Digitalized Industrial Production Systems and Industry 4.0
A special issue of Processes (ISSN 2227-9717). This special issue belongs to the section "AI-Enabled Process Engineering".
Deadline for manuscript submissions: closed (15 November 2021) | Viewed by 67197
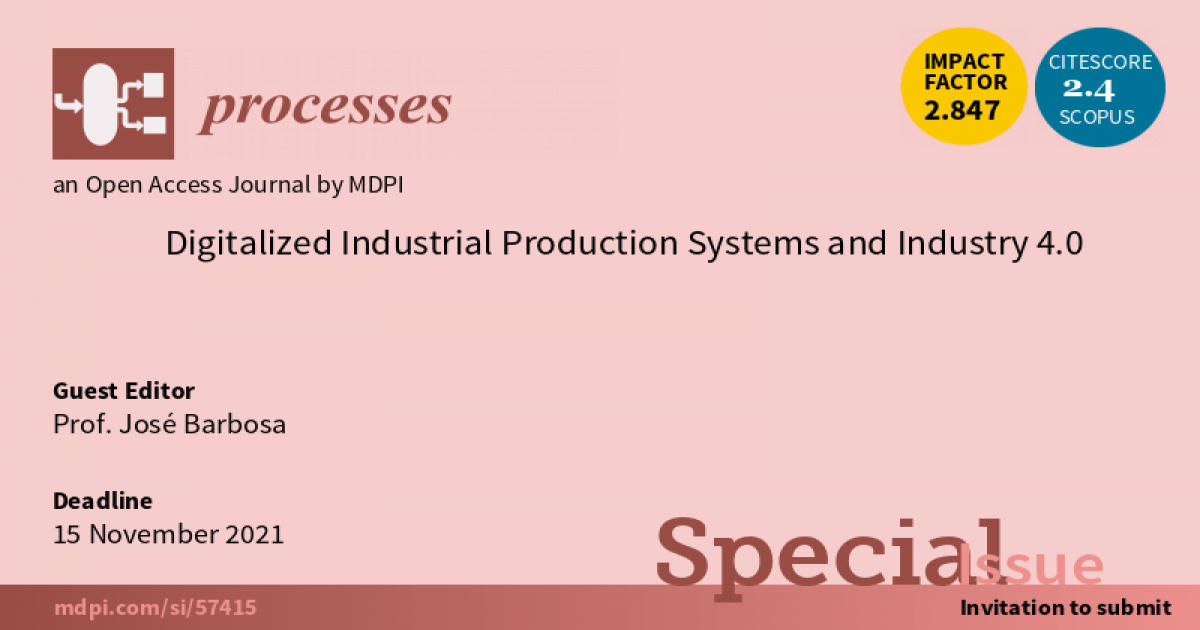
Special Issue Editor
Interests: cyber-physical systems; internet of things; multi-agent systems; holonic manufacturing systems; self-organization
Special Issues, Collections and Topics in MDPI journals
Special Issue Information
Dear Colleagues,
We are currently running a Special Issue entitled “Digitalized Industrial Production Systems and Industry 4.0”, to be published in the open access journal Processes. The submission deadline is 15 May 2021, and papers may be submitted immediately or at any point until this deadline as papers will be published on an ongoing basis.
The present Special Issue aims to present up-to-date information on the recent scientific advances in the digitalization of industrial production systems and in the application of industry 4.0 concepts. Real applications of the present topics are highly encouraged, as they would greatly inspire future application of innovative research.
Papers dealing with the following topics are especially sought (although the Special Issue is not strictly limited to these):
- Industrial CPS and smart manufacturing
- Architecture design and analysis
- Industrial IoT and factory of things and internet of things
- Modeling and control for cyber-physical systems
- Edge computing, fog computing, and IoT/IoE
- Machine-to-machine (M2M)/device-to-device communications and IoT/IoE
- Cloud-IoT/IoE cyber-physical systems
- Cyber-physical system architectures
- Human factors and humans in the loop in CPS
- The role of CPS in industry 4.0
- The role of IoT in industry 4.0
- The role of industrial agents in industry 4.0
- Design methodology, middlewares, principles, infrastructures, and tools for IIoT
- Application of CPS in smart domains (e.g., manufacturing, agriculture, building, etc.)
- Industrial applications of multi-agent systems
- Industrial agents in industry
Prof. José Barbosa
Guest Editor
Manuscript Submission Information
Manuscripts should be submitted online at www.mdpi.com by registering and logging in to this website. Once you are registered, click here to go to the submission form. Manuscripts can be submitted until the deadline. All submissions that pass pre-check are peer-reviewed. Accepted papers will be published continuously in the journal (as soon as accepted) and will be listed together on the special issue website. Research articles, review articles as well as short communications are invited. For planned papers, a title and short abstract (about 100 words) can be sent to the Editorial Office for announcement on this website.
Submitted manuscripts should not have been published previously, nor be under consideration for publication elsewhere (except conference proceedings papers). All manuscripts are thoroughly refereed through a single-blind peer-review process. A guide for authors and other relevant information for submission of manuscripts is available on the Instructions for Authors page. Processes is an international peer-reviewed open access monthly journal published by MDPI.
Please visit the Instructions for Authors page before submitting a manuscript. The Article Processing Charge (APC) for publication in this open access journal is 2400 CHF (Swiss Francs). Submitted papers should be well formatted and use good English. Authors may use MDPI's English editing service prior to publication or during author revisions.
Keywords
- digitalization
- industry 4.0
- internet of things
- cyber-physical systems
- multi-agent systems
- digital twins
Benefits of Publishing in a Special Issue
- Ease of navigation: Grouping papers by topic helps scholars navigate broad scope journals more efficiently.
- Greater discoverability: Special Issues support the reach and impact of scientific research. Articles in Special Issues are more discoverable and cited more frequently.
- Expansion of research network: Special Issues facilitate connections among authors, fostering scientific collaborations.
- External promotion: Articles in Special Issues are often promoted through the journal's social media, increasing their visibility.
- e-Book format: Special Issues with more than 10 articles can be published as dedicated e-books, ensuring wide and rapid dissemination.
Further information on MDPI's Special Issue policies can be found here.