Experimental and Numerical Study on the Plasma-Laser-Induced Ignition of Strut Stabilizer at Different Locations
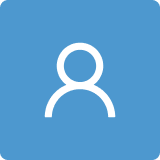
Round 1
Reviewer 1 Report
Comments and Suggestions for AuthorsThis article is to describe the experimental and numerical research on the ignition performance of a strut stabilizer with different ignition location by a plasma-laser igniter. The reviewer found the contents very interesting, while these were presented in a very poor way. Thus, this manuscript requires major revisions.
Detailed comments by the reviewer are as follows;
a) Selection of the target, i.e., the strut stabilizer, must be further justified. Combination of a fuel injector ring and a V-gutter is popular to give better fuel distribution within the recirculation region ($). Why did the authors select the strut stabilizer? The benefit and problem with the strut stabilizer over the conventional system should be clarified in the introduction section to show what is the problem with the strut stabilizer, so that the technical merit of the present study should be highlighted.
$ T. Inamura, et al., J. Propulsion and Power, 17(2001), pp. 860-868.
b) Why did the authors set fixed offset to the ignition location in the spanwise direction and change the streamwise location alone? The spanwise location would affect the ignition process too, so that limitation of the offset distance should also be justified.
c) For CFD part, verification of the grid convergence and boundary conditions such as adiabatic wall assumption should be verified. Note that in AIAA journals, CFD results without grid convergence verification will be rejected.
d) Experimental methods should be further described in detail. To the reviewer’s belief, fuel injection continued within a test run at targeted equivalence ratio, and igniter was repeatedly operated for 5 seconds. and if failed, went to the next equivalence ratio, so that minimum equivalence ratio against the ignition location was attained.
e) Technical words were used without definition. For example, what is the ignition performance? In line 141, the authors waited for 5 seconds after the operation of the ignition device to confirm ignition. Usually, this is to confirm flame-holding, not ignition. Was ignition equivalence ratio based on the injected flow rate, or measured local value? If the former, stabilizer-to-stabilizer spanwise distance would determine the whole airflow rate per stabilizer, and the spacing should be justified. If the latter, was the concentration measured at the ignition location? Was ignition limit stated in line 459 the ignition equivalence ratio?
f) In the sentence describing Fig. 5, the authors mentioned about flame shape and flame location, such information being not available to the readers as Fig. 5 showed only the area averaged value. These appeared in Fig. 6, while the location and the shape of the stabilizer were not shown in the figure. In line 323, the authors described about the turbulent kinetic energy distribution, while it was not shown in Fig. 8.
g) In line 459, the authors stated that the time required for the flame propagation to the shear layer is correlated with the ignition limit. Was that because of the similarity between Fig. 4 and Fig. 13? Was there any physical explanation on that correlation?
h) Figs. 14 and 15 were total incomprehensive to the reviewer. What was the greenline and/or blue line and redline? How could the authors judge the stability of the flame leading edge?
In conclusion, this manuscript required major revisions for publication.
Author Response
Please refer to the attachment and manuscript for the detailed revisions
Comment 1: Selection of the target, i.e., the strut stabilizer, must be further justified. Combination of a fuel injector ring and a V-gutter is popular to give better fuel distribution within the recirculation region ($). Why did the authors select the strut stabilizer? The benefit and problem with the strut stabilizer over the conventional system should be clarified in the introduction section to show what is the problem with the strut stabilizer, so that the technical merit of the present study should be highlighted.
Reply: Thank you for your comments. We have made some additions to the introduction section.
Comment 2: Why did the authors set fixed offset to the ignition location in the spanwise direction and change the streamwise location alone? The spanwise location would affect the ignition process too, so that limitation of the offset distance should also be justified.
Reply:Thank you for your comments. Shifting the ignition position in the spanwise direction will undoubtedly impact the ignition process. In this study, the ignition locations are situated on the central section, which locate in the same plane as the fuel injector and feature a high concentration of kerosene. Additionally, the central section is the furthest from the wall surfaces on either side, potentially minimizing the effects of corner vortices and wall cooling that could lead to flame extinction. This study primarily investigates the impact of various ignition positions along the flow direction on ignition performance. Future research may explore ignition positions across different spanwise directions.
