Optimization and Simulation of Permanent Magnet Motors
A special issue of Energies (ISSN 1996-1073). This special issue belongs to the section "F: Electrical Engineering".
Deadline for manuscript submissions: closed (10 May 2022) | Viewed by 7198
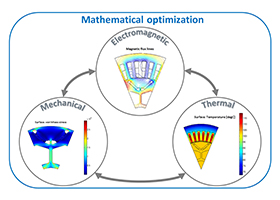
Special Issue Editors
Interests: electric machines and drives for power systems, electromobility, aerospace and general industrial applications; design, simulation and optimization of electric machines and power transformers
Special Issues, Collections and Topics in MDPI journals
Interests: electrical machines and drives; transportation electrification; renewable energies
Special Issues, Collections and Topics in MDPI journals
Special Issue Information
Dear Colleagues,
Electric machines are the main workhorses of our modern world. Among them, permanent magnet (PM) machines have reserved a special place for applications where high efficiency combined with high torque density and reduced size and weight are important. High-performance applications often require the electric machine to fulfill several conflicting requirements, thus pushing its design electromagnetically, thermally, and mechanically to the edge of feasibility. In such cases, machine designers face a serious challenge and need to resort to reliable multiphysical models combined with mathematical optimization as an automated decision-making tool.
This Special Issue focuses on simulation and optimization of permanent magnet machines used as a design tool. The specific topics of interest include (but are not limited to) the following:
- Analytical, semi-analytical, and numerical models;
- Electromagnetic, thermal, mechanical, and multiphysical models;
- Advanced iron loss and winding loss models;
- Simulation model tuning based on testbench measured data;
- Deterministic, heuristic or meta-model based single-objective and multiobjective optimization of PM machines;
- Reduction of computation efforts in optimization of PM machines using time-efficient preparation and solving of machine models and/or parallelization of the optimization tasks;
- Introduction of improved or novel optimization methods applied to PM machine design;
- Application-targeted (aerospace, traction, high-speed, etc.) simulation and optimization.
Prof. Dr. Damir Žarko
Prof. Dr. Ayman EL-Refaie
Guest Editors
Manuscript Submission Information
Manuscripts should be submitted online at www.mdpi.com by registering and logging in to this website. Once you are registered, click here to go to the submission form. Manuscripts can be submitted until the deadline. All submissions that pass pre-check are peer-reviewed. Accepted papers will be published continuously in the journal (as soon as accepted) and will be listed together on the special issue website. Research articles, review articles as well as short communications are invited. For planned papers, a title and short abstract (about 100 words) can be sent to the Editorial Office for announcement on this website.
Submitted manuscripts should not have been published previously, nor be under consideration for publication elsewhere (except conference proceedings papers). All manuscripts are thoroughly refereed through a single-blind peer-review process. A guide for authors and other relevant information for submission of manuscripts is available on the Instructions for Authors page. Energies is an international peer-reviewed open access semimonthly journal published by MDPI.
Please visit the Instructions for Authors page before submitting a manuscript. The Article Processing Charge (APC) for publication in this open access journal is 2600 CHF (Swiss Francs). Submitted papers should be well formatted and use good English. Authors may use MDPI's English editing service prior to publication or during author revisions.
Keywords
- Permanent magnet machines
- Modeling
- Multiphysics
- Heuristic optimization
- Meta-model based optimization
- Single- and multiobjective optimization
- Parallel computing in optimization
- Computation time minimization