Numerical Simulation and Optimization of a Phase-Change Energy Storage Box in a Modular Mobile Thermal Energy Supply System
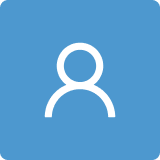
Round 1
Reviewer 1 Report
1. why triangular based elements have been selected for meshing?
2. In validation part, numerical results have been compared with [2]. Does all geometrical and operating conditions were same for the comparison?
3. Boundary conditions applied for the simulation should be mentioned properly.
4. Numerical scheme can be elaborated to give more information of the topic.
5. On what basis fin arrangements shown in table 2 selected ?
6. In figure 13, legends have been mentioned as conditions 1,2 and 3.? Instead of mentioning as conditions it is better to write them exactly what is that condition 1? Simikarly 2 and 3?
Quality of figures 13,14 and 15 needs improvement
minor editing is required
Author Response
- why triangular based elements have been selected for meshing?
Thank you for this question, Triangles are chosen as mesh cells due to their adaptation to complex surfaces and computational simplicity. It is stable to avoid singularities and easier to integrate with commonly used numerical methods.
- In validation part, numerical results have been compared with [2]. Does all geometrical and operating conditions were same for the comparison?
Thank you for this good question, the numerical results are compared using all the same geometric and operational conditions.
- Boundary conditions applied for the simulation should be mentioned properly.
Thank you for your good advice. After establishing the new heat accumulator model, the original heat transfer mechanism has not been changed, so the original mathematical model can still be used without any change. In addition, the calculation method and initial conditions are the same as the original model, but the boundary conditions are adjusted from the original 413K constant wall temperature to 453K constant wall temperature.
- Numerical scheme can be elaborated to give more information of the topic.
Thank you for the good advice you have given, and the text has been supplemented with a description of the numerical scheme.
- On what basis fin arrangements shown in table 2 selected ?
Thank you for your question, the fin arrangement was selected with reference to the fin arrangement in doi.org/10.1016/j.renene.2020.08.153.
- In figure 13, legends have been mentioned as conditions 1,2 and 3.? Instead of mentioning as conditions it is better to write them exactly what is that condition 1? Simikarly 2 and 3?
Thank you for your question, the specific parameters for working conditions 1, 2 and 3 are indicated in Table2.
The quality of figures 13, 14 and 15 has been upgraded.
Author Response File: Author Response.pdf
Reviewer 2 Report
This contribution deals about modeling of phase change materials to be used within modular and portable thermal energy storage systems. After showing and validating a shell-and-tube-like heat exchanger that includes the PCM, the authors simulates the modular configuration by considering fins too in order to improve the weak PCM thermal performances. Finally, the authors conclude that fins are able to improve the liquid phase rate of a 30%, and that expanded graphite cause a heat storage duration reduction, with an advance in terms of thermal performance.
The reviewer thinks that this is a really interesting contribution about modular thermal energy storage systems, that face the well-known problem of how to improve their poor thermal characteristics. It is then suggested to consider the present paper for publication after addressing the following points
· Mobile thermal energy storage systems are devices in which the weight might have an important role. Therefore, why didn't the authors analyzed this aspect? Why didn't they consider this constraints when running different simulations?
· The reviewer thinks that the introduction is fairly well-presented but some improvements are suggested, especially because latent thermal energy storage is one of the hottest topics nowadays in sustainable energy. For instance, the authors propose a particular modular device, but there is no mention about other potential designs like for instance shell and tube heat exchanger (doi.org/10.1016/j.est.2022.105975), water-PCM tanks (doi.org/10.1016/j.energy.2022.126479), or plate and fin heat exchangers (doi.org/10.1016/j.est.2022.106480). In order to underline the role of the design in PCM-based devices, the authors should mention all this within the paper introduction
· Which is the heat transfer coefficient value (Eq. 5)? How did the authors calculate this? Please report assumptions like heat transfer coefficient uniformity along the angle, and so on
· It seems that the authors use the enthalpy-porosity approach to simulate liquid motion within the PCM. If so, it is suggested to define the source terms Su and Sw in Eqs. 11 and 12, and also to present relevant variables such as the mushy-zone constant (doi.org/10.1615/ComputThermalScien.2016014279) and so on
· Are the authors neglecting the thermal resistance (and capacity) at the tube that separates the working fluid with the phase change materials? Is the uniform temperature (Tp = 140 °C) a reliable assumption by considering aspect like thermal inertia and also the flow temperature variation between inlet and outlet along the screen orthogonal direction (see Fig. 3)?
