Surface Science of Degradation and Surface Protection
A special issue of Coatings (ISSN 2079-6412). This special issue belongs to the section "Surface Characterization, Deposition and Modification".
Deadline for manuscript submissions: 20 July 2025 | Viewed by 11445
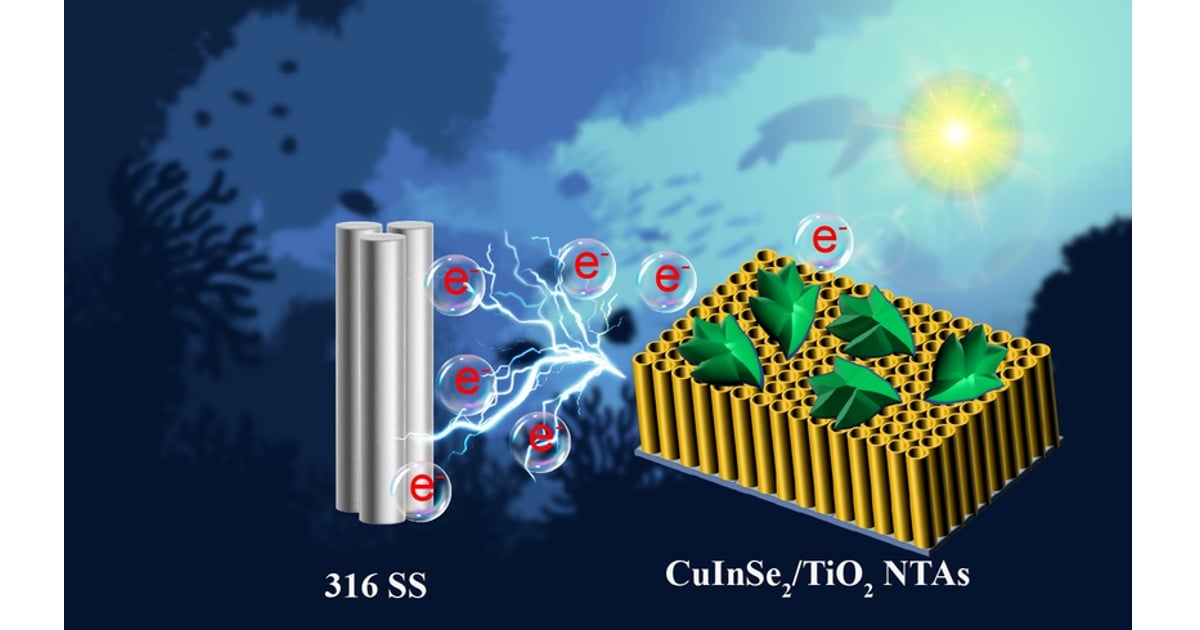
Special Issue Editors
Interests: cryogenics; magnetism-based characterization of metals and alloys; sustainable metallurgy and materials; hydrogen plasma-based reduction and hydrogen-based direct reduction of oxides and ores; thermal pro-cessing of alloys and implications on microstructure, surface and properties
Special Issues, Collections and Topics in MDPI journals
Interests: modified metallic surfaces; mechanical properties; microstructure; isotope analysis; wear; oxidation of metallic surfaces; corrosion; chemical characterization of surfaces
Special Issues, Collections and Topics in MDPI journals
Interests: heat treatment; metallic materials; material sciences; mechanical properties; microstructure; wear; surface properties; coatings; biomaterials; corrosion
Special Issues, Collections and Topics in MDPI journals
Special Issue Information
Dear Colleagues,
Different types of coatings and metal surfaces are a broad material group that impacts many aspects of everyday life. Due to their unique combination of properties, metallic surfaces, and organic/inorganic/self-healing coatings, which are used in various industries as protective elements (mechanical and corrosive), catalyzing media, optical materials, substrates, electrical conductors, magnetic media, biomaterials, etc. However, their applicability is often limited and plagued by degradation, which is a key factor for long-lasting material usage from both economic and sustainability perspectives. Degradation is a crude label for the deterioration of the material and/or its properties in exposed environments and/or conditions, ranging from static and dynamic mechanical loading to corrosive media and biological factors down to cyclic grinding and surface interaction with other materials. As such, it is vital to understand how the individual properties of the used metal coatings and metallic surfaces temporally evolve and are modified within their used environments and conditions.
For this reason, we are launching a new Special Issue in MDPI’s journal Coatings that aims to collect original research articles and review papers on the degradation of coatings and modified metallic surfaces. Contributions should focus on the fundamental characterization and understanding of the degradation processes under specific conditions, which are relevant for applying selected coatings/a modified surface. Both theoretical and experimental papers, as well as papers combining both aspects, are welcomed.
We look forward to receiving your contribution.
Dr. Matic Jovičević-Klug
Dr. Patricia Jovičević-Klug
Dr. László Tóth
Guest Editors
Manuscript Submission Information
Manuscripts should be submitted online at www.mdpi.com by registering and logging in to this website. Once you are registered, click here to go to the submission form. Manuscripts can be submitted until the deadline. All submissions that pass pre-check are peer-reviewed. Accepted papers will be published continuously in the journal (as soon as accepted) and will be listed together on the special issue website. Research articles, review articles as well as short communications are invited. For planned papers, a title and short abstract (about 100 words) can be sent to the Editorial Office for announcement on this website.
Submitted manuscripts should not have been published previously, nor be under consideration for publication elsewhere (except conference proceedings papers). All manuscripts are thoroughly refereed through a single-blind peer-review process. A guide for authors and other relevant information for submission of manuscripts is available on the Instructions for Authors page. Coatings is an international peer-reviewed open access monthly journal published by MDPI.
Please visit the Instructions for Authors page before submitting a manuscript. The Article Processing Charge (APC) for publication in this open access journal is 2600 CHF (Swiss Francs). Submitted papers should be well formatted and use good English. Authors may use MDPI's English editing service prior to publication or during author revisions.
Keywords
- organic and inorganic coatings
- self-healing coatings
- modified metallic surfaces
- degradation
- mechanical failure
- delamination
- corrosion
- biocorrosion
- tribology
- wear
Benefits of Publishing in a Special Issue
- Ease of navigation: Grouping papers by topic helps scholars navigate broad scope journals more efficiently.
- Greater discoverability: Special Issues support the reach and impact of scientific research. Articles in Special Issues are more discoverable and cited more frequently.
- Expansion of research network: Special Issues facilitate connections among authors, fostering scientific collaborations.
- External promotion: Articles in Special Issues are often promoted through the journal's social media, increasing their visibility.
- e-Book format: Special Issues with more than 10 articles can be published as dedicated e-books, ensuring wide and rapid dissemination.
Further information on MDPI's Special Issue policies can be found here.