Lubrication Performance of Misaligned Journal Bearings with Flexible Structure under Shock Load Conditions
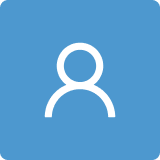
Round 1
Reviewer 1 Report
Comments and Suggestions for Authorsin this manuscript, the authors studied the lubricatin performance of misaligned journal bearing with flexible structure under shock load conditions by numerical method. The effect of flexbile structure on film pressure, deformation and film thickness was analyzed. The following comments are given,
1) The numercial model is suggested to be given more details, including the iteration procedure, the boundary conditions for the bearing deformation computation et al.
2) In the present paper, only the vertial load is included. In fact, the misaligned journal bearing would bear the torque. The shock and impuse behavior is more complicate than it is.
3) The effect of the A is provided in the paper, how about Lf?
4) Why another side is not set the flexible structure? How about the influence on the lubrication characteristic.
Author Response
Response to Reviewer 1
Dear Editor and Reviewer
We would like to thank the reviewers for their thorough reviews and useful comments and insights. Changes suggested by the reviewers have been incorporated in the manuscript. I hope that the referees will find them satisfactory. If there are further changes to be made, we will be happy to comply. We prepared sincere responses to your comments as follows.
……………………………………………………………………………………………………………………….
in this manuscript, the authors studied the lubrication performance of misaligned journal bearing with flexible structure under shock load conditions by numerical method. The effect of flexible structure on film pressure, deformation and film thickness was analyzed. The following comments are given,
Point 1: The numerical model is suggested to be given more details, including the iteration procedure, the boundary conditions for the bearing deformation computation et al.
Response 1 : We added more information as follows:
The Hydrodynamics Bearing formula and the Solid mechanics formula were combined into one matrix and the calculation was performed using a fully coupled method. The linear elastic material model was applied to the flexible area (groove) where deformation occurs, and the rigid material model was applied to other parts. The geometric part to which the rigid body model was applied was given the condition of fully constrained (de-formation = 0). A rigid material model was applied to the rotation axis, and full constraints were applied in the axial direction (z-axis).
Moreover, we informed about convergence criteria as follows
Convergence criteria are specified at a value of 10-3 for continuity, velocity, and deformation.
Point 2: In the present paper, only the vertical load is included. In fact, the misaligned journal bearing would bear the torque. The shock and impulse behavior is more complicate than it is.
Response 2: As the reviewer commented, in actual misaligned journal bearings, in addition to vertical loads, there can be shock and impulse from various directions. The resulting torque is received by the bearing. This analysis was performed with simply assuming that the vertical load and impact load also act in the vertical direction rather than the actual conditions. We are planning a verification experiment in the future, and at this time, we will reflect the opinions of the reviewers and will study the effects of the combination of impact load and vertical load from various directions. We will also measure the amount of torque as the resulting value. Thank you for your good comments.
Moreover, we added more explanation as followings:
In the case of actual misaligned journal bearings, shocks and impulses are applied in various directions in addition to the vertical load. In this study, in order to evaluate the lubrication characteristics of the flexible structure under impact load conditions, it was simply assumed that the impact load acts in the vertical direction.
Point 3: The effect of the A is provided in the paper, how about Lf ?
Response 3: The results of the effect of Lf are shown in Fig. 13. Under the same load conditions, as Lf increases, the minimum film thickness increases. In other words, as Lf increases, the length of the flexible structure increases, which means that the lubrication characteristics due to the flexible structure are improved.
Point 4: Why another side is not set the flexible structure? How about the influence on the lubrication characteristics?
Response 4: In accordance with the reviewer's opinion, we applied a flexible structure to one end of the journal bearing. The reason is that when the flexible structure was applied to both sides, it was difficult to perform various analyzes due to the disadvantage that the analysis took a long time to converge. However, when the flexible structure is applied to both sides, it is expected that lubrication performance will be improved in most cases compared to the existing one-end flexible structure. However, unlike when a flexible structure is applied to one side, the shape of a flexible structure with good lubrication properties is expected to be slightly different.
We thank the reviewer again for their time and insights.
Sincerely yours,
Corresponding author Sung-Ho Hong
Author Response File: Author Response.pdf
Reviewer 2 Report
Comments and Suggestions for AuthorsLubrication performance of journal bearings were analyzed by finite element simulation results. A flexible structure to solve the problem under shock load condition was evaluated.
However, the finite element model lacks verification.
So, if possible, please add more description on the reliability of FE model.
