Comparison of Energy Performance of Shaft Tubular Pump Device at Two Guide Vane Inlet Angles
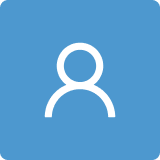
Round 1
Reviewer 1 Report
processes-1713802
Comparison of Energy Performance of Shaft Tubular Pump Device at Two Guide Vane Inlet Angles
The influence of the angle adjustment of the guide vane inlet on the energy performance of the pump device was studied in order to improve the efficiency under frequent operating conditions.
The advantage of the article is the experimental validation of the results of numerical CFD simulations.
The article deals with an interesting topic that is worth researching. The methods used are appropriately selected and the results achieved are practically applicable, but I have some partial comments that need to be taken into account / processed before accepting the article for publication.
- Figure 1 is divided into two pages and is not so clear - please correct.
- The computational software used for CFD simulations should be specified. Please add.
- It seems to me that the research was probably carried out under time-stable conditions. If this is the case, it is necessary to clearly declare this fact and also omit the time terms in the controlling differential equations - equations (2), (3), (4).
- It is also necessary to omit other members if they were not used in the simulation - such as the source of momentum F and the like.
- In general, the given equations do not describe what the software used to model, but only what was actually used in the model so that readers are not confused.
- It is a pity that no turbulence model other than RNG k-epsilon was used for comparison.
- Comments on the computational mesh - The structured mesh generated at forebay and outlet sump is not well fine at he top boundaries - see figure 5.
- It is not clear whether in other parts of the computational domain they were used at the surfaces of the prismatic layer of cells - which is necessary to achieve the required quality and suppress the so-called numerical diffusion. Add an figure or explainin it in the text.
- Explain why the symmetry boundary conditions were used and at which edges exactly they were used. It is not clear to me from Figure 5.
- Specify and discuss the shape of the velocity profile on the inlet boundary condition.
- Specify and discuss the turbulent characteristics used on this boundary condition.
Author Response
The authors wish to express their deep gratitude to you for your interest and constructive comments on our paper. We have carefully considered the comments and modified the manuscript, and the modifications were marked up using the “Track Changes” function.
Please see the attachment for detailed modification instructions.
Author Response File: Author Response.docx
Reviewer 2 Report
- From reading this paper, it is difficult to find what advances or key-tech are presented. In this article, the authors seem to adopt a different inlet-section angle of the guide vanes to improve the pumping efficiency of the pump device when operating at an extra-low frequency. It is suggested that the key developments should be highlighted in the text.
- How exactly to know the optimal angles for better energy performance?
- How many guide vanes were taken? why?
- Citation of Reference [29] seems not shown in the text.
Author Response
The authors wish to express their deep gratitude to you for your interest and constructive comments on our paper. We have carefully considered the comments and modified the manuscript, and the modifications were marked up using the “Track Changes” function.
Please see the attachment for detailed modification instructions.
Author Response File: Author Response.docx
Reviewer 3 Report
Thanks for the work done to Comparison of Energy Performance of Shaft Tubular Pump Device at Two Guide Vane Inlet Angles, afterwards analyzed inlet angle of the guide vane was adjusted by the method of Computational Fluid Dynamics.
Please answer the following points:
Abstract
- What is the innovation of the present article compared to the article - Xu, L., Ji, D., Shi, W., Xu, B., Lu, W. and Lu, L., 2020. Influence of inlet angle of guide vane on hydraulic performance of an axial flow pump based on CFD. Shock and Vibration, 2020. - except geometry and pump type(model is the TJ04-ZL-07 vs the TJ04-ZL-06) ?
Introduction
- The descriptions of the references and the similarities and innovations of their work have not been clearly examined.
Mathematical relations and formulas governing the problem
- What is the amount of Y+ in your numerical calculations along the solution range?
- The k-ε RNG model has a good ability to simulate rotational flows with low Reynolds number. For a better understanding of the flow profile design with dimensionless numbers, such as Reynolds number, Euler number (Eu), Eckert number (Ec)
- One of the distinguishing points of the blades is how the liquid passes and exits the blade blades, which are called specific velocities (Ns). This number, as one of the indicators used by pump designers, is used to describe the geometry of the blades and their classification based on the type of design and their application. Please mention this in your article.
Numerical solution model
- Can different other scenarios be implemented in these cases?) For example:unsteady flow, cavitation phenomenon or fine suspended particles(
- Independence of the mesh must be displayed in a separate section.
Analysis of results
- Explain the reason for the vortex in Figure 10 and its improvement from the perspective of fluid dynamics and flow physics.
- In this section, it is better to compare your results with the results of references.
- For numerical tasks performed with commercial software, analysis of results is necessary
- The physics of fluid flow has not been studied at all, and the reason why each case is better should be examined from a fluid perspective
- Numerical results are given only for the energy performance, while the pressure coefficient and finally the total domain contours should be presented
- The order in the legend is not clear in the figures.
Validation and authenticity of results
- It is not independently and comprehensibly stated whether the results are consistent with the approved models.
Conclusion
Is good
Structural review
- References should be given in chronological order or hierarchy.
- Verification of the present article should be expressed independently.
- An independent part of the analysis of results based on graphs or tables of output data is required.
This article needs correction despite the time consuming and comparative work done.
I wish you would correct and improve the work by considering the mentioned points.
Comments for author File: Comments.pdf
Author Response
The authors wish to express their deep gratitude to you for your interest and constructive comments on our paper. We have carefully considered the comments and modified the manuscript, and the modifications were marked up using the “Track Changes” function.
Please see the attachment for detailed modification instructions.
Author Response File: Author Response.docx
Reviewer 4 Report
Please refer to the attachment.
Comments for author File: Comments.docx
Author Response
The authors wish to express their deep gratitude to you for your interest and constructive comments on our paper. We have carefully considered the comments and modified the manuscript, and the modifications were marked up using the “Track Changes” function.
Please see the attachment for detailed modification instructions.
Author Response File: Author Response.docx
Round 2
Reviewer 1 Report
The manuscript has been improved. However some details could be performed in a better way, the manuscript can be recommended for publication in Processes journal.
Author Response
The authors wish to express their deep gratitude to you for your acknowledgement of the results of our manuscript improvements. We have spell-checked and improved some details, and the modifications were marked up using the “Track Changes” function.
Reviewer 2 Report
All comments have been addressed in this revision.
Author Response
The authors wish to express their deep gratitude to you for your acknowledgement of the results of our manuscript improvements. We have examined the manuscript in detail and made some modifications, and the modifications were marked up using the “Track Changes” function.
Reviewer 3 Report
Thanks for your attention and accuracy in improving the article. Introduction improved. The equations and methods of solving the mesh production process and its selection are clearly cracked.
- The meshing details were better displayed with a graph along the solution domain and the maximum and minimum values were indicated.(Y+ vs X)
Author Response
The authors wish to express their deep gratitude to you for your acknowledgement of the results of our manuscript improvements. We have examined the manuscript in detail and made some modifications, and the modifications were marked up using the “Track Changes” function. Many thanks for the further comment. The grid numbers of each component of calculation domain were added, and the maximum value of y+ in the pump impeller area was supplemented. Please see the second paragraph and Table 2 in section 3.1.2.
Reviewer 4 Report
NA
Author Response
The authors wish to express their deep gratitude to you for your acknowledgement of the results of our manuscript improvements. We have carefully checked the manuscript, and further revised and improved some details. The modifications were marked up using the “Track Changes” function.
Thanks a lot!