Investigation on Safety Dynamic Evolution Mechanism of a Distributed Low Carbon Manufacturing System with Large Time Delay
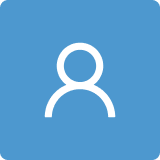
Round 1
Reviewer 1 Report
The paper may be published after English language edition
Author Response
Q.1: The paper may be published after English language edition.
Response: Thanks a lot for your comments. I am very much in favor of your proposal.
English grammatical style and word use have been checked and refined.
Author Response File: Author Response.pdf
Reviewer 2 Report
Main question addressed by the research: The work addresses the safety dynamic evolution mechanism of a distributed low carbon manufacturing system with large time delay.
Originality and relevance of the topic: The topic is relevant to the field and it considers a suitable model (research gap).
Added value of the paper: The manuscript takes into account the study of the low carbon manufacturing system, however the main purpose of it is not clearly stated. The paper should include what aspects are critical for these assessments and clearly explain why they are analysing those and why they are needed at the end of the Introduction.
Specific improvements for the paper to be considered:
- I think they have covered all the aspects required for the results, however the validation of the results is not clearly explained and this is essential in order to justify the reliability of the results.
- Introduction is weak and the context and application of the research is not properly set. Introduction should be improved.
- The low carbon perspective is not highlighted in this paper and previous studies do not show that, how to believe is it better? Section 4 is not clear about the more sustainable point of vied on the system.
- The conclusions are poor and they would need more elaboration so they clearly match the results.
Author Response
Main question addressed by the research: The work addresses the safety dynamic evolution mechanism of a distributed low carbon manufacturing system with large time delay. Originality and relevance of the topic: The topic is relevant to the field and it considers a suitable model (research gap).
Response: Thanks and noted.
Q.1: Added value of the paper: The manuscript takes into account the study of the low carbon manufacturing system, however the main purpose of it is not clearly stated. The paper should include what aspects are critical for these assessments and clearly explain why they are analysing those and why they are needed at the end of the Introduction.
Response: Thanks a lot for your comments. I am very much in favor of your proposal.
In the low-carbon intelligent manufacturing system, its future security risks mainly exist at the human-machine interface level. The disconnection or careless connection between human intelligence and machine intelligence in any link may lead to the generation and spread of risks in the entire manufacturing system. So, the main purpose is to reveal the inducing factors and safety dynamic evolution mechanism of frequent personal injury accident under low carbon manufacturing process, we have addressed this in Abstract and Introduction.
Safety is understood as a main obstacle for introducing human-robot collaboration in industrial production. Although there are some researches contributing to human-machine safety, the nonlinear dynamic evolution rule of the safety under low carbon manufacturing process was not revealed, and the human careless has time lag effect and influence on the safety in the low carbon manufacturing process. Therefore, this paper establishes a safety-careless dynamic evolution model of a distributed low carbon manufacturing system with large time delay and investigates its inducing factors and safety dynamic evolution mechanism, enhancing safety human-machine performance and working efficiency for low carbon manufacturing system. We have addressed these description in the Introduction.
Q.2: I think they have covered all the aspects required for the results, however the validation of the results is not clearly explained and this is essential in order to justify the reliability of the results.
Response: Thanks a lot for your comments. I am very much in favor of your proposal.
In section 3.2, mathematical analysis of the dynamic evolution model with large time delay and dynamic evolution has been carried out by 4 theorems and 4 proofs, which demonstrate the validity and correctness of the nonlinear dynamic evolution model of the human-machine safety system.
Q.3: Introduction is weak and the context and application of the research is not properly set. Introduction should be improved.
Response: Thanks a lot for your comments. I am very much in favor of your proposal.