· Erythritol properties are resumed in Table 1. The authors consider their values depending on the temperature (20 °C and 140 °C), but what about intermediate values? Did the authors assume that these vary with a linear law vs. the temperature? Besides, please report the thermal expansion coefficient (usually labelled as beta, 1/K) used for the computations
· CFD modeling of the modular cabinet shown in Fig. 10 is not really clear. Could the authors provide more detail here? For instance, are they just modeling the cabinet by assuming that the heat transfer fluid/PCM interface is at a uniform temperature (as previously done through the paper)? Please clarify this aspects
· Conditions simulated by considering more fins are shown in Fig. 12. Are the authors constraining weight when they run these simulations? As a suggestion, it might be also interesting to show some liquid fraction evolution plots (as previously done through the paper, see Figs. 6 and 7) for these cases
· Is the fins analysis (Table 2) done at equal weight? Furthermore, please provide thermal properties for the expanded graphite used
· The authors consider the use of expanded graphite too in subsection 5.2. Did they use this together with fins? If so, please consider the fact that some volume is substracted to the PCM, and that the weight might be a limit. Secondly, why did they use graphite instead of other comprehensive solutions that might collect fins, porous materials, and nanoparticles?
Author Response
- Mobile thermal energy storage systems are devices in which the weight might have an important role. Therefore, why didn't the authors analyzed this aspect? Why didn't they consider this constraints when running different simulations?
Thank you for this question, the weight of the equipment does impose some limitations on the system, we estimated the mass of the system based on volume and density, with allowances within the allowable loads of the trucks, also this paper focuses on the charging and exothermic processes, we will look into the weight issue later.
- The reviewer thinks that the introduction is fairly well-presented but some improvements are suggested, especially because latent thermal energy storage is one of the hottest topics nowadays in sustainable energy. For instance, the authors propose a particular modular device, but there is no mention about other potential designs like for instance shell and tube heat exchanger (doi.org/10.1016/j.est.2022.105975), water-PCM tanks (doi.org/10.1016/j.energy.2022.126479), or plate and fin heat exchangers (doi.org/10.1016/j.est.2022.106480). In order to underline the role of the design in PCM-based devices, the authors should mention all this within the paper introduction.
Thanks for the advice you gave, we have added this section to the introduction.
- Which is the heat transfer coefficient value (Eq. 5)? How did the authors calculate this? Please report assumptions like heat transfer coefficient uniformity along the angle, and so on.
Thank you for your question. In Equation 5αis the heat transfer coefficient. In this study it is assumed that the heat storage material is isotropic and therefore the heat transfer coefficient is uniform along the angle.
- It seems that the authors use the enthalpy-porosity approach to simulate liquid motion within the PCM. If so, it is suggested to define the source terms Su and Sw in Eqs. 11 and 12, and also to present relevant variables such as the mushy-zone constant (doi.org/10.1615/ComputThermalScien.2016014279) and so on.
The source term is effectively a damping term which takes on large values as the melt fraction approaches zero, while disappearing from the momentum equations as the melt fraction approaches 1. The mushy-zone constant is 1×105.
- Are the authors neglecting the thermal resistance (and capacity) at the tube that separates the working fluid with the phase change materials? Is the uniform temperature (Tp = 140 °C) a reliable assumption by considering aspect like thermal inertia and also the flow temperature variation between inlet and outlet along the screen orthogonal direction (see Fig. 3)?
