An Analysis of Axial Magnetic Coupling Force and Torque Dependencies on Its Structure Parameters Using a 3D FEM
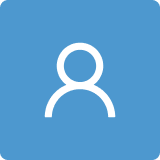
Round 1
Reviewer 1 Report
All the tables what is that 2, 4,6,8 and 10, please do indicate it clearly, example check the table 6, it is difficult to understand
The same in figures 7a and 7b also, what the need of present the same data in different forms like table and the same data in the form figure, it is meaningless
Figure 5 may have different colour, its easy to understand and differentiate
Figure 3 quality is poor, please give some parts names in the figure itself
Equations are formatted in a different ways from one another, all should be in the same format, also give explanation and reference to those equations
Author Response
Thank you very much for your valuable notes and suggestions, allowing to improve our work.
All the tables what is that 2, 4,6,8 and 10, please do indicate it clearly, example check the table 6, it is difficult to understand
Thank you for the note. The tables, their titles were clarified, structures improved. Some tables were moved to the appendix.
The same in figures 7a and 7b also, what the need of present the same data in different forms like table and the same data in the form figure, it is meaningless
Thank you for the note. The approach to present some results graphically in absolute values and numerically (in tables) in relative units, was chosen believing that the additional presentation of the data in relative units reveals interesting aspects which could be hardly noticed in absolute values. As this approach causes some doubts, the tables from the main text were moved to an appendix.
Figure 5 may have different colour, its easy to understand and differentiate
Thank you for the suggestion. Corrected.
Figure 3 quality is poor, please give some parts names in the figure itself
Thank you for the note. Corrected. Better quality picture inserted, names of the parts added in the picture.
Equations are formatted in a different ways from one another, all should be in the same format, also give explanation and reference to those equations
Thank you for the note. Corrected. Equations were reformatted. Explanation of the equations added and extended in the text, the references added.
Reviewer 2 Report
- Please improve the English.
- Please provide the clutch dimensions.
- Please provide results of "theoretical" calculations to compare them versus the experimental and 3D simulation results.
- Please explain the 3D simulation results, all details that could help to repeat the 3D simulations.
- Please explain the experimental arrangement: - the clutch is tested while the clutch parts are still (not moving)? - torque measurement? - the torque/force are calculated/measured while the two clutch halves are synchronized back to back? - what is the influence of the un synchronization position on the torque/force?
Author Response
Thank you very much for your valuable notes and suggestions, allowing to improve our work.
Please improve the English.
Corrected. The language was reviewed and corrected.
Please provide the clutch dimensions.
The clutch dimensions presented in the table 3. The table is extended. Some, missing parameters added.
Please provide results of "theoretical" calculations to compare them versus the experimental and 3D simulation results.
There are available analytical methods for torque and axial force of magnetic couplings calculations which are, also, discussed and referenced in our work [7,19,22-25]. The methods typically could be implemented without a need of particular software, have low demand on computational resources and are very valuable tools for initial design stages. However, they are based on some approximations, simplifications and are hardly applicable for the cases where peculiarities of the design are analysed [21]. The main aim of our work was to reveal dependencies of mechanical characteristics, on some specific design parameters of the clutches. Considering the main aim just experimental verification was chosen to assess an adequacy of the implemented model, similarly as in the research presented in [21] dealing with similar tasks. To reveal some characteristics of devices, which operation is based on permanent magnets interaction, some authors limited research methods just to an experimental approach [4]. As our experimental results matched results, obtained by simulations using the developed numerical 3D model, closely also considering the main objective of the work analytical calculations were considered optional for the goal.
Please explain the 3D simulation results, all details that could help to repeat the 3D simulations.
Corrected. To clarify settings of 3D FEM simulations table 4 was added in the text:
Table 4. Model details.
