Research on the Analysis of Residual Stress in Heat Treatment of Bellows Using ABAQUS
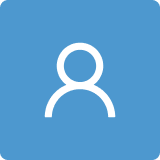
Round 1
Reviewer 1 Report
Comments and Suggestions for AuthorsThe manuscript describes a thermomechanical analysis of a bellows structure, including experimental result sand the simulation using Abaqus. The manuscript should be accepted for publication subject to the following minor updates:
- Manuscript Outline to be included at the end of Introduction Section;
- The authors should replace ideal with improved or desired material properties near line144;
- The authors should add scale bars in Figures 4 and Figure 5
- Near line 150 – the authors refer to fewer defects, but it is not clear relative to what;
- Add “Firstly” at the beginning of the sentence, before bellows in line 157;
- Add coordinate system in Figure 7 and all other simulation results;
- Add a legend to the diagrams in Figure 10, Figure 11 and elsewhere – what different lines in the diagram exactly represent;
- The authors should describe how the heating and cooling are defined in the FEM simulations, which is the main shortcoming of the methodology presented;
Author Response
1) Manuscript Outline to be included at the end of Introduction Section.
Reply 1): we thank the reviewer for the suggestion. Following reviewer’s suggestion, we have carefully checked and corrected for writing errors, and including some inappropriateness of expression. The changes have been highlighted in red color in the paper. The details are as follows:
-page 2, “Therefore, this study is based on ABAQUS finite element simulation software, using experimental and simulation curve processing analysis methods to analyze the residual stress and deformation of bellows after heat treatment, and to study the trend and distribution law of residual stress under different cooling times” has been revised as “In order to deeply analyze the distribution of residual stress in bellows after heat treatment, as well as the variation law of these stresses under different cooling times, we constructed a numerical model. This model not only considers the unique properties of the material, but also fully combines the geometric characteristics of the bellow. Through the operation and analysis of this model, we successfully obtained a detailed distribution of the residual stress present in of bellows after undergoing heat treatment. This achievement not only reveals the complexity and diversity of stress distributions in bellows during heat treatment; but also provides valuable data support for subsequent research. At the same time, the model also simulated the changes in the residual stress of the bellows under different cooling times. This simulation process enables us to directly observe the specific law of the influence of cooling time on residual stress, providing a powerful theoretical basis for optimizing heat treatment processes and reducing residual stress in relation to bellows”.
2) The authors should replace ideal with improved or desired material properties near line144.
Reply 2): Thank you for your comment. Based on the suggestions of the reviewers, we would like to demonstrate the metallographic diagram of the bellow before and after heat treatment through metallographic experiments to ensure that readers can clearly observe the significant changes in metallographic structure before and after heat treatment. Therefore, we have conducted a more detailed and in-depth analysis of the metallographic problem of the bellow and optimized and improved the metallographic diagram.
-page 5, “As shown in Figure 4, the metallographic austenite of the bellows after heat treatment is relatively less. The heat treatment parameters can be adjusted according to the changes in the metallographic diagram to obtain ideal material properties” has been revised as “As shown in Figure 4, the observation results of the metallographic structure show that after undergoing heat treatment, the internal structure of the bellow significantly trans-forms into austenite. Austenite, as an excellent microstructure, not only endows bellows with excellent plasticity and toughness, but the formation of austenite also significantly improves the corrosion resistance of bellows. This transformation means that bellows can withstand significant deformation without being easily broken in complex and ever-changing working environments, greatly enhancing their structural stability and reliability”.
3) The authors should add scale bars in Figures 4 and Figure 5.
Reply 3): We appreciate the reviewer's suggestions. Based on the feedback from the reviewers, we have added rulers to Figures 5 and 6 and made the following modifications.
- page 5, Change Figure 4 to:
(a) Preheat treatment (b) After heat Treatment
Figure 4. Metallographic structure before and after heat treatment.
-page 6, Change Figure 5 to:
Figure 5. Scanning image of the metal outer surface of the corrugated tube.
4) Near line 150 – the authors refer to fewer defects, but it is not clear relative to what.
Reply 4): Thank you for your suggestion. We agree with the reviewer's suggestion, but our description is not appropriate. The fewer defects described in this article are determined by observing the high surface flatness and good surface quality of the corrugated pipe through the Hikvision array camera group, thus indicating that the surface defects of the corrugated pipe are relatively few.
