From Structural Optimization Results to Parametric CAD Modeling—Automated, Skeletonization-Based Truss Recognition
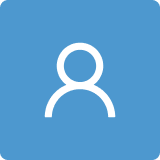
Round 1
Reviewer 1 Report
Modern point of view, even if are used properties for classical obtained materials (not from powders!
All calculated values are presented in different multiples of Pa. In my opinion should be used or Pa or MPa (only one multiple).
Anyway the values for Modulus of Elasticity and Poisson's Ratio are not the correct ones (according to MatWeb). The most erroneous values are for Modulus of Elasticity: they are in GPa not in MPa. So, all computations are questionable ! See rows 269-270, and 301.
Author Response
Dear Reviewer,
Thank you for the valuable comments. I have revised the manuscript strictly according to the recommendation. Your comments were carefully analyzed and detailed responses were addressed along with manuscript corrections. I believe that thanks to the suggested corrections the manuscript is now improved and worth publishing.
It seems in the first case study notes attached to our research data contained error, Young’s Modulus and Poisson Ratio used were indeed for the “generic” steel not for A36, as paper claims. This doesn’t change, in essence, the results of this paper as the analyzed bar bending problem is just a benchmark for structural optimization software. Ready results were used as input for the test of the developed algorithm.
Young’s Modulus unit was also invalid, the real data used was (value below was taken directly from the structural optimizer input file, the same values were used for testing result parametric model):
"Material": {
"Density": “7800”,
"E": ”200000000000”,
"Nu": “0.28”
},
Similarly for the second case study the input was correct and an invalid unit the the paper. Input used for optimization and analysis was:
"Material": {
"Nu": "0.33",
"E": "70e9",
"Density": "2800"
},
All units in the paper were converted into basic units - Pa. All units in MPa were converted into Pa, similarly Young’s modulus is given in Pa. Moreover, as a part of the unit unification, missing units were added to legends in all pictures using Von Mises stress for a color map.
I would like again to thank the Reviewer for a thorough review.
Best Regards
Jan Polak
Reviewer 2 Report
Well done to the authors for the in-depth and thorough analysis. Please consider these comments for improvement of the paper:
· There are many types of additive manufacturing. Any specific methods or techniques?
· Please explain further how the optimisation method introduced in this paper could benefit the additive manufacturing users
· Please briefly explain the concept of biomimetric approach. Some readers may not be familiar with the term.
· Please specify which CAD software is being used for Section 2.1 – Section 2.4
· What is the importance of Listing 1? Please consider to remove.
· For Section 3.1, it is quite unclear what the authors trying to achieve. Did the authors took designs from literature and apply using the method developed in this project?
· Please rewrite dimensions specified in the paper - 20x20x1000mm should be 20 mm x 20 mm x 1000 mm
· Some spelling errors can be spotted – please carry out a thorough proof read before submission
· For Figure 23, please provide caption for each figure a) – i)
· As the paper is only based on truss – please provide comments in the conclusion/discussion, possibility of applying the same approach for other type of structures – since additive manufacturing dealing with complex geometries hence it is important to address this point.
Minor spelling errors can be spotted
Author Response
Dear Reviewer,
Thank you for the valuable comments. I have revised the manuscript strictly according to the recommendation. Your comments were carefully analyzed and detailed responses were addressed along with manuscript corrections. I believe that thanks to the suggested corrections the manuscript is now improved and worth publishing.
- There are many types of additive manufacturing. Any specific methods or techniques?