Modelling environment |
“COMSOL Multiphysics 4.4” |
Space dimensions |
3D |
Physics |
AC/DC module |
Interface |
Magnetic Fields, No currents |
Study type |
Stationary |
Mesh type |
Free Tetrahedral |
Maximum element size |
1 mm |
Minimum element growth rate |
1.5 |
Curvature factor |
0.6 |
Resolution of narrow regions |
0.5 |
Please explain the experimental arrangement: - the clutch is tested while the clutch parts are still (not moving)? - torque measurement? - the torque/force are calculated/measured while the two clutch halves are synchronized back to back? - what is the influence of the un synchronization position on the torque/force?
Clarification of the experiment was added to the text. Now the explanation appears (corrections here in Italic):
Physical experiments were performed for the numerical model verification. Experimental stand constructed for a purpose of the torque measurement is presented in Fig. 2. It consists of servo amplifier (Mitsubishi Electric MR-J4-200A-RJ), servo motor (Mitsubishi Electric HG-SR152), fastening element 1 for the first half-clutch fastening on motor axis, fastening element 2 for the second half-clutch stationary fastening, intermediate of 8 mm thickness for assurance of parallel placement of the discs and for assurance of a required air gap length. Servo motor is equipped with the optical encoder in the feedback loop ensuring 0.01° angle resolution. Nominal torque of the motor is 7.2 Nm and its measurement resolution is 0.072 Nm. During the experiment one half-clutch was firmly fixed to the stationary experimental stand, the other to the shaft of servo motor. Torque of the servo motor was gradually increased and recorded. The intermediate during the experiment was removed. Maximal torques were obtained for the angular displacements close to 15˚, which match theoretical value for clutches having 6 pole-pairs. Theoretically maximum torque is obtained at angular displacement , where p denotes number of pole pairs [19]. This angular displacement (15˚) here and, in further presented simulations, was used for maximum torque calculations.
Tinius Olsen H10KT experiment machine with Tinius Olsen 500 N force sensor (type: DBBMTOL-500N) was used for measurements of the coupling’s axial force (see Fig. 3). Brushless motor with a half-clutch mounted on its shaft was fixed still. The other half-clutch was pulled by the machine by gradually increasing force. Both half-clutches were separated by 8 mm intermediate in the initial position. Force values causing clutch abruption were recorded. Measurements were repeated for different interacting pole pairs, followed by calculation of averages and standard deviations. Gravitation force acting on pulled half-clutch and on its fixing equipment was taken into consideration and excluded from the results. This way three versions of magnetic couplings, distinguishing from each other by the height of motor side half-clutch magnets were evaluated. Theoretically maximum axial force is for the case of 0˚ degree angular displacement [19]. Zero angular displacement is natural position of an unloaded magnetic clutch. Zero angular displacement here and, in further presented simulations, was used for maximum axial force calculations.
- Syam, S.; Soeparman, S.; Widhiyanuriawan, D.; Wahyudi, S. Comparison of Axial Magnetic Gears Based on Magnetic Composition Topology Differences. Energies 2018, 11, 1153.
- Fontchastagner, J.; Lubin, T.; Mezani, S.; Takorabet, N. Three-Dimensional Analytical Model for an Axial-Field Magnetic Coupling, Electromagn. Res. 2014, 35, 173–182.
- Lubin, T.; Mezani, S.; Rezzoug, A. Simple Analytical Expressions for the Force and Torque of Axial Magnetic Couplings. IEEE Trans. Energy Convers. 2012, 27(2), 536-546.
- Shin, H.; Choi, J.; Jang S.; Lim K. Design and Analysis of Axial Permanent Magnet Couplings Based on 3D FEM, IEEE Trans. Magn. 2013, 49(7), 3985-3988.
- Furlani, E. Formulas for the force and torque of axial couplings. IEEE Trans. Magn. 1993, 29(5), 2295-2301.
- Furlani, E., Analysis and optimization of synchronous magnetic couplings. Appl. Phys. 1996, 79(8), 4692.
- Yao, Y.D.; Chiou, G.J.; Huang D.R.; Wang, S.J. Theoretical computations for the torque of magnetic coupling. IEEE Trans. Magn. 1995, 31(3), 1881-1884.