-page 5, “Through the Hikvision array camera group, combined with optical cameras and im-age processing software, as shown in Figure 5, it can be seen that the bellows formed by two spinning processes has good surface quality, fewer defects, and higher accuracy.” has been revised as “Using the Hikvision array camera setup, along with optical cameras and image processing software, as illustrated in Figure 5, it is evident that the corrugated tube exhibits good smoothness and surface quality after undergoing two rounds of spinning and heat treatment”.
5) Add “Firstly” at the beginning of the sentence, before bellows in line 157.
Reply 5): Thank you for your suggestion. We agree with the reviewer's suggestion. Firstly, we added "Firstly" to the revised manuscript. Secondly, we polished the entire text in English, greatly improving the standardization of language and the readability of the article.
-page6, Firstly, the bellows were formed by welding steel plates into circular pipes, generating significant and complex residual stresses during the welding process;
6) Add coordinate system in Figure 7 and all other simulation results.
Reply 6): Thank you for the reviewer's suggestions. Your suggestion is very valuable. We have added a coordinate system in Figure 7 to help readers better understand the constraints on corrugated pipes during the simulation process. For the addition of other simulation results, they have been introduced in the following chapters, such as Figure 9, Figure 13, etc.
-page7, Change Figure 7 to:
Figure 7. Boundary condition.
7) Add a legend to the diagrams in Figure 10, Figure 11 and elsewhere – what different lines in the diagram exactly represent.
Reply 7): Thank you for the reviewer's suggestions. The curves in Figures 10 and 11 represent representative residual stresses in the axial direction. The experimental curves are represented below "Experimental", and the emulation results curves are represented below "Emulation". The text above the curve also provides relevant explanations.
8) The authors should describe how the heating and cooling are defined in the FEM simulations, which is the main shortcoming of the methodology presented.
Reply 8): Thank you for your suggestion. Regarding how to define heating and cooling in finite element simulation, we will refer to section 3.5 at the end of Chapter 3 In the "Simulation of Heat Treatment Conditions" section, detailed explanations have been added.
-Page 8, Additional parts, During the heating stage, the material properties are defined, and the thermal conductivity, coefficient of thermal expansion, Young's modulus, Poisson's ratio, and other parameters of the material are set, which are used to establish the thermal elastic constitutive relationship of the material. A heat conduction equation is established. Based on the heat conduction properties of materials and the geometric shape of the structure, a heat conduction equation was established to describe the temperature field distribution of the structure. To define the boundary conditions and loading conditions, the heating boundary conditions were set; the outer surface of the bellow was subjected to a high temperature, and the inner surface was subjected to room temperature. Concerning mesh partitioning, the structure was discretized into a finite element mesh.
During the cooling stage, the cooling conditions are defined as follows: the boundary conditions for cooling are determined, the boundary temperature of the structure is changed, and the cooling process is simulated. For the numerical solution, the same finite element model and solution method are used to solve the temperature field during the cooling process.
Author Response File: Author Response.pdf
Reviewer 2 Report
Comments and Suggestions for AuthorsThe study is a standard finite element model with little or no scientific relevance or interest.
The scientific or technological problem is not well described. References in the introduction do not connect to the scope of the article.
2.2.1. Measurement principle: Very peculiar choice of references. Use work from the original source or standard sources. The residual stress measurements are not satisfactory described.
2.3. Micro organization and macro structure: Not possible to understand.
3. Construction of finite element model for bellows: Not a very good description of the model and boundary conditions. Very difficult to understand, seems to be a description of how Solidworks was used.
3.4. Theoretical Model: The Johnson-Cook viscoplastic constitutive model is used without motivation, the equation is not correct, the description of the parameters wrong, and citation should be done to the original source. How was the parameters in the model determined?
4. Analysis of numerical simulation results: Conclusions are not correct, ex “Therefore, it can be con- 241 cluded that the longer the cooling time, the faster the residual stress decreases.” There is no evidence that the cooling time influences the rate of decrease of residual stresses.
5. Conclusions: (1) is not a conclusion. The other conclusions are just plain results from the simulations.
Comments on the Quality of English LanguageEnglish have to be improved for clarity and meaning.