Author Response
Response to Reviewer 2
Dear Editor and Reviewer
We would like to thank the reviewers for their thorough reviews and useful comments and insights. Changes suggested by the reviewers have been incorporated in the manuscript. I hope that the referees will find them satisfactory. If there are further changes to be made, we will be happy to comply. we prepared sincere responses to your comments as follows.
……………………………………………………………………………………………………………………….
Lubrication performance of journal bearings were analyzed by finite element simulation results. A flexible structure to solve the problem under shock load condition was evaluated.
However, the finite element model lacks verification.
So, if possible, please add more description on the reliability of FE model.
Point 1: Lubrication performance of journal bearings were analyzed by finite element simulation results. A flexible structure to solve the problem under shock load condition was evaluated.
However, the finite element model lacks verification.
So, if possible, please add more description on the reliability of FE model.
Response 1: As the reviewer commented, validity and reliability in numerical analysis are important aspects. Verification of the finite element model can be done by comparing results from similar researches or comparing experimental results, but it is difficult to do so at this point. However, we performed the analysis because we believed that the overall deformation of the flexible structure was reasonable. Therefore, we will add pictures and explanations of the overall transformation results as shown below. Moreover, we added explanation about boundary conditions of FE analysis.
Figure 6. Dimensionless displacement of overall misaligned journal bearing with flexible structure.
This was because the oil film thickness increased by elastic deformation in the flexible structure at the end of the bearing with lubrication performances of bearings improved as shown in Fig. 6. From the overall dimensionless displacement in Figure 6, it can be con-firmed that there is appropriate deformation due to oil film pressure in the area where the flexible structure is applied.
The linear elastic material model was applied to the flexible area (groove) where deformation occurs, and the rigid material model was applied to other parts. The geometric part to which the rigid body model was applied was given the condition of fully constrained (de-formation = 0). A rigid material model was applied to the rotation axis, and full constraints were applied in the axial direction (z-axis).
We are planning an experimental study as additional research, and will compare the numerical analysis and experimental results for cases where the impact load is not vertical.
We thank the reviewer again for their time and insights.
Sincerely yours,
Corresponding author Sung-Ho Hong
Author Response File: Author Response.pdf
Reviewer 3 Report
Comments and Suggestions for AuthorsThe authors study a new design of a journal bearing with flexible elements for improvement of its ability to resist shock load under misalignment conditions. The study is rather interesting and provides some valuable results for the readers. Also some questions and comments to the authors are listed below.
1. Please specify the geometrical parameters of the modeled bearing (r, l, h), as well as the lubricant parameters.
2. Is the considered range of A parameter 0.2..0.8 (and A>1 in ref.[23]) the actual range? Considering A=a/r, the thickness of the flexible structure should be of the bearing radius at A=1, so the bushing might be of huge diameter at least twice the shaft diameter, or even more in case if A>1. At the same time, according to the scales in Fig.1-3 it looks that a<<r. Please clarify this issue, and probably it is advisable to modify Fig.1-3 to provide better understanding of the actual scales of the bearing's elements.
3. It is recommended to give a more comprehensive review on studies on fluid film bearings under shock loading, as it is the main subject of the study.
4. It is recommended to place Figures closer to where they are mentioned in the text to avoid extra scrolling during reading.
5. The Conclusions sections should be revised to present information more concisely and avoid duplication of some points, such as regarding the further research.
Comments on the Quality of English LanguageEnglish is mostly clear, it is only advised to check the manuscript again to correct some minor typos/mistakes like in Lines 39, 45, 190, 213, 423, 441, 525 etc. Some stylistic improvements in the sentences' structure are also welcomed, however not mandatory, because it doesn't cause a lot of problems in understanding.
Author Response
Response to Reviewer 3
Dear Editor and Reviewer
We would like to thank the reviewers for their thorough reviews and useful comments and insights. Changes suggested by the reviewers have been incorporated in the manuscript. I hope that the referees will find them satisfactory. If there are further changes to be made, we will be happy to comply. we prepared sincere responses to your comments as follows.
……………………………………………………………………………………………………………………….
The authors study a new design of a journal bearing with flexible elements for improvement of its ability to resist shock load under misalignment conditions. The study is rather interesting and provides some valuable results for the readers. Also some questions and comments to the authors are listed below.
Point 1: Please specify the geometrical parameters of the modeled bearing (r, l, h), as well as the lubricant parameters.
