Influence of Welding Parameters and Filler Material on the Mechanical Properties of HSLA Steel S960MC Welded Joints
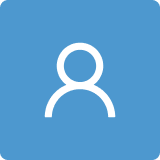
Round 1
Reviewer 1 Report
Dear Authors,
I have carefully read the manuscript and found the it interesting from the point of view of practical industrial application. The base material used is weldable, but its weldability may be improved, which is of great significance for modern production facilities. Characterization techniques are adequate, however, some improvements in presentation should be made in order to make the paper more readable:
lines 34-36 please rewrite, the sentence "To obtain sufficient..." is unclear
lines 40, 41, the sentence "Therefore,..." - can not say "we can achieve", but rather "it can be achieved" use passive form...There are more examples as this throughout the manuscript.
line 46: not "grain finesse", but "grain refinement"
line 97: please explain what is t8/5
line 124: not "investigated", rather "studied", or just avoid this and start the sentence with "Two types of filler..."
line 135: Cr content is rather low, I would replace it with Mo, which is more influential at these contents, or just add Mo in this list.
2.2 Welding procedure: please explain MCAW-S cooled in experimental part?
line 175: does this open circuit refer to tap water or?
line 198: why both mapping and linear hardness measurements were performed? Why selected mapping values were not used instead of separate linear measurements?
Figure 3: it is difficult to differentiate between curves and processes
lines 224-226: all experimental explanations belong to the experimental part, this is not the result
lines 270-271 referring to hardness before giving all hardness results is not appropriate. I suggest metallography to be moved after hardness.
Figure 6: choosing a different 240-260 HV color would avoid results confusion. More semi-dark blue color in 240-260 HV MCAW-S cooled specimen makes this specimen appear worse than it really is.
3.4 Tensile tests should come right after thermal cycle analysis, before metallography and hardness tests
Table 6: Was YS measured in weld metal or HAZ, if in HAZ, in which part of HAZ? How did you determine this? Did you assume these values refer to the area with the lowest hardness?
How was A measured? Is it also measured throughout the specimen? How were specimens cut? Perpendicular to the weld?
Please elaborate.
3.6 Soft Zone Characteristics - it is not characteristics, but rather properties
line 327: where the fracture occurs, should have been said in the tensile part
Table 7: it is confusing to give left side in the right column and right side in the left column
3.7:
giving formula would make the statements clearer
what is the point of dividing the width of the soft zone with the thickness of the welded material if all specimens were 3 mm thick?
Figure 9: these results should be given in the beginning of the results section. Why all macro sections were not shown?
line 396: "...significantly affected the negative impact... had a negative impact?
Overall, the paper is sound, but results and discussion section is a bit confusing, so this might be the biggest concern.
Thank you for giving me the opportunity to evaluate your work.
Author Response
Response to Reviewer 1 Comments
Dear reviewer,
Thank you very much for your valuable comments. I hope my answers and consequent article improvement will be sufficient. Please see the comments below, explaining each of your comments.
- lines 34-36: please rewrite, the sentence "To obtain sufficient..." is unclear
- We rewrote the sentence more clearly: "The mentioned strengthening mechanisms can be achieved through a thermo-mechanically controlled process."
- lines 40, 41, the sentence "Therefore,..." - can not say "we can achieve", but rather "it can be achieved" use passive form...There are more examples as this throughout the manuscript.
- Thank you for your advice. We checked the text and used passive form.
- line 46: not "grain finesse", but "grain refinement"
- line 97: please explain what is t8/5
- We added short explanation: “It was assumed that by reducing the heat input and time t8/5 (a cooling time between 800 °C and 500 °C), the soft zone would narrow and the strength would increase.”
- line 124: not "investigated", rather "studied", or just avoid this and start the sentence with "Two types of filler..."
- We removed the beginning of the paragraph and used the sentence you suggested.