Introduction has been revised as follows:
"In recent years, green low-carbon intelligent manufacturing has become the core technology to enhance the overall competitiveness of the global manufacturing industry [1]. Fundamentally, green and low-carbon intelligent manufacturing is to change each process of traditional manufacturing with the help of the constantly developing modern advanced technology, and create a new manufacturing form and mode. From the operating level, synergy of mechanical properties between human and machine in the traditional manufacturing process is developed toward a higher level of synergy of intelligence between human and machine intelligence, reducing the influence of human intelligence defects on manufacturing, and fully taking advantage of the machine intelligence to compensate for the lack of human intelligence. With the application of information technology and intelligent technology, the traditional operation interface and its management mode are changed, which will greatly increase the security risk of the future human-machine manufacturing system, and even contain new possible social risks. In such low-carbon intelligent manufacturing systems, its future security risks mainly exist at the human-machine interface level. The disconnection or careless connection between human intelligence and machine intelligence in any link may lead to the generation and spread of risks in the entire manufacturing system, and lead to the collapse of the system. Therefore, low-carbon intelligent manufacturing system is a highly complex human-machine cooperation system. Cooperation and safety problems are the main problems faced by the system, and effective human-machine cooperation is an important guarantee to ensure the safety and efficiency of the system [2]. It is quite necessary to investigate human-machine safety system under low carbon manufacturing process.
Safety is understood as a main obstacle for introducing human-robot collaboration in industrial production. There are some studies contributing to human-machine safety. For example, on the basis of Human Cyber Physical fusion intelligence, Liu et al. [3] discussed the mechanism of intelligent manufacturing system with HCP fusion and collaboration, and explored the HCP data fusion mechanism, collaboration mechanism and interaction mechanism. For concurrent simultaneous consideration of reliability and safety of manufacturing systems as well as flexibility and performance, a specialized control architecture was proposed by Ding et al. [4], they extended the architecture by a specific technique for the strategic controller: For the case of an intelligent manufacturing system which reacts adaptively to a human operator, control trajectories for a robot arm are computed online such that collision with the operator is excluded. The computation is based on solving a mixed-integer programming problem that takes a dynamic safety area around the operator into account as constraint. Human-machine interaction (HMI) safety for cyber-physical systems is critical and its analysis is mandatory in many domains such as SCADA, autonomous cars, and medical devices. Generation of dynamic accedent scenarios is the cornerstone of safety analysis. Fan et al. [5] presented a platform and associated methodology to effectively generate accident scenarios by modeling HMI errors using model-level fault injection, followed by simulation to produce dynamic evolutions of accident scenarios. Results showed that human mode confusion triggered by false displays may lead to severe accidents. In the study of Hanna et al. [6], the difference between traditional collaborative robots and intelligent human-robot collaboration was analyzed and a new safety approach was suggested, called Deliberative safety, which allows the humans and robots to switch between different safety measures based on the need for flexibility or efficiency to reach production goals. While considering system performance, a taxonomy was proposed to better support the design of deliberative safety as well as five safety measures was used in a deliberative safety approach, including perimeter safety, zone safety, reactive safety, planned and active safety, and when used together, they can enable intelligent human-robot collaboration.
For the safety studies under low carbon manufacturing process from previous works, the static safety evaluation method [7] was used to show that the safety index is in a certain range, but it can not be used to reveal the real dynamic evolution rule of the safety under low carbon manufacturing process. Obviously, the static safety evaluation method is easy to cause the inconsistent phenomena that static safety evaluation and safety trend did not coincide with accident rate in the practical process. The dynamic evolution theory [8-10] is a nonlinear dynamic and unbalanced evolution process theory [11] which is based on the non-constructive, non-human design principles of the rational evolution [12,13] and applied in vehicle-road safety [14], reactor safety[15], lithium-ion pouch cells safety[16], automated terminals safety[17], etc., but this theory has not been employed in safety evaluation of the low carbon manufacturing system. In a low-carbon intelligent manufacturing system, there is highly complex dynamic human-machine cooperation in the human-machine interface, and safety dynamic evolution of the inducing factors from human and equipment can lead to the generation and spread of risks in the system. So, it is very urgent how to effectively re-veal the inducing factors of frequent personal injury accident causing from mechanical equipment problem or human problem under low carbon manufacturing process. Human-machine safety engineering principle provides a very good idea for knowing the frequent personal injury phenomenon from the viewpoint of system [18,19], effectively overcoming one-sidedness shortcomings [20,21] and putting forward the feasible safety countermeasures. In addition, the human careless has time lag effect and influence on the safety in the low carbon manufacturing process, namely the effects on the safety caused by the careless will be shown after a certain period of time.