- Ausserlechner, U. The Maximum Torque of Synchronous Axial Permanent Magnetic Couplings. Electromagn Waves (Camb) 2012, 40, 1–29.
Reviewer 3 Report
The paper is a technical report well presented. It is suggested to propose where the system could be proposed. The ideas arise for robotic systems or for more complex robotic telematic systems. It is therefore suggested to remark this aspects and to look at the following paper that could increase the references:
EnergiesOpen AccessVolume 13, Issue 13July 2020 Article number 3376 Document type Article• Gold Open Access Source type Journal ISSN 19961073 DOI 10.3390/en13133376Force feedback assistance in remote ultrasound scan procedures
- Bucolo, Maidea, b;
- Buscarino, Arturoa, b;
- Fortuna, Luigia, b;
- Gagliano, Salvinaa
-
Author Response
Thank you for the suggestions, allowing to improve our work.
The paper is a technical report well presented. It is suggested to propose where the system could be proposed. The ideas arise for robotic systems or for more complex robotic telematic systems. It is therefore suggested to remark this aspects and to look at the following paper that could increase the references:
EnergiesOpen AccessVolume 13, Issue 13July 2020 Article number 3376 Document type Article• Gold Open Access Source type Journal ISSN 19961073 DOI 10.3390/en13133376 View more
Force feedback assistance in remote ultrasound scan procedures
Bucolo, Maidea, bSend mail to Bucolo M.; Buscarino, Arturoa, bSend mail to Buscarino A.; Fortuna, Luigia, bSend mail to Fortuna L.; Gagliano, SalvinaaSend mail to Gagliano S.
Thank you for the suggestion. Opportunity to apply magnetic couplings in control and robotic systems remarked in the text, the reference list extended.
Reviewer 4 Report
The manuscript entitled “Analysis of Force and Torque Dependencies of Axial Magnetic Coupling on Its Structure Parameters based on 3D FEM” studies the dependencies of torque and axial force on the structure of the synchronous axial magnetic coupling. The results were obtained by 3D FEM numerical simulations and experimentally validated.
The manuscript is well written and easy to follow. The study is based on the simulations that are also verified. The results are clearly presented and appropriately discussed.
Here are some comments I would like the authors to address before the manuscript is considered for publication:
1. Please add a paragraph describing the structure of the paper to the end of the Introduction section.
2. Please provide a Conclusions section in which the study’s main scientific contribution is outlined in the context of the previous research, and its value is emphasized.
3. Please address the limitations of the presented study in the Conclusions section.
4. Please also provide the directions for future research in the Conclusions section.
Author Response
Thank you very much for your valuable notes and suggestions, allowing to improve our work.
The manuscript entitled “Analysis of Force and Torque Dependencies of Axial Magnetic Coupling on Its Structure Parameters based on 3D FEM” studies the dependencies of torque and axial force on the structure of the synchronous axial magnetic coupling. The results were obtained by 3D FEM numerical simulations and experimentally validated.
The manuscript is well written and easy to follow. The study is based on the simulations that are also verified. The results are clearly presented and appropriately discussed.
Here are some comments I would like the authors to address before the manuscript is considered for publication:
- Please add a paragraph describing the structure of the paper to the end of the Introduction section.
Thank you for the suggestion. Structure of the paper described in the end of Introduction and it looks:
This paper is organized as follows. Section 2 describes the main research method – numerical 3D FEM simulation – applied in the work. Experimental model verification, parameters of the researched coupling and the model details are presented in section 3. Results of the research are presented in section 4. The results are summarized and discussed in Section 5. Conclusions are presented in section 6. Some research results are shown in appendix.
- Please provide a Conclusions section in which the study’s main scientific contribution is outlined in the context of the previous research, and its value is emphasized.
- Please address the limitations of the presented study in the Conclusions section.
- Please also provide the directions for future research in the Conclusions section.
