Numerical Investigation of an Experimental Setup for Thermoplastic Fuselage Panel Testing in Combined Loading
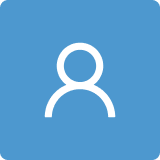
Round 1
Reviewer 1 Report
Comments and Suggestions for AuthorsThe authors present an interesting study on the design of a test rig to submit a thermoplastic stiffened panel under pressure/compression loading. There is a limited number of paper on full scale testing and therefore the interest in this subject is high. However the paper can be improved to increase its readibility.
The review is poor and the authors can use the litterature review done by Grotto et al https://doi.org/10.20944/preprints202311.1611.v1
Line 85 : what do you mean by the "stiffness of element non involved..."
The exploded view given figure 3 and the explanations are not clear. Before explaining the subcomponents, a figure of the principle of the rig must be provided. It should be self-consistent and include the actuator and the reacting elments given in figure 5.
What is the the purpose of the components described figure 3b and 3f
Give the size of the elements and the number od d.o.f. of the FEM used
The FEM boundary conditions are not clear especially on the compression area. Do you use locally a 3D model to model the resin container? Can you provide a detail of this area? On which zone are the group of slave nodes?
Author Response
Please see the attachment.
Author Response File: Author Response.pdf
Reviewer 2 Report
Comments and Suggestions for AuthorsThe submitted manuscript deals, as mentioned in the title, with the numerical investigation of a novel experimental test setup to investigate fuselage panels under combined loadings. In the first part of the manuscript the stiffened fuselage panel under investigation is introduced. After that the experimental setup of the novel testing approach is presented. Finally, numerical investigations of the fuselage panel under the loading conditions from the test rig are described. The content of the manuscript seems to be an original work, which deserves publication after a major revision addressing all points, listed below:
1) Abstract: The abstract must be revised. It is not clear to me from the abstract alone whether the design of a fuselage panel or an experimental test setup is the focus of the work.
2) Section 1: Two things are missing in the introduction. Firstly, other load cases of the fuselage or fuselage panels could be discussed before focusing on buckling. Examples could be found in https://doi.org/10.1007/s13272-011-0004-x , https://doi.org/10.1016/j.jcomc.2022.100236 ,
https://doi.org/10.1007/978-94-007-4282-6 .
Secondly, there is no specific statement on how the internal pressure, which is taken into account in the new test device, affects the buckling load. If the internal pressure increases the buckling load, which is expected, the author should give a clear reasoning for the effort to include it in the new test setup.
3) Section 1: The author of reference 27 should read Odermann and not Odermanna.
4) Section 1: The authors should clarify in line 122 what a level 2 test is as there are different definitions.
5) Section 1: In line 117 Table I should read Table 1.
6) Table 1: Why do the authors differentiate between tensile and compressive stiffness in the fibre direction for thermoplastic composites and not for thermoset composites? Here too, the compressive stiffness should be lower than the tensile stiffness.
7) Table 2: The authors should explain or at least provide references to the analytical methods used to estimate the missing parameters.
8) Table 3: The heading of Table 3 refers to fibre properties. A fibre volume content is given in the table, which refers to a composite, i.e. fibre and matrix. What is meant?
9) Figure 3: For Figure 3, I would suggest showing only 3a, but larger, and naming the individual parts in the figure. It is currently difficult to categorise the individual parts. Showing the overall construction and the individual parts from a similar perspective offers the reader no added value.
10) Figure 4: Similar to the comment on Figure 3 I would prefer one picture of the whole setup with the specimen installed for readability.
11) Section 4: How was the mesh size of 5 mm decided? Has a mesh convergence study be conducted? The authors should justify the choice of the mesh size.
12) Section 4: From my understanding the authors performed a linear eigenvalue buckling analysis without taking imperfections into account. If this is the case, the perfect buckling load is calculated. However, the actual buckling load determined in physical experiments will be far below the calculated load due to geometrical and material imperfections as well as imperfect load application. Shouldn't the more realistic, non-linear buckling analysis be used for the design of a test bench?
13) Section 4: Are there any comparable structures available in literature tested for buckling? How do the experimental results from literature compare to the numerical results in this work?
14) Figure 6: I would recommend to show a detail of the mesh, for example of the bottom corner of structure (a).
15) Section 4: In line 286 the authors mention that they only apply a fraction of the typical differential cabin pressure. They should quantifiy the fraction (could be around 50%, cf. https://doi.org/10.1007/978-94-007-4282-6 ).
16) Figure 9: The color scheme of subfigures a and b should be the same for better readability.
17) Section 4: The authors use a maximum stress criterion of the critical ply to judge the stressing effort of the structure. Why did the authors chose Max Stress over an interactive criterion like Hashin, Puck or LaRC? What limit values for Max Stress were used?
18) Section 4: Referring to comment 2, what is the difference in buckling load with and without applied differential pressure in the analysis?
19) Section 4, 5: Both the section on numerical modelling part as well as the discussion section have the section number 4.
20) Section 5 (discussion): The authors state in the discussion that the lower-than-typical 0.3 bar pressure does not cause damage in the stiffened panel. If the panel design is based on a real design, shouldn't pressure up to the typical differential pressure cause no damage?
21) Section 5 (discussion): Only results are summarised in the discussion. A critical reflection of the work and the identification of open points for future investigation is missing.
Based on the comments listed above, the reviewer recommends the publication of the paper after major revisions addressing clearly all the comments and suggestions listed above.
Author Response
Please see the attachment.
Author Response File: Author Response.pdf
Round 2
Reviewer 2 Report
Comments and Suggestions for AuthorsWith all comments now clearly addressed, the manuscript can be published in its current form.