Therefore, the large time delay is necessary to be considered when a dynamic evolution model of the human-machine safety is established by taking advantage of time delay differential formula theory [20-23]. In this paper, human factors for safety accidents under the distributed low carbon manufacturing process is analyzed firstly. Then, safety-careless dynamic evolution model of a distributed low carbon manufacturing system with large time delay is established. Finally, low carbon level evaluation of a human-machine safety system under low carbon manufacturing process and application case of this dynamic evolution model are investigated. This work will provide theoretical basis for the safety evaluation and control of the human-machine safety system under low carbon manufacturing process. "
Q.4: The low carbon perspective is not highlighted in this paper and previous studies do not show that, how to believe is it better? Section 4 is not clear about the more sustainable point of vied on the system.
Response: Thanks a lot for your comments. I am very much in favor of your proposal.
This manuscript is mainly to investigate the inducing factors and safety dynamic evolution mechanism of frequent personal injury accident under low carbon manufacturing process. The research object is the distributed low carbon manufacturing system with large time delay. In section 4.1, low carbon level evaluation of an application case about radial tire casing process has been investigated, which presents it is of good low carbon manufacturing system. Further low carbon investigation on low carbon manufacturing system with large time delay will be carried out in our future studies and propose more sustainable point of view for this system.
Q.5: The conclusions are poor and they would need more elaboration so they clearly match the results.
Response: Thanks a lot for your comments. Sorry for my carelessness, I am very much in favor of your proposal.
The conclusions has been revised as follows:
"(1) The dynamic evolution simulation results based on the mathematical analysis on the nonlinear dynamic evolution model demonstrate the validity and correctness of the nonlinear dynamic evolution model of the human-machine safety system.
(2) The qualitative analysis on the nonlinear dynamic evolution and the trend of the human-machine safety with the large time delay reveals the interaction evolution model with large time delay between the carelessness level and the safety level in four dynamic areas such as the safety area â… , the deterioration area â…¡, the asymptotically stable safety area â…¢ and the enhancement area â…£ of the safety ability.
(3) There are two singularities such as E1(0, 0) and E2(u0, v0) in the dynamic evolution model of the man-machine safety system with large time delay under low carbon manufacturing process; when the singularity El(0, 0) is an asymptotically stable point and unstable point, respectively, the area â… , area â…¡ and area â…£ have the basically same evolution patterns, but the area â…¢ has the different evolution state; another one unstable point E2(u0, v0) can lead to divergent oscillation in the area â… , area â…¡, area â…¢ and area â…£, where the safety level of the man-machine safety system eventually tend to be collapsed with time.
(4) For qualitative analysis on the nonlinear safety dynamic evolution trend, when the deterioration degree of the carelessness level is under the line DR, if the careless-ness level is no longer increased and safety level is a fixed value, the state of the safety level can be returned to the development area as long as the operation level and rapid strain ability is improved; when the safety state of the human-machine safety system is beyond the development area of the man-machine safety system, if the operation level and rapid strain ability is no longer increased and the carelessness level is a fixed value, the state of the safety level can be returned to the development area as long as the carelessness level can be overcome.
(5) Application case results of radial tyre casing process show that the overall evaluation grade of the low-carbon development trend is "good", but low-carbon structure and management need to be optimized; the equilibrium points of the human-machine safety system under low carbon manufacturing process are El=(0, 0) and E2=( 0.5333, 0.2489), and the changes of the carelessness level have a serious block effect on the safety development with time."