- Please explain further how the optimisation method introduced in this paper could benefit the additive manufacturing users
Both points were addressed by extending the BioniAMoto project description. Now it reads:
The efficiency of the algorithm is demonstrated in the second case study - the industrial use of biomimetic optimization in the BioniAMoto project. The aim of the BioniAMoto project is to develop a cost-effective method for manufacturing lightweight and efficient structural nodes for the automotive industry using additive manufacturing (AM) technologies and structural optimization. The project aims to create a new concept for manufacturing 3D structural nodes for vehicle frames using topology-optimized aluminum alloys that are joined together with readily available and commonly used extruded profiles. One of the parts manufactured as a part of the project is an aluminum box corner used in truck cars. The use of the presented approach enables conversion of results of the structural optimization to the parametric model, which simplifies post processing steps required to prepare the model for the manufacturing process. Two additive manufacturing processes are considered. The direct method, Laser Metal Powder Bed Fusion (LM-PBF) technology, uses a laser beam to fuse metal powder. Second approach is the indirect method using Laser Polymer Powder Bed Fusion (LP-PBF) technology to create the initial model which is used, in turn, to create mold used for the manufacturing using Injection Molding. Both approaches have limitations which require model processing before manufacturing. One example is the minimal element thickness imposed by both approaches. In the direct method the limiting factor is the thermal stress, in indirect -- the molten metal flow properties during the casting process. Use of parametric models in the CAD software allows adjustments of the optimized model to consider those phenomenons.
Moreover we hinted benefits yet to be researched in discussion section:
Presented approach is a fully automated parametrization procedure. On the other hand, when the manufacturing preparation requires increasing minimal thickness, for example to decrease thermal stresses during the manufacturing process, a parametric model produced by the algorithm can be used to manually apply corrections. Those corrections are then fused back with the original mesh, preserving features that were not captured by the parametric model while improving properties of the optimized mesh. Additional research is required to evaluate this approach for industrial use.
- Please briefly explain the concept of biomimetric approach. Some readers may not be familiar with the term.
Rewritten paragraph to: The goal of the used structural optimization algorithm is to equalize the surface strain energy density distribution. Topology with uniform distribution under a load has both maximal stiffness and minimal mass~\cite{nowak2021topology}. In nature this phenomenon is observed in trabecular bones. Bone tissue is constantly remodeled as it reacts to the external stress by growing in areas with high stress concentration and removing where it is not required \cite{muller2014change}. This bio-mechanic process is simulated in the structural optimization process to equalize surface strain energy density in the optimized model.
- Please specify which CAD software is being used for Section 2.1 – Section 2.4
Rewritten part of paragraph to: Input of the algorithm is both input data and the result mesh of the structural optimization system. Sample input for the algorithm, created using FreeCAD software, is provided on Figure~\ref{fig-problem-definition}.
- What is the importance of Listing 1? Please consider to remove.
Indeed it’s not important enough, it wasn’t even referenced, so, as suggested, it has been removed.
- For Section 3.1, it is quite unclear what the authors trying to achieve. Did the authors took designs from literature and apply using the method developed in this project?
We’ve changed the first sentence to better reflect the intention: “Process results were tested using two structural optimization solutions for which analysis has been done in the past. “, provided references to work with analysis of those examples and provided two papers with analysis of visually similar models.
- Please rewrite dimensions specified in the paper - 20x20x1000mm should be 20 mm x 20 mm x 1000 mm
Rewritten as suggested across all document.
- Some spelling errors can be spotted – please carry out a thorough proof read before submission
We apologize for the inconvenience, the article went through another round of proofreading and numerous mistakes were corrected.
- For Figure 23, please provide caption for each figure a) – i)
Captions provided for figures 21 and 23.
- As the paper is only based on truss – please provide comments in the conclusion/discussion, possibility of applying the same approach for other type of structures – since additive manufacturing dealing with complex geometries hence it is important to address this point.
Extended the first item in “areas of improvement” section to clearly convey our intended message:
\item Truss-based geometry was chosen because compared to more complex geometries it has less degrees of freedom to optimize so the heuristic refinement process converges fast. Chosen structural elements are insufficient for structures with bending moments under load and there is a need for support of more complex geometries to properly capture complexity of input meshes. The proposed heuristic refinement step and the fitness function in particular work with solutions built out of any parameterized geometries. This makes it possible to apply the algorithm to any geometries produced by structural optimization algorithms, without the current limitation to trusses.
I would like again to thank the Reviewer for a thorough review.
Best regards
Jan Polak
Round 2
Reviewer 1 Report
OK