- line 135: Cr content is rather low, I would replace it with Mo, which is more influential at these contents, or just add Mo in this list.
- We added Mo to the list.
- 2 Welding procedure: please explain MCAW-S cooled in experimental part?
- We added the sentence: “For MCAW-S, additional cooling marked as MCAW-S cooled was also used.” We also added information about MCAW-S cooled in the relevant part of the text: ”Water from the heat exchanger drained into the drain. The temperature was monitored by a thermocouple on the surface of the exchanger.”
- line 175: does this open circuit refer to tap water or?
- Yes, tap water flowed through the constructed heat exchanger and drained to the drain. The temperature was sensed by a thermocouple placed on the surface of the exchanger. This information was also added to the text.
- line 198: why both mapping and linear hardness measurements were performed? Why selected mapping values were not used instead of separate linear measurements?
- Firstly, we made linear hardness measurements that covered the entire sample (both HAZs and WM). Based on these measurements, we determined the width of both soft zones. Only after the tensile test, was the relevant soft zone determined (the one where the fracture occurred). Hardness maps, which were made as last, were made only in half profile on the relevant side of the weld. (Hardness maps were included in the experiment until the possible influence of the weld metal shape on the soft zone shape was demonstrated.)
- Figure 3: it is difficult to differentiate between curves and processes
- We tried to change the graph to make it more readable. We changed the X and Y axis, and also color of the curves for better contrast. We enlarged and moved the graph legend to increase the area of the graph.
- lines 224-226: all experimental explanations belong to the experimental part, this is not the result
- Thank you for notice. The text was edited.
- lines 270-271 referring to hardness before giving all hardness results is not appropriate. I suggest metallography to be moved after hardness.
- We have reordered the chapters as you recommended.
- Figure 6: choosing a different 240-260 HV color would avoid results confusion. More semi-dark blue color in 240-260 HV MCAW-S cooled specimen makes this specimen appear worse than it really is.
- We adjusted the color in the range of values 240-260 HV1. We hope, the way you expected.
- 4 Tensile tests should come right after thermal cycle analysis, before metallography and hardness tests
- We have reordered the chapters as you recommended.
- Table 6: Was YS measured in weld metal or HAZ, if in HAZ, in which part of HAZ? How did you determine this? Did you assume these values refer to the area with the lowest hardness?
- YS was measured based on the tensile test working diagram. Information about YS, testing procedure and the shape of specimens were edited in the text. Also all 5 figures of the fracture profile (Figure 5a-e) were added to the chapter Tensile test together with information about fracture location. After evaluating all the results, the values of YS cannot be referred to the area with lowest hardness. In all samples, YS was measured in the SCHAZ area. The largest decrease in hardness was recorded at the beginning of the ICHAZ area.
- How was A measured? Is it also measured throughout the specimen? How were specimens cut? Perpendicular to the weld? please elaborate.
- A was measured from the tensile test working diagram based on an extensometer. Major part of deformations was localized in the ICHAZ and SCHAZ areas, this is also referred in the text. Information about testing procedure and the shape of specimens were edited in the text.
- 6 Soft Zone Characteristics - it is not characteristics, but rather properties
- line 327: where the fracture occurs, should have been said in the tensile part
- All 5 figures of the fracture profile (Figure 5a-e) were added to the chapter “Tensile test” together with information about fracture location (all fractures occurred in SCHAZ area)
- Table 7: it is confusing to give left side in the right column and right side in the left column
- The mistake occurred while describing the columns, the soft zone width values were placed in the correct column. Thank you for your notice.
- 7: giving formula would make the statements clearer
- Equation was added to the text.
- what is the point of dividing the width of the soft zone with the thickness of the welded material if all specimens were 3 mm thick?
