Application and Analysis in Fluid Power Systems II
A special issue of Energies (ISSN 1996-1073). This special issue belongs to the section "D: Energy Storage and Application".
Deadline for manuscript submissions: closed (31 January 2024) | Viewed by 7661
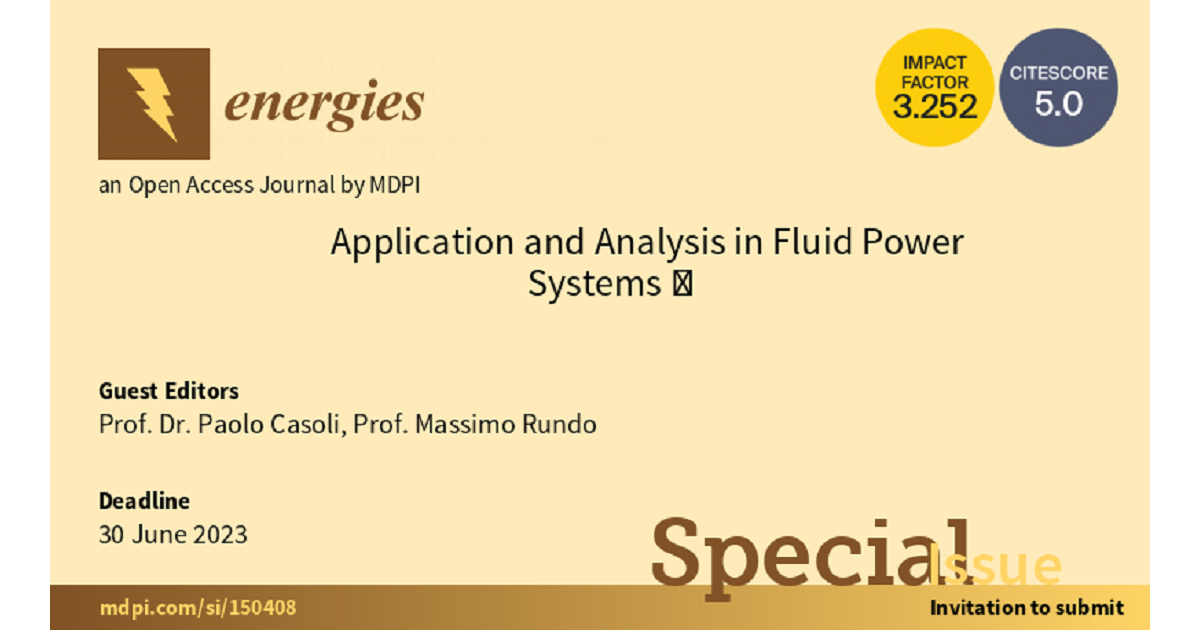
Special Issue Editors
Interests: hybrid hydraulic; industrial and mobile fluid power systems applications; condition monitoring in hydraulic systems
Special Issues, Collections and Topics in MDPI journals
Interests: fluid power; internal gear pump; crescent pump; gerotor pump; vane pump
Special Issues, Collections and Topics in MDPI journals
Special Issue Information
Dear Colleagues,
This special issue is a continuation of the previous and successful series of Special Issues with the topic of “Fluid Power Systems”. It aims to collect studies on the recent advances of fluid power technology in a wide range of topics, including the following:
- New methodologies for the analysis, modeling, simulation, and design of hydraulic and pneumatic components;
- Advanced configurations and design for hydrostatic machines and valves;
- New experimental approaches and techniques in hydraulic and pneumatic components;
- Advanced system configuration in mobile and industrial fluid power;
- Applications of fluid power in the field of hydrostatic, hybrid, and power split transmissions;
- Safety, prognostic, monitoring and fault detection in fluid power components;
- Hydraulic drives and actuators in powered prosthetics;
- Reduction in noise and vibration in hydraulic components and systems;
- Environmental topics and issues in fluid power;
- New system architectures based on EHA to reduce fuel consumption and increase productivity of fluid power machines;
- EHA: simulation, implementation, and component integration;
- Digital fluid power;
- Aerospace, off-road machinery and stationary applications;
- Control design methodologies and techniques for fluid power systems;
- New system configurations to reduce fuel consumption and increase productivity of fluid power machines;
- Applications of fluid power in the field of renewable energy;
- Fluid power in mobile and industrial robots;
- Smart fluids and materials for fluid power systems.
On behalf of Energies, I invite you to consider this Special Issue as an opportunity to publish your research results in the field of fluid power. We are looking forward to receiving your submissions.
Prof. Dr. Paolo Casoli
Prof. Massimo Rundo
Guest Editors
Manuscript Submission Information
Manuscripts should be submitted online at www.mdpi.com by registering and logging in to this website. Once you are registered, click here to go to the submission form. Manuscripts can be submitted until the deadline. All submissions that pass pre-check are peer-reviewed. Accepted papers will be published continuously in the journal (as soon as accepted) and will be listed together on the special issue website. Research articles, review articles as well as short communications are invited. For planned papers, a title and short abstract (about 100 words) can be sent to the Editorial Office for announcement on this website.
Submitted manuscripts should not have been published previously, nor be under consideration for publication elsewhere (except conference proceedings papers). All manuscripts are thoroughly refereed through a single-blind peer-review process. A guide for authors and other relevant information for submission of manuscripts is available on the Instructions for Authors page. Energies is an international peer-reviewed open access semimonthly journal published by MDPI.
Please visit the Instructions for Authors page before submitting a manuscript. The Article Processing Charge (APC) for publication in this open access journal is 2600 CHF (Swiss Francs). Submitted papers should be well formatted and use good English. Authors may use MDPI's English editing service prior to publication or during author revisions.
Keywords
- fluid power
- hydrostatic pumps and motors
- hydraulic control valves
- digital hydraulics
- water hydraulics
- hydrostatic transmissions
- hybrid and power split transmissions
- hydraulic hybrids
- hydraulic and pneumatic robots
- noise and vibration keyword
- oscillation damping
- energy efficiency
- fuel consumption
- drives and actuators
- hydraulic eco-fluids
- pneumatics
Related Special Issue
- Application and Analysis in Fluid Power Systems in Energies (13 articles)