Response 1: Since this is an interpretation of journal bearings applied to home appliances of electronic company, it is difficult to specify information about the actual size and lubricant due to company security reasons. Therefore, a dimensionless analysis was performed. We would appreciate your understanding on this matter.
Point 2: Is the considered range of A parameter 0.2..0.8 (and A>1 in ref.[23]) the actual range? Considering A=a/r, the thickness of the flexible structure should be of the bearing radius at A=1, so the bushing might be of huge diameter at least twice the shaft diameter, or even more in case if A>1. At the same time, according to the scales in Fig.1-3 it looks that a<<r. Please clarify this issue, and probably it is advisable to modify Fig.1-3 to provide better understanding of the actual scales of the bearing's elements.
Response 2: Since the actual range is A up to 0.8, Figure 1-3 have been changed.
Point 3: It is recommended to give a more comprehensive review on studies on fluid film bearings under shock loading, as it is the main subject of the study.
Response 3: As the reviewer commented, there are many things to consider when conducting research on misaligned journal bearings subjected to actual impact loads. To begin with, in actual misaligned journal bearings, in addition to vertical loads, there can be shock and impulse from various directions. Moreover, the resulting torque is received by the bearing. This analysis was performed with simply assuming that the vertical load and impact load also act in the vertical direction rather than the actual conditions. We sought to determine the effect of the flexible structure on impact load in terms of lubricating properties. However, we are planning a verification experiment in the future, and at this time, we will study the effects of the combination of impact load and vertical load from various directions. We will also measure the amount of torque as the resulting value. Thank you for your good comments.
Moreover, we added more explanation as followings:
In the case of actual misaligned journal bearings, shocks and impulses are applied in various directions in addition to the vertical load. In this study, in order to evaluate the lubrication characteristics of the flexible structure under impact load conditions, it was simply assumed that the impact load acts in the vertical direction.
Point 4: It is recommended to place Figures closer to where they are mentioned in the text to avoid extra scrolling during reading.
Response 4: We placed Figures closer to where they are mentioned in the text to avoid extra scrolling during reading.
Point 5: The Conclusions sections should be revised to present information more concisely and avoid duplication of some points, such as regarding the further research.
Response 5: We revised conclusions concisely as followings:
This research presents the application of a flexible structure to misaligned journal bear-ings to improve their lubrication performances under shock load conditions. Shock loads applied for various reasons can cause wear and failure due to contact in misaligned journal bearings. To improve this phenomenon, a flexible structure that could facilitate elastic deformation was applied to the end of the journal bearing and EHL analysis was per-formed on misaligned journal bearings. The impact load of the journal bearing was assumed to be in the form of a wave. It was applied in addition to the static load. Three conditions were used in which the overall maximum load was applied at 1.5, 2, and 3 times the static load. In addition, in order to improve conditions of poor lubrication such as metal-to-metal contact, the elastic modulus was reduced within the range of the elastic modulus of bearing steel currently used and lubrication characteristics were compared with those of the existing elastic modulus. Lubrication characteristics were estimated by comparing the minimum film thickness of the journal bearing with a flexible structure using different dimensionless thicknesses, lengths, and tilting ratios. The dimensionless thickness ratio (γ) for the flexible structure remained constant at 1 since it was determined that the rectangular-shaped flexible structure outperformed the tapered one in terms of enhancing lubrication properties in a previous research. Application of the flexible structure of misaligned journal bearings is very effective in improving lubrication characteristics under impact load conditions. This is because even if an impact load is added to the static load, a sufficient oil film thickness is secured due to elastic deformation in the flexible structure. Misaligned journal bearing with a flexible structure could prevent met-al-to-metal contact until reaching a maximum load of approximately three times the rated load. When contact occurs or the lubrication performances are poor in misaligned journal bearing with flexible structure, lubrication performances are significantly improved by changing the modulus of elasticity to be slightly lower. Finally, numerical results showed that the application of flexible structure to misaligned journal bearings improved lubrication characteristics under impact load conditions. However, from an empirical perspective, additional research is needed to apply experimental verification to actual systems such as compressor and hydraulic pump.
Comments on the Quality of English Language
English is mostly clear, it is only advised to check the manuscript again to correct some minor typos/mistakes like in Lines 39, 45, 190, 213, 423, 441, 525 etc. Some stylistic improvements in the sentences' structure are also welcomed, however not mandatory, because it doesn't cause a lot of problems in understanding
Answer: We corrected incorrect spellings.