Thank you for the suggestion. The conclusions added in the text, where the mentioned aspects covered:
- Conclusions
Permanent magnet magnetic clutches have the advantageous properties and have been finding their places in a wide range of applications. Naturally, the clutches became a relevant research object. Therefore, analysis of mechanical characteristics’ dependencies on structure parameters of the couplings are widely covered. Regardless of this fact, some aspects of the magnetic clutch design have been grey area, which was clarified in the research. As the results of this work are applicable just for axial type magnetic couplings, the research of the design aspects analysed in this work for magnetic couplings of radial type is potential space for the future work. One more prospective task for the future work is research of the main mechanical characteristics of permanent magnet couplings having unconventional topologies. Hybrid magnetic clutch consisting of radial and axial parts could be the example.
Reviewer 5 Report
The authors corrected the editing of the text, but the substantive changes are insignificant - minor editorial notes in the attachment.
Comments for author File: Comments.pdf
Author Response
In a name of the authors I would like to thank you for your valuable notes and suggestions. Changes, according to the notes, made in the manuscript are listed below.
The abstract was rewritten.
Language in the text was revised and improved.
Zoomed out view of the stand presented in figure 3 was removed.
Ranges of ordinate axes in figures 7a, 7b, and 8a, 8b were unified.
Order of cases’ list presented in legends of figures 9a and 9b was unified (also as were descriptions and colors of the curves).
Colors of the curves and markers were unified in figures 11a and 11b.
Numbering of the formulas in the text was revised and corrected.
Decimal places of numbers in the tables were unified.
General term “stress tensor” in the text was replaced by the more specific “Maxwell’s stress tensor”.
Term “average of the differences” was replaced by the term “mean absolute error”. “Differences” were replaced by “errors” in the tables 1 and 2.
Appendixes with the tables were removed from the text.
Parameters presented in table 3 and used in equation 7 were marked on the figures 1 and 4b.
Round 2
Reviewer 1 Report
The revised article is improved now and my queries are cleared by the authors.
Author Response
In a name of the authors I would like to thank you for your valuable notes and suggestions. Changes, according to the notes, made in the manuscript are listed below.
The abstract was rewritten.
Language in the text was revised and improved.
Zoomed out view of the stand presented in figure 3 was removed.
Ranges of ordinate axes in figures 7a, 7b, and 8a, 8b were unified.
Order of cases’ list presented in legends of figures 9a and 9b was unified (also as were descriptions and colors of the curves).
Colors of the curves and markers were unified in figures 11a and 11b.
Numbering of the formulas in the text was revised and corrected.
Decimal places of numbers in the tables were unified.
General term “stress tensor” in the text was replaced by the more specific “Maxwell’s stress tensor”.
Term “average of the differences” was replaced by the term “mean absolute error”. “Differences” were replaced by “errors” in the tables 1 and 2.
Appendixes with the tables were removed from the text.
Parameters presented in table 3 and used in equation 7 were marked on the figures 1 and 4b.
Reviewer 2 Report
It seems to me that the authors did not respond my concerns regarding the manuscript content.
Author Response
In a name of the authors I would like to thank you for your valuable notes and suggestions. Changes made in the manuscript are listed below.
The abstract was rewritten.
Language in the text was revised and improved.
Zoomed out view of the stand presented in figure 3 was removed.
Ranges of ordinate axes in figures 7a, 7b, and 8a, 8b were unified.
Order of cases’ list presented in legends of figures 9a and 9b was unified (also as were descriptions and colors of the curves).
Colors of the curves and markers were unified in figures 11a and 11b.
Numbering of the formulas in the text was revised and corrected.
Decimal places of numbers in the tables were unified.
General term “stress tensor” in the text was replaced by the more specific “Maxwell’s stress tensor”.
Term “average of the differences” was replaced by the term “mean absolute error”. “Differences” were replaced by “errors” in the tables 1 and 2.
Appendixes with the tables were removed from the text.
Parameters presented in table 3 and used in equation 7 were marked on the figures 1 and 4b.
Round 3
Reviewer 2 Report
To my humble opinion, the manuscript could be published.
Please check again the English, figure captions, tables, equations.