A Characteristic Study of Polylactic Acid/Organic Modified Montmorillonite (PLA/OMMT) Nanocomposite Materials after Hydrolyzing
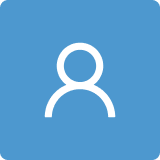
Round 1
Reviewer 1 Report
The authors use two terms: intercalation and exfoliation of OMMT. This is a significant difference because an intercalated structure is one in which the polymer chains are located between single, parallel silicate layers. In the exfoliated structure - silicate layers are dispersed in different directions in the polymer matrix, so the distances between the plates are greater than in the case of intercalated composites. This gives particularly good physicochemical and mechanical properties. The best method to reassure the reader of the structure the Authors have obtained is TEM research. The study should be supplemented with these studies.
The experimental part should also be supplemented with a description of the OMMT used and the parameters for the production of composites (only the temperature is given).
Author Response
We are very grateful to the reviewers for their suggestions for amendments to this manuscript, and we have made the following additional comments in accordance with the suggestions.
First, we supplemented Item 3.2, the morphology of the PLA nanocomposites, mainly by using TEM to examine the morphological changes of the composite material after blending PLA and OMMT.
3.2 The morphology of the PLA/OMMT nanocomposites
After mixing by torque rheometer, the PLA/OMMT nanocomposites can be examined by TEM to understand the change in the morphology of the composite material. The original OMMT of about 1 mm in diameter was mostly exfoliated silicate structure(100~200nm) by the intercalation effect of PLA polymer chains, and the obvious black filaments or strips can be observed in the TEM image of Figure 2, whether it is added with 3%wt OMMT-(A), 5%wt OMMT-(B), or 8%wt OMMT-(C), it can be dispersed evenly. As the ratio of OMMT increases, the content of layered silicate also increases proportionally. As shown in Figure 3, the TEM image shows the morphology of the PLA/OMMT nanocomposites obtained by co-rotating twin screw extruder, and the exfoliated silicate of the clay is evenly dispersed in the PLA to become a homogeneous composite materials, which is helpful for the improvement of physicochemical and mechanical properties.
Secondly, we have revised the second/third part of the experimental project as follows: (The main reason is that the reviewer suggested that the parameters and conditions of machine operation should be added.)
Preparation of hot pressed film specimen
40 g of PLA was blended with various amount of OMMT (0, 0.5, 3, 5, 8 wt%) by torque rheometer (Brabender, Model PL 2000), and then cut into pellets. Pour the sample into the feed tank first according to the formula ratio in Table 1, and the mixing temperature(200°C) was set for hot melting with a fixed speed of 50 rpm/min. After 2 minutes, the OMMT was poured into the feed tank for mixing, and the mixing sample was taken out after 6 minutes of mixing. After that, the nanocomposite was pressed (200°C) to form the 0.5-mm thick specimen by Compression Molding Machine (HAS-100 TON). The operation procedure of the hot press is as follows: raise the lower heating plate to a distance of about 1 cm from the upper heating plate, and preheat the material for 2 minutes. Next, raise the lower heating plate pressure to 650-675 psi and hold for 30 seconds, then raise the lower heating plate pressure to 1400-1450 psi and hold for 10 seconds. Relieve the pressure of the lower heating plate to an appropriate distance to take the object, remove the covered Teflon cloth, and take out the film-like specimen. Finally, this specimen was sealed by aluminum foil and left in dry cabinet.
Table 1 PLA/OMMT blending formula in torque rheometer
Sample label (Clay ratio) |
A (0.0%) |
B (0.5%) |
C (3.0%) |
D (5.0%) |
E (8%) |
PLA amount (g) |
40 |
40 |
40 |
40 |
40 |
OMMT amount (g) |
0 |
0.2 |
1.2 |
2 |
3.2 |
Preparation of injection molding specimen
4000 gram of PLA was blended with various amount of OMMT (0, 0.5, 3, 5, 8 wt%) by co-rotating twin screw extruder pelletizing system(SHJ-36), and the parameters and conditions of the machine operation are shown in Table 2.
