Journal Description
International Journal of Turbomachinery, Propulsion and Power
International Journal of Turbomachinery, Propulsion and Power
is an international, peer-reviewed, open access journal on turbomachinery, propulsion and power. The journal is owned by the EUROTURBO European turbomachinery society and is published quarterly online by MDPI.
- Open Access— free for readers, with article processing charges (APC) paid by authors or their institutions.
- High Visibility: indexed within Scopus, ESCI (Web of Science), Inspec, and other databases.
- Journal Rank: JCR - Q2 (Engineering, Aerospace)
- Rapid Publication: manuscripts are peer-reviewed and a first decision is provided to authors approximately 53.7 days after submission; acceptance to publication is undertaken in 17.5 days (median values for papers published in this journal in the first half of 2025).
- Recognition of Reviewers: reviewers who provide timely, thorough peer-review reports receive vouchers entitling them to a discount on the APC of their next publication in any MDPI journal, in appreciation of the work done.
Impact Factor:
1.8 (2024);
5-Year Impact Factor:
1.7 (2024)
Latest Articles
Body Force Modelling of a Multi-Stage High-Pressure Compressor Under Inlet Distortion
Int. J. Turbomach. Propuls. Power 2025, 10(2), 12; https://doi.org/10.3390/ijtpp10020012 - 17 Jun 2025
Abstract
►
Show Figures
The present work aims to propose a new calibration strategy of the Hall–Thollet Body Force (BF) model to simulate the flow in multi-stage compressors and to capture inlet distortion effects within the machine. Both global (0D) and radial (1D) correction terms are introduced
[...] Read more.
The present work aims to propose a new calibration strategy of the Hall–Thollet Body Force (BF) model to simulate the flow in multi-stage compressors and to capture inlet distortion effects within the machine. Both global (0D) and radial (1D) correction terms are introduced and calibrated to improve predictions in multi-stage compressors, accounting for highly interacting, highly loaded blades, falling outside the validity range of the model’s original coefficients. The modified model has been tested on the 3.5-stage high-pressure compressor CREATE, for which experimental data are available. The modified model is then employed to study different patterns of inlet distortion. The results show a very good agreement between Unsteady Reynolds-Averaged Navier–Stokes (URANS) simulations and Body Force calculations in terms of performance, key quantities along the radial and circumferential directions and distortion transfer across the compressor.
Full article
Open AccessArticle
Analysis of Interactions Among Loss-Generating Mechanisms in Axial Flow Turbines
by
Greta Raina, Yannick Bousquet, David Luquet, Eric Lippinois and Nicolas Binder
Int. J. Turbomach. Propuls. Power 2025, 10(2), 11; https://doi.org/10.3390/ijtpp10020011 - 13 Jun 2025
Abstract
►▼
Show Figures
Accurate loss prediction since the preliminary design steps is crucial to improve the development process and the aerodynamic performance of turbines. Initial design phases typically employ reduced-order models in which the different loss-generating mechanisms are assessed through correlations. These correlations are often based
[...] Read more.
Accurate loss prediction since the preliminary design steps is crucial to improve the development process and the aerodynamic performance of turbines. Initial design phases typically employ reduced-order models in which the different loss-generating mechanisms are assessed through correlations. These correlations are often based on the hypothesis of loss linearity, which assumes that losses from different sources can be summed to obtain the total losses. However, this assumption could constitute an oversimplification, as losses occur concurrently and can interact with each other, potentially impacting overall performance, all the more in low aspect ratio turbomachinery. The aim of this paper is to investigate the role of interactions between different phenomena in the generation of loss. 3D RANS simulations are run on two simplified representations of a turbine blade channel, a curved duct and a linear cascade, and on a real turbine vane. Several inlet and wall boundary conditions are employed to examine loss-generating phenomena both separately and simultaneously. This approach enables the analysis of where and how interactions occur and quantifies their influence on the overall losses. Losses caused by boundary layer–vortex interactions are found to be highly sensitive to the relative positions of these two phenomena. It was observed that the loss linearity assumption may be acceptable in certain cases, but it is generally inadequate for off-design conditions and twisted annular configurations.
Full article
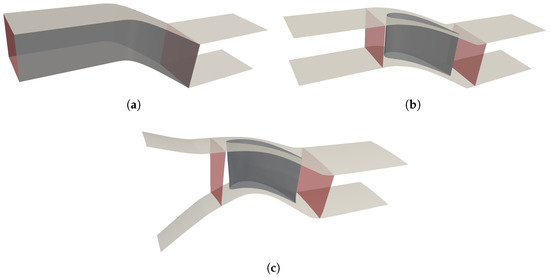
Figure 1
Open AccessFeature PaperArticle
Experimental Results in a Variable-Pitch Wells Rotor
by
Fabio Licheri, Tiziano Ghisu, Francesco Cambuli, Pierpaolo Puddu and Mario Carta
Int. J. Turbomach. Propuls. Power 2025, 10(2), 10; https://doi.org/10.3390/ijtpp10020010 - 11 Jun 2025
Abstract
►▼
Show Figures
Systems based on the oscillating water column (OWC) principle are often equipped with Wells turbines as power take-offs (PTOs) to convert sea-wave energy. The self-rectifying nature of the Wells turbine represents a strength for such applications, while its limited operating range, due to
[...] Read more.
Systems based on the oscillating water column (OWC) principle are often equipped with Wells turbines as power take-offs (PTOs) to convert sea-wave energy. The self-rectifying nature of the Wells turbine represents a strength for such applications, while its limited operating range, due to stall, is one of the most relevant limitations. A possible improvement lies in varying the blade stagger angle during operation as this can delay stall by reducing the incidence angle. Although the performance of variable-pitch Wells turbines has been studied in the past, their local aerodynamic performance has never been investigated before. This study addresses this important task by experimentally reconstructing the flow field along the blade height of a Wells turbine prototype, coupled to an OWC simulator, for three values of the stagger angle. The aerodynamic behavior of the Wells rotor is characterized at its inlet and outlet, showing how the interaction between adjacent blades changes due to the stagger angle. The rotor performance is evaluated and compared, providing useful information that is of general validity for similar rows of symmetric blade profiles when pitched at different stagger angles.
