Fabrication, Characterization, and Development of Hot-Deformed Magnets
A special issue of Materials (ISSN 1996-1944). This special issue belongs to the section "Materials Physics".
Deadline for manuscript submissions: 20 October 2024 | Viewed by 4923
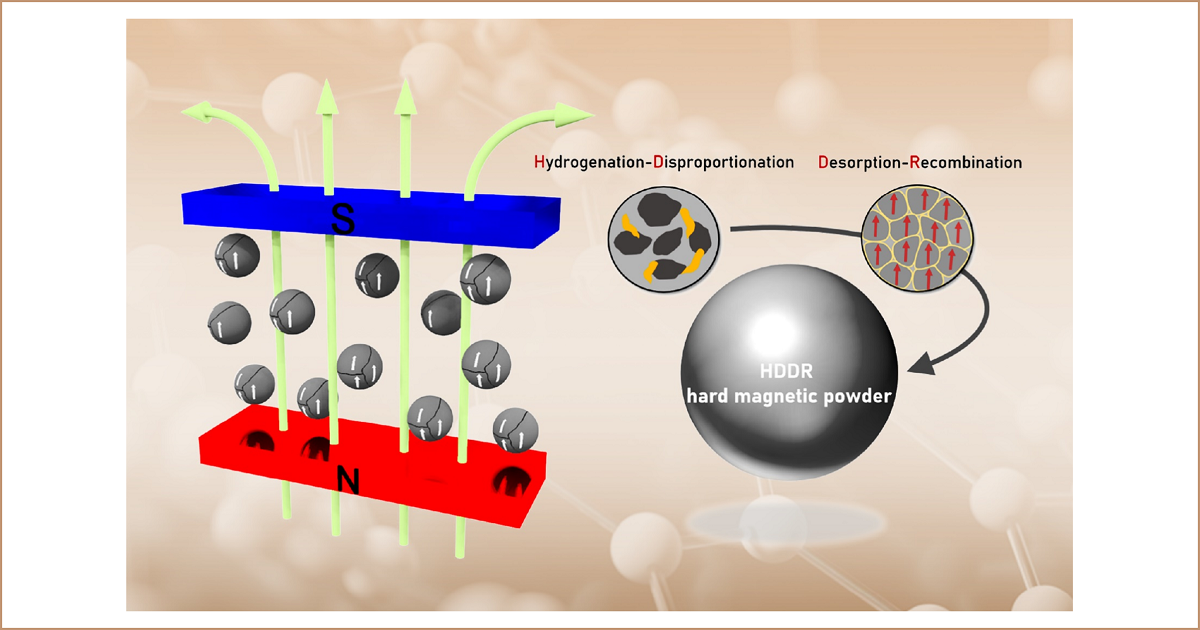
Special Issue Editors
Interests: magnetic materials; permanent magnets; rare-earth magnets; rare-earth free magnets; sintering; hot deformation; microstructure characterization
Special Issue Information
Dear Colleagues,
1) High-performance permanent magnets are a core material in the production of motors of next-generation mobility driven by environmentally friendly electric energy. In particular, among various magnet manufacturing processes, the hot-deformation process is a promising next-generation industrial process for the production of high-coercivity permanent magnets comprising nano-sized grains. Therefore, for sustainable R&D in the permanent magnet field, significant research results regarding the fabrication, characterization, and development of hot-deformed magnets should be accumulated and shared.
2) The aim of this Special Issue, entitled “Fabrication, Characterization, and Development of Hot-Deformed Magnets“, is to share the state-of-the-art development in high-performance hot-deformed permanent magnets. We cordially invite you to contribute to the permanent magnet field both academically and industrially by submitting your meaningful research results regarding hot-deformed magnets. We are sure that your contribution will be of great help to the growth and expansion of the worldwide permanent magnet field. Manuscripts in the form of full research papers, communications, and review articles are encouraged.
Dr. Tae-Hoon Kim
Dr. Xin Tang
Guest Editors
Manuscript Submission Information
Manuscripts should be submitted online at www.mdpi.com by registering and logging in to this website. Once you are registered, click here to go to the submission form. Manuscripts can be submitted until the deadline. All submissions that pass pre-check are peer-reviewed. Accepted papers will be published continuously in the journal (as soon as accepted) and will be listed together on the special issue website. Research articles, review articles as well as short communications are invited. For planned papers, a title and short abstract (about 100 words) can be sent to the Editorial Office for announcement on this website.
Submitted manuscripts should not have been published previously, nor be under consideration for publication elsewhere (except conference proceedings papers). All manuscripts are thoroughly refereed through a single-blind peer-review process. A guide for authors and other relevant information for submission of manuscripts is available on the Instructions for Authors page. Materials is an international peer-reviewed open access semimonthly journal published by MDPI.
Please visit the Instructions for Authors page before submitting a manuscript. The Article Processing Charge (APC) for publication in this open access journal is 2600 CHF (Swiss Francs). Submitted papers should be well formatted and use good English. Authors may use MDPI's English editing service prior to publication or during author revisions.
Keywords
- permanent magnets
- rare-earth based magnets
- rare-earth free magnets
- hot deformation
- microstructure
- magnetic properties