Table 2 Co-rotating twin screw extruder parameter setting
Sample label |
A |
B |
C |
D |
E |
PLA amount (g) |
4000 |
4000 |
4000 |
4000 |
4000 |
OMMT amount (g) |
0 |
20 |
120 |
200 |
320 |
Clay ratio (%) |
0.0% |
0.5% |
3.0% |
5.0% |
8.0% |
Zone 1 temperature (℃) |
160 |
160 |
160 |
160 |
160 |
Zone 2 temperature (℃) |
163 |
162 |
160 |
155 |
150 |
Zone 3 temperature (℃) |
183 |
182 |
180 |
175 |
170 |
Zone 4 temperature (℃) |
188 |
187 |
185 |
180 |
178 |
Zone 5 temperature (℃) |
192 |
192 |
190 |
185 |
183 |
Zone 6 temperature (℃) |
184 |
182 |
180 |
175 |
173 |
Zone 7 temperature (℃) |
177 |
177 |
175 |
170 |
168 |
Feed chamber (℃) |
173 |
172 |
170 |
165 |
163 |
Melt pressure (MPa) |
11.36 |
11.36 |
11.36 |
11.36 |
11.36 |
Feeder speed (rpm) |
51~54 |
51~54 |
51~54 |
51~53 |
50~49 |
Pelletizing machine speed (rpm) |
150~160 |
150~160 |
150~160 |
150~160 |
150~160 |
Transmission electron microscopy (TEM)
The samples for TEM analysis were prepared by placing the films of PLA/OMMT nanocomposites into epoxy resin capsules and by curing these capsules at 70℃ for 24 h in a vacuum oven. Then, the cured epoxy resin that contained the PLA/OMMT nanocomposites was microtomed with a Reichert-Jung Ultracut-E to form 60~90 nm-thick slices (Optische Werke AG Wien, Austria). Subsequently, one layer of carbon around 10 nm-thick was deposited onto the slices, which placed on 100-mesh copper nets for TEM observation using a JEOL 2010 instrument (Tokyo, Japan) that was operated at an accelerating voltage of 200 kV.
Because of the addition of Tables 1 and 2, and Figures 4 and 5, some figures and tables will have some changes to their original numbers. The attached file is the complete revised manuscript with TEM test results (Figure 4 and 5)
Author Response File: Author Response.doc
Reviewer 2 Report
The paper entitled as “A Characteristic Study of polylactic acid / Organic modified montmorillonite (PLA/OMMT) Nanocomposite Materials after Hydrolyzing” investigates different nanocomposite materials following hydrolysis. The paper is well written, however, there are some major issues that should be addressed before consideration of publications. The introduction/literature review does not provide an appropriate background to the reader. It fails to provide state-of-the art references (from the past 2 or 5 years). Moreover, the novelty of the paper is unclear. The originality and the objectives of the research should be highlighted in the last paragraph in the Introduction section.
My additional comments are the following:
- The OMMT abbreviation is inappropriate in the abstract. (missing “organic” word in the first place the abbr. used)
- Provide the title of y axis in Figure 4.
- Correct the typing error in title of Section 4.4.1
- Correct the typing error in Table 3: Hydrol-ysis --> Hydrolysis
- Line 155: delete of
- Line 166-167: A reference is used from 2003. Thus, the presented results cannot be considered as novel, state of the art findings. References from the past 2-5 years should be used.
Author Response
We would like to thank the reviewers for their suggestions. Most importantly, the references must be strengthened to provide readers with appropriate background information, preferably citing articles from the past 2 or 5 years. Therefore, we have added more than 20 recently published journal reports(blue mark), and we have also removed the earlier literature, which is listed below. In addition, in view of the unclear novelty of the paper, we also revised and strengthened the last paragraph(red mark) of the introduction to highlight the originality and objectives of this study.
- Introduction
Recently, biodegradable polymers have been intensively studied due to the depletion of fossil energy and its impacts on environment [1-3]. Biodegradable polymers, defined by American Society for Testing and Material (ASTM) as being degradable by reacting with microbes, such as germ and fungus, can re-nourish soils during composting. In other words, these polymers possess sustainability and eco-efficiency. Polylactic acid (PLA), one of the polymers, represents the best environmental friendly product. It has hydrolysable ester functional group, enabling its waste to be naturally decomposed to H2O and CO2 during composting [4]. Therefore, PLA is so far the most economical and competitive biodegradable polymers [5-10].
PLA is a long-chained thermoplastic polyester, including α, β and γ structures [11-12], as shown in Figure 1. However, compared with traditional polymers, the applications of pure PLA are limited due to its rigid and less flexible characteristics [13-17]. In industry, the procedures of manufacturing PLA is (1)hydrolysis of corn and wheat, (2)transfer of starch to glucose or maltose, (3) biological fermentation to obtain lactic acid monomer, (4)condensation or ring opening polymerization [18-19].
