Effect of Sintering Parameters on the Mechanical Properties and Wear Performance of Alumina Inserts
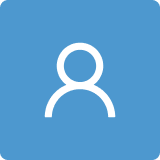
Round 1
Reviewer 1 Report
The paper had analyzed the machinability of alumina inserts which were sintered under different temperatures and holding time in high speed turning of AISI 1045 carbon steel. But the machining performance of these inserts hadn’t been analyzed deeply because of the lack of physical and mechanical properties of the inserts. For these reasons, the paper hadn’t established a closer relationship between the machinability and property of these inserts. The paper also hadn’t clarified the influencing mechanism of “Relative Density” and “Shrinkage” on the wear form of alumina inserts. Some other problems should be modified:
1. Line 157-167, is there any pictures to show the difference of porosity in these inserts which prepared under different temperature, otherwise there isn’t any evidence to support the argument.
2. In Fig. 5 and Fig. 6, the colour of “Thickness” or “Length” could be the same.
3. Line 197-200, these sentences could be descripted in Line 157-167, as a evidence to show grain growth and porosity in different inserts.
4. Line 225, secondary particles or tertiary particles could be added to the structure, such as zirconia, chromia and magnesia, but the word hadn’t been done in the experiment, the analysis had nothing to do with this paper.
5. There is no scale label or magnification times in Fig. 10 and Fig. 11. In line 331, the Figure 10 should be Figure11.
6. The conclusions should be rewritten, it is the result or discovery based on the analysis but not the phenomenon of the experiment.
Author Response
Dear Referees,
Thank you for your suggestions. All the responses to the comments have been given in the box. Also, the correction that has been added to the manuscript have been highlighted in YELLOW.
The paper had analyzed the machinability of alumina inserts which were sintered under different temperatures and holding time in high speed turning of AISI 1045 carbon steel. But the machining performance of these inserts hadn’t been analyzed deeply because of the lack of physical and mechanical properties of the inserts. For these reasons, the paper hadn’t established a closer relationship between the machinability and property of these inserts. The paper also hadn’t clarified the influencing mechanism of “Relative Density” and “Shrinkage” on the wear form of alumina inserts. Some other problems should be modified:
|
|
Point |
Response |
1. Line 157-167, is there any pictures to show the difference of porosity in these inserts which prepared under different temperature, otherwise there isn’t any evidence to support the argument.
|
Page 9: The differences of porosity has been shown in Figure 6(a) and 6(b). |
2. In Fig. 5 and Fig. 6, the colour of “Thickness” or “Length” could be the same.
|
Page 7: The colour of “Thickness” or “Length” have been updated with consistent colour in Figure 4 and Figure 5. |
3. Line 197-200, these sentences could be descripted in Line 157-167, as a evidence to show grain growth and porosity in different inserts.
|
Page 8, Line 274-276: The sentenced have been relocated to add extensive discussion on grain growth and porosity in different inserts. |
4. Line 225, secondary particles or tertiary particles could be added to the structure, such as zirconia, chromia and magnesia, but the word hadn’t been done in the experiment, the analysis had nothing to do with this paper.
|
This paragraph has been removed since the authors agreed that the statement has nothing to do with the article |
5. There is no scale label or magnification times in Fig. 10 and Fig. 11. In line 331, the Figure 10 should be Figure11.
|
Page 12-13 : The scale labels for Fig. 10 and Fig. 11 have been added. |
6. The conclusions should be rewritten, it is the result or discovery based on the analysis but not the phenomenon of the experiment. |
Page 14, Line 401-429 : The whole conclusion has been rewritten according to the comments. |
Author Response File: Author Response.docx
Reviewer 2 Report
The work presented approaches to a study of alumina inserts made with sintering temperatures and different waiting times. Alumina cutting inserts were developed taking into account the control of the sintering temperature and the waiting time. Sintered samples were analyzed based on shrinkage size, and density. The microstructure was studied by microscopic observation. The cutting tool life has been studied considering different cutting speeds. Finally, the wear mechanisms after machining were also studied.
Congratulations. The work shows that there is a good study, however, there are some concerns about your work that can be resolved by improving the work and its understanding. Please see the attachment.
Comments for author File: Comments.pdf
Author Response
Dear Referees,
Thank you for your suggestions. All the responses to the comments have been given in the box. Also, the correction that has been added to the manuscript have been highlighted in YELLOW.
