Flow Performance and Its Effect on Shape Formation in PDMS Assisted Thermal Reflow Process
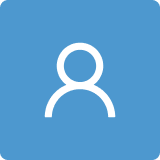
Round 1
Reviewer 1 Report
This study is related to the theoretical modeling on the PDMS assisted thermal reflow process which was proposed by the authors before. Please refer the followings:
- What is the main contribution or impact of this manuscript, compared to the authors' previous papers [10-12]? What is the better or improved result in the microlens lens fabrication using this theoretical model discussed in this manuscript? The readers expect that the careful control or optimization of processing parameters based on the improved theoretical model can result in more improved structural realization in microlens arrays. Please include some improved structural data on the fabricated microlens array after applying this theoretical model.
- In Fig. 6, there is a shape difference in the final simulated and experimental profiles. Please include more discussion why this difference was still occurred even with the improved theoretical model.
Author Response
Please see the attachment.
Author Response File: Author Response.pdf
Reviewer 2 Report
The manuscript submitted presents the development of a theoretical model for the reflow process of PDMS on complex surfaces and the subsequent shape transfer to the cure PDMS.
My observations on the manuscript are as follows:
- In the introduction/Background section discuss what would be specific applications of the ability to transfer complex patterns to a cured PDMS substrate.
- Disambiguate what DMD stands for.
- Section 2.1 – what temperature does the initial pour of PDMS solution takes place at?
- Section 2.2 – what is a “viscosity liquid”?
- In equation (4) specify what the “sigmarp” coefficient is.
- What are the values of the “sigmarp” and the “contact angle” and how are they determined?
- In Figure 2 the measured and predicted viscosities curves at different temperatures show quite large discrepancies. Explain these discrepancies and discuss how they affect the overall results of the theoretical model.
- Are the results in Figure 3 measured or simulated?
- What is the connection between the work presented in Section 3.1 (grating array) and the work presented in Section 3.2 (microlens array)?
- In the work from Section 3.3, where does the original asymmetry in the microlens arises from? For both section 3.2 and 3.3 are the initial photoresist patterns fabricated using DMD maskless lithography?
- In the Conclusions, when specifying the use of the model for optimization, specify what are the specific parameters that can be optimized using the model. Is it the reflow temperature, the reflow time, or the initial structure of the photoresist pattern? How do you specifically see your model implemented within the process design of an arbitrary microstructure? Does the model work for arbitrary designs or does it assume only periodic structures with periodic boundary conditions?
Author Response
Please see the attachment.
Author Response File: Author Response.pdf
Round 2
Reviewer 2 Report
Authors have addressed the review comments satisfactory.