Full article
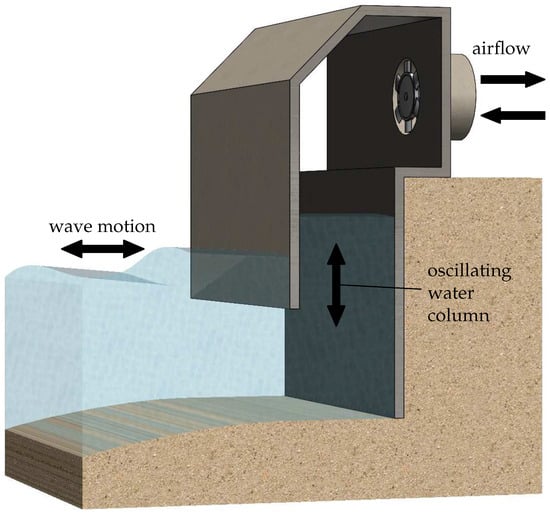
Figure 1
Open AccessArticle
Effects of Tip Injection on a Turbofan Engine with Non-Invasive High-Speed Actuators
by
Yannik Schäfer, Marcel Stößel, Arnaud Barnique and Dragan Kožulović
Int. J. Turbomach. Propuls. Power 2025, 10(2), 9; https://doi.org/10.3390/ijtpp10020009 - 27 May 2025
Abstract
►▼
Show Figures
This paper presents an analysis of the stability margin improvement (SMI), which is also known as stall margin improvement, achieved by continuous tip air injection. New piezoelectric actuators were designed and manufactured with a new engine inlet for the Larzac 04 C5 jet
[...] Read more.
This paper presents an analysis of the stability margin improvement (SMI), which is also known as stall margin improvement, achieved by continuous tip air injection. New piezoelectric actuators were designed and manufactured with a new engine inlet for the Larzac 04 C5 jet engine. It has noninvasive injection positions that do not have any measurable effect on the inlet air flow when it is switched off. The main focus of the system design was to achieve high power of the injected air and, as a result, a high SMI. The results presented enable a maximum SMI of 99%. A variety of engine operating conditions and injection positions were experimentally tested and discussed regarding SMI. Additionally, the complex relationship between SMI gains and thrust specific fuel consumption (TSFC) is explored in a power balance analysis, revealing a trade-off between SMI improvement and increased energy consumption.
Full article
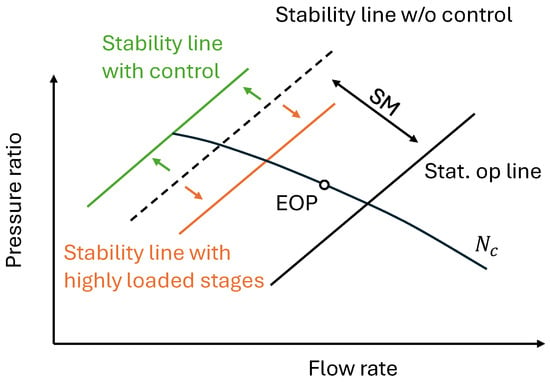
Figure 1
Open AccessArticle
A Quasi-Direct Numerical Simulation of a Compressor Blade with Separation Bubbles and Inflow Turbulence
by
Guglielmo Vivarelli, João Anderson Isler, Chris D. Cantwell, Francesco Montomoli, Spencer J. Sherwin, Yuri Frey-Marioni, Marcus Meyer, Iftekhar Naqavi and Raul Vazquez-Diaz
Int. J. Turbomach. Propuls. Power 2025, 10(2), 8; https://doi.org/10.3390/ijtpp10020008 - 27 May 2025
Abstract
►▼
Show Figures
Within the turbomachinery industry, components are currently assessed deploying standard second-order steady solvers. These are unable to capture complicated unsteady phenomena that have a critical impact on component performance. In this work, the high-order spectral h/p solver Nektar++ will be applied to a
[...] Read more.
Within the turbomachinery industry, components are currently assessed deploying standard second-order steady solvers. These are unable to capture complicated unsteady phenomena that have a critical impact on component performance. In this work, the high-order spectral h/p solver Nektar++ will be applied to a compressor blade to study the turbulent transition mechanisms and assess the effect of incoming disturbances with quasi-DNS resolution. The case will be modelled at an angle of incidence of to match the original experimental loading at . At clean inflow conditions, Kelvin–Helmholtz instabilities appear on both sides of the blade due to a double separation, with the pressure side one not being reported in the experiments. The separation is gradually removed by the incoming turbulent structures but at different rates on the two sides of the blade. It will be shown that there is an optimal amount of turbulence intensity that minimises momentum thickness, which is strongly related to losses. Moreover, a discussion on the spanwise extrusion will be included, this being a major player in the modelling costs. Finally, the wall-clock time and the exact expenditure to run this case will be outlined, providing quantitative evidence of the feasibility of considering a quasi-DNS resolution in an industrial setting.
Full article
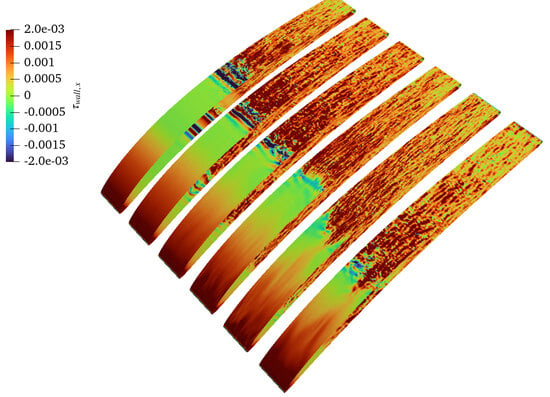
Graphical abstract
Open AccessArticle
Aeroelastic Response in an Oscillating Transonic Compressor Cascade—An Experimental and Numerical Approach
by
Carlos Alberto Tavera Guerrero, Nenad Glodic, Mauricio Gutierrez Salas and Hans Mårtensson
Int. J. Turbomach. Propuls. Power 2025, 10(2), 7; https://doi.org/10.3390/ijtpp10020007 - 1 Apr 2025
Abstract
The steady-state aerodynamics and the aeroelastic response have been analyzed in an oscillating linear transonic cascade at the KTH Royal Institute of Technology. The investigated operating points ( and ) represent an open-source virtual compressor (VINK) operating at a
[...] Read more.