Author Response File: Author Response.pdf
Reviewer 3 Report
This manuscript set out to investigate the usefulness of a distributed low carbon manufacturing system with significant time delay through a nonlinear safety dynamic evolution model was developed. The simulation results of the mathematical analysis and dynamic evolution also serve to confirm the accuracy of the established model. According to the findings of a qualitative analysis of the nonlinear safety dynamic evolution and trend of man-machine safety in a low carbon manufacturing process, there is an interaction evolution model of carelessness and safety level in the four dynamic regions, such as the safety area I, the deterioration area II, the asymptotically stable safety area III, and the enhancement area IV of the safety ability. Additionally, the findings might serve as a theoretical foundation for the assessment of safety and management of distributed low carbon production. I think that the current manuscript is good and needs minor modifications as follows:
1- The introduction provides a good, generalized background of the topic that quickly gives the reader an appreciation of the wide range of applications for this technology. However, to make the introduction more substantial, the author may wish to provide several references to substantiate the claim made in the first sentence " ......... but it can not be used to reveal the real dynamic evolution rule of the safety under low carbon manufacturing process." (that is, provide references to other groups who do or have done research in this area).
2- The second sentence should explains the research to current and potential of low carbon manufacturing process.
3- This sentence helpfully explains the motivation for the manuscript "It is very urgent how to effectively reveal the inducing factors of frequent personal injury accident causing from mechanical equipment problem or human problem under low carbon manufacturing process" However, to make the motivation clearer and to differentiate the paper some more from other applied papers, the author may wish to provide another sentence giving examples of some of the applications of this technology, along with appropriate references.
4- The experimental apparatus is quite standard, and is appropriate for the study, especially given that the main focus of the paper was the large time delay is necessary to be considered when a dynamic evolution model of the human-machine safety is established by taking advantage of time delay differential formula theory. However, I think the research objectives for this study need to be made clearer in specific points.
5- Section 2 "Analysis on human factors for safety ......." It can be formulated on the basis that it is a "Theoretical Framework"
6- Figure 5. Technological process of radial tyre casing (It seems that the use of red color in writing with a blue background is stressful for the eye, please choose calm colors).
7- The literature cited is relevant to the study, but there are several instances, which have been noted above, in which the author makes assertions without substantiating them with references.
Author Response
This manuscript set out to investigate the usefulness of a distributed low carbon manufacturing system with significant time delay through a nonlinear safety dynamic evolution model was developed. The simulation results of the mathematical analysis and dynamic evolution also serve to confirm the accuracy of the established model. According to the findings of a qualitative analysis of the nonlinear safety dynamic evolution and trend of man-machine safety in a low carbon manufacturing process, there is an interaction evolution model of carelessness and safety level in the four dynamic regions, such as the safety area I, the deterioration area II, the asymptotically stable safety area III, and the enhancement area IV of the safety ability. Additionally, the findings might serve as a theoretical foundation for the assessment of safety and management of distributed low carbon production. I think that the current manuscript is good and needs minor modifications as follows:
Q.1: The introduction provides a good, generalized background of the topic that quickly gives the reader an appreciation of the wide range of applications for this technology. However, to make the introduction more substantial, the author may wish to provide several references to substantiate the claim made in the first sentence " ......... but it can not be used to reveal the real dynamic evolution rule of the safety under low carbon manufacturing process." (that is, provide references to other groups who do or have done research in this area).
Response: Thanks a lot for your comments. I am very much in favor of your proposal.
Several references have been provided to support the above sentence. The detail description is as follows.