Organic modified montmorillonite (OMMT) has large interlayer distance and lipophilicity. The properties not only decrease the surface energy of silicate, but also increase the affinity between OMMT layers and polymer molecular chains, and result in the uniform distribution of OMMT in polymer substrate to form polymer/layered silicate (PLS) nanocomposites [20-22]. In practical application, even the weight percentage of OMMT in PLS is less than 10 wt% (usually 3~5%), the product’s stiffness, strength, heat resistance and mechanical property can compete with conventional glass fibers or other mineral filling enhanced composites (filler content ≧30%) [23-25].Furthermore, OMMT has outstanding brightness and transparency, because its nano-particle is smaller than the wave length of visible light [26-27].
The manufacture of PLS nanocomposites is called intercalation compounding, including intercalative polymerization and polymer intercalation [28]. Intercalative polymerization can be categorized as monomer addition polymerization and monomer condensation, while polymer intercalation can be classified into polymer solution intercalation and polymer melting intercalation. The purpose of manufacturing PLS is to accomplish intercalation dispersion, which keeps the ordered structure of layered silicate, or exfoliation dispersion. Because that the disordered structure would cause the structure discrepancy and various property [29].
So far several researches have focused on the manufacture and properties investigation of PLA nanocomposites [30-32]. Bandyopadhyay et al. found that layered silicate, prepared by polymer melting intercalation, could be used as the barrier for blocking the gas, rise the decomposition temperature(Tmax) of PLA/organic modified fluorine clay nanocomposites [33]. Sinha et al. investigated on the heat deformation test (HDT) of PLA/organic modified synthesized fluorine mica nanocomposites, and indicated that heat deformation was substantially improved by little change of Tm [34]. Paul et al. studied on the heat stability of PLA nanocomposites and found that the heat stability increased primarily but then decreased as the content of OMMT increasing [35-36]. The bio-degradation of PLA is usually complex. At first the unstable bonds on main chain are hydrolyzed to develop oligomers. Then oligomer is further decomposed to H2O and CO2 when an appropriate enzyme exists. The above chain reaction of the hydrolysis of polymer makes a huge impact on bio-degradation [4, 9].
It is a major challenge in the chemical process to produce biodegradable nanocomposites with good quality and homogeneous blending quickly and in large quantities. Therefore, in this study, PLA/OMMT nanocomposites were prepared by a torque rheometer and a co-rotating twin screw extruder method instead of the conventional solution blending method, in which a co-rotating twin screw extruder pelletizing system was used for mechanical blending and molding by an injection mold to produce PLA/OMMT nanocomposites and specimens quickly and in large quantities. The nanocomposites are subsequently subjected to thermogravimetric analysis to measure their thermal stability. PLA/OMMT nanocomposites is immersed in phosphate solution at 37°C to monitor the thermal properties before/after hydrolysis by DSC, and finally, the hydrolyzed PLA/OMMT nanocomposites was subjected to tensile strength test to determine the material strength.
- Reference
- Nurul, M.F.; Jayaraman, K.; Bhattacharyya, D.; Mohamad, M.H.; Saurabh, C.K.; Hussin, M.H.; HPS, A.K. Green composites made of bamboo fabric and poly (lactic) acid for packaging applications—A review. Materials2016, 9(6), 435.
- Youssef, A. M.; El-Sayed, S. M.Bionanocomposites materials for food packaging applications: Concepts and future outlook. Polym. 2018, 193, 19– 27.
- Havstad, M.R. Chapter 5—Biodegradable Plastics. In Plastic Waste and Recycling; Letcher, T.M., Ed.; Academic Press: Cambridge, MA, USA, 2020, 97–129.
- Weng,X.; Jin, Y.J.; Meng, Q.Y.; Wang, L.; Zhang, M.; Wang, Y.Z.Biodegradation behavior of poly (butylene adipate-co-terephthalate)(PBAT), poly (lactic acid)(PLA), and their blend under soil conditions. Polym. Test. 2013, 32, 918– 926.
- Ncube, L.K.; Ude, A.U.; Ogunmuyiwa, E.N.; Zulkifli, R.; Beas, I.N. Environmental Impact of Food Packaging Materials: A Review of Contemporary Development from Conventional Plastics to Polylactic Acid Based Materials.Materials 2020, 13 (21), 4994.
- Farah, S.; Anderson, D.G.; Langer, R. Physical and mechanical properties of PLA, and their functions in widespread applications—A comprehensive review. Drug Deliv. Rev.2016, 107, 367–392.