Author Response
Authors’ Replies to Reviewer #2:
1) The study is a standard finite element model with little or no scientific relevance or interest. The scientific or technological problem is not well described. References in the introduction do not connect to the scope of the article.
Reply 1): Thank you very much for your careful review and valuable feedback on our research. We fully understand your concerns regarding the scientific relevance and problem description of the finite element model in this study.
Regarding the issue of unclear description of technical issues, we acknowledge that the description of specific technical details and methods in the paper may not be detailed enough. We will further supplement and improve this section to ensure that readers can clearly understand the research methods and models we have adopted. In this article, we first reviewed the relevant measurement methods and research on residual stress, with a particular emphasis on the importance of residual stress distribution. Although the measurement and analysis of residual stress have received widespread attention in multiple fields and materials, there is relatively little research on the measurement and distribution of residual stress in bellows, a specific structural component. Therefore, this article focuses on the specific object of bellows and analyzes in depth the relevant research on residual stress from a measurement perspective. By systematically reviewing and evaluating existing measurement methods, we aim to provide valuable references and insights for the accurate measurement and distribution of residual stress in bellows.
We attach great importance to your opinions and suggestions, and will carefully revise and improve the paper based on these suggestions. We look forward to further efforts to better meet academic requirements and contribute to research in related fields.
Related citations in this article.
[7] Bin W, Hongliang M, Rongbo L, et al. The single effect of microstructure, residual strain and geometric structure on the stress corrosion cracking behavior of scratched alloy 690TT[J]. Corrosion Science, 2024,227:111709.
[8] Lu W, Sun J, Su H, et al. Experimental research and numerical analysis of welding residual stress of butt welded joint of thick steel plate[J]. Case Studies in Construction Materials, 2023,18:e1991.
[9] Guo H, Huang A, Xiong W, et al. Finite Element Simulation and Residual Stress Analysis of the Whole Process of Metal Bellows Forming[J]. Journal of materials engineering and performance, 2024,33: 3758-3769
[10] Mai C, Xue H L Z, Bao S A X Z. Influence of Interlayer Temperature and Welding Sequence on the Temperature Distribution and Welding Residual Stress of the Saddle-Shaped Joint of Weldolet-Header Butt Welding[J]. Materials, 2021,14: 5980
2) 2.2.1. Measurement principle: Very peculiar choice of references. Use work from the original source or standard sources. The residual stress measurements are not satisfactory described.
Reply 2): Thank you for your comment. We agree with the reviewer's comments and have carefully checked some of the expressions. We have extended the description of residual stress measurement to address the issue of unclear description in residual stress measurement.
-page 4,5Additional parts, X-rays are electromagnetic waves with short wavelengths that can penetrate a certain thickness of material and undergo diffraction in crystals. When X-rays are irradiated on the surface of a crystal, the grains inside will undergo scattering. During this scattering process, X-rays interact with atoms in the crystal, causing them to change direction. This phenomenon is called diffraction. The angle of diffraction is closely related to the crystal structure and lattice parameters. When the crystal is affected by residual stress, the plane spacing of the crystal plane will change. This change will cause a corresponding shift in the diffraction angle of the incident X-ray. By measuring the change in diffraction angle and combining it with the Bragg equation, the magnitude and distribution of residual stress in the material can be inferred. During the measurement process, it is necessary to accurately control the incident angle and diffraction angle to-conduct effective data analysis and processing.
3) 2.3. Micro organization and macro structure: Not possible to understand.
Reply 3): Thank you for the reviewer's suggestions. In response to the issue of unclear description of microstructure and macroscopic structure, we have enriched and improved the pronunciation, increased the scale, and highlighted certain parts in detail.
-page5, Change Figure 4 to:
(a) Preheat treatment (b) After heat Treatment
Figure 4. Metallographic structure before and after heat treatment.
-page 6, Change Figure 5 to:
Figure 5. Scanning image of the metal outer surface of the corrugated tube.