Your question is a good one. The thermal resistance on the tube is small and negligible compared to that of the PCM. The change in flow temperature between inlet and outlet along the screen orthogonal direction is within 2-3°C, which has a small effect on the study, so the assumption is reliable.
- Erythritol properties are resumed in Table 1. The authors consider their values depending on the temperature (20 °C and 140 °C), but what about intermediate values? Did the authors assume that these vary with a linear law vs. the temperature? Besides, please report the thermal expansion coefficient (usually labelled as beta, 1/K) used for the computations.
Thank you for your thoughtful question. In this paper we consider these values to be linearly related to temperature and assume that the density of the heat storage material varies with temperature only in the buoyancy force, i.e. the Boussinesq assumption is used. In addition the coefficient of thermal expansion used in the calculations is 0.001.
- CFD modeling of the modular cabinet shown in Fig. 10 is not really clear. Could the authors provide more detail here? For instance, are they just modeling the cabinet by assuming that the heat transfer fluid/PCM interface is at a uniform temperature (as previously done through the paper)? Please clarify this aspects.
To simplify the analysis, the following assumptions are made in this paper:
(1) The heat storage material is isotropic;
(2) The heat loss of the heat storage box is neglected.
(3) Compared with the model size, the thickness of the copper tubes inside the heat accumulator is negligible and has little effect on heat transfer, so the tube wall thickness is ignored in the calculations;
(4) The density of the heat storage material is considered to vary with temperature only in the buoyancy force, while the other parameters are used to vary linearly, i.e., the Boussinesq assumption is used;
(5) The radiative heat exchange of the heat storage material is ignored and only the heat exchange due to convection and conduction is calculated;
The flow is assumed to be two-dimensional, i.e., the temperature change in the Y-direction is neglected, and the temperature drop is considered to be negligible with the flow of the thermal fluid.
- Conditions simulated by considering more fins are shown in Fig. 12. Are the authors constraining weight when they run these simulations? As a suggestion, it might be also interesting to show some liquid fraction evolution plots (as previously done through the paper, see Figs. 6 and 7) for these cases.
Thank you for your question. We have limited the weight by limiting the density and volume. Also added in the text is a new diagram of the phase transition in the case of different fins.
- Is the fins analysis (Table 2) done at equal weight? Furthermore, please provide thermal properties for the expanded graphite used.
Thank you for your question. The fin sizes are different for different working conditions and the corresponding weights are also different. Thermophysical properties of the expanded graphite used:
PCM |
melting enthalpy(kJ/kg) |
phase transition temperature (℃) |
thermal conductivity(W/m·K) |
erythritol |
339 |
117.7 |
0.326 |
- The authors consider the use of expanded graphite too in subsection 5.2. Did they use this together with fins? If so, please consider the fact that some volume is substracted to the PCM, and that the weight might be a limit. Secondly, why did they use graphite instead of other comprehensive solutions that might collect fins, porous materials, and nanoparticles?
Thank you for your question. We did use the expanded graphite together with the fins as a way to reduce the charging and discharging time; if we judge purely based on the thermal conductivity, the higher the proportion of porous medium, the higher the thermal conductivity of the composite, but the latent heat of phase transition will also be slightly reduced as a result, so selecting the appropriate proportion of porous medium is a must to think about, so the proportion of expanded graphite is limited in this study; in the [30,31] in which Japanese scholars Oya et al. proposed that erythritol has a high latent heat of phase transition and better thermal stability, which is in line with the nature of the ideal phase transition thermal storage material. However, the low thermal conductivity of erythritol results in an unacceptably slow heat transfer rate, which was investigated by laser flash method and differential scanning calorimetry. -composite composed of composite phase change materials, and finally concluded that vacuum impregnation of porous materials with erythritol can effectively prepare highly stable phase change composites, the latent heat of the composites is almost directly proportional to the volume ratio, and the porous materials have no effect on the melting point of erythritol (118 ℃), which has the best effect on the expansion of the graphite, so expanded graphite was used in this study.