Comment 3: For CFD part, verification of the grid convergence and boundary conditions such as adiabatic wall assumption should be verified. Note that in AIAA journals, CFD results without grid convergence verification will be rejected.
Reply:Thank you for your comments. In this study, the grid scale is primarily validated through the Power Spectral Density (PSD) of pressure fluctuations within the downstream shear layer. Drawing from relevant literature on flow around a cylinder, the cylinder wall is modeled as a no-slip boundary. As this study focuses solely on the non-reacting flow field, the adiabatic wall conditions do not significantly impact the calculations, since only fluid flow characteristics are considered, without thermal effects. However, your suggestions on boundary settings are invaluable. In our other thermal calculations, the temperature of the bluff body wall has a significant impact on the simulation results.
Comment 4: Experimental methods should be further described in detail. To the reviewer’s belief, fuel injection continued within a test run at targeted equivalence ratio, and igniter was repeatedly operated for 5 seconds. and if failed, went to the next equivalence ratio, so that minimum equivalence ratio against the ignition location was attained.
Reply:Thank you for your comments. We have added some descriptions about the ignition test process.
Comment 5: Technical words were used without definition. For example, what is the ignition performance? In line 141, the authors waited for 5 seconds after the operation of the ignition device to confirm ignition. Usually, this is to confirm flame-holding, not ignition. Was ignition equivalence ratio based on the injected flow rate, or measured local value? If the former, stabilizer-to-stabilizer spanwise distance would determine the whole airflow rate per stabilizer, and the spacing should be justified. If the latter, was the concentration measured at the ignition location? Was ignition limit stated in line 459 the ignition equivalence ratio?
Reply:Thank you for your comments. Some technical words have been added explanations in this paper. The described ignition performance refers to the minimum ignition equivalence ratio, and the ignition performance in the abstract has been revised. The description on line 141 has been updated. After operating the ignition device, wait for 5 seconds to ensure stable combustion of the flame post-ignition, which is then considered successful. The ignition equivalence ratio is calculated based on the injection flow rate. The ignition limit on line 459 is the ignition equivalence ratio.
Comment 6: In the sentence describing Fig. 5, the authors mentioned about flame shape and flame location, such information being not available to the readers as Fig. 5 showed only the area averaged value. These appeared in Fig. 6, while the location and the shape of the stabilizer were not shown in the figure. In line 323, the authors described about the turbulent kinetic energy distribution, while it was not shown in Fig. 8.
Reply:Thank you for your comments. We have made revisions to the sentence describing Fig. 5 to enhance the article's readability. In Fig. 6, we included the stabilizer structure within each time series image to clearly show their location and shape. We have revised the description of Figure 8, noting that the distribution of turbulent kinetic energy is derived from Figure 7.
Comment 7: Figs. 14 and 15 were total incomprehensive to the reviewer. What was the greenline and/or blue line and redline? How could the authors judge the stability of the flame leading edge?
Reply:Thank you for your comments. The legends and explanations have bee added in the figs. 14 and 15. The lines in Figs 14 and 15 depict the extremum of the flame edge in different directions at various times. In this study, the stability of the flame leading refers to whether the flame can sustain combustion once it has reached a specific location.
Author Response File: Author Response.docx
Reviewer 2 Report
Comments and Suggestions for AuthorsThe paper is interesting in trying to explain the connection between the position of the initial ignition location and the development of flame. However, there are a few issues to be addressed.
1) The abstract should not contain symbols that will later be explained (L/D).
2) Please, rephrase lines 20-21 for clarity.
3) You may reconsider changing "ways" for "paths" in line 23.
4) The ignition performance idea introduced in the abstract is somehow obscured until reading the full paper.
5) Please, rephrase lines 46-48 for the sake of clarity.