-page 5, “As shown in Figure 4, the metallographic austenite of the bellows after heat treatment is relatively less. The heat treatment parameters can be adjusted according to the changes in the metallographic diagram to obtain ideal material properties” has been revised as “As shown in Figure 4, the observation results of the metallographic structure show that after undergoing heat treatment, the internal structure of the bellow significantly trans-forms into austenite. Austenite, as an excellent microstructure, not only endows bellows with excellent plasticity and toughness, but the formation of austenite also significantly improves the corrosion resistance of bellows. This transformation means that bellows can withstand significant deformation without being easily broken in complex and everchanging working environments, greatly enhancing their structural stability and reliability”.
-page 5, “Through the Hikvision array camera group, combined with optical cameras and im-age processing software, as shown in Figure 5, it can be seen that the bellows formed by two spinning processes has good surface quality, fewer defects, and higher accuracy.” has been revised as “Using the Hikvision array camera setup, along with optical cameras and image processing software, as illustrated in Figure 5, it is evident that the corrugated tube exhibits good smoothness and surface quality after undergoing two rounds of spinning and heat treatment.”.
4) 3. Construction of finite element model for bellows: Not a very good description of the model and boundary conditions. Very difficult to understand, seems to be a description of how Solidworks was used.
Reply 4): Thank you for the reviewer's suggestions. We believe that your suggestions are very valuable. To address the issue of unclear description of the model and boundary conditions, we have made the following improvements.
-page 6,For section 3.1 We have simplified the description of the construction of the corrugated pipe model in the "Geometric model" section. Solidworks is a commonly used modeling software, and we will not elaborate on the process of model construction here. “By using Solidworks 3D modeling to restore the shape and structure of bellows, the accuracy of the 3D model directly affects the final result of simulation. The structural parameters of the bellows are shown in Table 3 above, 3D modeling diagram are shown in Figure 6.” has been revised as “Referring to the structural parameters of the bellow provided in Table 3, we constructed a three-dimensional model as shown in Figure 6.
-page 7, In response to the problem of fuzzy description of boundary conditions, we have revised the textual description of boundary conditions and added a schematic diagram of boundary condition coordinates, so that readers can clearly understand the position and method of boundary constraints. “All steps consider geometric nonlinearity and use automatic time increments. In these three analysis steps, the constraints are all on the end face of the bellow. The actual process of the bellow heat treatment process is achieved by constraining "displacement/rotation" to control the radial deformation of the bellow. The definition and position of the constraints for the bellow are shown in Table 4 and Figure 7. In addition, these constraint definitions will not change during heat treatment.” has been revised as “The analysis steps all consider geometric nonlinearity and use fixed time increments in the increments. The actual process of corrugated pipe heat treatment is achieved by controlling the radial deformation of the corrugated pipe by constraining "displacement/rotation". In these three analysis steps, geometric constraints are on the end faces on both sides of the corrugated pipe. The specific constraint definitions are shown in Table 4 and Figure 7, and geometric constraints are implemented throughout the entire simulation process.”.
-page7, Change Figure 7 to:
Figure 7. Boundary condition.
5) 3.4. Theoretical Model: The Johnson-Cook viscoplastic constitutive model is used without motivation, the equation is not correct, the description of the parameters wrong, and citation should be done to the original source. How was the parameters in the model determined?
Reply 5): Thank you for your valuable suggestion. The formula issue is a major issue that we have encountered. Thank you for your careful review to help us identify this issue. We have provided a detailed explanation of the JC constitutive model and corrected any errors in the formula.
-page 7, 8Additional parts , The J-C constitutive model comprehensively considers the relationship between rheological stress and strain, strain rate, and temperature, and can meet the simulation mate-rial requirements under various conditions. The J-C constitutive parameter in ABAQUS is defined by hardening in material plasticity, where "Transition Temperature" refers to the yield stress not affected by temperature changes at or below this temperature. When fitting temperature parameters, the turning point of the temperature rheological stress curve can be used to determine and replace the room temperature parameters in the original model, thereby improving the accuracy of the model.
-page 8, “
|
(2) |
In the formula: A and B are strain correlation coefficients; n is the hardening index; c is the strain rate correlation coefficient; is the equivalent plastic strain rate; is the reference value for strain rate; m is the thermal softening coefficient of the material; and for room temperature and material melting point.” has been revised as
|
(2) |
In the formula: represents the rheological stress, A indicates the yield stress at the reference temperature and strain rate, B denotes the strain hardening coefficient of the material, ε represents the plastic strain, n denotes the strain hardening index of the material , indicates the strain rate, represents the reference strain rate, T denotes the test temperature, and and relate to room temperature and material melting point.