We thank the reviewer again for their time and insights.
Sincerely yours,
Corresponding author Sung-Ho Hong
Author Response File: Author Response.pdf
Round 2
Reviewer 1 Report
Comments and Suggestions for AuthorsIt is suggested to be accepted in the journal.
Author Response
Thank you for your review.
Reviewer 3 Report
Comments and Suggestions for AuthorsThe authors have improved the manuscript in some aspects according to the remarks. However, some issues still remain unclear/ignored, but they are crucial for the quality of a possible paper in Lubricants journal.
1. The principle of reproducibility is an important principle of scientific publishing. The use of dimensionless geometric parameters under the limitations you mentioned is acceptable, since the results can be reproduced by other researchers using the principle of similarity. However, information about the lubricant considered is necessary for this. Please specify in the text the lubricant used for calculations and/or its rheological parameters, such as viscosity, density, etc.
I also recommend adding to the manuscript an explicit statement about the impossibility of providing the specific values for the geometric parameters of the bearing. Thus, clarity in presentation and adherence to the principle of reproducibility of results will reduce readers' doubts about the quality of the study and the journal Lubricants publishing it.
2. Thank you for your answer, but it did not clarify the situation. According to Eq. 1, A=a/r. If we rely on Figure 2 and assume that it is made in real scale, then the ratio will be approximately A=a/r=1/10=0.1, that is, a<<r. This ratio was the same in the old version of the manuscript. In the new version, the authors increased the outer radius of the bearing sleeve, but this did not affect any of the parameters, r or a. What is the point of the changes made to the drawings?
Values of parameter A > 0.1..0.3, such as 0.8, and even more so >1, look unrealistic. With such ratios (a=r), the deformations of the flexible structure will be negligible. Please clarify this issue in more detail.
3. The explanation you added regarding the direction of the loads considered will be very useful to readers. However, my remark did not concern clarification of the conditions of the numerical experiment, but a more detailed presentation of the scientific background and results of other authors in this area. The current version of the introduction gives little insight into recent advances by other authors in this area, although the work under review is specifically focused on improving behavior under shock loads. I recommend adding more references to the relevant papers of other authors and analyzing their achievements in the field so that readers can compare the quality of their results with them.
4,5 - OK.
I hope that the manuscript will be finalized by the authors according to the comments above and published soon.
Author Response
Response to Reviewer 3
Dear Editor and Reviewer
We would like to thank the reviewers for their thorough reviews and useful comments and insights. Changes suggested by the reviewers have been incorporated in the manuscript. I hope that the referees will find them satisfactory. If there are further changes to be made, we will be happy to comply. we prepared sincere responses to your comments as follows.
……………………………………………………………………………………………………………………….
The authors study a new design of a journal bearing with flexible elements for improvement of its ability to resist shock load under misalignment conditions. The study is rather interesting and provides some valuable results for the readers. Also some questions and comments to the authors are listed below.
Point 1: The principle of reproducibility is an important principle of scientific publishing. The use of dimensionless geometric parameters under the limitations you mentioned is acceptable, since the results can be reproduced by other researchers using the principle of similarity. However, information about the lubricant considered is necessary for this. Please specify in the text the lubricant used for calculations and/or its rheological parameters, such as viscosity, density, etc.
I also recommend adding to the manuscript an explicit statement about the impossibility of providing the specific values for the geometric parameters of the bearing. Thus, clarity in presentation and adherence to the principle of reproducibility of results will reduce readers' doubts about the quality of the study and the journal Lubricants publishing it.
Response 1: We added more information about lubricants and geometric parameters as follows:
The dynamic viscosity and density of the lubricant used in the analysis are 0.02083 Pa·s and 904 kg/m3, respectively. It is difficult to specify information about the actual size and lubricant due to company security reasons since this is an interpretation of journal bearings applied to home appliances of electronic company. Therefore, a dimensionless analysis was performed.
Point 2: Thank you for your answer, but it did not clarify the situation. According to Eq. 1, A=a/r. If we rely on Figure 2 and assume that it is made in real scale, then the ratio will be approximately A=a/r=1/10=0.1, that is, a<<r. This ratio was the same in the old version of the manuscript. In the new version, the authors increased the outer radius of the bearing sleeve, but this did not affect any of the parameters, r or a. What is the point of the changes made to the drawings?
Values of parameter A > 0.1..0.3, such as 0.8, and even more so >1, look unrealistic. With such ratios (a=r), the deformations of the flexible structure will be negligible. Please clarify this issue in more detail.