6) What is an "electric nozzle" in line 61?
7) The inlet temperature in the afterburner of 1600 K? I never heard of such high level at least in gas turbine engines or ramjets. The reference given [11] does not provide any clue in this direction.
8) Fig. 2a is not clear enough. At the backend it seems there is a prismatic structure that does not make sense. What does Fig. 2b have do to with your CFD computation? Or does it? It seems more like a DNS experiment not a LES one.
9) You must change the position of Fig. 4. It is right below the title of the subsection 3.1.
10) How do you define ignition equivalence ratio? Is it the same with the usual equivalence ratio? The discussion of this parameter should be postponed until subsection 3.3 when kerosene is injected.
11) The flame area is a 2D parameter that can be extracted from a 2D photo? I would say that S is 3D property.
12) The injection of kerosene was performed for a cold flow? Once with ignition, the distribution represented in Fig. 10a certainly will change.
13) Based on Fig. 1c it seems that the laser ignition is performed in the symmetry plane. How do you explain that all initial (t=0ms) X/D coordinates of ignition kernels stay around X/D=-0.2 and do not vary? How can you control this?
14) Fig. 12 is a superposition of two cold flow images (10a and 7). What is the relevance of the flame trajectories in this cold environment?
15) How do you define flame edge and what is the meaning of red and green lines in Fig. 14? Is it leading edge and trailing edge? Likewise for Fig. 15. You need to introduce a legend for these figures.
16) The flame extended speed in Fig. 16 shouldn't be somehow symmetrical along X direction? Also, could you, please, check the magnitude of these velocities, especially upstream as they seem too high.
Comments on the Quality of English Language
I have already done so in the comments section
Author Response
Please refer to the attachment and manuscript for the detailed revisions
Comment 1: The abstract should not contain symbols that will later be explained (L/D).
Reply:Thank you for your comment. The symbol L/D has been deleted.
Comment 2: Please, rephrase lines 20-21 for clarity.
Reply: Thank you for your comment. The lines 20-21 have been rephrased for clarity
Comment 3: You may reconsider changing "ways" for "paths" in line 23.
Reply:Thank you for your comment. This word has been changed.
Comment 4: The ignition performance idea introduced in the abstract is somehow obscured until reading the full paper.
Reply:Thank you for your comment. We have changed the "ignition performance" to the "minimum ignition equivalence ratio", which may make the abstract easier to understand
Comment 5: Please, rephrase lines 46-48 for the sake of clarity.
Reply:Thank you for your comment. The lines 46-48 has been somewhat rephrased for the sake of clarity.
Comment 6: What is an "electric nozzle" in line 61?
Reply:Thank you for your comment. We have changed the "electric nozzle" as "spark plug".
Comment 7: The inlet temperature in the afterburner of 1600 K? I never heard of such high level at least in gas turbine engines or ramjets. The reference given [11] does not provide any clue in this direction.
Reply:Thank you for your comment. We have corrected the description of this error to 1300K.
Comment 8: Fig. 2a is not clear enough. At the backend it seems there is a prismatic structure that does not make sense. What does Fig. 2b have do to with your CFD computation? Or does it? It seems more like a DNS experiment not a LES one.
Reply:Thank you for your comment. We have adjusted Fig. 2a to enhance its clarity. Fig. 2b shows the PSD of pressure fluctuations at a specific point from the LES results, demonstrating that the LES method and configurations employed in this study satisfy the criteria for analytical precision in turbulent flows. In Figure 2b, the turbulence energy spectrum with a -5/3rd power scaling rate is also shown. By comparing the attenuation law of the obtained energy spectrum in the high frequency range, it is verified that the calculation method in this paper meets the accuracy requirements of turbulence flow analysis.
Comment 9: You must change the position of Fig. 4. It is right below the title of the subsection 3.1.
Reply:Thank you for your comment. We have changed the position of Fig. 4.