The steady-state aerodynamics and the aeroelastic response have been analyzed in an oscillating linear transonic cascade at the KTH Royal Institute of Technology. The investigated operating points ( and ) represent an open-source virtual compressor (VINK) operating at a part speed line. At these conditions, a shock-induced separation mechanism is present on the suction side. In the cascade, the central blade vibrates in its first natural modeshape with a 0.69 reduced frequency, and the reference measurement span is 85%. The numerical results are computed from the commercial software Ansys CFX with an SST turbulence model, including a reattachment modification (RM). Steady-state results consist of a Laser-2-Focus anemometer (L2F), pressure taps, and flow visualization. Steady-state numerical results indicate good agreement with experimental data, including the reattachment line length, at both operating points, while discrepancies are observed at low-momentum regions within the passage. Experimental unsteady pressure coefficients at the oscillating blade display a fast amplitude decrease downstream, while numerical results overpredict the amplitude response. Numerical results indicate that, at the measurement plane, for both operating points, the harmonic amplitude is dominated by the shock location. At midspan, there is an interaction between the shock and the separation onset, where large pressure gradients are located. Experimental and numerical responses at blades adjacent to the oscillating blade are in good agreement at both operating points.
Full article
(This article belongs to the Special Issue Selected Papers from the 16th International Symposium on Unsteady Aerodynamics, Aeroacoustics and Aeroelasticity of Turbomachines (ISUAAAT16))
►▼
Show Figures
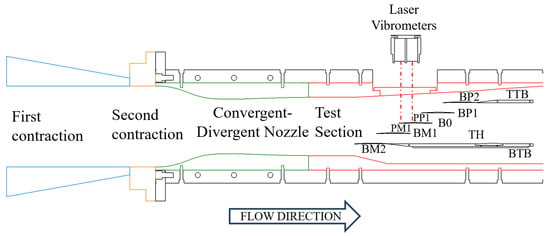
Figure 1
Open AccessArticle
Preliminary Assessment of Geometric Variability Effects Through a Viscous Through-Flow Model Applied to Modern Axial-Flow Compressor Blades
by
Arnaud Budo, Jules Bartholet, Thibault Le Men, Koen Hillewaert and Vincent E. Terrapon
Int. J. Turbomach. Propuls. Power 2025, 10(2), 6; https://doi.org/10.3390/ijtpp10020006 - 1 Apr 2025
Abstract
►▼
Show Figures
An important question for turbomachine designers is how to deal with blade and flowpath geometric variabilities stemming from the manufacturing process or erosion during the component lifetime. The challenge consists of identifying where stringent manufacturing tolerances are absolutely necessary and where looser tolerances
[...] Read more.
An important question for turbomachine designers is how to deal with blade and flowpath geometric variabilities stemming from the manufacturing process or erosion during the component lifetime. The challenge consists of identifying where stringent manufacturing tolerances are absolutely necessary and where looser tolerances can be used as some geometric variations have little or no effects on performance while others do have a significant impact. Because numerical simulations based on Reynolds-averaged Navier–Stokes (RANS) equations are computationally expensive for a stochastic analysis, an alternative approach is proposed in which these simulations are complemented by cheaper through-flow simulations to provide a finer exploration of the range of variations, in particular in the context of robust design. The overall goal of the present study is to evaluate the adequacy of a viscous time-marching through-flow solver to predict geometric variability effects on compressor performance and, in particular, to capture the main trends. Although the computational efficiency of such a low-fidelity solver is useful for parametric studies, it is known that the involved assumptions and approximations associated with the through-flow (TF) approach introduce errors in the performance prediction. Thus, we first evaluate the model with respect to its underlying assumptions and correlations. To accomplish this, TF simulations are compared to RANS simulations applied to a modern low-pressure compressor designed by Safran Aero Boosters. On the one hand, the TF simulations are fed with the exact radial distribution of the correlation parameters using RANS input data in order to isolate the modeling error from correlation empiricism. Moreover, in the context of multi-fidelity optimization, such distributions can be predicted using the more detailed RANS simulations that are performed on selected operating points. On the other hand, correlations from the literature are assessed and improved. It is shown that the solver provides realistic predictions of performance but is highly sensitive to the underlying correlations. Then, two modeling aspects linked to the blade leading edge, namely incidence correction and camber line computation, are discussed. As geometric variability precisely at the blade leading edge has a significant impact on the performance, we assess how these two aspects influence the variability propagation in this region. Moreover, we propose a strategy to mitigate these model uncertainties, and geometric variabilities are introduced at the blade leading edge in order to quantify the resulting variation in performance. Finally, within the scope of this preliminary study, perturbations of the three-dimensional position of undeformed stator blades and deformations of the hub and shroud contours are introduced one factor at a time per simulation. Their range is defined based on the tolerance limits typically imposed in the industry and on observed manufacturing variability. It is found that the through-flow model broadly provides realistic predictions of performance variations resulting from the imposed geometric variations. These results are a promising first step towards the use of the through-flow modeling approach for geometric uncertainty quantification.
Full article
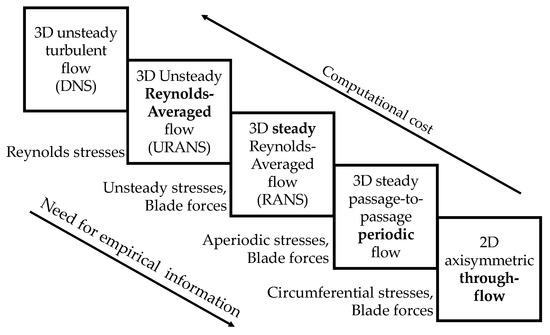
Figure 1
Open AccessArticle
Considerations for High-Fidelity Modeling of Unsteady Flows in a Multistage Axial Compressor
by
Douglas R. Matthews and Nicole L. Key
Int. J. Turbomach. Propuls. Power 2025, 10(1), 5; https://doi.org/10.3390/ijtpp10010005 - 10 Mar 2025
Abstract
►▼
Show Figures
This paper presents the development and validation of a high-fidelity, unsteady, computational fluid dynamics (CFD) model of the Purdue 3-Stage Axial Research Compressor. A grid convergence study assesses the spatial discretization accuracy of the single-passage, steady-state computational model. Additionally, the periodic-unsteady convergence of
[...] Read more.