Author Response File: Author Response.pdf
Reviewer 3 Report
- The current form of the manuscript does not adequately present the novelty of the methodology employed and the significance of the results presented. The authors should clearly explain how their approach differs from previous studies and highlight the novel aspects of their work.
- It is unclear how the present work is built on previous studies. The authors should revise the introduction section and explain the major previous findings, research gaps, and the contribution(s) of the present study.
- The manuscript text includes many repetitions that make the article long and hard to read. The manuscript text should be revised carefully.
- Appropriate references should be provided when introducing the enthalpy method in line 129.
- What is the "temperature method" the authors are referring to?
- Detailed information regarding the methodology used in the simulations should be provided. This should include a clear description of the enthalpy porosity method and how it is implemented in the simulations.
- The assumptions made to develop the numerical models should be clearly stated in the paper.
- The definition of Su and Sw employed in the momentum equation (Eq. 11 and 12) should be provided in the paper.
- The authors state that they employed ANSYS Fluent to numerically simulate solidification and melting. The solidification and melting model in ANSYS Fluent uses a parameter called the mushy-zone constant that can affect the numerical predictions. The value of this parameter should be reported in the paper. Moreover, the authors should refer to the following study and explain how sensitive their numerical predictions are to the value of this parameter.
"Sensitivity of numerical predictions to the permeability coefficient in simulations of melting and solidification using the enthalpy-porosity method." Energies 12, no. 22 (2019): 4360.
"Performance enhancement of a horizontal latent thermal energy storage unit with elliptical fins." Applied Thermal Engineering 225 (2023): 120191.
- The information reported in Table 1 is not sufficient to reproduce the results presented in the paper. The authors should explain how they modelled the variation of density, specific heat capacity, viscosity and thermal conductivity of the material with temperature.
- The authors should replace "Latent heat" with "Latent heat of fusion" in Table 1.
- Appropriate references should be added to the paper when introducing the numerical schemes used in the paper.
- The authors should analyse, report and discuss the effect of the computational time-step size on the numerical predictions.
- The figures reported in the paper look blurred. The quality of the figures should be improved.
- The authors should also compare the numerically predicted fraction of molten material (liquid fraction) with experimental data and discuss the findings in section 2.6.
- It is highly recommended that the authors avoid using AI-generated text in the manuscript.
- All acronyms and symbols used in the paper should be properly defined upon their first use to facilitate understanding for readers.
The manuscript requires extensive language editing to rectify any spelling and grammatical errors in the text. Moreover, there are inconsistencies in the use of English. The authors should seek assistance from a native English speaker to read and correct the manuscript text.
Author Response
- The current form of the manuscript does not adequately present the novelty of the methodology employed and the significance of the results presented. The authors should clearly explain how their approach differs from previous studies and highlight the novel aspects of their work.
Thank you for your suggestion. The experimental methodology used in this paper is a reference to methods that have been used by previous authors and is not novel; the importance of the results has been reflected in the concluding part of the introduction.
- It is unclear how the present work is built on previous studies. The authors should revise the introduction section and explain the major previous findings, research gaps, and the contribution(s) of the present study.
Thank you for your suggestion. Changes have been made to the introductory section.
- The manuscript text includes many repetitions that make the article long and hard to read. The manuscript text should be revised carefully.
Thank you for your suggestion. We have revised the manuscript to avoid duplicates.
- Appropriate references should be provided when introducing the enthalpy method in line 129.
Thank you for your suggestion. We have included references [20] in the relevant section.
- What is the "temperature method" the authors are referring to?
"Temperature method" typically refers to an approach used in numerical simulations, such as finite element analysis or computational fluid dynamics, to solve temperature distribution problems within a given domain. This method involves discretizing the domain into elements, assigning temperature values at specific points (nodes), and then solving the governing equations to calculate temperature distributions. It's widely used in various fields including heat transfer analysis, material behavior simulations, and environmental modeling.
