An Improved Zero-Flowrate Switching Control Method to Reduce Switching Losses in a Hydraulic Actuator
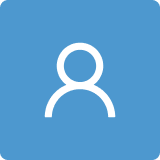
Round 1
Reviewer 1 Report
Comments and Suggestions for AuthorsComment 1: the paper presents an improved zero-flowrate switching control method to reduce switching losses in a hydraulic actuator. The author has presented a similar concept in previous publications: Peng, S. Modeling and Theoretical Analysis of Zero-Flowrate-Switching Control Method for a Dynamic Load System to Reduce Switching Power Loss of Control Valves. Actuators 2023, 12, 183. In previous work, the method can only be applied in occasions where the opening/closing times are less than 2 ms, which is limited in actual applications. In the improved method, this time has been improved to 20 ms, which matches more applications in industry fields. The author should describe more research work to show the advanced merits of this new method.
Comment 2: measuring flowrate is difficult in a fast-response controller. Even though the opening/closing time of the valve has been improved to 20 ms, which is still hard for a flowrate sampling system.
Comment 3: the author proposes ideal hydraulic impedance applied in the novel method, which means the feasibility of this new method depends on accuracy modeling of hydraulic impedance, like designing of capacity/inductor components with accurate capacitance/inductance value, resistance modelling of various components through the lines. How would this be realize in a real system?
Comment 54: as explained in Figure 14, a command is generated and sent to three different logic controllers, who will send command signals to three different hydraulic valves, respectively. The authors should explain more details in the figure: 1) how and by what is the command generated? 2) How is the logic controllers realized? 3)how do the sensors (for flowrates and pressures) communicate with the controller?
Comments on the Quality of English LanguageComment 5: some languge errors should corrected:
In section 3, paragraph 2“By inputing proper pressure difference at inlet of capacity, there will be a flowrate increase through the auxiliary control line,”
“inputing” should be “inputting”
In section 4, paragraph 1: “In this paper, commecial software AMESim is used to build models for hydraulic systems.”
“commecial” should be “commercial”
Author Response
Response 1: The relating research work has been described in the paper. In existing research work, very fast valves are applied in the application, but very fast valves are very expensive, and difficult to purchase. Another merit is better efficiency performance. With the method proposed in this paper, the switching loss is almost reduced by 99.9%.
Response 2: there are several method to decide when to switch valves. The first one, sample flowrate with flowmeter by KRACH VC0.2 F1 which is able to response 40L/min in 5.8ms, which is fast enough for the case in this paper. The second one, calculate switching times ahead. This is feasible when flowrate before switching is constant.
Response 3: there are equations to calculate impedance of hydraulic components with different structures. These equations can be corrected with simulation models and experiments.
Response 4: 1) The computer will generate the command and send it to a PLC logic controller; 2) the logic controller can be realized with a PLC controller; 3) The sensors will collect data from hydraulic system and send the data to a PLC controller. The PLC will calculate valve command with the data.
Respond 5: Already corrected.
Reviewer 2 Report
Comments and Suggestions for AuthorsThe paper is about an interesting topic, but I report relevant suggestions.
About section IV.A I suggest to reduce the description of the Amesim sub models from the help file, but only describes the models adopted for the simulations.
It is not clear if the frequency dependent friction are used or not to model the circuit or it is only a feature of Amesim.
Page 10. Check sentence: “…and friction of conduit walls of the conduits”
In figure 8 adds tick marks in y axix 0-500 l/min
Improve y-axis figure 10, the maximum value label is not reported.
The course of the flow rate in figure 10 depends on the capacity but also on the pipe diameter, being pipe 3 with a lower diameter respect to pipe 2, the author should point out this aspect.
Table 3. Report in the caption that it is referred to figure 11. Pipe 2 has a very little diameter 4 mm, could the authors comment this aspect. Results with a pipe 2 diameter equal to 25 mm should be reported.
A further table with the pipes geometry information about HS system, figure 12, should be added, for a better comparison between them.
Figure 19. y-axis requires the title and unit.
Figure 17. Why the flow rate through the line Q1 is equal zero but the displacement of the cylinder is not constant. It is not possible, or give an explanation. In HS system there is only the line Q1. As a matter of in figure 15 the cylinder displacement is constant when the flow rate Q1 is zero.
The authors should give more details about the computation of the switching power loss, presenting the pressure drop and flow rate in the section considered.
Author Response
Dear reviewer:
Thanks for the very precious comments which help me to improve my work. I have responsed them one by one. Please feel free to contact me if you have any more questions.
Best wishes!
Comments: About section IV.A I suggest to reduce the description of the Amesim sub models from the help file, but only describes the models adopted for the simulations.
Response: The description of AMESim submodels is presented to show simulation models match the methodology proposed in this paper. AMESim provide several different submodels with different impedance characteristics. I have state why I choose these submodels.
Comment: It is not clear if the frequency dependent friction are used or not to model the circuit or it is only a feature of Amesim.
Page 10. Check sentence: “…and friction of conduit walls of the conduits”
Response: of course the frequency dependent friction is used, it is the reason of resistance.
Comment: In figure 8 adds tick marks in y axix 0-500 l/min
Response:the space is very limited to add tick marks but I have stated that the peak value of flowrate is 464L/min and final flowrate is 373L/min.
Comment:Improve y-axis figure 10, the maximum value label is not reported.
Response:In figure 10, I have stated that the maximum flowrate is 281.3L/min.
Comment:The course of the flow rate in figure 10 depends on the capacity but also on the pipe diameter, being pipe 3 with a lower diameter respect to pipe 2, the author should point out this aspect.
Response:capacity is a character which relates to pipe volume which is equal to pi*d2/4. The diameter of the pipe is already in consideration.
Comment: Table 3. Report in the caption that it is referred to figure 11. Pipe 2 has a very little diameter 4 mm, could the authors comment this aspect. Results with a pipe 2 diameter equal to 25 mm should be reported.
Response: I have discussed this problem in section VII, changing the diameters of the pipes is a way to changing the ratio of resistance of the two lines. By changing the ratio of the resistance of the two lines, it is able to regulate the ratio of flowrates of the two lines.
Comment:A further table with the pipes geometry information about HS system, figure 12, should be added, for a better comparison between them.
Response:pipe geometry information about improved zero-flowrate switching system is presented to help analysis impedance components like capacity, inductor and resistors. There are no impedance components in HS system, thus there is no reason to compare pipe geometry between the two systems.
Comment: Figure 19. y-axis requires the title and unit.
Response: y-axis is switching power loss which is already marked in the figure. The unit has already been added.
Comment: Figure 17. Why the flow rate through the line Q1 is equal zero but the displacement of the cylinder is not constant. It is not possible, or give an explanation. In HS system there is only the line Q1. As a matter of in figure 15 the cylinder displacement is constant when the flow rate Q1 is zero.
Response: yes, the displacement of the cylinder becomes constant at 1s when command signal becomes zero, as you can understand. But ‘1s’ for ‘displacement’is not in the same position as the ‘command’ and ‘flowrate’. The figure has been improved and the problem has been removed.
Comment: The authors should give more details about the computation of the switching power loss, presenting the pressure drop and flow rate in the section considered.
Response: I have added statement in VI paragraph 1: “Switching power losses of each valve have been calculated as the production of the pressure drop and flowrates of the valves. total switching power losses is also accumulated.”
Round 2
Reviewer 2 Report
Comments and Suggestions for AuthorsThe authors have implemented all the suggestions.