- Dahman, Y. Poly (Lactic Acid): Green and Sustainable Plastics. Technol.2014, 2, e121.
- Darie-Niţă, R.N.; Vasile, C.; Irimia, A.; Lipşa, R.; Râpă, M. Evaluation of some eco-friendly plasticizers for PLA films processing. Appl. Polym. Sci.2016, 133(13), 43223.
- Siakeng, R.; Jawaid, M.; Ariffin, H.; Sapuan, S.; Asim, M.; Saba, N. Natural fiber reinforced polylactic acid composites: A review. Compos.2018, 40, 446–463.
- Righetti, M.C.; Cinelli, P.; Mallegni, N.; Massa, C.A.; Aliotta, L.; Lazzeri, A. Thermal, Mechanical, Viscoelastic and Morphological Properties of Poly (lactic acid) based Biocomposites with Potato Pulp Powder Treated with Waxes. Materials 2019, 12, 990.
- Alemán, C.; Lotz, ; Puiggali, J. Crystal Structure of the α-Form of Poly(L-lactide) , Macromolecules 2001, 34, 4795–4801.
- Saeidlou, ; Huneault, M. A.;Li, H.;Park, C. B. Poly(lactic acid) crystallization. Prog. Polym. Sci. 2012, 37, 1657–1677.
- Betancourt, N.G.; Cree, D.E. Mechanical properties of poly (lactic acid) composites reinforced with CaCO3 eggshell based fillers. MRS Adv.2017, 2, 2545–2550.
- Aliotta, L.; Gigante, V.; Coltelli, M.B.; Cinelli, P.; Lazzeri, A. Evaluation of mechanical and interfacial properties of bio-composites based on poly (lactic acid) with natural cellulose fibers. J. Mol. Sci.2019, 20, 960.
- McCutcheon, J.;Zhao,B.; Jin,K.; Bates, F. S. ; Ellison , C. J.. Crazing Mechanism and Physical Aging of Poly(lactide) Toughened with Poly(ethylene oxide)-block-poly(butylene oxide) Diblock Copolymers. Macromolecules 2020, 53(22), 10163–10178.
- Nagarajan,; Mohanty ,A. K.;Misra, M. Perspective on Polylactic Acid (PLA) based Sustainable Materials for Durable Applications: Focus on Toughness and Heat Resistance. ACS Sustain. Chem. Eng. 2016, 4(6), 2899-2916.
- Odent, J.; Raquez, J.; Dubois, P.Highly Toughened Polylactide-Based Materials through Melt-Blending Techniques. In Biodegradable Polyesters; Fakirov, S., Ed.; Wiley-VCH Verlag GmbH & Co. KGaA: Berlin, 2015.
- Nyambo, C.; Mohanty, A.K.; Misra, M. Polylactide-based renewable green composites from agricultural residues and their hybrids Biomacromolecules 2010, 11, 1645–
- Van den Berg, S. A.;Zuilhof, H.;Wennekes, T. Clickable Polylactic Acids by Fast Organocatalytic Ring-OpeningPolymerization in Continuous Flow. Macromolecules 2016, 49, 2054–2062 .
- Hwang, J.;Liu, H. J. Influence of Organophilic Clay on the Morphology, Plasticizer-Maintaining Ability, Dimensional Stability, and Electrochemical Properties of Gel Polyacrylonitrile (PAN) Nanocomposite Electrolytes. Macromolecules 2002 , 35, 7314–7319.
- Cui, Y.; Kumar, S.; Rao Kona, B.; van Houcke, D.Gas barrier properties of polymer/clay nanocomposites. RSC Adv. 2015, 5, 63669– 63690.
- Francis,V.;Jain, K. Experimental investigations on fused deposition modelling of polymer-layered silicate nanocomposite. VirtualPhys. Prototyp. 2016, 11, 109-121.
- Goh,; Heising,J. K.; Yuan, Y.; Karahan, H. E.; Wei, L.;Zhai,S.; Koh,J. X.;Htin, N. M.; Zhang,F.; Wang, R.; Fane, A. G.; Dekker, M.; Dehghani,F.; Chen , Y.* Sandwich-Architectured Poly(lactic acid)–Graphene Composite Food Packaging Films. ACS Appl. Mater. Interfaces 2016, 8(15), 9994–10004.
- Hamed, N.S.; Razavi, R.S.; Mohammad Reza L. E.; Ramazani, M. The effect of organoclay on the morphology and mechanical properties of PAI/clay nanocomposites coatings prepared by the ultrasonication assisted process. Sonochem. 2017, 38, 306–316.