- Detailed information regarding the methodology used in the simulations should be provided. This should include a clear description of the enthalpy porosity method and how it is implemented in the simulations.
Thank you for your suggestion. We have added references and a detailed description of the enthalpy-porosity method in the Methods Used in Simulation section.
- The assumptions made to develop the numerical models should be clearly stated in the paper.
Thank you for your suggestion. To simplify the analysis, the following assumptions are made in this paper:
(1) The heat storage material is isotropic;
(2) The heat loss of the heat storage box is neglected.
(3) Compared with the model size, the thickness of the copper tubes inside the heat accumulator is negligible and has little effect on heat transfer, so the tube wall thickness is ignored in the calculations;
(4) The density of the heat storage material is considered to vary with temperature only in the buoyancy force, while the other parameters are used to vary linearly, i.e., the Boussinesq assumption is used;
(5) The radiative heat exchange of the heat storage material is ignored and only the heat exchange due to convection and conduction is calculated;
The flow is assumed to be two-dimensional, i.e., the temperature change in the Y-direction is neglected, and the temperature drop is considered to be negligible with the flow of the thermal fluid.
- The definition of Su and Sw employed in the momentum equation (Eq. 11 and 12) should be provided in the paper.
Su and Sw are the source terms of the momentum equation. The source term is effectively a damping term which takes on large values as the melt fraction approaches zero, while disappearing from the momentum equations as the melt fraction approaches 1.
- The authors state that they employed ANSYS Fluent to numerically simulate solidification and melting. The solidification and melting model in ANSYS Fluent uses a parameter called the mushy-zone constant that can affect the numerical predictions. The value of this parameter should be reported in the paper. Moreover, the authors should refer to the following study and explain how sensitive their numerical predictions are to the value of this parameter.
Sensitivity of numerical predictions to the permeability coefficient in simulations of melting and solidification using the enthalpy-porosity method." Energies 12, no. 22 (2019): 4360.
"Performance enhancement of a horizontal latent thermal energy storage unit with elliptical fins." Applied Thermal Engineering 225 (2023): 120191.
Thank you for your suggestion. The mushy-zone constant is 1×105. It is demonstrated that numerical predictions of an isothermal phase-change problem are independent of the permeability coefficient for sufficiently fine meshes.
- The information reported in Table 1 is not sufficient to reproduce the results presented in the paper. The authors should explain how they modelled the variation of density, specific heat capacity, viscosity and thermal conductivity of the material with temperature.
In this paper, we consider these values to be linearly related to temperature and assume that the density of the heat storage material varies with temperature only in the buoyancy force, i.e., we adopt the Boussinesq assumption.
- The authors should replace "Latent heat" with "Latent heat of fusion" in Table 1.
Thank you for your advice, it has been revised in the text.
- Appropriate references should be added to the paper when introducing the numerical schemes used in the paper.
Thank you for your advice. We have included the appropriate references in the numerical scheme section of this paper.
- The authors should analyse, report and discuss the effect of the computational time-step size on the numerical predictions.
The size of the time step affects the accuracy of the numerical prediction. Smaller time steps allow for more precise tracking of time-dependent processes, resulting in more accurate results. Larger time steps can lead to significant errors, especially when capturing rapid changes. Time step size also affects the computational cost of the simulation. Smaller time steps require more computational resources and time to complete the simulation. Finding a balance between accuracy and computational efficiency is critical. The choice of time step size also affects the convergence of the numerical solution. As the time step decreases, the solution may converge to more accurate results. However, too small a time step may result in slower convergence or increased computational burden. After comparing our multiple simulations, the numerical solution converges better and within a tolerable computational burden for a time step of 0.1s.
- The figures reported in the paper look blurred. The quality of the figures should be improved.
Thank you for your advice. The quality of the images in the text has been upgraded.
