Effect of TiN on Sulfide Morphology of Non-Quenched and Tempered Steel
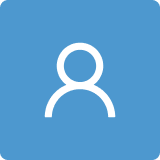
Round 1
Reviewer 1 Report (Previous Reviewer 3)
Dear authors. You have made good work and the subject is interesting. Anyhow I think you should describe the problems you are solving more accurately: how these steels you are studied, are produced today in industry and what are the main industrial problems with them (ingot casting, continuous casting?), is Ti addition tested in industry? And are the main problems chain like, longitudinal MnS inclusions/precipitates? Is your composition similar with industrial composition, any cooperation with industry? I also wonder why oxygen contents (19 – 30 ppm) and Al contents (50 to 160 ppm) are so different in the sample cases and why 19 ppm oxygen is obtained with lowest Al content? Si content is also low in the first case. Does this mean that it is difficult to control the steel composition in the laboratory system? Your conclusion is that Ti addition is a new idea and it is cleat that it has positive effects on MnS inclusions/precipitates, but are the results good enough? For highest Ti about 62% are pure MnS and for lowest Ti 85%. Is this enough? And your one conclusion is that TiN need to be forming much earlier than MnS to get good effects. We can speak about primary TiN and MnS and secondary TiN/TiCN and MnS. The secondary are forming below the solidus. Typically, the secondary MnS precipitates are chain-line precipitates. Above solidus the MnS are coarser and I think more evenly distributed in the matrix. What is your opinion about the secondary particles compared with primary particles? And MnS can be (MnFe)S or (MnFe)S-O. Ti addition may lead to problems too, as TiO2 formation and nozzle clogging. But it also reduces the grain growing effectively. I hope you will discuss more widely about the results (positive effects – are they enough? – negative effects?). You have used only one steel grade, I assume? Are the results general for other these kinds of steels too? You have made inhouse thermodynamic model and calculations but I hope you will also use commercial thermodynamic tools which have more advanced algorithms. Your model is a good inhouse model, but it has many simplifications and the results are not very accurate. So if you have a commercial tool available with large databanks, I think you should use these kind of tools. The ratio Mn/S is also an important factor. I hope you will consider my comments and submit this again and continue this important subject.
Author Response
Please see the attachment
Author Response File: Author Response.pdf
Reviewer 2 Report (New Reviewer)
1. I am asking the authors to explain the sense of using such a low vacuum (below 100 Pa). 2. In order to improve the quality of the presented material, please specify in what form (powder or sponge) and how titanium was incorporated into the steel. Did this method of introduction ensure its homogeneity throughout the entire volume of the ingot? 3. Does introducing Ti into steel have a better effect than introducing Zr? 4. I am asking the authors to explain in the text of the article how the ingot forging temperature was determined. What anvils (shape) were used to forge the ingot and according to what scheme the forging process was carried out. The article should specify the value of the applied crumple. 5. In the authors' opinion, if the material is heated to T = 1250 ° C several times in the forging process, will it change the size of inclusions? 6. The term "rolled steel" appears frequently in the article. As the test samples were taken from forged material, I am asking you to standardize the terminology in the text of the article. 7. In the opinion of the reviewer, for the better readability of the article, the purpose of the work should be included. Some information on this is provided in the introduction.8. Page 3, line 100-102. Does not specified spectrometry method and spectrometer equipment (INCA - it is software shell, but not a spectrometer model). Is it WDS or EDS method? This is principal moment, because this is question of accuracy limits and sensitivity of measurement. Also does not specified method of general chemical analysis of ignots on Table 1. Please add all the analytical methods and all of used equipment models.
9. Page 4, lines 137-140. Here is also shown part of method without enough specification. 25mm2 is huge area for SEM. Is it analysed by one shot or it was series of shot? I think that it was no less than 10 images with equval square 25 mm2. Another way you can not recieve an enough practical resolution for recognition 1 mkm particles. If it was not single shot - the next question is about system of positiong this images - is it neighbored merged shots of one big area or combination of random shots from various points? Acoording to table 8 information and its description, more than 1200 inclusion was recognised for each sample and the chemical composition for each inclusion was determined and counted Ti-containing inclusions. It is too much for manual recognition, but the text have no information about automatic analysis method and its accuracy and basic setup.