6) 4. Analysis of numerical simulation results: Conclusions are not correct, ex “Therefore, it can be con- 241 cluded that the longer the cooling time, the faster the residual stress decreases.” There is no evidence that the cooling time influences the rate of decrease of residual stresses.
Reply 6): Thank you for the valuable suggestions from the reviewer. We have made the following modifications to address the conclusion issue.
-page 9, “Therefore, it can be concluded that the longer the cooling time, the faster the residual stress decreases.” has been revised as “Therefore, it can be concluded that the longer the cooling time, the greater the reduction in residual stress”.
7) 5. Conclusions: (1) is not a conclusion. The other conclusions are just plain results from the simulations.
Reply 7): Thank you for the reviewer's suggestions. We have made extensive revisions and polishing to the conclusion, as follows.
-page 14, “(1) Establish a finite element analysis model for residual stress in stainless steel bel-lows heat treatment based on ABAQUS, and explore the distribution trend of residual stress and deformation of bellows under different cooling times during the heat treatment cooling stage, as well as after heat treatment.” has been revised as “A residual stress analysis model for stainless steel bellows during heat treatment was constructed using ABAQUS software. The distribution trends of residual stress and de-formation in bellows during the heat treatment cooling stage and after heat treatment un-der different cooling time conditions were explored”.
-page 14 “(3) The analysis of experimental and simulation results shows that the residual stress at the peak of the bellow in the middle position is significantly lower after heat treatment, and the distribution trend of residual stress at the valley is more uniform.” has been revised as “(3) The analysis of experimental and simulation results shows that the peak residual stress of the bellow in the middle position is significantly reduced after heat treatment, and the distribution trend of residual stress in the valley is more uniform. This helps to reduce the risk of stress concentration and stress corrosion cracking, thereby improving the fatigue life of bellows”.
-page 14 “(4) The different cooling times of heat treatment have a certain impact on the defor-mation of bellows, but the effect is relatively small. As the cooling time increases, the de-formation decreases. Starting from 300 seconds, the deformation decreases by 1.748%, 0.794%, 0.338%, 0.258%, and 0.142% for each additional 300 seconds on the original basis. The deformation distribution at the ridge and valley of the bellows along the axis direction is relatively uniform.” has been revised as “(4) The different cooling times of heat treatment have a certain impact on the defor-mation of bellows, but the impact is relatively small. As the cooling time increases, for-mation decreases. Starting from 300 seconds, for every additional 300 seconds on the original basis, the deformation decreases by 1.748%, 0.794%, 0.338%, 0.258%, and 0.142%, respectively. The deformation at the peaks and valleys of the bellow is relatively evenly distributed along the axis direction, avoiding the structural instability caused by local stress concentration, making the bellow more resistant to external pressure and impact during use, thus extending its service life”.
8) English have to be improved for clarity and meaning.
Reply 8): Thank you for carefully reviewing our manuscript and providing valuable feedback. We have carefully considered your concerns about the clarity and meaning of our writing, and we appreciate your guidance in this regard. In order to improve the clarity of our writing, we will reread the relevant chapters of the paper and polish them to ensure a clearer explanation of scientific motivation, goals, and contributions. We are committed to making necessary revisions to our manuscript to ensure that it meets the standards of clarity, conciseness, and scientific rigor. We appreciate the time and effort you have invested in our work and look forward to further discussions to improve our documents.
Author Response File: Author Response.pdf
Reviewer 3 Report
Comments and Suggestions for AuthorsThe prinicpal results were presented on Figures 8 and 12.
The first subject is the evaluation of the residual stresses: "The distribution of residual stress in bellows is mainly caused by uneven displacement and expansion. Figure 8 shows the bar graph of residual stress reduction rate under different cooling times. It can be observed that the residual stress reduction rate increases with the increase of cooling time. Figure 9 shows the residual stress distribution cloud map under different cooling times, indicating a significant residual stress at the ridge. After data calculation, it can be concluded that in the five cooling time zones of 300s~600s, 600s~900s, 900s~1200s, 1200s~1500s, and 1500s~1800s, the average residual stress changes per 100s are 5.35MPa, 5.32MPa, 5.47MPa, 5.70MPa, and 5.80MPa. Therefore, it can be concluded that the longer the cooling time, the faster the residual stress decreases."