- Of course, in the case of using a base material with the same thickness, the XSZ conversion is not necessary. However, we proceeded from the assumption we mentioned in the introduction that the width of the soft zone itself, without taking into account the thickness of the material, is an irrelevant parameter. The XSZ parameter will make easier comparisons with other similar studies, in the case of a suitably chosen methodology for determining the width of the soft zone. We also used the relevant literature, where the XSZ was also taken as the main parameter for determining the influence of the soft zone on the strength of welds.
- Figure 9: these results should be given in the beginning of the results section. Why all macro sections were not shown?
- Chapter 3.5 was edited into: 3.5 Microstructural and Macrostructural Analysis. We added information and pictures of macrostructures. Therefore, we have removed the mentioned image. The information in the text that referred to the removed image now refers to the figures in chapter 3.5.
- line 396: "...significantly affected the negative impact... had a negative impact?
- Conclusions part was edited, including the mentioned sentence.
Author Response File: Author Response.pdf
Reviewer 2 Report
Dear Authors,
I have read your paper titled "Influence of Welding Parameters and Filler Material on the Mechanical Properties of HSLA steel S960MC Welded Joints", which presents very interesting investigations. Manuscript fulfils the aims and scope of journal, and can be considered for publishing after some minor improvements.
Introduction:
This section is well written. I have minor remark here
- As you stated in abstract, the cooling rate significantly affects the properties of welded joints - I fully agree. As it was stated in literature, the different cooling rate resulted in number of cold cracks in welded joint (e.g., 10.2478/adms-2014-0008 ). However, this information is missing in your paper.
Materials and Methods:
- Table 2 - please add information about carbon equivalent, which is one of factor allows to access the weldability of steel.
- Table 4 - I propose to preent units in different way - [mm/s] and [kJ/mm], it will be more readable.
- Have you used any requirements from relevant standards? If no, please describe why. If yes, please add relevant standards' numbers in section "2.3. Mechanical Testing and Microstructural Analysis".
Results and discussion:
- In the name of section move "d" to "D" - Results and Discussion.
- In my opinion you should discuss your results wider with results frm other articles. Please underline the most important advantatges of your work (e.g. relation cracks vs cooling rate).
- Fig. 3 - As you truely stated, the most important is t8/5. Following this, I propose to mark 500°C in the figure.
- Line 294 - avoid space in bracket.
- Except hardness mapping, please mention in the text maxiumum values of hardness measured during tests.
- Tensile test - what was the shape of specimen used in this test? Some methodology information are missing here.
Conclusions:
- Please support conclusions with values from tests.
Author Response
Response to Reviewer 2 Comments
Dear reviewer,
Thank you very much for your valuable comments. I hope my answers and consequent article improvement will be sufficient. Please see the comments below, explaining each of your comments.
- As you stated in abstract, the cooling rate significantly affects the properties of welded joints - I fully agree. As it was stated in literature, the different cooling rate resulted in number of cold cracks in welded joint (e.g., 10.2478/adms-2014-0008 ). However, this information is missing in your paper.
- Thanks for your feedback. We did not deal much with the occurrence of cracks in the article, as the manufacturer, some literature and the manufacturers of welded structures do not report significant problems with the occurrence of cracks. However, you are right that at high cooling rates, the formation of cracks in the weld metal is probable, so we have included this information in the article with a literature reference:
“Despite the resistance to cracking, cracks in the weld metal could occur in cases where the cooling rate is too high. When welding TMCP steel, a similar phenomenon can be encountered during such a conditions, e.g. wet welding [32].”
- Thanks for your feedback. We did not deal much with the occurrence of cracks in the article, as the manufacturer, some literature and the manufacturers of welded structures do not report significant problems with the occurrence of cracks. However, you are right that at high cooling rates, the formation of cracks in the weld metal is probable, so we have included this information in the article with a literature reference:
- Materials and Methods: Table 2 - please add information about carbon equivalent, which is one of factor allows to access the weldability of steel.
- Carbon equivalent is given in Table 1 according to chemical composition in Table 2. We added the note under the Table 2.
- Table 4 - I propose to present units in different way - [mm/s] and [kJ/mm], it will be more readable.