10. Figures 2-7 and 9-14. All the SEM pictures have visual information only, but no numerical spectra data presented. It will be much more better to add the information of inclusions chemical percentage and could be spectra screenshots. All of figures have a lot of free space from the right side and it can be used for more full and rich data presentation.
11. Figures 18 - 19. The text size in legend and under the axises is so small and unreadable. Another figures have also non equivale different text size each figure. Please harmonise the text size for ALL figures.
Author Response
Please see the attachment.
Author Response File: Author Response.pdf
Round 2
Reviewer 1 Report (Previous Reviewer 3)
Dear authors. Thank you for the good answers you have given to my comments I sent to you. From my side this could now be published. Anyhow I hope that you include more the text from your answers to the published paper. I think the readers would like to read more about these things you have answered to me. Now you have added only some text. Please add more.
Author Response
Please see the attachment.
Author Response File: Author Response.pdf
This manuscript is a resubmission of an earlier submission. The following is a list of the peer review reports and author responses from that submission.
Round 1
Reviewer 1 Report
The presented manuscript covers an interesting study on inclusion evolution focusing on the influence of TiN on sulfide morphology. The following aspects should be considered to improve the manuscript:
- Introduction: The first sentence using "green steel" might not be a good choice. Especially today "green steel" is significantly more often related to "hydrogen steelmaking"; should be rephrased without using "green steel".
- The authors describe 2D and 3D analysis as possible characterization methods only in a very short paragraph only. The specific methods behind (especially 3D) have to be described a little bit more precisely. The comparison between 2D and 3D needs to be more clear.
- Values of automated SEM/EDS measurements as well as light optical microscopy should not be given in absolute values (1225, 1202,...909, 950,..) but should be normalized to the measured sample area.
- Some minor english and typo errors: e.g. line 78, 99, 133, 222,
Author Response
Please see the attachment.
Author Response File: Author Response.pdf
Reviewer 2 Report
This research field has been studied by many authors over many decades. It is a well-reported scientific area. It is evident from the reference list in this work that almost none of the extensive literature on the topic published in the major Western journals has been studied, much of it specifically related to this particular aspect of sulphide precipitation.
The work is lacking in experimental aspects;
- Sulphide morphology has been studied by many authors using the technique of deep etching to reveal the sulphide inclusion shape in 3D. The method is an essential confirmation of conventional 2D microscopy and should have been included in this study. A excellent example is to be found in "Sulfide Inclusions in Steel", ed J deBarbadillo, publ ASM 1974, pp 135 - 158. (an authoritative review which is not referenced in this paper). Results are required to confirm the speculations in the paper derived from 2D observations.
- Sulphide morphology is known to be directly related to the steel's oxygen potential. This aspect has not been studied or reported in this paper although it has a direct and probably critical effect on the results/conclusions.
Author Response
Please see the attachment.
