Welding and Joining Technologies: Processes, Parameters, Structures, Properties and Simulations
A special issue of Materials (ISSN 1996-1944). This special issue belongs to the section "Materials Physics".
Deadline for manuscript submissions: 20 August 2024 | Viewed by 3337
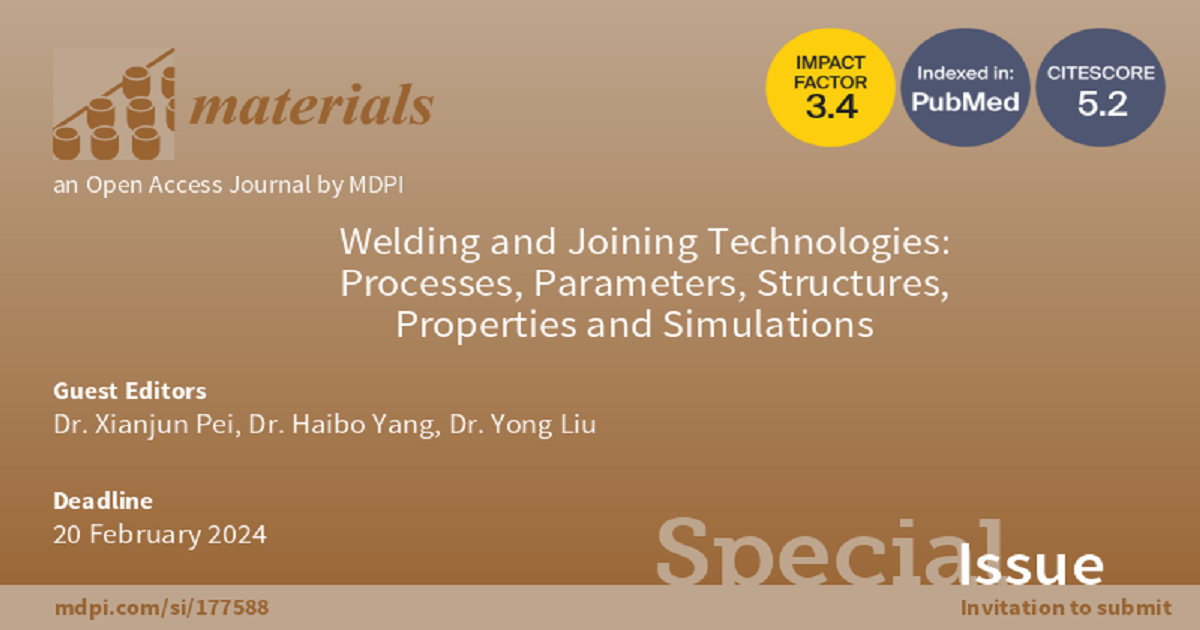
Special Issue Editors
Interests: fatigue and fracture; welding and joining; structural integrity; residual stress; computational method; mechanics of welded structures
Special Issues, Collections and Topics in MDPI journals
2. School of Ocean Engineering, Harbin Institute of Technology at Weihai, Weihai 264200, China
Interests: fatigue performance analysis of welded structures; multiaxial stress state; fatigue lifetime prediction; fatigue crack initiation and propagation; traction structural stress method
Special Issues, Collections and Topics in MDPI journals
Special Issue Information
Dear Colleagues,
We are pleased to announce the launch of a Special Issue on "Welding and Joining Technologies: Processes, Parameters, Structures, Properties and Simulations" in Materials. This Special Issue aims to provide a platform for scientists and academicians to share their latest research findings on and insights into various aspects of welding and joining technologies.
Scope of submissions: The Special Issue invites original research articles, review papers, and case studies that contribute to the advancement of knowledge in the fields of welding and joining. The topics of interest include, but are not limited to, the following:
- Welding processes: Arc welding, resistance welding, laser welding, electron beam welding, etc.
- Joining techniques: Adhesive bonding, mechanical fastening, soldering, brazing, etc.
- Parameter optimization: Investigation and optimization of welding and joining parameters for improved performance and efficiency.
- Structures and properties: Characterization and evaluation of welded as well as joined structures and their mechanical, thermal, and corrosion properties.
- Simulation and modeling: Development and application of simulation and modeling techniques for predicting as well as analyzing welding and joining processes and their outcomes.
- Emerging trends and technologies: Innovative approaches, materials, and technologies in welding and joining.
We look forward to your contributions and believe that this Special Issue will significantly contribute to the advancement of welding and joining technologies. Should you have any inquiries, please do not hesitate to contact the Editorial Office.
Sincerely,
Dr. Xianjun Pei
Dr. Haibo Yang
Dr. Yong Liu
Guest Editors
Manuscript Submission Information
Manuscripts should be submitted online at www.mdpi.com by registering and logging in to this website. Once you are registered, click here to go to the submission form. Manuscripts can be submitted until the deadline. All submissions that pass pre-check are peer-reviewed. Accepted papers will be published continuously in the journal (as soon as accepted) and will be listed together on the special issue website. Research articles, review articles as well as short communications are invited. For planned papers, a title and short abstract (about 100 words) can be sent to the Editorial Office for announcement on this website.
Submitted manuscripts should not have been published previously, nor be under consideration for publication elsewhere (except conference proceedings papers). All manuscripts are thoroughly refereed through a single-blind peer-review process. A guide for authors and other relevant information for submission of manuscripts is available on the Instructions for Authors page. Materials is an international peer-reviewed open access semimonthly journal published by MDPI.
Please visit the Instructions for Authors page before submitting a manuscript. The Article Processing Charge (APC) for publication in this open access journal is 2600 CHF (Swiss Francs). Submitted papers should be well formatted and use good English. Authors may use MDPI's English editing service prior to publication or during author revisions.
Keywords
- welding and joining
- welding metallurgy
- weldability
- residual stress
- computational method
- mechanics of welded structures
- parameter optimization
- fatigue and fracture
- structural integrity