- Sato, ; Yamauchi, J.; Takahashi, Y.; Kanehashi, S.; Nagai, K.* Effects of Nanofiller-Induced Crystallization on Gas Barrier Properties in Poly(lactic acid)/Montmorillonite Composite Films. Ind. Eng. Chem. Res. 2020, 59(27), 12590–12599.
- Pluta, M. Morphology and properties of polylactide modified by thermal treatment, filling with layered silicates and plasticization, Polymer 2004, 45, 8239–8251.
- Basu, A.; Nazarkovsky, M.; Ghadi, R.; Khan, W.; Domb, J.* Poly(lactic acid)-based nanocomposites. Polym. Adv. Technol. 2016, 28(8).
- Chafidz, A.; Tamzysi, C.; Kistriyani, L.; Kusumaningtyas, R. D.; Hartanto, D. Mechanical Properties of PP/clay Nanocomposites Prepared from Masterbatch: Effect of Nanoclay Loadings and Re-Processing. Key Mater. 2019, 805, 59–64.
- Nagy, D.; Kókai, Polymer-based nanocomposites with nanoclay. IOP Conf. Ser.: Mater. Sci. Eng. 2018, 448, 012021.
- Cao, Y.; Xu, P.; Lv, P.; Lemstra, P. J.; Cai, X.; Yang, W.; Dong, W.; Chen, M.; Liu, T.; Du, M.; Ma, P. Excellent UV Resistance of Polylactide by Interfacial Stereocomplexation with Double-Shell-Structured TiO2 ACS Appl. Mater. Interfaces2020, 12(43), 49090–49100.
- de Azevedo Gonçalves Mota, R.C.; de Menezes, L.R.; da Silva, E.O. Poly(lactic acid) polymers containing silver and titanium dioxide nanoparticles to be used as scaffolds for bioengineering. Mater. Res. 2021.
- Liu, C.; Shen, J.; Yeung, K. W. K.; Tjong, S. C. Development and Antibacterial Performance of Novel Polylactic Acid-Graphene Oxide-Silver Nanoparticle Hybrid Nanocomposite Mats Prepared By Electrospinning. ACS Biomater. Sci. Eng.2017, 3 (3), 471–486.
- Li,;Zhang, C.;Weng, Y. Improvement of the Gas Barrier Properties of PLA/OMMT Films by Regulating the Interlayer Spacing of OMMT and the Crystallinity of PLA. ACS Omega 2020, 5(30), 18675–18684.
- He,;Xu, W.H.; Zhang, H.; Qu, J.P. Constructing Bone-Mimicking High-Performance Structured Poly(lactic acid) by an Elongational Flow Field and Facile Annealing Process. ACS Appl. Mater. Interfaces 2020, 12(11), 13411–13420 .
- Araújo, ; Botelho, G.; Oliveira, M.; Machado, A.V. Influence of clay organic modifier on the thermal-stability of PLA based nanocomposites. Appl. Clay Sci. 2014, 88–89, 144–150.
- Alves, J. L.; Rosa, P. T. V.; Realinho, V.; Antunes, M.; Velasco, J. I.; Morales, A. R. The effect of Brazilian organic-modified montmorillonites on the thermal stability and fire performance of organoclay-filled PLA nanocomposites. Clay Sci. 2020,194, 105697:1–105697:8.
- Huang, M.; Hwang, J. J.; Liu, H. J.; Lin, L. H. Crystallization Behavior of Poly(L-lactic acid)/Montmorillonite Nanocomposites. J. Appl. Polym. Sci. 2010, 117, 434–442 .
The reviewer 2 additional comments have been revised or supplemented in accordance with their comments.
The OMMT abbreviation is inappropriate in the abstract. (missing “organic” word in the first place the abbr. used) (Corrected)
Provide the title of y axis in Figure 4. (Corrected)
Correct the typing error in title of Section 4.4.1 (Corrected)
Correct the typing error in Table 3: Hydrol-ysis --> Hydrolysis (Corrected)
Line 155: delete of (Corrected)
Line 166-167: A reference is used from 2003. Thus, the presented results cannot be considered as novel, state of the art findings. References from the past 2-5 years should be used. (Added references 35,36)
Author Response File: Author Response.doc
Round 2
Reviewer 1 Report
I recommend the publication in its current form
Reviewer 2 Report
I accept the modifications and recommend the presented work.