Comment 10: How do you define ignition equivalence ratio? Is it the same with the usual equivalence ratio? The discussion of this parameter should be postponed until subsection 3.3 when kerosene is injected.
Reply:Thank you for your comment. The ignition equivalence ratio refers to the minimum equivalence ratio that can successfully ignite. The ignition equivalence ratio is identical to the standard equivalence ratio, representing the ratio of the actual fuel-to-air ratio to the stoichiometric fuel-to-air ratio. In this study, the actual fuel-to-air ratio is determined by the ratio of the kerosene flow rate to the air flow rate. The definition of equivalence ratio was added in section 3.3.
Comment 11: The flame area is a 2D parameter that can be extracted from a 2D photo? I would say that S is 3D property.
Reply:Thank you for your comment. The flame image captured by a single high-speed camera represents the flame's integration along the shooting direction. In numerous studies of flame propagation trajectories, this 3D projection is employed to delineate flame boundaries, determine flame centroids, and analyze flame propagation trajectories.
Comment 12: The injection of kerosene was performed for a cold flow? Once with ignition, the distribution represented in Fig. 10a certainly will change.
Reply:Thank you for your comment. The injection of kerosene was performed in a non-reacting flow. Once with ignition, the instantaneous kerosene concentration distribution certainly will change, due to the influence of the flow field and flame structure. As illustrated in fig. 10, the kerosene concentration behind the stabilizer is highly nonuniform. Consequently, igniting at different positions with mixtures of varying equivalence ratios directly impacts the formation and size of the initial flame kernel, subsequently influencing the trajectory of flame propagation.
Comment 13: Based on Fig. 1c it seems that the laser ignition is performed in the symmetry plane. How do you explain that all initial (t=0ms) X/D coordinates of ignition kernels stay around X/D=-0.2 and do not vary? How can you control this?
Reply:Thank you for your comment. The position of the initial flame kernel is determined by the laser focal point's location. In the experiments, after the laser ignition probe was adjusted, it was mounted on a uniaxial displacement device to maintain consistent laser height for each trial, as depicted in Figure 1b. Throughout the experiments, the laser's focal points were consistently positioned below the central area, roughly at X/D=-0.2, which is consistent with Figure 1c.
Comment 14: Fig. 12 is a superposition of two cold flow images (10a and 7). What is the relevance of the flame trajectories in this cold environment?
Reply:Thank you for your comment. The flow field's distribution is crucial for flame propagation and stable combustion. In this study, the ignition location was categorized based on the burner's non-reactive flow field, specifically within or outside the recirculation zone. The kerosene distribution significantly influences the creation of the initial flame kernel and the flame intensity during propagation, further impacting the flame's trajectory.
Comment 15: How do you define flame edge and what is the meaning of red and green lines in Fig. 14? Is it leading edge and trailing edge? Likewise for Fig. 15. You need to introduce a legend for these figures.
Reply:Thank you for your comment. The legends and explanations have been added in the figs. 14 and 15. The lines in Figs 14 and 15 depict the extremum of the flame edge in different directions at various times.
Comment 16: The flame extended speed in Fig. 16 shouldn't be somehow symmetrical along X direction? Also, could you, please, check the magnitude of these velocities, especially upstream as they seem too high.
Reply:Thank you for your comment. The flame extended speed in the X direction is asymmetric. As mentioned in this study, flames typically spread first to the shear layer on one side and then to the opposite side. Once one side stabilizes, the overall flame intensity becomes greater than during the initial spread of the flame core. Consequently, the flame's edge has a stronger heat source when propagating in the positive X direction, resulting in a slightly higher diffusion speed than in the negative X direction.
The speed in positive Z direction has been verified and found accurate. The flame edge's expansion speed depends not only on the turbulent flame velocity but also on the local airflow speed. Figure 11 clearly shows the flame's movement within the flow field, and in Figure 9, the instantaneous velocity at the observation point has at times exceeded 60 m/s. These two factors combined may result in high flame extended speeds.