This paper presents the development and validation of a high-fidelity, unsteady, computational fluid dynamics (CFD) model of the Purdue 3-Stage Axial Research Compressor. A grid convergence study assesses the spatial discretization accuracy of the single-passage, steady-state computational model. Additionally, the periodic-unsteady convergence of the unsteady signals of a multiple-passage transient blade row model was explored. Computational predictions were compared with experimental measurements to evaluate the efficacy of the various modeling decisions. Notably, transient blade row model calculations employing the Scale-Adaptive Simulation (SAS) formulation of Menter’s Shear Stress Transport (SST) turbulence model exhibited a significantly improved agreement with experimental data compared to steady-state calculations. Particularly, in conjunction with the SAS-SST turbulence model, the transient calculations significantly improved the spanwise (radial) mixing characteristics of the transient-average stagewise total temperature profiles. Spectral analyses of the transient signals compared with unsteady pressure measurements showed fundamental and second harmonic blade-passing frequency amplitudes matching within 5–7% in the embedded stage. This research underscores the importance of including accurate geometry, practical minimization of modeling assumptions using higher-fidelity physics models, comprehensive convergence assessment, and the comparison and validation of computational predictions with experimental measurements.
Full article
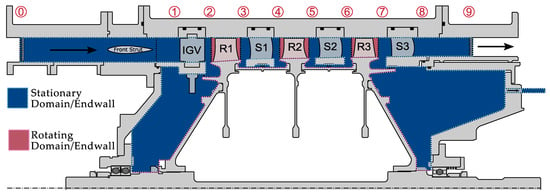
Figure 1
Open AccessFeature PaperArticle
Cavity Instabilities in a High-Speed Low-Pressure Turbine Stage
by
Lorenzo Da Valle, Antonino Federico Maria Torre, Filippo Merli, Bogdan Cezar Cernat and Sergio Lavagnoli
Int. J. Turbomach. Propuls. Power 2025, 10(1), 4; https://doi.org/10.3390/ijtpp10010004 - 4 Mar 2025
Abstract
►▼
Show Figures
This study investigates the time-resolved aerodynamics in the cavity regions of a full-scale, high-speed, low-pressure turbine stage representative of geared turbofan engines. The turbine stage is tested in the von Karman Institute’s short-duration rotating facility at different purge rates (PR) injected through the
[...] Read more.
This study investigates the time-resolved aerodynamics in the cavity regions of a full-scale, high-speed, low-pressure turbine stage representative of geared turbofan engines. The turbine stage is tested in the von Karman Institute’s short-duration rotating facility at different purge rates (PR) injected through the upstream hub cavity. Spectra from the shroud and downstream hub cavity show perturbations linked to blade passing frequency and rotor speed. Asynchronous flow structures associated with ingress/egress mechanisms are observed in the rim seal of the purged cavity. At 0% PR, the ingress region extends to the entire rim seal, and pressure fluctuations are maximized. At 1% PR, the instability is suppressed and the cavity is sealed. At 0.5%, the rim-seal instability exhibits multiple peaks in the spectra, each corresponding to a state of the instability. Kelvin–Helmholtz instabilities are identified as trigger mechanisms. A novel technique based on the properties of the cross-power spectral density is developed to determine the speed and wavelength of the rotating structures, achieving higher precision than the commonly used cross-correlation method. Moreover, unlike the standard methodology, this approach allows researchers to calculate the structure characteristics for all the instability states. Spectral analysis at the turbine outlet shows that rim-seal-induced instabilities propagate into regions occupied by secondary flows. A methodology is proposed to quantify the magnitude of the induced fluctuations, showing that the interaction with secondary flows amplifies the instability at the stage outlet.
Full article
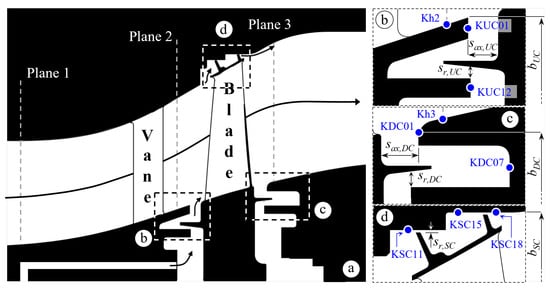
Figure 1
Open AccessArticle
Panel Method for 3D Inviscid Flow Simulation of Low-Pressure Compressor Rotors with Tip-Leakage Flow
by
Valentin Caries, Jérôme Boudet and Eric Lippinois
Int. J. Turbomach. Propuls. Power 2025, 10(1), 3; https://doi.org/10.3390/ijtpp10010003 - 6 Feb 2025
Abstract
►▼
Show Figures
This paper presents a low-order three-dimensional approach for predicting the inviscid flow around low-pressure compressors. The method is suitable for early design stages and allows a broad exploration of design possibilities at minimal cost. It combines the vortex lattice method with the panel
[...] Read more.
This paper presents a low-order three-dimensional approach for predicting the inviscid flow around low-pressure compressors. The method is suitable for early design stages and allows a broad exploration of design possibilities at minimal cost. It combines the vortex lattice method with the panel method by using a mixed boundary condition. In addition, it models the tip-leakage flow using an iterative algorithm. First, the verification of the approach is carried out on a low-pressure compressor configuration. The wake length is a decisive parameter for ensuring correct flow deflection in ducted applications. A periodicity condition is introduced and validated, which reduces the computational and memory requirements. On average, the calculations take less than one minute in real time. The approach is validated on the same low-pressure compressor configuration. A good agreement is obtained with RANS concerning the mean flow and the tip-leakage flow characteristics. Sensitivity to the mass flow rate is also fairly well predicted, although discrepancies develop at lower mass flow rates.