The work presented approaches to a study of alumina inserts made with sintering temperatures and different waiting times. Alumina cutting inserts were developed taking into account the control of the sintering temperature and the waiting time. Sintered samples were analyzed based on shrinkage size, and density. The microstructure was studied by microscopic observation. The cutting tool life has been studied considering different cutting speeds. Finally, the wear mechanisms after machining were also studied. Congratulations. The work shows that there is a good study, however, there are some concerns about your work that can be resolved by improving the work and its understanding, such as:
|
|
Point |
Response |
# Lines 54 to 56: - The authors should rewrite this sentence: “In contrast to carbide, the machining of alumina inserts necessitates no drainage system and a cleaner environment, which contributes to a more sustainable manufacturing process [6,7].” Something is missing, maybe it's missing some words. I propose: “…and it has a cleaner environment,…” |
Page 2, Line 56: The sentence has been refined (highlighted in yellow) |
# Materials and methods: - The authors state that the fine powders were poured into the mold before being pressed with manual hydraulics with a load of 2 tons. It is necessary to identify the press used. Brand and model. - Authors should review the entire materials and methods subchapter. All equipment used must be well identified, with the brand and model of the equipment, for example the mentioned CNC. |
Page 3, Figure 1. Some important machineries that involved in the methodology have been updated with brand and model, highlighted in yellow. This is including hand press (Everest Analytical) and Cold Isostatic press (AIP3-12-60CPA American Isostatic Presses). Page 4, Figure 2. The CNC Machine that used in the study was also updated with brand and model (Haas SL-20T). |
# Lines 195 to 196: - The authors state: “Finally, the structure provided sufficient hardness to function as a cutting tool with acceptable performance [14, 15].” They should further develop or explain what they mean. Are the references to justify acceptable performance? Or is it to validate that the acceptable performance is in accordance with the values presented in the works of references 14 and 15? |
Page 8, Line 251-255 : The paragraphs have been revised. The authors initially try to elaborate their discussion with refer to the works presented in the references 14 and 15, but not the values. The references also have been revised. |
# Images 7 and 8 are not of recommended quality. The scale at the bottom of the image is not very clear. |
Page 12-13 : The scale label of Fig. 10 and Fig. 11 have been added |
# The sentence in lines 242 to 244 is unclear. Please rewrite this sentence to make your reading clearer. |
Page 10, line 306-311; The elaboration on the respected paragraph has been refined. |
# In the conclusions you can add more information: - Is there any difference between the results of the trapezoid and round inserts? What are the differences? What do you think influences this difference? Or is the shape of the inserts indifferent? If they don't comment on the shape, why did they use two shapes in this study? |
Page 14, Line 401-429: The whole conclusion has been rewritten according to the comments. Page 14, Line 408-411: The information regarding trapezoid and round inserts has been added into conclusion as well. Page 6-7. Line 200-221: The comments between two shapes have been added.
|
- When you state the maximum relative density of 93.1% obtained in this study, they can add a comment on the value obtained under the conditions identified, as was done in the abstract. Check this value. In the abstract, you have 91.3% and in the conclusions, you have 93.1%. |
Page 1, Line 24; Page 14, Line 413: The relative density value has been checked with 91.3 %, and it is consistent throughout the results. |
Author Response File: Author Response.docx
Reviewer 3 Report
Research in the field of cutting ceramics is a very actual topic. The use of cutting ceramics is mainly suitable for difficult-to-machine materials (see various manufacturers of monolithic ceramic cutters). Even basic and applied research in this area gives promising results (e.g. your cited references or articles: https://doi.org/10.1016/j.promfg.2017.11.006, https://doi.org/10.3103/S1068798X19120074, https://doi.org/10.1007/s11148-019-00272-7).
However, I see the focus and title of the submitted article as problematic, as pure oxide ceramics are known for their fragility. This property is undesirable for cutting materials. This is also one of the reasons why research and development in this area was focused on reinforced cutting ceramics.
The following information is missing in the experimental part, which I recommend to be added:
- the chemical composition of used alumina powders in experiments (is it pure Al2O3?);
- basis for choosing the sintering temperature, or range of sintering temperatures;
- dimensions and geometry of the cutting inserts;
- justify the choice of machined material and cutting conditions;
Figure 10 - Missing zoom scale. The procedure (standard, e.g. ISO 3685) according to which the wear dimensions were obtained is missing.
The chapter Conclusions contains only a brief summary of obtained results. What is the next direction for potential research?