- We have changed the units to cm/min (welding speed) and kJ/cm, in this form they are often used in welding practice.
- Have you used any requirements from relevant standards? If no, please describe why. If yes, please add relevant standards' numbers in section "2.3. Mechanical Testing and Microstructural Analysis".
- Thanks for the notice, this is important information that we forgot to provide. We performed all tests according to the relevant standards, which we stated in the text:
“The elongation value was determined from the tensile test working diagram based on an extensometer and subsequently recalculated against the evaluated length. The performance of the tensile test and location of the test specimen were made according to the relevant standard STN EN ISO 4136. The test specimens were chosen to be non-proportional. Dimensions and designations were determined following the recommendations set out in the standard EN ISO 6892-1. The dimensions of the test specimen are shown in the Figure 3.”;” The bend test, which was performed in order to obtain an overview of the ductility of the weld, was performed on four samples from each welded joint, where two samples were loaded from the root side (TRBB) and two samples from the face side (TFBB) of the weld according to STN EN ISO 5173”. - As we stated, Figure 3 was added as information about the dimension of tensile test specimens.
- Thanks for the notice, this is important information that we forgot to provide. We performed all tests according to the relevant standards, which we stated in the text:
- Results and discussion: In the name of section move "d" to "D" - Results and Discussion.
- In my opinion you should discuss your results wider with results from other articles. Please underline the most important advantages of your work (e.g. relation cracks vs cooling rate).
- We added some sentences to the Tensile test results: “Compared to other studies dealing with GMA welding of S960MC steel, it is possible to observe a significant impact of material thickness on weldability, as presented in the introduction. In the work of Schneider et. al., where 8 mm thick S960MC steel was welded with a comparable filler material, sufficient yield strength and tensile strength were achieved. Using standard GMAW, the cooling time was t8/5 = 6.5 s (root pass) and t8/5 = 9.5 (filler pass) [12]. Compared to the GMAW-S sample, where t8/5 = 17 s, there is a significant increase in the cooling rate caused by the influence of the material thickness.”
- And Bend test results: “Based on a literature review in the introduction, at high values of the cooling rate, cracks can occur in the weld metal [32]. After performing the bend test and visual inspection, despite the significant increase in the cooling rate, no cracks occurred. The steel can be considered resistant to cracking even at relatively high cooling rates (t8/5 = 5.0 s at MCAW-S welding). However, this statement cannot be applied in general, as the thickness of the welded material increases, the susceptibility to cracking also increases. In such cases, the manufacturer's recommendations must be followed, and crack protection re-strictions applied (e.g. preheating).”
- 3 - As you truly stated, the most important is t8/5. Following this, I propose to mark 500°C in the figure.
- We tried to improve the graph to make it clearer. We changed the X and Y axis to made it more readable and we also marked temperatures 800°C and 500°C.
- Line 294 - avoid space in bracket.
- Except hardness mapping, please mention in the text maximum values of hardness measured during tests.
- We have added a sentence to the text that specifies the measured hardness values. “The hardness reached the highest value in the weld metal and ranges from 370 to 430 HV1 depending on the welding method used.”
- Tensile test - what was the shape of specimen used in this test? Some methodology information are missing here.
- Information about tensile test specimen was edited in the text: “The performance of the tensile test and location of the test specimen were made according to the relevant standard STN EN ISO 4136. The test specimens were chosen to be non-proportional. Dimensions and designations were determined following the recommendations set out in the standard EN ISO 6892-1. The dimensions of the test specimen are shown in the Figure 3.” Figure 3 was added as information about the dimension of tensile test specimens.
- Conclusions: Please support conclusions with values from tests.
- The conclusions were edited and supported by the values from the experimental part. These values were also compared with other experiments in Chapter 3 Results and Discussion.