Full article
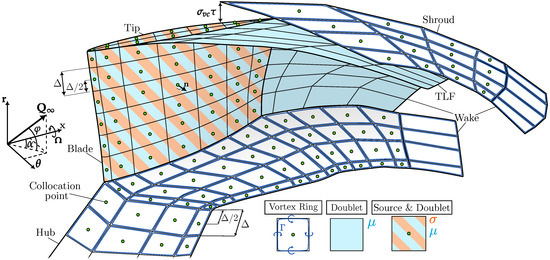
Figure 1
Open AccessFeature PaperArticle
An Open Test Case for High-Speed Low-Pressure Turbines: The SPLEEN C1 Cascade
by
Gustavo Lopes, Loris Simonassi, Samuel Gendebien, Antonino Federico Maria Torre, Marios Patinios, Nicolas Zeller, Ludovic Pintat and Sergio Lavagnoli
Int. J. Turbomach. Propuls. Power 2025, 10(1), 2; https://doi.org/10.3390/ijtpp10010002 - 3 Feb 2025
Cited by 1
Abstract
►▼
Show Figures
Aviation accounts for a significant share of global CO2 emissions, necessitating efficient propulsion technologies to achieve net-zero emissions by 2050. Geared turbofan architectures offer a promising solution by enabling higher bypass ratios and improved fuel efficiency. However, geared turbofans introduce significant aerodynamic
[...] Read more.
Aviation accounts for a significant share of global CO2 emissions, necessitating efficient propulsion technologies to achieve net-zero emissions by 2050. Geared turbofan architectures offer a promising solution by enabling higher bypass ratios and improved fuel efficiency. However, geared turbofans introduce significant aerodynamic and structural challenges, particularly in the low-pressure turbine. Current understanding of high-speed low-pressure turbine behavior under engine-representative conditions is limited, especially regarding unsteady wake interactions, secondary flows, and compressibility effects. To address these gaps, this work presents a novel test case of high-speed low-pressure turbines, the SPLEEN C1. The test case and experimental methodology are depicted. The study includes the commissioning and characterization of a transonic low-density linear cascade capable of testing quasi-3D flows. The rig’s operational stability, periodicity, and inlet flow characterization are assessed in terms of loss and turbulence quantities to ensure an accurate representation of engine conditions. These findings provide a validated experimental platform for studying complex flow interactions in high-speed low-pressure turbines, supporting future turbine design and efficiency advancements.
Full article
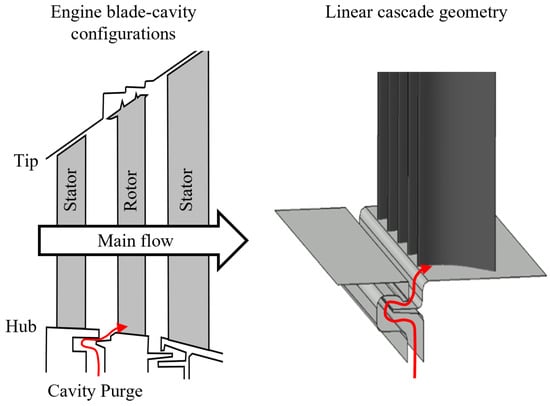
Figure 1
Open AccessArticle
Computational Design of an Energy-Efficient Small Axial-Flow Fan Using Staggered Blades with Winglets
by
Mustafa Tutar and Janset Betul Cam
Int. J. Turbomach. Propuls. Power 2025, 10(1), 1; https://doi.org/10.3390/ijtpp10010001 - 9 Jan 2025
Abstract
►▼
Show Figures
The present study introduces a conceptual design of a small axial-flow fan. Both individual and combined effects of blade stagger angle and winglet on the performance of the fan design are investigated in design and off-design operating conditions using a computational flow methodology.
[...] Read more.
The present study introduces a conceptual design of a small axial-flow fan. Both individual and combined effects of blade stagger angle and winglet on the performance of the fan design are investigated in design and off-design operating conditions using a computational flow methodology. A stepwise solution, in which a proper stagger angle adjustment of a specifically generated blade profile is followed by appending a winglet at the tip of the blade with consideration of different geometrical parameters, is proposed to improve the performance characteristics of the fan. The initial model comparison analysis demonstrates that a three-dimensional, Reynolds-averaged Navier–Stokes (RANS) equation-based renormalization group (RNG) k–ε turbulence modeling approach coupled with the multiple reference frame (MRF) technique which adapts multi-block topology generation meshing method successfully resolves the rotating flow around the fan. The results suggest that the use of a proper stagger angle with the winglet considerably increases the fan performance and the fan attains the best total efficiency with an additional stagger angle of +10° and a winglet, which has a curvature radius of 6.77 mm and a twist angle of −7° for the investigated dimensioning range. The present study also underlines the effectiveness of passive flow control mechanisms of the stagger angle and winglets for energy-efficient axial-flow fans.
Full article
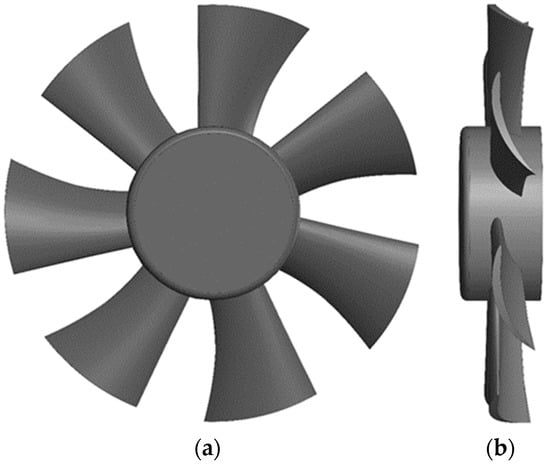
Figure 1
Open AccessArticle
In-Hole Measurements of Flow Inside Fan-Shaped Film Cooling Holes and Downstream Effects
by
Emin Issakhanian
Int. J. Turbomach. Propuls. Power 2024, 9(4), 36; https://doi.org/10.3390/ijtpp9040036 - 2 Dec 2024
Abstract
►▼
Show Figures
The study of low-speed jets into crossflow is critical to the performance of gas turbines. Film cooling is a method to maintain manageable blade temperatures in turbine sections while increasing turbine inlet temperatures and turbine efficiencies. Initially, cooling holes were cylindrical. Film cooling
[...] Read more.
