Topic Menu
► Topic MenuTopic Editors

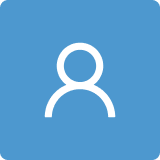
Research on the Mechanical Wear of Gear-Shaped Parts
Topic Information
Dear Colleagues,
Gear-shaped parts are widely used in industries for the purpose of sealing, power transmission, etc. They are usually in direct contact with paired gears to perform their functionalities, and surface wear due to the interaction of micro-contact of rough sliding surfaces is one of several failure modes. Apart from the direct material loss that leads to the functional failure, the wear causes the system to change its vibration and noise characteristics and consequently accelerates the occurrence of other failure modes.
At present, contemporary wear theories make it possible to build a relatively accurate model to assess the wear state of a surface, and the wear measurement techniques are capable of displaying the surface topographies at an enlarged scale. However, the in-depth wear mechanism of gear-shaped parts bridging the manufacturing process, molecular details, and macroscale properties of materials remains unclear. A good understanding of the wear mechanism and the monitoring and evaluation method is desired for the strength enhancement of gear-shaped parts and elongation of gear-like systems.
This Topic aims to provide a premier international platform for professionals to discuss and present their most recent research on the mechanical wear of gear-shaped parts. The articles in this Topic will cover various topics, including surface modification, lubrication, and tribology; anti-friction design; wear and wear evaluation; and fault diagnosis or damage detection of gears. Submissions on other topics are also welcomed.
Prof. Dr. Qingbing Dong
Prof. Dr. Zhibo Yang
Topic Editors
Keywords
- gear-shaped parts
- surface evolution
- wear detection
- tribology and lubrication
- fracture and fatigue
- fault diagnosis
Participating Journals
Journal Name | Impact Factor | CiteScore | Launched Year | First Decision (median) | APC |
---|---|---|---|---|---|
![]()
Applied Sciences
|
2.5 | 5.3 | 2011 | 18.4 Days | CHF 2400 |
![]()
Machines
|
2.1 | 3.0 | 2013 | 15.5 Days | CHF 2400 |
![]()
Materials
|
3.1 | 5.8 | 2008 | 13.9 Days | CHF 2600 |
Preprints.org is a multidisciplinary platform offering a preprint service designed to facilitate the early sharing of your research. It supports and empowers your research journey from the very beginning.
MDPI Topics is collaborating with Preprints.org and has established a direct connection between MDPI journals and the platform. Authors are encouraged to take advantage of this opportunity by posting their preprints at Preprints.org prior to publication:
- Share your research immediately: disseminate your ideas prior to publication and establish priority for your work.
- Safeguard your intellectual contribution: Protect your ideas with a time-stamped preprint that serves as proof of your research timeline.
- Boost visibility and impact: Increase the reach and influence of your research by making it accessible to a global audience.
- Gain early feedback: Receive valuable input and insights from peers before submitting to a journal.
- Ensure broad indexing: Web of Science (Preprint Citation Index), Google Scholar, Crossref, SHARE, PrePubMed, Scilit and Europe PMC.