Author Response File: Author Response.pdf
Reviewer 3 Report
REFEREE REPORT
on paper “Influence of Welding Parameters and Filler Material on the Mechanical Properties of HSLA steel S960MC Welded Joints”
by authors Miloš Mičian, Martin Frátrik and Daniel Kajánek,
submitted to Metals
The paper “Influence of Welding Parameters and Filler Material on the Mechanical Properties of HSLA steel S960MC Welded Joints” is devoted to investigation of the influence of welding parameters and filler material on changes in the heat-affected zone (HAZ) of thermo-mechanically controlled processed steel welded joints. It has been shown that significant effect of heat input on the cooling rate, which mostly affected the soft zone width in the HAZ and thus the overall mechanical properties of the welded joints. The topic of this paper is critically actual. The data are reliable and do not cause much doubt. Nevertheless, there are several points before the paper can be published. I hope that authors after major revisions can improve the paper and can publish it in Metals Journal.
- Why did authors focused on Strenx 960MC steel? Where it does use? Include in Introduction part the information about its advantages.
- Table 2 – did you investigate the chemical composition or it is information in steel specification? Add this information in Materials and Methods part.
- Why did you choose exactly these filler materials: Union X96 and Böhler X96 L-MC? What’s reason to use it?
- Figure 4 – How do you explain the grains behavior? Why does it change from coarse to fine grained? What mechanism can you suggest? I advise you to discuss this point more detailed; use this ref. [doi:10.3390/nano10061245, doi:10.1007/s10854-019-01556-x, doi:10.3390/nano10061077] for discussion.
- What equipment did you use for microstructure evaluation? Add necessary information in Materials and Methods part.
- Conclusion part is too small. It should be widening and more practical recommendation should be included.
Author Response
Response to Reviewer 3 Comments
Dear reviewer,
Thank you very much for your valuable comments. I hope my answers and consequent article improvement will be sufficient. Please see the comments below, explaining each of your comments.
- Why did authors focused on Strenx 960MC steel? Where it does use? Include in Introduction part the information about its advantages.
- Strenx 960MC steel sheets are a frequent choice of several companies, when welding heavy vehicles, mobile crane jibs and other components of mobile crane systems. Manufacturers encountered problems with insufficient strength when approving welding procedures. Due to the ongoing problems and growing share of TMCP high-strength steels used in industry, we have started their research. To be more specific about use of Strenx960MC we have added sentence: “All these properties are fully met by the assessed steel S960MC, which was developed specifically for the load-bearing parts of cranes and other heavy equipment.”
- Table 2 – did you investigate the chemical composition or it is information in steel specification? Add this information in Materials and Methods part.
- The chemical composition mentioned in the article is according to the EN 10204 3.1 material certificate provided by the steel manufacturer (SSAB). We also made our own measurements of chemical composition, which were almost identical and therefore we only stated the values measured by the manufacturer. We mentioned this information in the text: ”The mechanical properties of the steel given by the inspection certificate are shown in Table 1 and the chemical composition according to the EN 10204 3.1 material certificate provided by the steel manufacturer (SSAB) is in Table 2.”
- Why did you choose exactly these filler materials: Union X96 and Böhler X96 L-MC? What’s reason to use it?
- We have chosen UnionX96 because it was the most widely used filler material used by nearby companies to weld S960MC steel. Based on good references from the manufacturers of welded structures, we have also chosen the same manufacturer (Voestalpine) when choosing the metal-cored wire. The reason for using metal-cored wire is its high potential in reducing heat input, while it is not necessary to significantly change the existing technology as it was mentioned in the text.
- Figure 4 – How do you explain the grains behavior? Why does it change from coarse to fine grained? What mechanism can you suggest? I advise you to discuss this point more detailed; use this ref. [doi:10.3390/nano10061245, doi:10.1007/s10854-019-01556-x, doi:10.3390/nano10061077] for discussion.