Author Response File: Author Response.docx
Reviewer 3 Report
Comments and Suggestions for AuthorsThe paper presents experimental results on strut stabilizer with Plasma-Laser-Induced Ignition. Experiments are performed for aviation kerosene burning in air at atmospheric pressure, with optical registration system applied to register the ignition and flame propagation modes. Tests are supported by numerical simulations of non-reacting flow performed by Large-Eddy simulations with known WALE model for the turbulent viscosity. Different ignition modes are obtained, and flame propagation trajectories are analyzed. The effects of the shear layer and recirculation zone are discussed for different ignition locations.
Generally, the paper is well-written, and the material presented is certainly of interest to specialists in engine and ramjet design. The conclusions are supported by the experimental findings.
However, there are some issues that must be resolved:
1. Section 2.2.1 is not written clearly and must be revised. The method applied (Large-eddy simulations) must be stated first (currently it is mentioned somewhere in the middle, line 202, after the boundary conditions, lines 199-200, which is illogical). Also, there are many undefined symbols scattered around. For example, formula (1) looks like taken from some other text, without explanation of what each symbol means (only Sij with overbar is explained, but not other symbols). The inlet velocity is denoted by u_0 on line 198, then it appears as U on line 212, and then it appears as U_\inf on line 224. Are these the same quantities?
2. What type of software was used in the simulations? Was it some commercial code, or an in-house code? What were the numerical schemes used for discretization? It is not appropriate just to say "LES simulations", the tools must be specified and relevant references given.
3. Line 354: "A uniform mixture of oil and gas is beneficial..." - what kind of oil is meant here? Kerosene? Please rephrase.
4. Line 364: "The diffusion and propagation process of flame kernel.." - the term "diffusion" does not seem appropriate here. Rephrase.
Comments on the Quality of English Language
A thorough check of English is recommended. Some issues are:
line 123: "Planer" must be "Planar", capitalize the words in the PLIF method name
line 171: "laser-induced" must be "laser-induced ignition"
line 375: " denote" must be "denoted"
lines 525-527: why u_f is boldface?
Author Response
Comment 1: Section 2.2.1 is not written clearly and must be revised. The method applied (Large-eddy simulations) must be stated first (currently it is mentioned somewhere in the middle, line 202, after the boundary conditions, lines 199-200, which is illogical). Also, there are many undefined symbols scattered around. For example, formula (1) looks like taken from some other text, without explanation of what each symbol means (only Sij with overbar is explained, but not other symbols). The inlet velocity is denoted by u_0 on line 198, then it appears as U on line 212, and then it appears as U_\inf on line 224. Are these the same quantities?
Reply: We are grateful for the suggestion. We have included additional details on LES large-eddy simulation in section 2.2.1 and clarified the symbols in the formulas. Additionally, the notation 'U' on line 212 has been updated to 'u_0' to prevent any confusion. On line 224, 'U_inf' denotes the inlet velocity in the validation example. To prevent confusion with the term 'incoming flow velocity' elsewhere in the article, we have used 'U_inf'.
Comment 2: What type of software was used in the simulations? Was it some commercial code, or an in-house code? What were the numerical schemes used for discretization? It is not appropriate just to say "LES simulations", the tools must be specified and relevant references given.
Reply: Thank you for your comment. Commercial software ANSYS FLUENT is used in the simulation, and relevant explanations have been added in the article.
Comment 3: Line 354: "A uniform mixture of oil and gas is beneficial..." - what kind of oil is meant here? Kerosene? Please rephrase.
Reply: Thank you for your comments. Modifications have been made. It has been changed to a uniform mixture of fuel and air.
Comment 4: Line 364: "The diffusion and propagation process of flame kernel.." - the term "diffusion" does not seem appropriate here. Rephrase.
Reply:Thank you for your comments. To avoid ambiguity, "diffusion" has been removed
Comment 5: line 123: "Planer" must be "Planar", capitalize the words in the PLIF method name
line 171: "laser-induced" must be "laser-induced ignition"
line 375: " denote" must be "denoted"
lines 525-527: why u_f is boldface?
