Laser-Ultrasound-Based Grain Size Gauge for the Hot Strip Mill
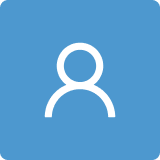
Round 1
Reviewer 1 Report
In this manuscript provides a new online grain size gauge installed in a hot strip mill, based on laser ultrasonics is presented. This is significant for industrial application to improve the technical control level, therefor the qulity of the steel sheet could be improved.
Only minor revision should be made to improve the readability,e.g. rewrite the conclusion with several paragraphs to give concluded remarks to the readers.
Author Response
Thank you for your suggestion we have tried to make the conclusion more clear. pleas see the Revised Manuscript
Reviewer 2 Report
This manuscript focused on a new online grain size gauge based on laser ultrasonics method for the hot strip mill. The topic is quite meaningful and novel and some interesting results were obtained. The manuscript is easily readable concerning language, style and presentation. Some minor revisions should be made before accepted for publication as described as follows.
(1) Figure 1 and Figure 2 were not discussed in the main text.
(2) How to identify fine equiaxed grains and twins in this test method?
(3) How do surface defects such as oxidation scales, inclusions and cracks affect the test accuracy?
Author Response
- Thank you for noticing, we have added descriptions in the main text
- This is described in detail of the reference [Tuomo Nyyssönen et al] explaining how prior austenite twin boundaries can be extracted from quenched steels. And we have added a comment in the text that “The grain boundaries are defined in this work as a misorientation of > 5°”
- This is a good comment and we have added some text explaining some of the circumstances that limits the accuracy of the gauge.
Pleas see the Revised Manuscript
Reviewer 3 Report
This paper used a method call laser ultrasonic based grain size gauge to measure the grain size in strip. The used method is new and of scientific meaning. Meanwhile, the method is well descripted and the results are interesting. However, there are some points that need to be further explained:
(1) The grain size from EBSD in Figure 5 is obviously larger than MLI grain size. For example, the grain size is around 100 um from EBSD while the MRL grain size is around 20um. Please add the related explain about this. Meanwhile, the scale bar from EBSD images are too small to be seen for Fig 5(b) to Fig5(f).
(2) For Figure 7, are the grain size from the measured results by EBSD/ MPGR with mean linear intercept method or are they measured by LUS? If they are measured by EBSD, it is suggested to show some EBSD results from the hot strip specimen. If not, it is suggested to measure a few samples from the hot strips by EBSD or other methods to verify the measured grain size by LUS.
Comments for author File: Comments.pdf
Author Response
- Thanks for your comment we have made some changes in Figure 6 (old Figure 5) of the article, below we will motivate the changes and explain some of the question marks .
- As it is written in the caption the EBSD images are scaled to share the same size scale bar. To avoid confusion, we decided to keep only one visible scale bar for all the micrographs. And rephrased the last sentence in the caption.
- Yes, it definitely looks as if the grains are larger, however, as you might know, the rule of thumb when working with grain size the average grain size of a map with enough grains is roughly the largest visible grain size divided by three. As noted in the text we use the grain size definition mean linear intercept including the twin boundaries (which is not area weighted). The software automatically extracts a MLI ~40 µm for the EBSD measurement in Figure 6(g) and the sample is one of the points in Figure 5. The important point is that the correlation of the grain size measurement vs EBSD is as mentioned in the text 0.8.
- Additionally, as mentioned elsewhere in the text the samples were taken to ~900 °C for the final LUS grain size measurement and for clarity this particular graph does not show this part of the measurement. The EBSD micrographs are primarily shown for pedagogic reasons and the Figure is only included as “An example of the GLUS measured grain size as a function of time”.
- Figure 8 (old 7) is in fact the LUS measured grain size. We have now clarified that in the text and caption. Regarding the verification with EBSD on material from the mill, it is currently planned and will be carried out as soon as possible, but we will not be able to get the results in time for this publication.
Pleas see the Revised Manuscript
Reviewer 4 Report
Comments for author File: Comments.pdf
Author Response
- One of the co-authors is a native English speaker and without indication on where you find errors in the English language of the article we cannot improve more. We therefore have to assume that the technically correct spelling of echos if that is what was intended when implying “bad quality English”, so we have therefore changed to the other correct spelling: echoes.
- Thank you for your suggestion we have now moved the general part of the grain size calculation from the methods section to the introduction. The specific part describing our newly developed method is kept in the methods section.
- Thanks for the suggestion. This will make the paper easier to understand for people without prior knowledge of laser ultrasound. We have added a schematic explaining the technique in the new Figure 1.
- The function of laser ultrasonic instruments is already well described in the reference list already [1-11]. We do not see the need of adding one more refence.
- We have now also included the description of the interferometer used. Anyone knowledgeable in the laser ultrasonic field should now easily be able to source their own copy of this laser ultrasonic grain size measurement system since all the essential parameters are now disclosed.
Pleas see the Revised Manuscript
Round 2
Reviewer 3 Report
The manuscript has been improved after modification and can be accepted after minor modification.
For the introduction part, it is not necessary to have a subtitle of 1.1 as there are no other subparts in the introduction. It is suggested to remove the subtitle of 1.1.
Reviewer 4 Report
authors significantly enhance the quality of the manuscript, which could be accepted now.