- The authors should also compare the numerically predicted fraction of molten material (liquid fraction) with experimental data and discuss the findings in section 2.6.
Thank you for your advice. The sensible specific heat of phase change thermal storage materials is considered to be linear up to 117°C, which varies in the experiments but does not deviate too far from the experimental data, and therefore the model assumptions and computational setups mentioned in the previous section are considered to be reasonable and valid.
- It is highly recommended that the authors avoid using AI-generated text in the manuscript.
Thank you for your advice. We used AI to optimise the syntax and form of just some of the text in our manuscripts.
- All acronyms and symbols used in the paper should be properly defined upon their first use to facilitate understanding for readers.
Thank you for your advice. All acronyms and symbols used in the paper have been appropriately defined when first used.
Author Response File: Author Response.pdf
Reviewer 4 Report
Thank you for you effort and interesting work.
I have some comments that must be considered in the modified manuscript.
-------------------------------------------------------------------------------
This study introduces the concept of modular storage and transportation and presents the design of a modular mobile phase change energy storage compartment system to enhance the energy transfer efficiency of mobile heating.
Notes:
1) Long sentences are found in general (and specially in Abstract).
2) A very long (Conclusion) section, with few numerical values of the main findings. Please improve it.
3) At the end of your (Introduction) you explained the previous work in details. But, you did not explain what is the novelty of your work, or, at least what is the difference between your work and the previous work.
4) You need also to add a section for paper organization.
5) Title of Sec. 2 is (Validation of Model Validity)... Two similar words in 3 words! Please use the validity or validation once only in the same title.
6) Most of equations used need reference(s). Example: Eq. 1 and Eq. 2.
7) Data in Table 1 need a reference.
8) Most figures axes titles need best resolution (larger fonts).
9) Figure 9 has a very poor resolution.
10) I see comparisons of your results at different conditions. But, I do not see any comparison with previously published results. OR: at least, tell us how can you judge the correctness of your results.
11) Title 2.7 must be in a separate line.
Fine English editing is required, especially with long sentences.
Author Response
- Long sentences are found in general (and specially in Abstract).
Thank you for your advice. We have revised the article to try to present it in long sentences.
- A very long (Conclusion) section, with few numerical values of the main findings. Please improve it.
Thank you for your advice. We have modified the conclusion section.
- At the end of your (Introduction) you explained the previous work in details. But, you did not explain what is the novelty of your work, or, at least what is the difference between your work and the previous work.
Thank you for your advice. Changes have been made to the introductory section in the text.
- You need also to add a section for paper organization.
Thank you for your advice. This section has been added after the summary in the text.
- Title of Sec. 2 is (Validation of Model Validity)... Two similar words in 3 words! Please use the validity or validation once only in the same title.
Thank you for your advice. We have changed it in the text.
- Most of equations used need reference(s). Example: Eq. 1 and Eq. 2.
Thank you for your advice. We have included references where relevant in the text.
- Data in Table 1 need a reference.
Thank you for your advice. References to the data in Table 1 have been given in the text, i.e., references [26-29].
- Most figures axes titles need best resolution (larger fonts).
Thank you for your advice. The resolution of the images in the text has been optimised.
- Figure 9 has a very poor resolution.
Thank you for your advice. The resolution of Figure 9 has been upgraded.
- I see comparisons of your results at different conditions. But, I do not see any comparison with previously published results. OR: at least, tell us how can you judge the correctness of your results.
Thank you for your question.We compared the simulation results with the previous experimental results in the model validation section, and the overall trend of the data over time was basically the same, and the corresponding simulated temperature data did not deviate too far from the experimental data, so we judged the results to be correct.
- Title 2.7 must be in a separate line.
Thank you for the advice you gave, it has been changed in the text.
Author Response File: Author Response.pdf
Round 2
Reviewer 2 Report
The paper can be accepted as it is in the revised form
Reviewer 3 Report
The authors have addressed the reviewers' comment in the revised manuscript. The revised version can be accepted for publication after editorial corrections.