Later of the page 10 one reads: "Through finite element simulation of heat treatment cooling conditions, the deformation of bellows under different cooling rates was obtained. Table 6 shows that even though the deformation change at different cooling rates is negligible, there is still a certain pattern, that is, as the cooling rate slows down, the displacement deformation also slows down. As shown in Figure 12, with the increase of cooling time, the degree of deformation gradually decreases."
On my opinion, the with the increase of cooling time, the degree of RESIDUAL deformation gradually decreases. The TRUE TOTAL deformation will INCREASE with with the increase of cooling time. The authors must properly and unambiguously define, what deformations were evaluated.
The type of the finite element mesh on Fig. 7 seem to be very coarse for an accurate evaluation of the residual stresses. The reviewer strongly recommneds to use the rectangular mesh of the midsurface, or a hexaedral mesh of the voluminar body of revolution. Moreover, a high order of finite elements must be used for the simulation. The isorparametric quadratic elements are preferrable for the proper simulation.
The detailed review of the methods and of the overall presentation will be provided after the answering of the prinicpal question.
Comments on the Quality of English LanguageThe definitions of the residial stresses and strains must be given explicitly. Without the proper definitions the presented results could not be uniquely identified.
Author Response
1) The first subject is the evaluation of the residual stresses: "The distribution of residual stress in bellows is mainly caused by uneven displacement and expansion. Figure 8 shows the bar graph of residual stress reduction rate under different cooling times. It can be observed that the residual stress reduction rate increases with the increase of cooling time. Figure 9 shows the residual stress distribution cloud map under different cooling times, indicating a significant residual stress at the ridge. After data calculation, it can be concluded that in the five cooling time zones of 300s~600s, 600s~900s, 900s~1200s, 1200s~1500s, and 1500s~1800s, the average residual stress changes per 100s are 5.35MPa, 5.32MPa, 5.47MPa, 5.70MPa, and 5.80MPa. Therefore, it can be concluded that the longer the cooling time, the faster the residual stress decreases."
Reply 1): Thank you for the valuable suggestions from the reviewer. We have made some modifications to this paragraph.
-page 9, “Therefore, it can be concluded that the longer the cooling time, the faster the residual stress decreases.” has been revised as “Therefore, it can be concluded that the longer the cooling time, the greater the reduction in residual stress”.
2) Later of the page 10 one reads: "Through finite element simulation of heat treatment cooling conditions, the deformation of bellows under different cooling rates was obtained. Table 6 shows that even though the deformation change at different cooling rates is negligible, there is still a certain pattern, that is, as the cooling rate slows down, the displacement deformation also slows down. As shown in Figure 12, with the increase of cooling time, the degree of deformation gradually decreases."
On my opinion, the with the increase of cooling time, the degree of RESIDUAL deformation gradually decreases. The TRUE TOTAL deformation will INCREASE with with the increase of cooling time. The authors must properly and unambiguously define, what deformations were evaluated.
Reply 2): Thank you for your suggestion. We have made some modifications to address this issue.
-page 11, “As shown in Figure 12, with the increase of cooling time, the degree of de-formation gradually decreases.” has been revised as “as cooling time increases, the degree of residual deformation gradually decreases. As cooling time increases, total deformation increases.
3) The type of the finite element mesh on Fig. 7 seem to be very coarse for an accurate evaluation of the residual stresses. The reviewer strongly recommneds to use the rectangular mesh of the midsurface, or a hexaedral mesh of the voluminar body of revolution. Moreover, a high order of finite elements must be used for the simulation. The isorparametric quadratic elements are preferrable for the proper simulation.
Reply 3): Thank you very much for your detailed review and valuable suggestions on our research work. We attach great importance to your suggestions on finite element mesh types and high-order finite element simulation methods, and have conducted in-depth discussions and analysis on these suggestions.
In the simulation process of evaluating residual stress, we did consider various mesh types. However, after detailed simulation testing and comparative analysis, we found that under the current research conditions, the current grid type is able to accurately capture the distribution and changes of residual stress. Although rectangular meshes of intermediate surfaces or hexahedral meshes of volume rotations may have higher accuracy in some cases, in our model, these mesh types may introduce additional complexity and uncertainty, thereby affecting the reliability of simulation results.