Author Response File: Author Response.pdf
Reviewer 3 Report
Dear authors. Your work is interesting. Yes, it is correct that Ti is used a lot with microalloying steels mainly to reduce harmful precipitates (carbonitrides). But it helps also because it modify harmful precipiates and get them to form at higher temperature and they are then bigger and not so harmful. The reason for this is that diffusion is faster and as you mention, TiN can be nucleating core. And as you mention these last benefits are not studied so much. And your results show that this is true at least partly. Some comments: 1) Your Al content is very low and total oxygen quite high anyhow. As I understand you only find aluminium oxides. Because at room temperature, dissolved oxygen should be almost zero, so I think you should have orher oxydes too in the samples, or how? What about TiO2 - titanium has very strong affinity to oxygen? MnO? SiO2? And what about TiCN. I think you should have this too. 2) TiO2 may lead also to strong clogging of the nozzles. 3) I think Ti might also form TiCS sulfides? 4) And I think Ti has also negative effects on mechanical properties, even it reduce, as precipitate, the grain growing. 5) Ca treatment. You mention that it is not stable and ideal. But it is very much used in industry and is very succesfull. Especially to avoiding harmfull MnS chains along the boundaries and transforming Al2O3 to calciumaluminates, which are liquid at higher temperatures. But your Al content is so low and S content high that it might be that in your case Ca treatment just lead more or less to solid CaS sulfides, which causes clogging problems and to avoid MnS chains, Ca are needed too much - a lot of problems, what is your opinion? 6) In the introduction part you mention the four morphology group of MnS sulfides and say that the number II should be avoided. It could be good if you write a bit more about this subject. How to avoid the II group etc. Also for me the English names for morphologies are not all so clear: fan, spindle-like,... it could be nice to have a picture which shows the forms visually, if possible. 7) Experimental trials: cooling rate during solidification and after that have effects on the results. Do you have any estimations about your cooling rates during solidification and after that, and what i syour opinion, how cooling rate affects the results. 8) Figures 2 to 7: It would be good if you put there in the figure text which morphology group MnS sulfides are belonging (groups I to IV) and why? And also put to the figure texts the steel composition number in question. 9) You mention that in the test steel, as to sulfides, you have pure MnS and various composite inclusions (Fig 2.) I see only MnS inclusions in the figure? But from figure 8, I can see you have anyhow also composite inclusion stoo in the test steel grade with low Ti content. 10) Figure 8: we can see that even with high Ti content, the most inclusions are not Ti containing sulfides, are the rest pure MnS sulfides. 11) How do you see the effects of Ti additions if anyhow most sulfides are pure MnS even with highest Ti content? The difference with to lower Ti content is not so big. And with Ti 0.055 or even with 0.028 the formation of TiO2 is likely at higher temperatures, especially with low Al content as you have, and this is causing clogging problems during continuous casting. It is also likely that TiCN is forming at lower temperatures, because your C content is quite high, or what is your opinion? 12) Or how did you evaluate the effects of Ti additions - no mechanical testing? 13) Figures 9-14, please add the steel grade in question in the figure text too. 14) Figures 16 and 17: we can clearly see some effects but are they enough? Are they significant? Hoe to make the conclusions? Especially if anyhow the amount of pure MnS is very big in all these cases. 15) Itcould be good also to get some informaton about the effects on the inclusion/precipiates sizes, not only to the lebght-width ratio. 16) Thermodynamic model: You have made a lot of good work in modelling. But today a lot of commercial tools are available whish are more accurate and scientific with less assumptions as for instance IDS software, ThermoCalc, FactSage,...Your model is very good but it is a bit simple with many assumptions. For instance Scheil model is not the best one to model solidification because it assumes diffusion is zero at the solid phase and this distribution coefficient is constant etc. I propose that in the future you will use commercial thermodynamic tools with very large thermodynamic databanks and only a few assumptions compared with your model. Also the diffusion can be handled and activities of not pure inclusions/precipitates, etc. Anyhow I see you have made good model, so you are very talent, but it is abit too simple compared with many commercial tools. But anyhow your results are very clear that with higher Ti and N, TiN is forming much higher thanMnS. I think it is very reasonable. 17) My conclusion is that your work is very good and it can be published by just after taking carefully into account my comments above. Best regards and congratulations for the hard work.
Author Response
Please see the attachment.
Author Response File: Author Response.pdf
Round 2
Reviewer 2 Report
The need for 3D confirmation of the suphide shape has been dismissed too lightly. Conclusion #1 refers explicitly to sulphide shape only as determined in 2D. The conclusion would be much strengthened by confirmation with 3D analysis, particularly with reference to the widely-used standard of forms of the sulphides as types 1, 11 or 111.
The contention that the oxygen content is of no importance with regard to sulphide precipitation in this steel must be substantiated either by further experiment or by suitable reference to existing reports. If the work is to be of general value, this aspect would be particularly important.
Author Response
Please see the attachment.
Author Response File: Author Response.pdf
Reviewer 3 Report
I think the authors answers are good and from my side this can now be published.
Author Response
Thank you very much for your evaluation and recognition.
Round 3
Reviewer 2 Report
The authors responses indicate that the work reported is not complete and is a "work in progress" which requires further experimentation before the conclusions can be fully substantiated. The authors are recommended to continue the work until the required results can be obtained, and then publish the results.