Response 2: If a flexible structure is not applied, metal-to-metal contact occurs in most cases when an impact load is applied. However, when applying a flexible structure, the contact does not occur even under the condition that the maximum value of the impact load is three times the static load. As the reviewer said, increasing the A value to 0.8 is an unrealistic design condition. However, to check the results under conditions where the impact load condition was increased, the results when the A was 0.8 were also included. Therefore, an explanation for this part was added as follows.
It is almost unrealistic to apply conditions where A is 0.8 or more. The actual applicable range will be 0.4 or less. However, the analysis was performed to show that the lubrication characteristics were improved by the flexible structure even when the total load was about three times the static load.
Point 3: The explanation you added regarding the direction of the loads considered will be very useful to readers. However, my remark did not concern clarification of the conditions of the numerical experiment, but a more detailed presentation of the scientific background and results of other authors in this area. The current version of the introduction gives little insight into recent advances by other authors in this area, although the work under review is specifically focused on improving behavior under shock loads. I recommend adding more references to the relevant papers of other authors and analyzing their achievements in the field so that readers can compare the quality of their results with them.
Response 3: We found more relevant references and added references and explanation as follows.
- Jamali, H.U.; Sultan, H. S.; Abdullah, O.I.; Al-Tamimi, A.N.J.; Abbud, L.H.; Ruggiero, A.; Al-Dujaili, Z. A. Effect of chamfer form and parameters on the characteristics of finite length journal bearing under impact load. Lubricants 2023, 11, 73-28. https://doi.org/10.3390/lubricants11020073.
- Jamali, H.U.; Sultan, H. S.; Abdullah, O.I.; Al-Tamimi, A.N.J.; Abbud, L.H.; Ruggiero, A.; Al-Dujaili, Z. A. Analysis of the performance of chamfered finite-length journal bearings under dynamic loads. Mathematics 2023, 11, 587-21. https://doi.org/10.3390/math11030587.
- Pai, R.; Majumdar, B.C. Stability of submerged four-lobe oil journal bearings under dynamic load. Wear 1992, 154, 95-108. https://doi.org/10.1016/0043-1648(92)90245-4.
- Strzelecki, S. Operating characteristics of heavy loaded cylindrical journal bearing with variable axial profile. Mater. Res. 2005, 8, 481-486.
- Nacy, S.M.; Effect of chamfering on side-leakage flow rate of journal bearings. Wear 1997, 212, 95-102. https://doi.org/10.1016/S0043-1648(97)00122-1.
- Nicoletti, R. Optimization of journal bearing profile for higher dynamic stability limits. J. Tribol. 2012, 135, 011702. https://doi.org/10.1115/1.4007885.
- Ghosh, M.K.; Satish, M.R. Stability of multillobe hybrid bearing with short sills –Part II. Tribol. Int. 2003, 36, 633-636. https:// doi.org/10.1016/S0301-679X(03)00007-0.
- Jiang, L.; Feng, Q.; Coit, D.W. Modeling zoned shock effects on the stochastic degradation in dependent failure processes. IIE Trans. 2015, 47, 460-470. https://doi.org/10.1080/0740817X.2014.955152.
- Song, S.I.; Coit, D.W. Feng, Q.M. Reliability analysis of multi-component series systems subject to hard and soft failures with dependent shock effects. IIE Trans. 2016, 48, 720-735. https://doi.org/10.1080 /0740817X.2016.1140922.
Moreover, lobe-type profiles or pockets were applied to the bearings to improve lubrication characteristics under impact load conditions [39-42]. A study was conducted using chamfer and profile to improve the lubrication characteristics of misaligned journal bearings under conditions where no shock load was applied [43-45]. The chamfer and profile were applied to minimize the vibration amplitude and to enhance the turbine stability limits. Research is also being conducted on methods to appropriately describe impact loads [46-48].
Moreover, there is little analysis under large impact load conditions.
Thus, the objective of this study was to evaluate lubrication performances of a groove-type flexible structure for preventing metal-to-metal contact under large shock load conditions, where the maximum value of the impact load was approximately three times the static load.
We thank the reviewer again for their time and insights.
Sincerely yours,
Corresponding author Sung-Ho Hong
Author Response File: Author Response.pdf
Round 3
Reviewer 3 Report
Comments and Suggestions for AuthorsThe authors have answered the questions satisfactorily and made the necessary changes to the manuscript. The paper may be accepted.