"Safety is understood as a main obstacle for introducing human-robot collaboration in industrial production. There are some studies contributing to human-machine safety. For example, on the basis of Human Cyber Physical fusion intelligence, Liu et al. [3] discussed the mechanism of intelligent manufacturing system with HCP fusion and collaboration, and explored the HCP data fusion mechanism, collaboration mechanism and interaction mechanism. For concurrent simultaneous consideration of reliability and safety of manufacturing systems as well as flexibility and performance, a specialized control architecture was proposed by Ding et al. [4], they extended the architecture by a specific technique for the strategic controller: For the case of an intelligent manufacturing system which reacts adaptively to a human operator, control trajectories for a robot arm are computed online such that collision with the operator is excluded. The computation is based on solving a mixed-integer programming problem that takes a dynamic safety area around the operator into account as constraint. Human-machine interaction (HMI) safety for cyberphysical systems is critical and its analysis is mandatory in many domains such as SCADA, autonomous cars, and medical devices. Generation of dynamic accedent scenarios is the cornerstone of safety analysis. Fan et al. [5] presented a platform and associated methodology to effectively generate accident scenarios by modeling HMI errors using model-level fault injection, followed by simulation to produce dynamic evolutions of accident scenarios. Results showed that human mode confusion triggered by false displays may lead to severe accidents. In the study of Hanna et al. [6], the difference between traditional collaborative robots and intelligent human-robot collaboration was analyzed and a new safety approach was suggested, called Deliberative safety, which allows the humans and robots to switch between different safety measures based on the need for flexibility or efficiency to reach production goals. While considering system performance, a taxonomy was proposed to better support the design of deliberative safety as well as five safety measures was used in a deliberative safety approach, including perimeter safety, zone safety, reactive safety, planned and active safety, and when used together, they can enable intelligent human-robot collaboration.
For the safety studies under low carbon manufacturing process from previous works, the static safety evaluation method [7] was used to show that the safety index is in a certain range, but it can not be used to reveal the real dynamic evolution rule of the safety under low carbon manufacturing process. Obviously, the static safety evaluation method is easy to cause the inconsistent phenomena that static safety evaluation and safety trend did not coincide with accident rate in the practical process. "
[3] Liu Q., Liu M., Zhou H.L., Yan F., Ma Y.Y., Shen W. M. Intelligent manufacturing system with human-cyber-physical fusion and collaboration for process fine control. Journal of Manufacturing Systems, 2022, 64: 149–169.
[4] Ding H., Kain S., Schiller F., Stursberg O. Increasing Reliability of Intelligent Manufacturing Systems by Adaptive Optimization and Safety Supervision. Proceedings of the 7th IFAC Symposium on Fault Detection, Supervision and Safety of Technical Processes Barcelona, Spain, June 30 - July 3, 2009.
[5] Fana C.F., Chana C.C., Yua H.Y., Yih S. A simulation platform for human-machine interaction safety analysis of cyber-physical systems. International Journal of Industrial Ergonomics, 2018, 68: 89–100.
[6] Hanna A, Larsson S., Götvall P., Bengtsson K. Deliberative safety for industrial intelligent human–robot collaboration: Regu-latory challenges and solutions for taking the next step towards industry 4.0. Robotics and Computer–Integrated Manufacturing, 2022, 78:102386.
Q.2: The second sentence should explains the research to current and potential of low carbon manufacturing process.
Response: Thanks a lot for your comments. I am very much in favor of your proposal.
Following sentences have been presented to explain back ground, current development and research necessity of the low carbon manufacturing process and its human-machine safety.
"In recent years, green low-carbon intelligent manufacturing has become the core technology to enhance the overall competitiveness of the global manufacturing industry [1]. Fundamentally, green and low-carbon intelligent manufacturing is to change each process of traditional manufacturing with the help of the constantly developing modern advanced technology, and create a new manufacturing form and mode. From the operating level, synergy of mechanical properties between human and machine in the traditional manufacturing process is developed toward a higher level of synergy of intelligence between human and machine intelligence, reducing the influence of human intelligence defects on manufacturing, and fully taking advantage of the machine intelligence to compensate for the lack of human intelligence. With the application of information technology and intelligent technology, the traditional operation interface and its management mode are changed, which will greatly increase the security risk of the future human-machine manufacturing system, and even contain new possible social risks. In such low-carbon intelligent manufacturing systems, its future security risks mainly exist at the human-machine interface level. The disconnection or careless connection between human intelligence and machine intelligence in any link may lead to the generation and spread of risks in the entire manufacturing system, and lead to the collapse of the system. Therefore, low-carbon intelligent manufacturing system is a highly complex human-machine cooperation system. Cooperation and safety problems are the main problems faced by the system, and effective human-machine cooperation is an important guarantee to ensure the safety and efficiency of the system [2]. It is quite necessary to investigate human-machine safety system under low carbon manufacturing process. "
[1] Shojaeinasaba A., Charter T., Jalayer M., Khadivi M., Ogunfowora O., Raiyani N., Yaghoubi M., Najjaran H. Intelligent manufacturing execution systems: A systematic review. Journal of Manufacturing Systems, 2022, 62: 503-522.
