Modal Analysis of Ultrasonic Spot Welding for Lightweight Metals Joining
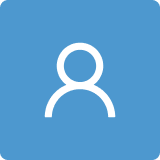
Round 1
Reviewer 1 Report
Dear Authores,
very interessting topic. Altought i am an industrial expert in US welding, I have never seen a simulation approach. Perhaps a graphical description between Simulation Input, Simulation Method and outcome would be great for a better understanding of the red linie.
Thank you.
Author Response
Your recognition of our work is deeply appreciated, and it serves as a tremendous source of motivation. We are dedicated to advancing our research to deliver useful simulation approach and extend its applicability within the welding industry. Thank you for the comment on the simulation dataflow, we have added a schematic drawing in Fig. 3 for better understanding of simulation methods. Relevant description was added in Section 2.3 titled by “Connection of simulation approaches and experiments”.
Reviewer 2 Report
In this study, authors developed a modal analysis tool for ultrasonic spot welding of lightweight materials, focusing on magnesium and aluminum alloys. It identifies coupon geometry and weld spacing as critical factors impacting welding reliability, with experimental validation through temperature monitoring and comparisons with joint strength and fracture location. The research contributes insights into optimizing ultrasonic welding processes for lightweight materials. The article is well-written, effectively conveying scientific outcomes for both experts and newcomers to the field. I strongly recommend this publication in its present form.
Author Response
We sincerely appreciate your affirmation of this work. This is very encouraging for us. We will endeavor to continue our research on the ultrasonic welding simulation towards a matured engineering tool that can contribute to weld design and process optimization. In the future, we will further improve and validate the modal analysis tool through advanced in-situ measurement of displacement and local stresses.
Reviewer 3 Report
The manuscript reports the results of combined modelling and experimental study of ultrasonic welding. The modelling background is described in terms of equations of general physical laws found in textbooks - there appears to be little novelty or cutting edge knowledge underlying the approach adopted by the authors.
It is not clear whether temperature-dependent deformation properties of materials have been incorporated in the simulation - at least, there is no evidence of data being used for that purpose. It is also not clear whether the effect of contact deformation conditions on the vibration frequency and amplitude has been considered.
Thus, apart from the reference to de Vries experiment, there does not appear to be significant amount of 'take home' conclusions - it is noted that the authors identify the node and anti-node effects as the key determinant; but, frankly, this could be anticipated without detailed simulation, so that the work carried out amounts to confirmation of this general rule.
Major revision is required to make the manuscript sufficiently well-structured and content-full to warrant publication.
There are some instances of incorrect English grammar in the text.
Author Response
Please see attached.
Author Response File: Author Response.pdf
Reviewer 4 Report
Dear Authors,
I have read your manuscript with interest and I consider it as up-to-date.
However, I have a few comments for you to consideration.
1. (Keywords section) There is no justification to repeat words or phrases from the title to the keywords. In this way you can't use potential of keywords (as metadata) to increase visibility of your potential manuscript in internet browsers.
I suggest new keywords: solid-state welding; aluminium joints; aluminium welds; joints computing; joints modelling, etc.
2. There is no reliable and in-depth verification of modeling through physical experiment.
3. Both mathematical modeling and the verifying physical process should be precisely described in order to meet the condition of reproducibility and repeatability of experiments.
4. There is no in-depth discussion of the results.
5. The conclusions should be clear in terms of describing the impact of welding conditions on the properties of the joints, as announced in the introduction.
Regards
Author Response
Thank you for the comments. Please see the attachment.
Author Response File: Author Response.pdf
Reviewer 5 Report
The work is focused on ultrasonic spot welding. For the most part, the authors apply simulation methods to optimize the welding geometry, so the work is purely technical. In this regard, the practical relevance of the work is high, but fundamental knowledge was not obtained. Nevertheless, the relevance is present. There are the following comments:
1. You need to check the affiliation carefully. In particular, the indexes.
2. The results in Figure 3 are certainly interesting, but the motivation for such a model is not quite clear. Yes, in laboratory studies it is possible to weld in this way, so there may be a swaying effect of the free end, but in industrial conditions this effect will obviously be eliminated, since the workpieces will be much larger and will be fixed.
3. The caption in Figure 4b should include the source number.
4. There is also a slight confusion of terms in this section. Both "vibration amplitude" and "relative motion" are used at once, which should be avoided, especially in the figures.
5. In the caption to Figure 5, I suggest that you include ¼ λ,and ½ λ for clarity.
6. It is not quite clear which amplitude of vibration is referred to in Figures 3 and 6. As I understand it, in the case of Figure 3 the vibration is vertical and in the case of Figure 6 the vibration is horizontal, correct?
7. For the experiment in Figure 7, the same questions as before. How relevant is such a task if the actual workpiece will be rigidly fixed? Perhaps offsets would not even be needed to avoid hotspot?
8. Section 3.3: what is the purpose of using inches? It is common in the journal to use SI Units.
Author Response
Dear Reviewer,
Thank you for the comments. Please see the attachment.
Best regards
Author Response File: Author Response.pdf
Round 2
Reviewer 4 Report
Dear Authors,
I have no more comments.
Regards