Reply: Thank you for your comments on the quality of English language, the wording you mentioned has been modified.
Author Response File: Author Response.docx
Round 2
Reviewer 1 Report
Comments and Suggestions for AuthorsThe authors made intensive rebuttal and revisions against my comments, however, there are still some insufficiency as described below. Thus, this manuscript still needs major revisions. Detailed comments by the reviewer are as follows, the comment numbering being the same as the first review.
a) The description on the strut stabilizer was reasonable, while no references were cited on this issue in the revised manuscript.
b) There was misunderstanding on my comment. My concern was the offset in the X direction, not in the Y direction.
c) On the grid convergence, add the PSD results in the manuscript (can be in appendix), or refer relevant reference of the authors’ previous study.
d) The authors described ‘gradually reduce the kerosene flow’ in line 153. Did it mean continuous test or another test with reduced flow rate? If former, flame existed during the flow rate transition and extinction could occur, so that it should be named as flame-holding limit, not ignition limit, as clear extinction should occur before the next operation of the ignition device to check the ignition limit. Clarify the description.
e) Correlation was not applicable to the X=70 case. Need exact description. Also, physical explanation on the correlation is highly welcomed.
g) Relation between the stability of the flame leading and sustainability of the flame should be discussed. Furthermore, stability should be quantified based on Figs. 14 and 15, i.e, it was difficult to judge stability from Figs. 14 and 15.
In conclusion, this manuscript still needs major revisions for publication.
Author Response
Please see the attachment.
Comment 1: The description on the strut stabilizer was reasonable, while no references were cited on this issue in the revised manuscript.
Reply: Thank you for your comments. The relevant reference has been added and highlighted.
Comment 2: There was misunderstanding on my comment. My concern was the offset in the X direction, not in the Y direction.
Reply:Thank you for your comments. The offset along the X direction is significant. As one moves away from the center along the X-axis, the equivalence ratio of the mixture gradually increases, favoring ignition. However, concurrently, the airflow speed also increases, which is detrimental to ignition. Thus, there may be a point along the Y-axis where the minimum ignition equivalence ratio is at its minimum. These are our conjectures, and future experiments will be conducted to investigate them.
Comment 3: On the grid convergence, add the PSD results in the manuscript (can be in appendix), or refer relevant reference of the authors’ previous study.
Reply:Thank you for your comments. In this study, the grid scale is primarily validated through the Power Spectral Density (PSD) of pressure fluctuations within the downstream shear layer. Figure 2 (b) shows the PSD results.
Comment 4: The authors described ‘gradually reduce the kerosene flow’ in line 153. Did it mean continuous test or another test with reduced flow rate? If former, flame existed during the flow rate transition and extinction could occur, so that it should be named as flame-holding limit, not ignition limit, as clear extinction should occur before the next operation of the ignition device to check the ignition limit. Clarify the description.
Reply:Thank you for your comments. We have added some descriptions about the ignition test process. Every reduction in fuel flow rate constitutes a new experiment. In fact, prior to each ignition, we shut off the kerosene injection and purge the test section to prevent the influence of residual kerosene on the ignition test.
Comment 5: Correlation was not applicable to the X=70 case. Need exact description. Also, physical explanation on the correlation is highly welcomed.
Reply:Thank you for your comments. Additional explanations have been provided. The minimum ignition equivalence ratio is directly linked to the time it takes for the flame to reach the shear layer, when the ignition position is within the recirculation zone. When the ignition position is within the recirculation zone, the flame propagates to the shear layer and is stabilized near the bluff body's trailing edge, creating a stable heat source. The longer it takes for the flame kernel to reach the shear layer, the more heat will be dissipated during propagation, necessitating a stronger initial flame kernel. The equivalence ratio directly influences the size and temperature of the initial flame during formation. When the ignition position is outside the recirculation zone, as shown in Figure 11's flame propagation, the flame does not reach the vicinity of the bluff body's trailing edge upon reaching the shear layer. This differs from the stability mechanism observed previously, rendering the aforementioned correlation inapplicable.
