Laser Material Processing and Thermal Joining Process
A special issue of Applied Sciences (ISSN 2076-3417). This special issue belongs to the section "Optics and Lasers".
Deadline for manuscript submissions: closed (20 May 2024) | Viewed by 6319
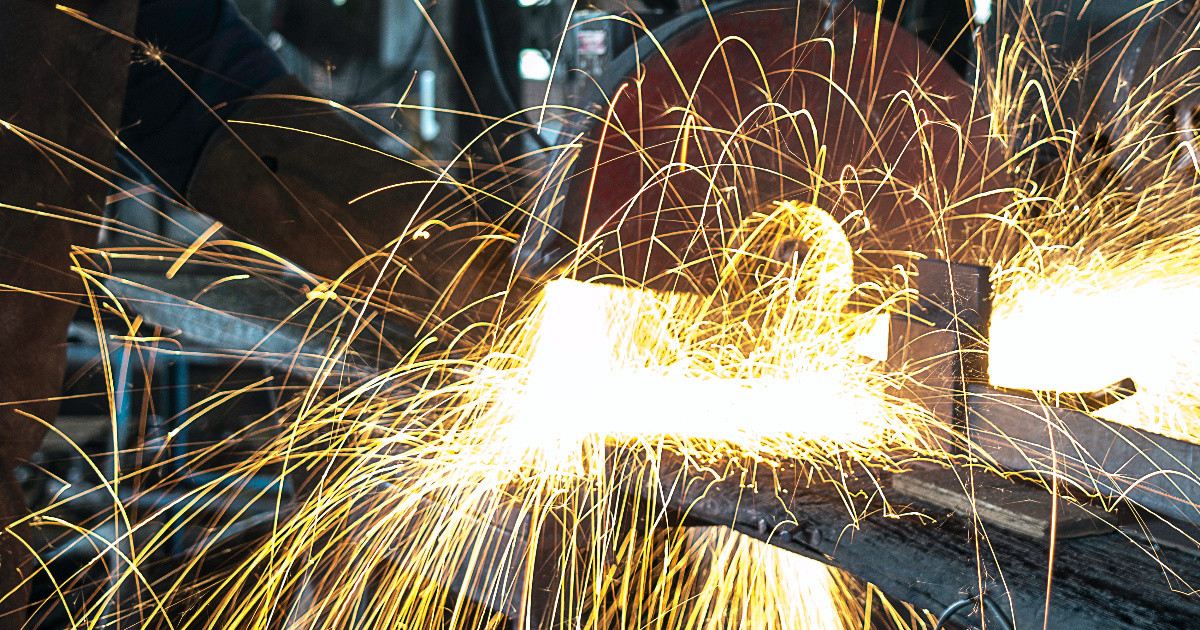
Special Issue Editor
Interests: joining technology; laser welding; laser-assited metal-polymer joining; process technology; material science; systems engineering; modelling; simulation
Special Issue Information
Dear Colleagues,
This special issue addresses original scientific articles and detailed reviews related to important and novel developments in the field of laser material processing and thermal joining processes.Both fields are of great importance, and innovative approaches in process design and systems engineering are increasing the range of applications for cutting-edge industries, for example in electromobility and other branches. This special issue focusses specifically on contributions dealing with novelties in process design, material science and systems engineering and their interaction in the context of laser material processing and thermal joining processes
Dr. Klaus Schricker
Guest Editor
Manuscript Submission Information
Manuscripts should be submitted online at www.mdpi.com by registering and logging in to this website. Once you are registered, click here to go to the submission form. Manuscripts can be submitted until the deadline. All submissions that pass pre-check are peer-reviewed. Accepted papers will be published continuously in the journal (as soon as accepted) and will be listed together on the special issue website. Research articles, review articles as well as short communications are invited. For planned papers, a title and short abstract (about 100 words) can be sent to the Editorial Office for announcement on this website.
Submitted manuscripts should not have been published previously, nor be under consideration for publication elsewhere (except conference proceedings papers). All manuscripts are thoroughly refereed through a single-blind peer-review process. A guide for authors and other relevant information for submission of manuscripts is available on the Instructions for Authors page. Applied Sciences is an international peer-reviewed open access semimonthly journal published by MDPI.
Please visit the Instructions for Authors page before submitting a manuscript. The Article Processing Charge (APC) for publication in this open access journal is 2400 CHF (Swiss Francs). Submitted papers should be well formatted and use good English. Authors may use MDPI's English editing service prior to publication or during author revisions.
Keywords
- laser material processing, e.g. laser welding (cw and pw), surface structuring
- thermal joining processes, e.g. friction stir welding, ultrasonic welding
- innovative process design and technology, e.g. adjustable intensity distributions in laser material processing, tool design in friction stir welding
- dynamic behavior of processes and tools, e.g. keyhole stability and tool wear
- systems engineering including fixture design, process monitoring and control
- joining of similar and dissimilar materials, e.g. steel-steel, aluminum-copper, aluminum-steel, metal-plastic
- optimization, modelling and simulation
- seam defects, formation mechanismns and avoidance
- structural performance
Benefits of Publishing in a Special Issue
- Ease of navigation: Grouping papers by topic helps scholars navigate broad scope journals more efficiently.
- Greater discoverability: Special Issues support the reach and impact of scientific research. Articles in Special Issues are more discoverable and cited more frequently.
- Expansion of research network: Special Issues facilitate connections among authors, fostering scientific collaborations.
- External promotion: Articles in Special Issues are often promoted through the journal's social media, increasing their visibility.
- Reprint: MDPI Books provides the opportunity to republish successful Special Issues in book format, both online and in print.
Further information on MDPI's Special Issue policies can be found here.