We agree that high-order finite element simulation methods have higher accuracy and better convergence in theory. However, in practical applications, the use of higher-order elements can also lead to a significant increase in computational costs, especially in our model. Considering the limitations of computing resources and the efficiency of simulation time, we have decided to use lower order elements for simulation at the current stage. Of course, in future research, we will consider using high-order elements for simulation when conditions permit, in order to further improve the accuracy and reliability of simulation results.
Finally, we understand the advantages of the use of isoparametric quadratic elements, but considering the specific conditions and needs of the current study, we believe that the use of is oparametric quadratic elements at the current stage is not the optimal choice. We will continue to monitor the research progress in this field and make corresponding adjustments and optimizations according to actual needs in future work.
Thank you again for your suggestion. We will continue to work hard to improve and perfect our research work. If you have any further questions or suggestions, please feel free to contact us at any time.
4) Moderate editing of English language required
Reply 4): Thank you for carefully reviewing our manuscript and providing valuable feedback. We have carefully considered your concerns about the clarity and meaning of our writing, and we appreciate your guidance in this regard. In order to improve the clarity of our writing, we will reread the relevant chapters of the paper and polish them to ensure a clearer explanation of scientific motivation, goals, and contributions. We are committed to making necessary revisions to our manuscript to ensure that it meets the standards of clarity, conciseness, and scientific rigor. We appreciate the time and effort you have invested in our work and look forward to further discussions to improve our documents.
Author Response File: Author Response.pdf
Reviewer 4 Report
Comments and Suggestions for AuthorsThe paper addresses a problem with practical interest. Results are described in details. Some additional figure showing the extend of plastification and remaining stresses on the speciment for various cases of treatment would help.
Author Response
The paper addresses a problem with practical interest. Results are described in details. Some additional figure showing the extend of plastification and remaining stresses on the speciment for various cases of treatment would help.
Reply ): Thank you very much for your valuable review comments. We are honored by your attention to the issues discussed in this article and your recognition of the detailed results description. Your suggestion to introduce additional numbers to demonstrate plasticization elongation and residual stress under different processing conditions greatly enhances the persuasiveness and practicality of this article. These specific digital data not only help readers to have a more intuitive understanding of the performance changes of corrugated pipes during heat treatment, but also provide valuable references for research and application in related fields. We sincerely appreciate your recognition of the quality of this article and look forward to receiving your guidance and assistance in the future. Thank you again for your review work. Your support is of great significance to us.
Author Response File: Author Response.pdf
Round 2
Reviewer 2 Report
Comments and Suggestions for AuthorsThe citations have to be checked and changed.
Author Response
1) The citations have to be checked and changed.
Reply 1): We appreciate the reviewer's suggestions. Based on the suggestions of the reviewers, we carefully checked the references in the citations, deleted some irrelevant literature, and added some more relevant literature to this article. These changes have been highlighted in blue in the paper. Specifically, as follows:
-page 1,2
Deleted citation.
Mai et al. [11] established a three-dimensional finite element model and suggested that there is a significant stress gradient on the fusion line on both sides of the weld seam, and high or low interlayer temperatures can generate significant residual stresses. Jiang et al. [12] analyzed the influence of high energy ultrasound on the welding process and the surface temperature field after welding, and the results showed that the tensile strength of the adjustment group during welding and the thermal adjustment group after welding was the best. Xiao et al. [13] used a combination of experimental and numerical simulation methods to study the distribution of welding residual stress in the repair area when using different welding repair methods.
Studying of the distribution law of residual stress in depth is of great significance, and researchers have summarized a series of effective methods for studying residual stress. Sun et al. [14] investigated the formation mechanism of residual stress in a hot-rolled strip and how to control it, establishing a coupled analytical model for residual stress. Li et al. [15] proposed a residual stress field inference method based on a data causal knowledge fusion model, which compensates for the shortcomings of pure da-ta-driven models. Zhou et al. [16] proposed a method for reverse engineering the residual stress distribution of Ti-6Al-4V end milling titanium alloy based on thin plate defor-mation measurements. Ying et al. [17] established a unit cell model for the typical one-dimensional periodicity of U-shaped bellow structures to achieve equivalent analysis of the overall mechanical properties of bellows.