[2] Villani V., Pini F., Leali F., Secchi C. Survey on humanrobot collaboration in industrial settings: Safety, intuitive interfaces and applications. Mechatronics, 2018, 55: 248-266.
Q.3: This sentence helpfully explains the motivation for the manuscript "It is very urgent how to effectively reveal the inducing factors of frequent personal injury accident causing from mechanical equipment problem or human problem under low carbon manufacturing process" However, to make the motivation clearer and to differentiate the paper some more from other applied papers, the author may wish to provide another sentence giving examples of some of the applications of this technology, along with appropriate references.
Response: Thanks a lot for your comments. I am very much in favor of your proposal.
Other sentences have been provided as follows to make the motivation clearer in this manuscript. Some of the application examples have been given.
" For the safety studies under low carbon manufacturing process from previous works, the static safety evaluation method [7] was used to show that the safety index is in a certain range, but it can not be used to reveal the real dynamic evolution rule of the safety under low carbon manufacturing process. Obviously, the static safety evaluation method is easy to cause the inconsistent phenomena that static safety evaluation and safety trend did not coincide with accident rate in the practical process. The dynamic evolution theory [8-10] is a nonlinear dynamic and unbalanced evolution process theory [11] which is based on the non-constructive, non-human design principles of the rational evolution [12,13]and applied in vehicle-road safety [14], reactor safety[15], lithium-ion pouch cells safety[16], automated terminals safety[17], etc., but this theory has not been employed in safety evaluation of the low carbon manufacturing system. In a low-carbon intelligent manufacturing system, there is highly complex dynamic human-machine cooperation in the human-machine interface, and safety dynamic evolution of the inducing factors from human and equipment can lead to the generation and spread of risks in the system. So, it is very urgent how to effectively reveal the inducing factors of frequent personal injury accident causing from mechanical equipment problem or human problem under low carbon manufacturing process. "
[16] Zhou M.Z., Hu L.L., Chen S.R., Zhao X. Different mechanical-electrochemical coupled failure mechanism and safety evaluation of lithium-ion pouch cells under dynamic and quasi-static mechanical abuse. Journal of Power Sources, 2021, 497: 229897.
[17] Li J.J., Yu A.Q., Xu B.W. Risk propagation and evolution analysis of multi-level handlings at automated terminals based on double-layer dynamic network model. Physica A: Statistical Mechanics and its Applications, 2022, 605: 127963.
Q.4: The experimental apparatus is quite standard, and is appropriate for the study, especially given that the main focus of the paper was the large time delay is necessary to be considered when a dynamic evolution model of the human-machine safety is established by taking advantage of time delay differential formula theory. However, I think the research objectives for this study need to be made clearer in specific points.
Response: Thanks a lot for your comments. I am very much in favor of your proposal.
In the low-carbon intelligent manufacturing system, its future security risks mainly exist at the human-machine interface level. The disconnection or careless connection between human intelligence and machine intelligence in any link may lead to the generation and spread of risks in the entire manufacturing system. Safety is understood as a main obstacle for introducing human-robot collaboration in industrial production. However, the nonlinear safety dynamic evolution mechanism under low carbon manufacturing process was not revealed, and the human careless has time lag effect and influence on the safety in the low carbon manufacturing process. Therefore, the research objective for this study is to reveal the inducing factors and safety dynamic evolution mechanism of frequent personal injury accident under low carbon manufacturing process, we have addressed this description in Abstract and Introduction.