The study of low-speed jets into crossflow is critical to the performance of gas turbines. Film cooling is a method to maintain manageable blade temperatures in turbine sections while increasing turbine inlet temperatures and turbine efficiencies. Initially, cooling holes were cylindrical. Film cooling jets from these discrete round holes were found to be very susceptible to jet liftoff, which reduces surface effectiveness. Shaped holes have become prominent for improved coolant coverage. Fan-shaped holes are the most common design and have shown good improvement over round holes. However, fan-shaped holes introduce additional parameters to the already complex task of modeling cooling effectiveness. Studies of these flows range in hole lengths from those found in actual turbine blades to very long holes with fully developed flow. The flow within the holes themselves is difficult to study as there is limited optical access. However, the flow within the holes has a strong effect on the resulting properties of the jet. This study presents velocity and vorticity fields measured using high-resolution magnetic resonance velocimetry (MRV) to study three different fan-shaped hole geometries at two blowing ratios. Because MRV does not require line of sight, it provides otherwise hard-to-obtain experimental data of the flow within the film cooling hole in addition to the mainflow measurements. By allowing measurement within the cooling hole, MRV shows how a poor choice of diffuser start point and angle can be detrimental to film cooling if overall hole length and cooling flow velocity are not properly accounted for in the design. The downstream effect of these choices on the jet height and counter-rotating vortex pair is also observed.
Full article
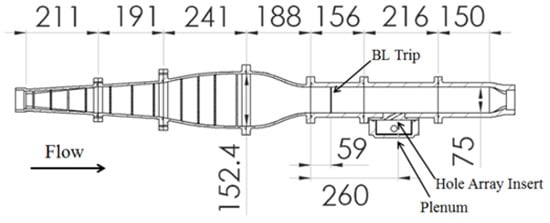
Figure 1
Open AccessFeature PaperArticle
Experimental Investigation of Synchronous-Flow-Induced Blade Vibrations on a Radial Turbine
by
Marios Sasakaros, Markus Schafferus, Manfred Wirsum, Arthur Zobel, Damian Vogt, Alex Nakos and Bernd Beirow
Int. J. Turbomach. Propuls. Power 2024, 9(4), 35; https://doi.org/10.3390/ijtpp9040035 - 8 Nov 2024
Cited by 1
Abstract
►▼
Show Figures
In this study, a thorough experimental investigation of the synchronous blade vibrations of a radial turbine is performed for different IGV configurations. First, the blade modes are measured experimentally and calculated numerically. Subsequently, the vibrations are recorded with two redundant measurement systems during
[...] Read more.
In this study, a thorough experimental investigation of the synchronous blade vibrations of a radial turbine is performed for different IGV configurations. First, the blade modes are measured experimentally and calculated numerically. Subsequently, the vibrations are recorded with two redundant measurement systems during real operation. Strain gauges were applied on certain blades, while a commercial blade-tip-timing system is used for the measurement of blade deflections. The experimentally determined vibration properties are compared with numerical estimations. Initially, the vibrations recorded with the “nominal” IGV were presented. This IGV primarily generates nodal diameter (ND) 0 vibrations. Subsequently, the impact of two different IGV configurations is examined. First, a mistuned IGV, which has the same number of vanes as the “nominal” IGV is examined. By intentionally varying the distance between the vanes, additional low engine order excitations are generated. Moreover, an IGV with a higher number of vanes is employed to induce excitations at higher frequency modes and ND6 vibrations. Certain vibrations are consistently measured across all IGV configurations, which cannot be attributed to the spiral turbine casing. In addition, a turbine–compressor interaction has been observed.
Full article
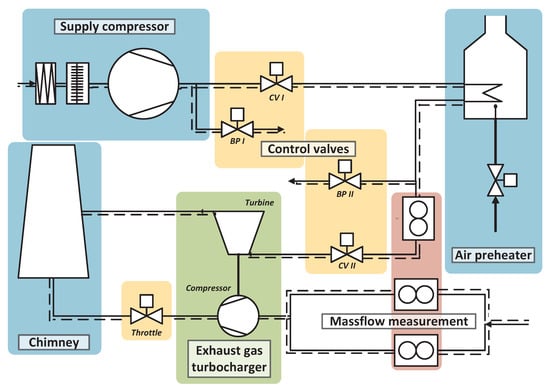
Figure 1
Open AccessArticle
Rotationally Induced Local Heat Transfer Features in a Two-Pass Cooling Channel: Experimental–Numerical Investigation
by
David Gutiérrez de Arcos, Christian Waidmann, Rico Poser, Jens von Wolfersdorf and Michael Göhring
Int. J. Turbomach. Propuls. Power 2024, 9(4), 34; https://doi.org/10.3390/ijtpp9040034 - 4 Nov 2024
Cited by 1
Abstract
►▼
Show Figures
Turbine blades for modern turbomachinery applications often exhibit complex twisted designs that aim to reduce aerodynamic losses, thereby improving the overall machine performance. This results in intricate internal cooling configurations that change their spanwise orientation with respect to the rotational axis. In the
[...] Read more.
Turbine blades for modern turbomachinery applications often exhibit complex twisted designs that aim to reduce aerodynamic losses, thereby improving the overall machine performance. This results in intricate internal cooling configurations that change their spanwise orientation with respect to the rotational axis. In the present study, the local heat transfer in a generic two-pass turbine cooling channel is investigated under engine-similar rotating conditions ( ) through the transient Thermochromic Liquid Crystal (TLC) measurement technique. Three different angles of attack ( ) are investigated to emulate the heat transfer characteristics in an internal cooling channel of a real turbine blade application at different spanwise positions. A numerical approach based on steady-state Reynolds-averaged Navier–Stokes (RANS) simulations in ANSYS CFX is validated against the experimental method, showing generally good agreement and, thus, qualifying for future heat transfer predictions. Experimental and numerical data clearly demonstrate the substantial impact of the angle of attack on the local heat transfer structure, especially for the radially outward flow of the first passage, owing to the particular Coriolis force direction at each angle of attack. Furthermore, results underscore the strong influence of the rotational speed on the overall heat transfer level, with an enhancement effect for the radially outward flow (first passage) and a reduction effect for the radially inward flow (second passage).