- The grain behavior in the CGHAZ and FGHAZ areas was explained in the chapter 3.5 Microstructural and Macrostructural Analysis. The reason for grain refinement was the various austenitization temperature and the soaking time at this temperature. In the FGHAZ area, this temperature was only slightly higher than the Ac3 temperature and the soaking time was very short, so we can observe a fine grain. Of course, this grain refinement was also reflected in the measured mechanical properties, which we described in the text. The mechanism of grain boundaries strengthening is especially important here, where the increase in the number of grain boundaries acts like a barrier to the movement of dislocations, which we also proved with one of the references you recommended.
- What equipment did you use for microstructure evaluation? Add necessary information in Materials and Methods part.
- The whole chapter Materials and Methods has been supplemented with the necessary information about the equipment used. Standards according to which test samples were taken, tests performed and evaluated were also added.
- Conclusion part is too small. It should be widening and more practical recommendation should be included.
- The Conclusions part was supported by values from experiments and recommendations were also given regarding the welding methods used, which may be useful for practice.
Author Response File: Author Response.pdf
Reviewer 4 Report
This article contains some useful information in industries. However following points should be modified for the publication.
- Where are the fractured portion in tensile tests?
- What is A50mm in Table6?
- The effects of softening on joint tensile strength have been studied in the papers. Please refer "Performance of welded joints in TMCP steel plates", Welding International 1991, 5(8), pp.598-601.
- Authors should discuss the role of inclusions in TMCP microalloyed steel containing Ti, Nb and V.
Author Response
Response to Reviewer 4 Comments
Dear reviewer,
Thank you very much for your valuable comments. I hope my answers and consequent article improvement will be sufficient. Please see the comments below, explaining each of your comments.
- Where are the fractured portion in tensile tests?
- All 5 figures of the fracture profile (Figure 5a-e) were added to the chapter Tensile test together with information about fracture location (all fractures occurred in SCHAZ area)
- What is A50mm in Table6?
- We have modified the information about the samples in the text. Since we used a non-proportional sample, the evaluated sample length was also adapted. Standard EN ISO 6892-1 recommends for non-proportional samples to indicate the evaluated length in the designation of a parameter A. Therefore, the information about the evaluated length was entered directly in the designation as A50mm.
- The effects of softening on joint tensile strength have been studied in the papers. Please refer "Performance of welded joints in TMCP steel plates", Welding International 1991, 5(8), pp.598-601.
- The article was used in the relevant part of the introduction, where the effect of softening is mentioned (as reference no. 33).
- Authors should discuss the role of inclusions in TMCP microalloyed steel containing Ti, Nb and V.
- In the introduction, we added more information about the effect of Nb and V on the properties of TMCP steels. We have also added several references in the sections where the elements Nb, V, Ti are mentioned.
Author Response File: Author Response.pdf
Reviewer 5 Report
The present work deals with the clarification of the influences of welding parameters on the mechanical properties of welded joints made of modern thermomechanically rolled steel S960MC. It is known from practical experience that the fine-grained microstructure of this steel grade reacts sensitively to the heat of the welding process and can be irreversibly destroyed if the heat input is too high. The deteriorated strength properties in the heat-affected zone of the welds may be the result of such process heat exposure. Within the scope of the present work, the interaction between the welding process parameters and the resulting mechanical-technological properties of the welded joints is demonstrated. The subject of the present study is of high practical importance for industrial paxis.
The introductory part sufficiently reflects the problems of welding processing of HSLA steels. The results are described and discussed in a clearly form.
Nevertheless, there are some comments and suggestions for improvement on the manuscript:
Line 24 in Introduction: thermo-mechanically controlled processed (TMCP) - this term has already been explained in the abstract. This also concerns the terms HAZ, GMAW, MCAW. I don't think it is necessary to explain these abbreviations again in the text.
relative thickness of the soft zone (XSZ): this term is explained many times in the text, s. Line 69, Line 77, 362, 365, 371, 398, 408. Is such a form of writing necessary? Please check and correct if appropriate.