"Therefore, the large time delay is necessary to be considered when a dynamic evolution model of the human-machine safety is established by taking advantage of time delay differential formula theory [20-23]. In this paper, human factors for safety accidents under the distributed low carbon manufacturing process is analyzed firstly. Then, safety-careless dynamic evolution model of a distributed low carbon manufacturing system with large time delay is established. Finally, low carbon level evaluation of a human-machine safety system under low carbon manufacturing process and application case of this dynamic evolution model are investigated. This work will provide theoretical basis for the safety evaluation and control of the human-machine safety system under low carbon manufacturing process. "
Q.5: Section 2 "Analysis on human factors for safety ......." It can be formulated on the basis that it is a "Theoretical Framework".
Response: Thanks a lot for your comments. I am very much in favor of your proposal.
Section 2 "Analysis on human factors for safety ......." has been revised as "Theoretical framework ".
Q.6: Figure 5. Technological process of radial tyre casing (It seems that the use of red color in writing with a blue background is stressful for the eye, please choose calm colors).
Response: Thanks a lot for your comments. I am very much in favor of your proposal.
The blue background has been revised in the Fig.5 according to your suggestion, which is comfortable for readers.
Figure 5. Technological process of radial tyre casing.
Q.7: The literature cited is relevant to the study, but there are several instances, which have been noted above, in which the author makes assertions without substantiating them with references.
Response: Thanks a lot for your comments. I am very much in favor of your proposal.
Relevant references have been cited and presented in Introduction to makes above assertions more convincing.
[1] Shojaeinasaba A., Charter T., Jalayer M., Khadivi M., Ogunfowora O., Raiyani N., Yaghoubi M., Najjaran H. Intelligent manufacturing execution systems: A systematic review. Journal of Manufacturing Systems, 2022, 62: 503-522.
[2] Villani V., Pini F., Leali F., Secchi C. Survey on humanrobot collaboration in industrial settings: Safety, intuitive interfaces and applications. Mechatronics, 2018, 55: 248-266.
[3] Liu Q., Liu M., Zhou H.L., Yan F., Ma Y.Y., Shen W. M. Intelligent manufacturing system with human-cyber-physical fusion and collaboration for process fine control. Journal of Manufacturing Systems, 2022, 64: 149–169.
[4] Ding H., Kain S., Schiller F., Stursberg O. Increasing Reliability of Intelligent Manufacturing Systems by Adaptive Optimization and Safety Supervision. Proceedings of the 7th IFAC Symposium on Fault Detection, Supervision and Safety of Technical Processes Barcelona, Spain, June 30 - July 3, 2009.
[5] Fana C.F., Chana C.C., Yua H.Y., Yih S. A simulation platform for human-machine interaction safety analysis of cyber-physical systems. International Journal of Industrial Ergonomics, 2018, 68: 89–100.
[6] Hanna A, Larsson S., Götvall P., Bengtsson K. Deliberative safety for industrial intelligent human–robot collaboration: Regu-latory challenges and solutions for taking the next step towards industry 4.0. Robotics and Computer–Integrated Manufacturing, 2022, 78:102386.
[16] Zhou M.Z., Hu L.L., Chen S.R., Zhao X. Different mechanical-electrochemical coupled failure mechanism and safety evaluation of lithium-ion pouch cells under dynamic and quasi-static mechanical abuse. Journal of Power Sources, 2021, 497: 229897.
[17] Li J.J., Yu A.Q., Xu B.W. Risk propagation and evolution analysis of multi-level handlings at automated terminals based on double-layer dynamic network model. Physica A: Statistical Mechanics and its Applications, 2022, 605: 127963.
Author Response File: Author Response.pdf
Round 2
Reviewer 2 Report
The paper has significantly improved
Author Response
Q.1: English language and style are fine/minor spell check required.
Response: Thanks a lot for your comments. I am very much in favor of your proposal.
English language and style had been checked and refined, and reference style had been checked and revised.
And revised portion had been marked in red color texts in the paper.
Author Response File: Author Response.doc