Effect of Bending Process on Microstructure, Mechanical Properties and Crack Formation of 5% Ni Steel
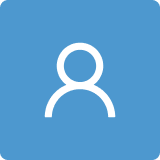
Round 1
Reviewer 1 Report
The paper would become good enough and even practically useful after certain improvements as follows.
1. Although the main conclusions on the deformation distribution and related damage features in the bended plate are quite obvious (expected), the results, in principle, deserve publication as they concern an important potential application of advanced strong steel. At the same time, to get practicable, specific recommendations are wanted (e.g. admitted ratios of thickness to the bending radius) rather than a general consideration.
2. Finally yet importantly, the authors should remove poorly justified “decorative” statements which do not refine the paper but confuse the reader. Specifically:
(a) It is presumed that OXIDES plastically deform following the bending scheme (Fig. 5). However, such particles are normally very hard so that proves are needed to admit their plasticity at room temperature. Indeed, the shown few particles could have non-equiaxed shapes BEFORE the bending; anyway, only a statistically significant analysis of this issue may confirm the strong authors’ presumption.
(b) It is careless to relate the increase of dislocation density EXCLUSIVELY to pile-ups at grain boundaries; more so that such a statement could hardly be proved directly. Meanwhile, notable strains of about 50% at the plate surfaces enable a regular multiplication of dislocations in interiors of deformed grains.
(c) To the reviewer’s knowledge, the increase of “hard orientation” fraction with the growing strain and related textures is not a general regularity. Anyway, solid references should be given to support such an idea. Besides, the phenomenon itself is usually called “orientation hardening” rather than the work hardening that is mostly due to the growing dislocation density.
(d) The presumed crucial role of stress concentration at grains of “harder orientations” is not at all convincing. First, contrary to this statement, the color contrast in Fig 7c for mid-thickness is even stronger than in Fig.7a (outer surface layer). Second, just the higher average strength (deforming stress) and lower ductility of surface layers are enough to promote the cracking.
Besides, unlike the parent austenite phase, the term “grain” as such is hardly relevant to the MARTENSITE microstructure composed of thin laths, grouped in packets and blocks. The related initial spread of orientations inside any FORMER grain is at least comparable to the re-orientations of actual martensite crystals (blocks) during the considered plate bending.
(e) Recrystallization or notable recovery in this high-strength steel at ROOM TEMPERATURE does not look plausible. As to Ref. [22], molecular dynamics, applicable to few thousands of atoms at most, is hardly representative for much larger relevant volumes which have micron dimensions; moreover, mentioned mechanisms due to the so called SEVERE deformation (strain degree of hundreds per cent) do not correspond to the considered strain in bending.
(f) The employed KAM function of EBSD actually reflects the crystal curvature (orientation gradient) and hence underlying distributions of lattice defects rather than local STRESSES as claimed by the authors. The micro-stress sometimes MAY be correlated with KAM but it is not the general rule. Besides, the local KAM itself is dependent on both the scanning step and the number of involved neighboring points; this issue (ignored in the paper) should be carefully considered for each specific scale level of the investigated microstructure.
Author Response
Please see the attachment.
Author Response File: Author Response.pdf
Reviewer 2 Report
The proposed article can be valorized as follows:
1. The English language of the text and sentence constructions should be improved throughout the text.
3. Sentence in the introductory part: The LNG storage and transportation materials .... misspelled. Namely, the transported material does not require better resistance to cracking ... that is meaningless. There are more such situations in the text. It needs to be controlled and repaired.
4. A distinction should be made between the neutral axis relating to the cross-section of the girder and the neutral line connecting the points on the neutral axes of the cross-sections. In Fig. 1, and is completely misrepresented. first, it is not a neutral axis but it should be a neutral line but it is also completely mislocated. The neutral axis of the section, for example, in the bent part of the section lies in the direction from the center of gravity of the section shifted towards the center of the curvature of the section. In any case, the picture is completely wrong and needs to be changed. Please look at the material related to curved girders.
4. The article is pretty poorly written and needs to be checked throughout the article. The microstructure analysis leaves a better impression, but it loses its significance due to poor article writing and fundamental errors.
5. References must be added.
Author Response
Please see the attachment.
Author Response File: Author Response.pdf
Round 2
Reviewer 1 Report
Now it is OK.
Author Response
Thank you very much for your patient and meticulous review. We have learned a lot from your review, which is very helpful to our future scientific research work. Once again, we would like to express our heartfelt thanks to you.
Reviewer 2 Report
Some improvements have been made. Unfortunately, Fog 1 is still totally wrong and must not remain so. This Fig 1 should either be completely removed or the features related to the neutral line or neutral plane should be removed from it. This is completely wrong, look in the literature for determining the position of the neutral line (axis) or the surface of curved supports.
Author Response
Please see the attachment.
Author Response File: Author Response.pdf
Round 3
Reviewer 2 Report
Thanks for your accepting the reality, since previously shown neutral line (as well as neutral surface) was totally wrong indicated.
Now, the paper can be passed on to a further stage.
Regards.