Advanced Manufacturing Processes
A special issue of Applied Sciences (ISSN 2076-3417). This special issue belongs to the section "Mechanical Engineering".
Deadline for manuscript submissions: closed (20 December 2023) | Viewed by 10568
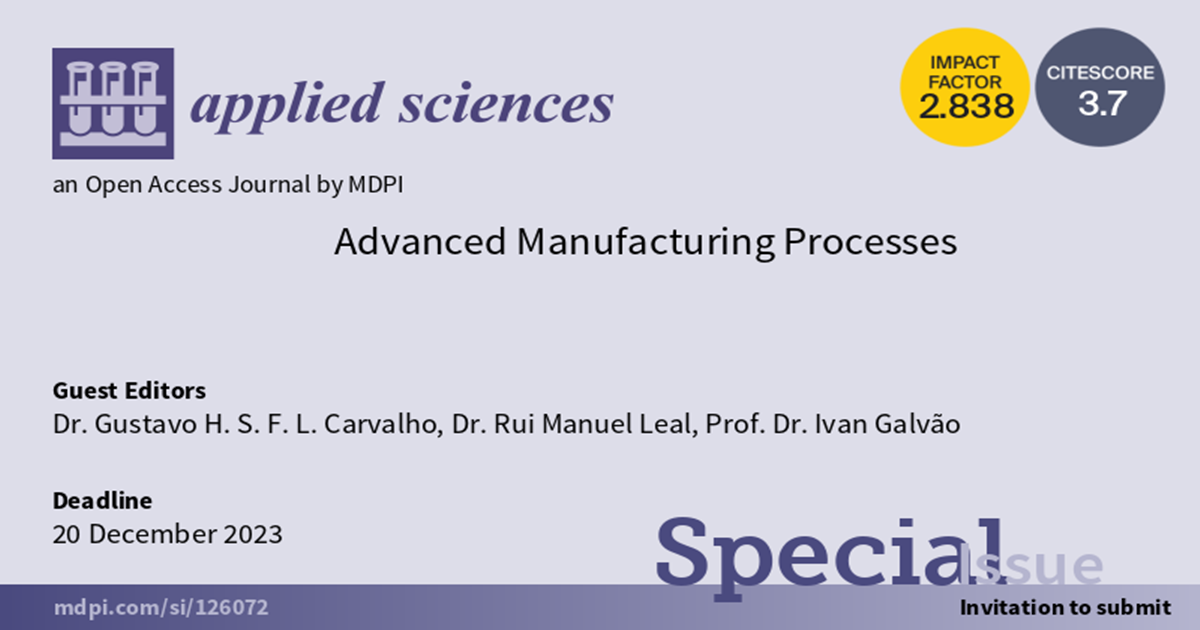
Special Issue Editors
2. CEMMPRE, Department of Mechanical Engineering, University of Coimbra, Rua Luís Reis Santos, 3030-788 Coimbra, Portugal
Interests: explosive welding; welding; additive manufacturing; WAAM; metallurgy; metallurgical characterization
2. CEMMPRE, Department of Mechanical Engineering, University of Coimbra, Rua Luís Reis Santos, 3030-788 Coimbra, Portugal
Interests: welding technology; processing technology; microstructural and mechanical characterization; friction stir welding; explosion welding
Special Issues, Collections and Topics in MDPI journals
2. CEMMPRE, Department of Mechanical Engineering, University of Coimbra, Rua Luís Reis Santos, 3030-788 Coimbra, Portugal
Interests: solid-state welding; friction stir welding; explosion welding; dissimilar materials welding; solid-state processing
Special Issues, Collections and Topics in MDPI journals
Special Issue Information
Dear Colleagues,
The advancement of engineering and the emergence of increasingly individualized and specific applications boost the need to develop advanced manufacturing processes capable of delivering all the required characteristics. These processes, which have very particular features or were developed more recently, deserve special attention in current manufacturing engineering research to overcome their challenges. This progress will spread the use of these processes, resulting in better quality components with lower manufacturing costs and lower environmental impact.
This Special Issue will publish high-quality, original research and review papers addressing manufacturing processes such as additive manufacturing technologies, solid-state welding processes (e.g., friction stir welding, explosive welding, magnetic pulse welding), advanced fusion welding and coating processes, powder metallurgy, among others. Different aspects related to these processes may be addressed, including process development, metallurgical characterization, machining, corrosion resistance, industrial applications, improvements in energy efficiency, sustainability and environmental impact, heat treatment and post-processing, case studies, and numerical modeling and simulation.
Dr. Gustavo H. S. F. L. Carvalho
Dr. Rui Manuel Leal
Dr. Ivan Galvão
Guest Editors
Manuscript Submission Information
Manuscripts should be submitted online at www.mdpi.com by registering and logging in to this website. Once you are registered, click here to go to the submission form. Manuscripts can be submitted until the deadline. All submissions that pass pre-check are peer-reviewed. Accepted papers will be published continuously in the journal (as soon as accepted) and will be listed together on the special issue website. Research articles, review articles as well as short communications are invited. For planned papers, a title and short abstract (about 100 words) can be sent to the Editorial Office for announcement on this website.
Submitted manuscripts should not have been published previously, nor be under consideration for publication elsewhere (except conference proceedings papers). All manuscripts are thoroughly refereed through a single-blind peer-review process. A guide for authors and other relevant information for submission of manuscripts is available on the Instructions for Authors page. Applied Sciences is an international peer-reviewed open access semimonthly journal published by MDPI.
Please visit the Instructions for Authors page before submitting a manuscript. The Article Processing Charge (APC) for publication in this open access journal is 2400 CHF (Swiss Francs). Submitted papers should be well formatted and use good English. Authors may use MDPI's English editing service prior to publication or during author revisions.
Keywords
- additive manufacturing
- solid-state welding
- friction stir welding
- impact welding processes
- explosive welding
- magnetic pulse welding
- advanced fusion welding processes
- powder metallurgy/sintering
- numerical modeling and simulation