Comment 6: Relation between the stability of the flame leading and sustainability of the flame should be discussed. Furthermore, stability should be quantified based on Figs. 14 and 15, i.e, it was difficult to judge stability from Figs. 14 and 15.
Reply:Thank you for your comments. In the discussion of Figures 14 and 15, stability refers to the fixed position of the flame edge, specifically the flame leading edge position (purple line) in Figure 15. This stability has not yet been quantified with an appropriate indicator and can only be analyzed qualitatively.
Author Response File: Author Response.docx
Reviewer 2 Report
Comments and Suggestions for AuthorsAccept in present form.
Author Response
Please see the attachment.
Author Response File: Author Response.docx
Reviewer 3 Report
Comments and Suggestions for AuthorsI believe that authors took into account all my questions. Few issues, however, are remaining that must be addressed to improve the text clarity:
1. "The control equation in the LES method is filtered to provide a large-scale structure, which is considered as the result of the solution" (lines 207-208) is very vague. Change "control equation" to "governing equations", and rephrase the rest (in LES, flow structures having the scales larger than the filter width (of the order of grid cell size) are calculated directly, while the smaller-scale (therefore, subgrid-scale) flow features are modelled.
2. In Equations (1) and (2) the filtered quantities are denoted by overbar, whereas on the following lines 213, 214 the overbar is missing
3. Line 247: "All the wall conditions are non-slip and adiabatic boundaries" - temperature or energy is never included in the governing equations (1), (2), therefore, reference to "adiabatic" boundaries is irrelevant. Also rephrase the whole sentence, "wall conditions are non-slip boundaries" sounds wrong. Suggestion: "On all solid walls, the no-slip boundary conditions were set" or something similar.
4. What is f on lines 257, 258? Define it clearly
Comments on the Quality of English LanguageNo specific comments, English is acceptable in my view
Author Response
Comment 1: "The control equation in the LES method is filtered to provide a large-scale structure, which is considered as the result of the solution" (lines 207-208) is very vague. Change "control equation" to "governing equations", and rephrase the rest (in LES, flow structures having the scales larger than the filter width (of the order of grid cell size) are calculated directly, while the smaller-scale (therefore, subgrid-scale) flow features are modelled.
Reply: Thank you for your comment. The vague sentence (lines 207-208) has been rephrased.
Revision
In lines 210-212:
In LES, large eddies are resolved directly, while small eddies are modeled using a subgrid scale model. The governing equations for an incompressible flow form of the continuity and the Reynolds Averaged Navier-Stokes equations are specified as follows
Comment 2: In Equations (1) and (2) the filtered quantities are denoted by overbar, whereas on the following lines 213, 214 the overbar is missing
Reply: Thank you for your comment. The filtered quantities have been revised in lines 213 and 214.
Revision:
In lines 213-214:
where is the filtered velocity component along the Cartesian coordinates , is the density of fluid and is the pressure, is the subgrid-scale stresses term.
Comment 3: Line 247: "All the wall conditions are non-slip and adiabatic boundaries" - temperature or energy is never included in the governing equations (1), (2), therefore, reference to "adiabatic" boundaries is irrelevant. Also rephrase the whole sentence, "wall conditions are non-slip boundaries" sounds wrong. Suggestion: "On all solid walls, the no-slip boundary conditions were set" or something similar.
Reply: Thank you for your comments. The sentence has been rephrased as "On all solid walls, the no-slip boundary conditions were set".
Revision:
In line 247:
On all solid walls, the no-slip boundary conditions were set.
Comment 4: What is f on lines 257, 258? Define it clearly
Reply:Thank you for your comments. f is the vortex shedding frequency.
Revision:
In lines 256-258:
The Strouhal number defined by St=fD/u0 is typically between 0.2 and 0.29 for the flow around a circular cylinder, where f is the vortex shedding frequency.