-page15
Deleted literature.
[11] Mai C, Xue H L Z, Bao S A X Z. Numerical Simulation and Experimental Verification of Residual Stress in the Welded Joints of Weldolet-Branch Pipe Dissimilar Steels[J]. Materials, 2022,15: 1044.
[12] Xiaowei Jiang C X, Jing dong L, Jiang quan L A L W. A Study on the Ultrasonic Regulation of the Welding Performance and Residual Stress of 316L Stainless Steel Pipes[J]. Materials, 2022,15: 6255.
[13] Xin Xiao Q L M H. Effect of Welding Sequence and the Transverse Geometry of the Weld Overlay on the Distribution of Residual Stress in the Weld Overlay Repair of T23 Tubes[J]. Metals, 2021,11: 568.
[14] Hao W, Jie S, Wen P, et al. Analysis of flatness and critical crown of hot-rolled strip based on thermal–mechanical coupled residual stress analytical model[J]. Applied Mathematical Modelling, 2017,26(11):5385-5395.
[15] Li D, Li Y, Liu C, et al. An online inference method for condition identification of workpieces with complex residual stress distributions[J]. Journal of Manufacturing Systems, 2024,73: 192-204.
[16] Zhou J, Qi Q, Liu Q, et al. Determining residual stress profile induced by end milling from measured thin plate deformation[J]. Thin-Walled Structures, 2024,200: 111862.
[17] Ying X, Yan J, Zhang K, et al. Study on equivalent mechanical properties of U-shaped bellows based on novel implementation of asymptotic homogenization method[J]. Marine Structures, 2024,96:103622.
-page1,2
Newly added citations.
Heat treatment has a significant impact on residual stress in steel materials, and ap-propriate heat treatment conditions can effectively reduce or regulate residual stress, thereby improving material properties and crack propagation behavior. Jonan et al. [11] investigated the effect of heat treatment on residual stress in welded lap steel specimens, revealing that when heat treatment is performed at high temperatures, the initial residual stress value can sometimes decrease by more than 50%. Jae et al. [12] investigated the effect of heat treatment conditions on residual stress in laser powder bed melting of martensitic aged 18Ni-300 steel. The results showed that when the cantilever specimen was subjected to aging heat treatment, deformation was significantly reduced, indicating a reduction in inherited residual stress. Ji et al. [13] analyzed the formation and evolution mechanism of residual stress during solid solution heat treatment of 316L/Q235B composite plates, as well as the influence of different factors on residual stress. The results indicate that the bending stress caused by interlayer thermal stress is the main factor for the formation of residual stress in the solution heat treatment process of composite plates. Fan et al. [14] investigated the effect of residual stress caused by three different cooling methods during heat treatment on the crack propagation behavior of GH4169 discs. The results showed that the AJC method suppresses the crack surface opening by introducing residual compressive stress near the center hole surface, thereby improving the crack propagation life of the disc.
-page15
Newly added literature.
[11] Joana K R, José M M, Weimin G, et al. Quantification of Residual Stress Relief by Heat Treatments in Austenitic Cladded Layers[J]. Materials, 2022,15(4):1364-1364.
[12] Jae Hyun Yu Q J K H. Influence of Several Heat Treatments on Residual Stress in Laser Powder Bed-Fused Maraging 18Ni-300 Steel[J]. Applied sciences, 2023.13(11):6572.
[13] Ji X, Zhao Z, Sun C, Liu X, Wang R, Su C. Study on Residual Stress Evolution Mechanism and Influencing Factors of 316L/Q235B Composite Plate during Solution Heat Treatment[J]. Crystals, 2023, 13: 436.
[14] Menglong F, Chuanyong C, Haijun X, et al. Effect of Residual Stress Induced by Different Cooling Methods in Heat Treatment on the Fatigue Crack Propagation Behaviour of GH4169 Disc
Reviewer 3 Report
Comments and Suggestions for AuthorsThe script have been improved and could be considered for publication
Author Response
The script have been improved and could be considered for publication
Reply ): Thank you very much for your valuable review comments. The paper has adopted the editorial service recommended by the journal, and the writing level of the entire text has been improved.
Author Response File: Author Response.pdf