Novel Analysis of Tribological Characterization in Machining Processes
A special issue of Applied Sciences (ISSN 2076-3417). This special issue belongs to the section "Mechanical Engineering".
Deadline for manuscript submissions: closed (20 December 2022) | Viewed by 5260
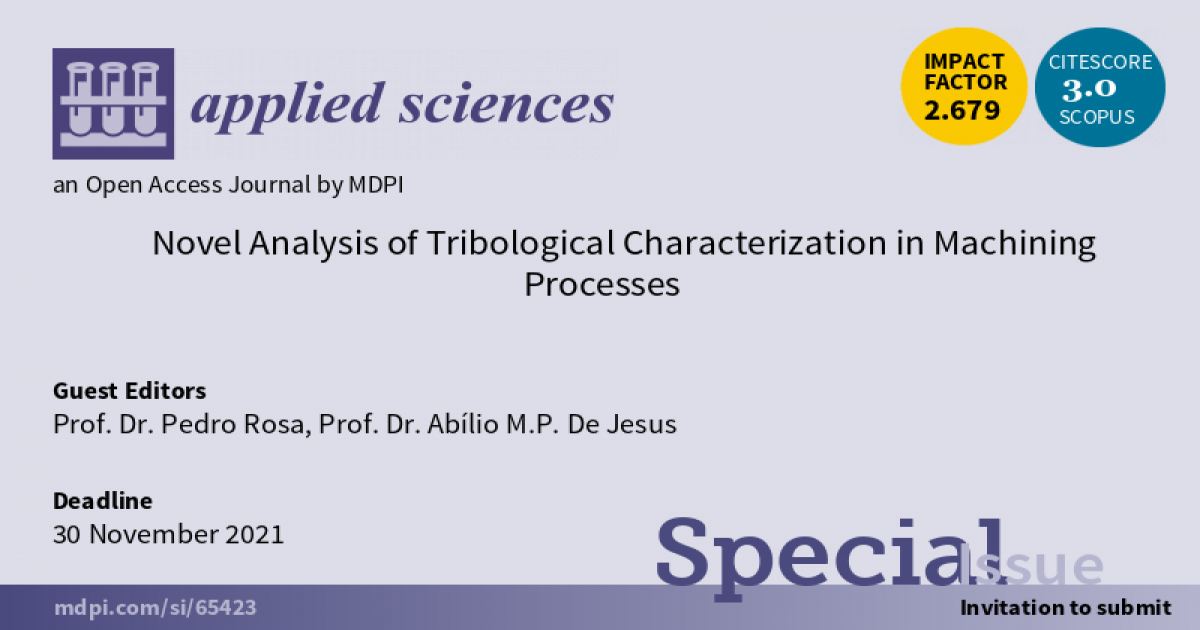
Special Issue Editors
Interests: machining; metal cutting; plasticity; tribology; ductile fracture; mechanical testing; machine tools
Interests: manufacturing processes; simulation; fracture mechanics
Special Issues, Collections and Topics in MDPI journals
Special Issue Information
In machining technologies, friction between the cutting tool and the chip is a key parameter that influences the productivity and quality of the machined part. Despite this, obtaining realistic friction input data for simulation-based analysis and optimization methodologies remains an issue for several reasons. First, tribological conditions in metal cutting are significantly different from those observed in the well-established tribology of machine elements and metal forming processes, thus hindering the use of reference values and experimental techniques. Second, theoretical models are based exclusively on the mathematical theory of plasticity, which limits the capability to perform a realistic modeling of the friction mechanics. Understanding the microstructural and tribo-chemical phenomena occurring during the formation and sliding of the chip over the rake surface is of utmost importance for a physically realistic simulation of the machining processes.
This Special Issue will focus on the latest advances in machining tribology related to the development of new experimental techniques and comprehensive theoretical models to support the effective simulation of the chip formation mechanics. Review articles and novel research papers are invited, covering the following areas:
- Original equipment and testing procedures focused on the interaction between chip, cutting tool, and surrounding environment for the independent characterization of friction.
- Theoretical modeling and simulation of machining in a more comprehensive and contextualized approach in the study of friction and wear mechanics, as well as for the optimization of process conditions and quality of machined parts.
- Novel contributions to the fundamental understanding of friction, lubrication, surface science, and advancement in the field of machining tribology are also objectives of this Special Issue.
- Lastly, but no less important, it is appropriate to include case studies and solved problems elucidated with sufficient schematics, diagrams, and references to serve as a perfect textbook for targeted readers.
Prof. Dr. Pedro Rosa
Prof. Dr. Abílio M.P. De Jesus
Guest Editors
Manuscript Submission Information
Manuscripts should be submitted online at www.mdpi.com by registering and logging in to this website. Once you are registered, click here to go to the submission form. Manuscripts can be submitted until the deadline. All submissions that pass pre-check are peer-reviewed. Accepted papers will be published continuously in the journal (as soon as accepted) and will be listed together on the special issue website. Research articles, review articles as well as short communications are invited. For planned papers, a title and short abstract (about 100 words) can be sent to the Editorial Office for announcement on this website.
Submitted manuscripts should not have been published previously, nor be under consideration for publication elsewhere (except conference proceedings papers). All manuscripts are thoroughly refereed through a single-blind peer-review process. A guide for authors and other relevant information for submission of manuscripts is available on the Instructions for Authors page. Applied Sciences is an international peer-reviewed open access semimonthly journal published by MDPI.
Please visit the Instructions for Authors page before submitting a manuscript. The Article Processing Charge (APC) for publication in this open access journal is 2400 CHF (Swiss Francs). Submitted papers should be well formatted and use good English. Authors may use MDPI's English editing service prior to publication or during author revisions.
Keywords
- machining
- metal cutting
- tribology
- friction
- lubrication
- wear
- dry sliding
- surface roughness
- tribo-oxidation
- stick–slip