New Insight of Powder Metallurgy: Microstructure, Durability and Mechanical Properties—2nd Edition
A special issue of Materials (ISSN 1996-1944). This special issue belongs to the section "Metals and Alloys".
Deadline for manuscript submissions: 20 June 2025 | Viewed by 2223
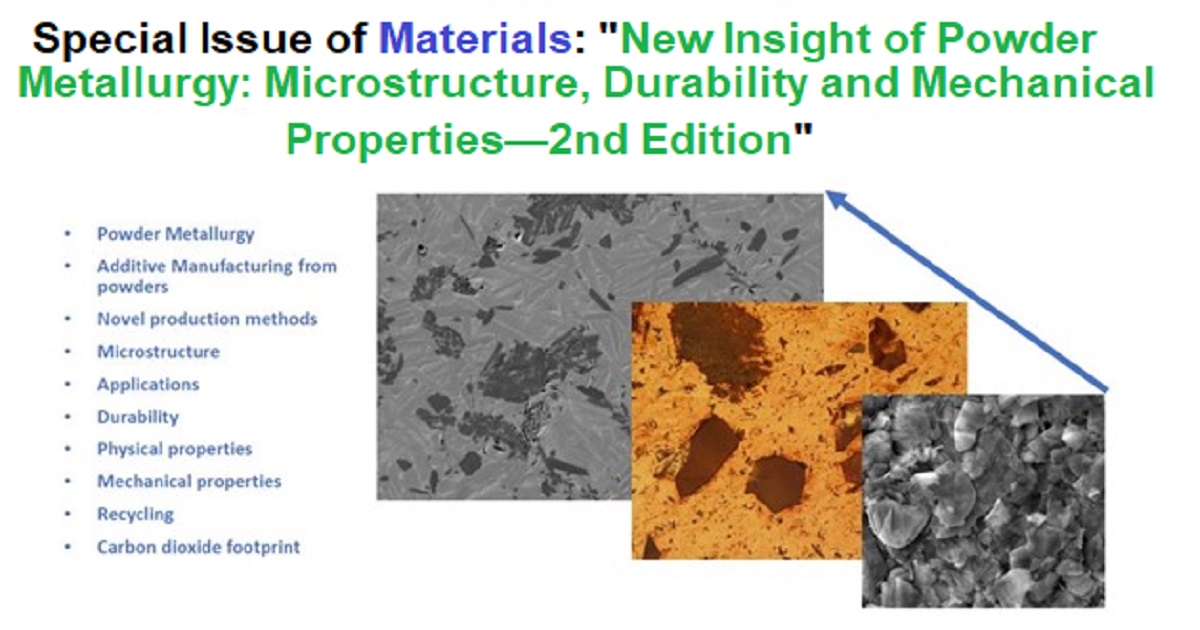
Special Issue Editors
Interests: powder metallurgy; metal matrix composites; copper–graphite; titanium; aluminum foams; concentrated solar power
Special Issues, Collections and Topics in MDPI journals
Interests: additive manufacturing; powder metallurgy; metal injection moulding; titanium alloys; metal foam; material modelling; solid mechanics
Special Issues, Collections and Topics in MDPI journals
Interests: thermal spray coatings; powder metallurgy; severe plastic deformation; ironmaking and steelmaking
Special Issues, Collections and Topics in MDPI journals
Special Issue Information
Dear Colleagues,
We would like to invite submissions to the second edition of this Special Issue of Materials focusing on the fundamental and applied aspects of novel materials fabrication using powder metallurgy technologies and their properties.
Powder metallurgy technologies offer flexibility in materials, microstructure and design, as major fractions of the material remain in the solid state and even insoluble material combinations can be employed.
Powder metallurgy methods are used for the manufacturing of materials where other property and shaping technologies cannot be applied. A key example is the additive manufacturing of materials from powders.
The high purity of powders, controlled at their production stage, together with the possibility of changing their size and morphology determine the end properties of powder metallurgy products and are highly attractive at material markets.
Papers dealing with sintering; process parameters; the influence of innovative preparation methods such as electric-current-assisted sintering, microwave radiation or lasers; and fully compacted materials or porous preforms or foams are of interest to this Special Issue.
Finally, contributions that focus on additive manufacturing preparation from powders are also highly welcome.
We hope to receive high-quality articles, communications, and reviews reporting advancements in the fascinating field of powder metallurgy.
Dr. Jaroslav Kováčik
Dr. Anchalee Manonukul
Prof. Dr. Pasquale Cavaliere
Guest Editors
Manuscript Submission Information
Manuscripts should be submitted online at www.mdpi.com by registering and logging in to this website. Once you are registered, click here to go to the submission form. Manuscripts can be submitted until the deadline. All submissions that pass pre-check are peer-reviewed. Accepted papers will be published continuously in the journal (as soon as accepted) and will be listed together on the special issue website. Research articles, review articles as well as short communications are invited. For planned papers, a title and short abstract (about 100 words) can be sent to the Editorial Office for announcement on this website.
Submitted manuscripts should not have been published previously, nor be under consideration for publication elsewhere (except conference proceedings papers). All manuscripts are thoroughly refereed through a single-blind peer-review process. A guide for authors and other relevant information for submission of manuscripts is available on the Instructions for Authors page. Materials is an international peer-reviewed open access semimonthly journal published by MDPI.
Please visit the Instructions for Authors page before submitting a manuscript. The Article Processing Charge (APC) for publication in this open access journal is 2600 CHF (Swiss Francs). Submitted papers should be well formatted and use good English. Authors may use MDPI's English editing service prior to publication or during author revisions.
Keywords
- powder metallurgy
- additive manufacturing from powders
- novel production methods
- microstructure
- applications
- durability
- physical properties
- mechanical properties
- recycling
- carbon dioxide footprint
Benefits of Publishing in a Special Issue
- Ease of navigation: Grouping papers by topic helps scholars navigate broad scope journals more efficiently.
- Greater discoverability: Special Issues support the reach and impact of scientific research. Articles in Special Issues are more discoverable and cited more frequently.
- Expansion of research network: Special Issues facilitate connections among authors, fostering scientific collaborations.
- External promotion: Articles in Special Issues are often promoted through the journal's social media, increasing their visibility.
- e-Book format: Special Issues with more than 10 articles can be published as dedicated e-books, ensuring wide and rapid dissemination.
Further information on MDPI's Special Issue policies can be found here.