docx
Reviewer 3 Report
In this paper, the framework of robotic vision-based defects inspection system is proposed and developed in the cloud-edge computing environment. In this way, the YOLOv5 object detection algorithm is used to inspect multi-scale defects in which a YOLO-SPD-Conv module is added to further retain discriminant information of small defects. Experimental results show that the system can achieve 98.6% efficiency in less than 1 second. However, before the paper is accepted, authors should consider the following questions.
1. Please explain why rotating the captured weld image by 180 degrees makes the final model more robust in terms of orientation.
2. Please give the parameter settings for Faster R-CNN+ResNet-50, SSD+ResNet-50 and YOLOv5s.
3. Please complete Figure 12. For example, the titles of the horizontal and vertical axes, etc.
4. Please analyze why the speed of the proposed algorithm in this paper is better than other algorithms.
5. The references can be further expanded to highlight the significance of this study. Such references can be added.
[1] title: Development of real-time vision-based fabric inspection system
[2] title: Neural network-based motion modeling and control of water-actuated soft robotic fish
[3] title: Automatic defect detection of metro tunnel surfaces using a vision-based inspection system
[4] title: Swimming modeling and performance optimization of a fish-inspired underwater vehicle (FIUV)
[5] title: Computer-vision-based fabric defect detection: A survey
[6] title: A review on recent advances in vision-based defect recognition towards industrial intelligence
Moderate editing of English language required
Author Response
Please see the attachment.
Author Response File: Author Response.docx
Round 2
Reviewer 3 Report
In this paper, the framework of robotic vision-based defects inspection system is proposed and developed in the cloud-edge computing environment. In this way, the YOLOv5 object detection algorithm is used to inspect multi-scale defects in which a YOLO-SPD-Conv module is added to further retain discriminant information of small defects. Experimental results show that the system can achieve 98.6% efficiency in less than 1 second. In this version, the authors have already replied all the questions I proposed before,but there is still one question:
1. Why are the start and end points of the data in Figure 12 different in the two manuscripts?
Moderate editing of English language required
Author Response
Please see the attachment.
Author Response File: Author Response.pdf