Author Response File: Author Response.docx
Round 3
Reviewer 1 Report
Comments and Suggestions for AuthorsThe authors made intensive rebuttal and revisions against my comments, most of them were of my satisfaction. However, some more revisions are necessary as mentioned below. Thus, minor revisions are required before publication. As the revisions are to add missing information, so that further review is not necessary to the reviewer’s belief. The comment numbering is the same as the first review.
a) The reference I asked is not on the V-gutter, but on the strut stabilizer. The authors claimed that the strut stabilizer should have lesser total pressure loss in comparison to the conventional combination of injector ring and the V-gutter, however, they did not include any reference supporting the claim. On all claims the authors have made in the introduction section, the authors should justify by showing either relevant references or their own results in the main text.
b) The authors should add the description they have made in the rebuttal letter to the main text.
g) To the reviewer, flame location looks like to be stabilized at about t=10 ms for all cases including L=65 mm. Make clear description on the difference between the Figs. 15a) to 15f) and 15g) in the manuscript. Note that the time variation in Fig. 15g) was close to that in Fig. 15a).
In conclusion, this manuscript still needs minor revisions for publication, but no need for further review.
Author Response
Comment a): The reference I asked is not on the V-gutter, but on the strut stabilizer. The authors claimed that the strut stabilizer should have lesser total pressure loss in comparison to the conventional combination of injector ring and the V-gutter, however, they did not include any reference supporting the claim. On all claims the authors have made in the introduction section, the authors should justify by showing either relevant references or their own results in the main text.
Reply:Thank you for your comments. We have added some references on the application of strut stabilizers.
Revision:
Reference:
[2] Wadia, A. R., James, F. D. F110-GE-132: Enhanced Power Through Low-Risk Derivative Technology. Journal of Turbomachinery, 2001, 123(3): 544-551.
[3] Li W., Tan X., Huang X., et al. Application of double-wall cooling structure in the integrated strut flame stabilizer. Thermal science and engineering progress, 2022, 36(1): 101526.
[4] Ebrahimi, H. Overview of gas turbine augmentor design, operation, and combustion oscillation. 42nd AIAA/ASME/SAE/ASEE Joint Propulsion Conference & Exhibit, California, America, 9-12 July 2006.
Comments b): The authors should add the description they have made in the rebuttal letter to the main text.
Reply: Thank you for your comments. We have added the description to the main text. It may well be suitable as a future work.
Revision:
In lines 660-666:
In this present study, only the impact of different axial ignition locations on ignition performance was investigated. However, we noticed that the offset along the horizontal direction is significant. As one moves away from the center along the horizontal direction, the equivalence ratio of the mixture gradually increases, favoring ignition. However, con-currently, the airflow speed also increases, which is detrimental to ignition. Thus, there may be a point along the direction where the minimum ignition equivalence ratio is at its minimum. The future experiments will be conducted to investigate them.
Comments g): To the reviewer, flame location looks like to be stabilized at about t=10 ms for all cases including L=65 mm. Make clear description on the difference between the Figs. 15a) to 15f) and 15g) in the manuscript. Note that the time variation in Fig. 15g) was close to that in Fig. 15a).
Reply: Thank you for your comments. At 10ms, all flame edges have indeed stabilized, but the timing of flame edge stabilization varies at different ignition positions. For example, in Fig.15(c), the trailing edge is stabilized at 4ms, while in Fig. (g), it is stabilized at 6.2ms. In the main text, we have a section discussing the differences between the two, specifically focusing on the flame leading edge, which we consider to be the most significant difference.
Revision:
In lines 584:590:
However, due to the lack of a certain degree of flame formation downstream of the stabilizer, the temperature in the recirculation zone is relatively low, which makes it impossible to heat the fresh mixture in the shear layer. When the flame trailing edge propagates to the rear of the recirculation zone (i.e., Z/D > 1.4), it rapidly propagates downstream. During this process, the leading edge of the flame starts to propagate upstream and eventually becomes fixed at the trailing edge of the stabilizer.