Author Response
Dear Referees,
Thank you for your suggestions. All the responses to the comments have been given in the box. Also, the correction that has been added to the manuscript have been highlighted in YELLOW.
Research in the field of cutting ceramics is a very actual topic. The use of cutting ceramics is mainly suitable for difficult-to-machine materials (see various manufacturers of monolithic ceramic cutters). Even basic and applied research in this area gives promising results (e.g. your cited references or articles: https://doi.org/10.1016/j.promfg.2017.11.006, https://doi.org/10.3103/S1068798X19120074, https://doi.org/10.1007/s11148-019-00272-7). However, I see the focus and title of the submitted article as problematic, as pure oxide ceramics are known for their fragility. This property is undesirable for cutting materials. This is also one of the reasons why research and development in this area was focused on reinforced cutting ceramics. The following information is missing in the experimental part, which I recommend to be added:
|
|
Point |
Response |
- the chemical composition of used alumina powders in experiments (is it pure Al2O3?);
|
Page 3 : The chemical properties of Alumina has been shown in Table 1, subjected to the information given from the supplier. |
- basis for choosing the sintering temperature, or range of sintering temperatures;
|
Page 3, Line 107-109 : The state on how range of sintering temperature were selected has been explained in the text. |
- dimensions and geometry of the cutting inserts;
|
Page 2, Line 89-90. Dimension of the cutting inserts have been updated in the text. Page 6, Figure 3: Dimension of the inserts together with the designation axis have been updated in the figure. |
- justify the choice of machined material and cutting conditions;
|
Page 4, Line 128-131 : The selection of workpiece material have been elaborated, with Table 3 has been added to show chemical composition of workpiece material. Page 4, Line 134-135 : The justification of cutting conditions has been elaborated.
|
Figure 10 - Missing zoom scale. The procedure (standard, e.g. ISO 3685) according to which the wear dimensions were obtained is missing.
|
Page 12-13 : The scale label of Fig. 10 and Fig. 11 has been added |
The chapter Conclusions contains only a brief summary of obtained results. What is the next direction for potential research?
|
Page 14, Line 426-431 : The whole conclusion has been rewritten according to the comments. |
Author Response File: Author Response.docx
Reviewer 4 Report
Remarks:
fig. 1f - Big letter at the beginning (Example not example)
line 97 - you should use proper symbol of temperature not small letter "o"
table 2 - feed rate insted of feedrate
fig 3 - second column, after sintering not adfter
line 180 - different size and type of font
fig. 7 - If its possible, please format that figures in one line
fig. 8 - If its possible, please format that figures in one line
fig. 10 - on the picture should be groove formation...not groove fromation
Author Response
Dear Referees,
Thank you for your suggestions. All the responses to the comments have been given in the box. Also, the correction that has been added to the manuscript have been highlighted in YELLOW.
Point |
Response |
fig. 1f - Big letter at the beginning (Example not example) |
Page 3, Figure 1(f) : Updated (Highlighted in yellow) |
line 97 - you should use proper symbol of temperature not small letter "o" |
The proper symbol has been updated for the whole words involving (°C) |
table 2 - feed rate insted of feedrate |
Page 4 : Table 2 now changed to Table 4. The words of feed rate have been updated (Highlighted in yellow) |
fig 3 - second column, after sintering not adfter |
Figure 3 : The words of ‘after’ have been updated (Highlighted in yellow) |
line 180 - different size and type of font |
Page 7, Line 223 : The font has been refined (Highlighted in yellow) |
fig. 7 - If its possible, please format that figures in one line |
Page 9, Figure 7 now changed to Figure 6 and has been formatted for better presentation. |
fig. 8 - If its possible, please format that figures in one line |
Page 9, Figure 8 now changed to Figure 7 and has been formatted for better presentation. |
fig. 10 - on the picture should be groove formation...not groove fromation |
Page 12, Figure 10. Updated (Highlighted in yellow) |
Author Response File: Author Response.docx
Round 2
Reviewer 1 Report
Based on the phenomenon of turning, the wear mechanism of alumina inserts should be analyzed, so it would be better.
Reviewer 2 Report
The work presented has quality in accordance with the requirements of the Lubricants journal. It is well structured, written, and well supported by references. Congratulations.
Reviewer 3 Report
Since the authors followed the recommendations, made the necessary adjustments and clarified their positions, I recommend publishing the article in its current form (after adjustments).