Full article
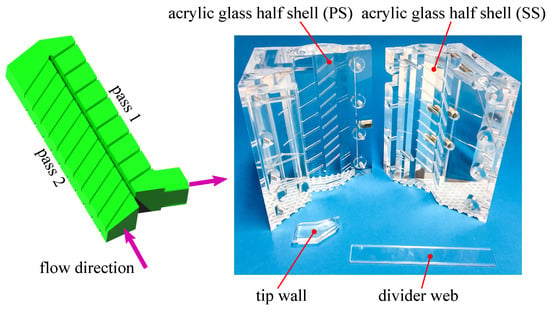
Figure 1
Open AccessArticle
Predictive Modeling of NOx Emissions from Lean Direct Injection of Hydrogen and Hydrogen/Natural Gas Blends Using Flame Imaging and Machine Learning
by
Iker Gomez Escudero and Vincent McDonell
Int. J. Turbomach. Propuls. Power 2024, 9(4), 33; https://doi.org/10.3390/ijtpp9040033 - 3 Oct 2024
Abstract
►▼
Show Figures
This research paper explores the use of machine learning to relate images of flame structure and luminosity to measured NOx emissions. Images of reactions produced by 16 aero-engine derived injectors for a ground-based turbine operated on a range of fuel compositions, air pressure
[...] Read more.
This research paper explores the use of machine learning to relate images of flame structure and luminosity to measured NOx emissions. Images of reactions produced by 16 aero-engine derived injectors for a ground-based turbine operated on a range of fuel compositions, air pressure drops, preheat temperatures and adiabatic flame temperatures were captured and postprocessed. The experimental investigations were conducted under atmospheric conditions, capturing CO, NO and NOx emissions data and OH* chemiluminescence images from 27 test conditions. The injector geometry and test conditions were based on a statistically designed test plan. These results were first analyzed using the traditional analysis approach of analysis of variance (ANOVA). The statistically based test plan yielded 432 data points, leading to a correlation for NOx emissions as a function of injector geometry, test conditions and imaging responses, with 70.2% accuracy. As an alternative approach to predicting emissions using imaging diagnostics as well as injector geometry and test conditions, a random forest machine learning algorithm was also applied to the data and was able to achieve an accuracy of 82.6%. This study offers insights into the factors influencing emissions in ground-based turbines while emphasizing the potential of machine learning algorithms in constructing predictive models for complex systems.
Full article
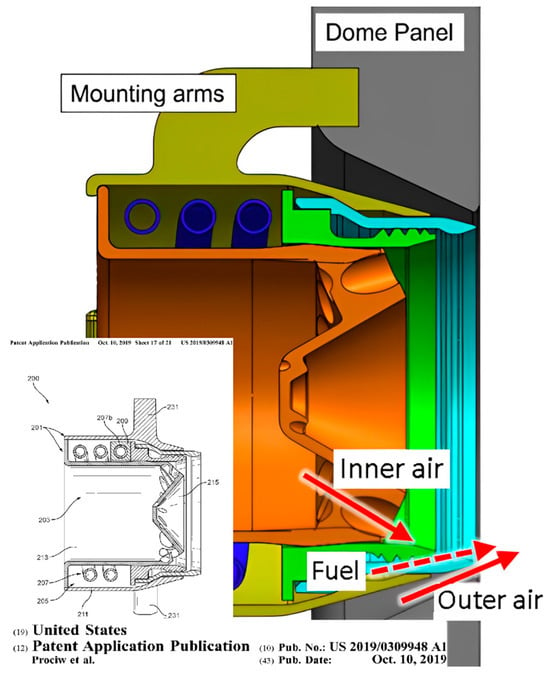
Figure 1
Open AccessFeature PaperArticle
Prediction of Fan Array Performance with Polynomial and Support Vector Regression Models
by
Philipp Ostmann, Martin Rätz, Martin Kremer and Dirk Müller
Int. J. Turbomach. Propuls. Power 2024, 9(4), 32; https://doi.org/10.3390/ijtpp9040032 - 3 Oct 2024
Abstract
►▼
Show Figures
The increasing utilisation of demand-controlled ventilation strategies leads to the frequent operation of fans under part-load conditions. To accurately predict the energy demand of a ventilation system with a fan array in the early design stages, models that calculate reliable results across the
[...] Read more.
The increasing utilisation of demand-controlled ventilation strategies leads to the frequent operation of fans under part-load conditions. To accurately predict the energy demand of a ventilation system with a fan array in the early design stages, models that calculate reliable results across the whole operating range are required. We present the comparison of a polynomial and a machine learning approach through support vector regression (SVR) to predict the fan performance over a wide range of typical operating points. For fitting and validation, we use experimental data. We investigate the extrapolation performance of both approaches. The SVR model achieves a slightly better representation of the experimental data with a lower error, especially when only sparse data are available. Both approaches yield similar results when the evaluation is conducted within the experimentally captured domain but deviates outside the domain. At operating points that are far from the experimentally captured domain, the polynomial models yield fan efficiencies that are physically plausible, while the SVR models drastically overpredict the fan efficiency. To rate the influence of such deviations towards modelling the actual energy demand, both approaches are applied to an operation simulation of a simplified office building. Both approaches yield similar results despite differing extrapolation capabilities.
Full article
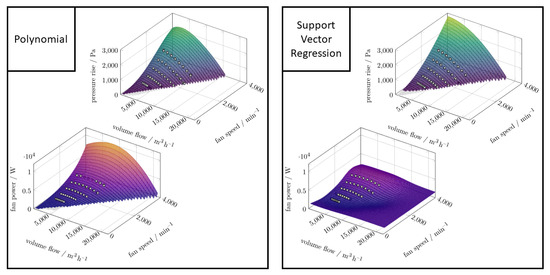
Graphical abstract
Open AccessFeature PaperArticle
Development and Design Validation of an Inflow-Settling Chamber for Turbomachinery Test-Benches
by
Michael Henke, Stefan Gärling, Lena Junge, Lars Wein and Hans-Ulrich Fleige
Int. J. Turbomach. Propuls. Power 2024, 9(4), 31; https://doi.org/10.3390/ijtpp9040031 - 24 Sep 2024
Abstract
At Leibniz University of Hannover, Germany, a new turbomachinery test facility has been built over the last few years. A major part of this facility is a new 6 MW compressor station, which is connected to a large piping system, both designed and
[...] Read more.