Please check the writing style for XSZ as it appears differently in the text: XSZ or XSZ?
The explanation for t8/5 appears in the text in the Line 210. please explain the meaning of the time t8/5 at the first mention (Line 97).
Please check and unify the writing style for t8/5 throughout the text: t8/5 or t8/5?
Table 1, Table 3 - my suggestion is to show the Fe content as a balance. (Fe bal.)
Figure 9: What is the dimension of the values 5.61 and 4.64? Are these given in mm? The macrographs do not have a scale. Please complete the figure.
Author Response
Response to Reviewer 5 Comments
Dear reviewer,
Thank you very much for your valuable comments. I hope my answers and consequent article improvement will be sufficient. Please see the comments below, explaining each of your comments.
- Line 24 in Introduction: thermo-mechanically controlled processed (TMCP) - this term has already been explained in the abstract. This also concerns the terms HAZ, GMAW, MCAW. I don't think it is necessary to explain these abbreviations again in the text.
- We have modified the text so that it does not contain unnecessary explanations or long terms. In some sentences, we still left long terms, for a better readability.
- Relative thickness of the soft zone (XSZ): this term is explained many times in the text, s. Line 69, Line 77, 362, 365, 371, 398, 408. Is such a form of writing necessary? Please check and correct if appropriate.
- We have also modified the text so that it does not contain unnecessary explanations or long terms. In some sentences, we still left long terms, for a better readability.
- Please check the writing style for XSZ as it appears differently in the text: XSZ or XSZ?
- Thanks for the notice. The writing style of these terms has been unified.
- The explanation for t8/5 appears in the text in the Line 210. please explain the meaning of the time t8/5 at the first mention (Line 97).
- The term t8/5 was explained at the first mention: “It was assumed that by reducing the heat input and time t8/5 (a cooling time between 800 °C and 500 °C), the soft zone would narrow and the strength would increase.”
- Please check and unify the writing style for t8/5 throughout the text: t8/5 or t8/5?
- Thanks for the notice. The writing style of these terms has been unified.
- Table 1, Table 3 - my suggestion is to show the Fe content as a balance. (Fe bal.)
- Fe bal. was added to Table 2 and Table 3 as you suggested.
- Figure 9: What is the dimension of the values 5.61 and 4.64? Are these given in mm? The macrographs do not have a scale. Please complete the figure.
- We added other macrostructures to the chapter 3.5. Therefore, we removed the mentioned image. The information in the text that referred to the removed image now refers to the figures in chapter 3.5. Information about used units were added as you suggested.
Author Response File: Author Response.pdf
Round 2
Reviewer 1 Report
Dear Authors, the only problem I can detect is the Table 7, where I suggested left and right columns to be reversed. You just changed the right/left titles, while soft zone values remained as were.
Author Response
Response to Reviewer 1 Comments
(Round 2)
Dear reviewer,
Please allow us to explain the last remaining problem. We made the correction after the Round 1 already, but we probably did not provide enough explanation. After you indicate the mistake with Table 7, we compared the values in Table 7 with our original measured values. We found that the values of the width of the soft zone were given in the correct column already before the revision, the only mistake was the columns title. Thus, the values in the left column belonged to the width of the left soft zone and the values in the right column belonged to the width of the right soft zone. As we said, the only mistake occurred when describing the columns, where we named the left values as “Right”, instead of “Left”, and vice versa. Therefore, after the first round of reviews, we only changed the column titles and not the values. Thank you very much for your understanding, and we apologize for the insufficient explanation in the Round 1.
Author Response File: Author Response.pdf
Reviewer 3 Report
I feel that paper can be accepted.
Author Response
Response to Reviewer 3 Comments
(Round 2)
Dear reviewer,
Please allow us to thank you once again for your valuable comments in the Round 1. We strongly believe that this article will be of interest to many readers.
Author Response File: Author Response.pdf