At Leibniz University of Hannover, Germany, a new turbomachinery test facility has been built over the last few years. A major part of this facility is a new 6 MW compressor station, which is connected to a large piping system, both designed and built by AERZEN. This system provides air supply to several wind tunnel and turbomachinery test rigs, e.g., axial turbines and axial compressors. These test rigs are designed to conduct high-quality aerodynamic, aeroelastic, and aeroacoustic measurements to increase physical understanding of steady and unsteady effects in turbomachines. One primary purpose of these investigations is the validation of aerodynamic and aeroacoustic numerical methods. To provide precise boundary conditions for the validation process, extremely high homogeneity of the inflow to the investigated experimental setup is imminent. Thus, customized settling chambers have been developed using analytical and numerical design methods. The authors have chosen to follow basic aerodynamic design steps, using analytical assumptions for the inlet section, the “mixing” area of a settling chamber, and the outlet nozzle in combination with state-of-the-art numerical investigations. In early 2020, the first settling chamber was brought into operation for the acceptance tests. In order to collect high-resolution flow field data during the tests, Leibniz University and AERZEN have designed a unique measurement device for robust and fast in-line flow field measurements. For this measurement device, total pressure and total-temperature rake probes, as well as traversing multi-hole probes, have been used in combination to receive high-resolution flow field data at the outlet section of the settling chamber. The paper provides information about the design process of the settling chamber, the developed measurement device, and measurement data gained from the acceptance tests.
Full article
(This article belongs to the Special Issue Selected Papers from the 10th EVI-GTI International Conference on Gas Turbine Instrumentation)
►▼
Show Figures
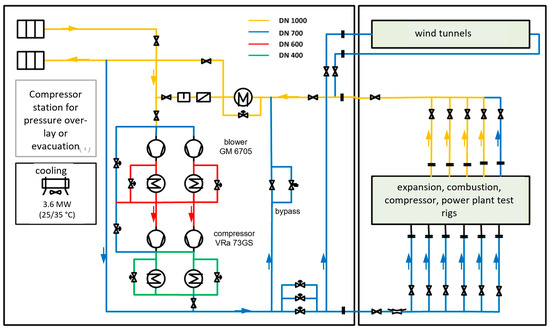
Figure 1
Open AccessTechnical Note
Verification of the Gage Factor of a High-Temperature Strain Gage for the Dynamic Testing of Gas Turbines
by
Oleksii Podobied, Ihor Vernyhora and Oleksii Kulikov
Int. J. Turbomach. Propuls. Power 2024, 9(3), 30; https://doi.org/10.3390/ijtpp9030030 - 20 Sep 2024
Abstract
This paper presents an analysis of factors causing the change in the real gage factor of high-temperature strain gages installed with ceramic cements. A calibration tool to mimic the load on the strain gage during the testing of gas turbines and to determine
[...] Read more.
This paper presents an analysis of factors causing the change in the real gage factor of high-temperature strain gages installed with ceramic cements. A calibration tool to mimic the load on the strain gage during the testing of gas turbines and to determine the real gage factor is described. Calibration data obtained for two samples of nickel–chromium strain gages and two samples of iron–chromium–aluminum strain gages are given and analyzed.
Full article
(This article belongs to the Special Issue Selected Papers from the 10th EVI-GTI International Conference on Gas Turbine Instrumentation)
►▼
Show Figures
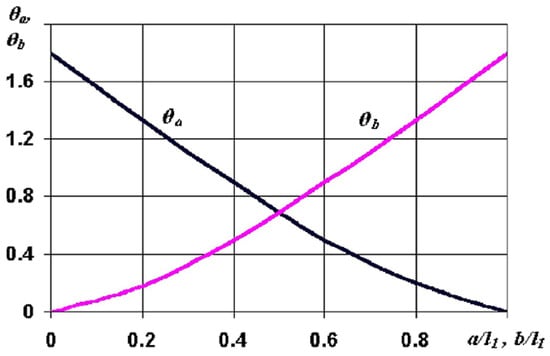
Figure 1
Open AccessArticle
Analysis and Prediction of the Stability Limit for Centrifugal Compressors with Vaneless Diffusers
by
Xavier Flete, Nicolas Binder, Yannick Bousquet, Viviane Ciais, Sandrine Cros and Nicolas Poujol
Int. J. Turbomach. Propuls. Power 2024, 9(3), 29; https://doi.org/10.3390/ijtpp9030029 - 5 Aug 2024
Abstract
►▼
Show Figures
A numerical study was conducted to identify the mechanisms involved in the destabilisation of centrifugal compressors with vaneless diffusers. A stability analysis—carried out on the rotating and fixed parts of the studied machines—showed that the vaneless diffuser is a limiting component at a
[...] Read more.
A numerical study was conducted to identify the mechanisms involved in the destabilisation of centrifugal compressors with vaneless diffusers. A stability analysis—carried out on the rotating and fixed parts of the studied machines—showed that the vaneless diffuser is a limiting component at a low mass flow rate. It was demonstrated that the reorganisation of stall patterns into recirculation in the inducer stabilises the impellers’ flow fields. As the destabilisation of vaneless diffusers has been a recurrent topic in the literature, many models have shown that it is the inlet-flow angle that drives the loss of stability. Models from the literature have estimated critical angle values using the geometry of the diffuser. Thus, for a given stage, expressing the diffuser inlet-flow angle as a function of the mass flow rate allows one to estimate its stability limit. However, this law needs to be calibrated to consider each compressor’s geometrical and aerodynamic specificities. This calibration can be achieved through single-passage steady simulations performed at stable operating points with high mass flow rates. With this methodology, a designer can estimate the stability limit of a centrifugal compressor with a vaneless diffuser from single-passage RANS calculations.
Full article
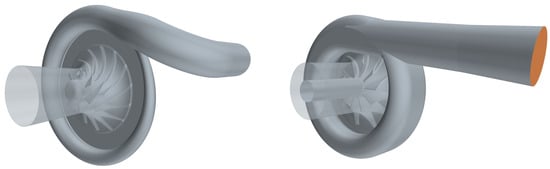
Figure 1
Highly Accessed Articles
Latest Books
E-Mail Alert
News
Topics

Conferences
Special Issues
Special Issue in
IJTPP
Advances in Industrial Fan Technologies
Guest Editors: Massimo Masi, Thomas CarolusDeadline: 30 September 2025