Recent Advances in Fatigue and Fracture of Engineering Materials
A special issue of Applied Sciences (ISSN 2076-3417). This special issue belongs to the section "Materials Science and Engineering".
Deadline for manuscript submissions: 31 October 2024 | Viewed by 2803
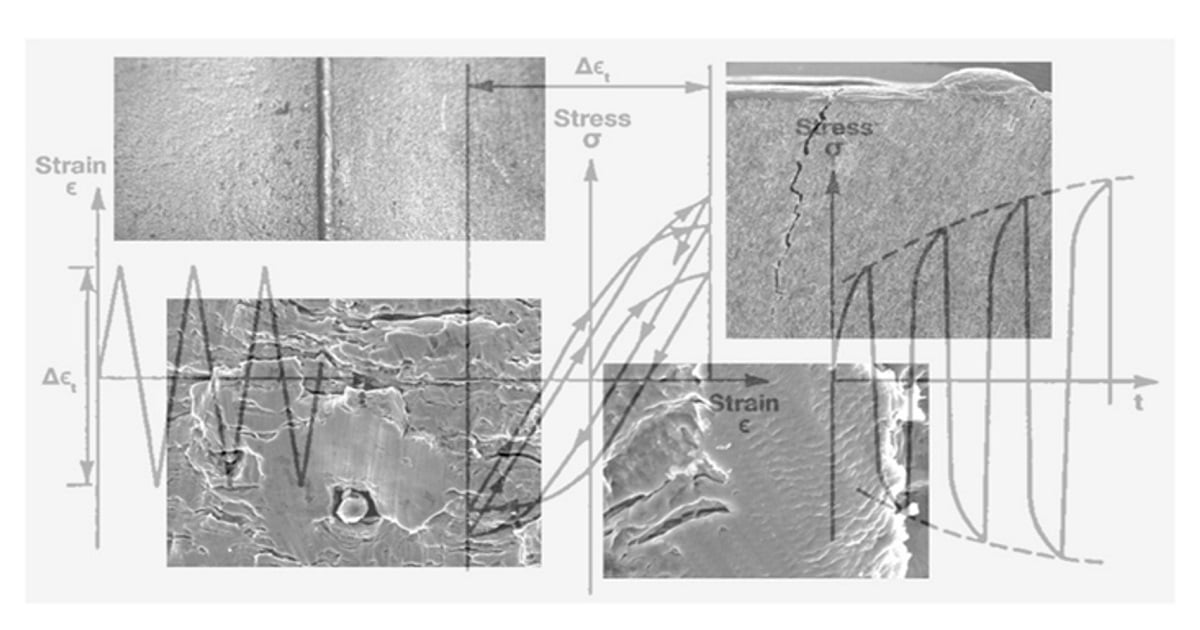
Special Issue Editors
Interests: mechanical engineering; mechanical properties; fracture mechanics; mechanical behavior of materials; microstructure; mechanical testing; failure analysis; construction; metals; fracture
Interests: friction stir welding; aluminum alloys; mechanical behavior of materials; microstructure; fatigue
Special Issues, Collections and Topics in MDPI journals
Interests: laser beam welding; hybrid laser arc welding; additive manufacturing; mechanical behavior of materials
Special Issues, Collections and Topics in MDPI journals
Special Issue Information
Dear Colleagues,
Fatigue properties are crucial in a wide range of structural materials utilized in civil engineering, automotive, energy industry, aeronautics and amon many others. Current trends and challenges in design require the development of new materials and wide knowledge about their properties. Metals, their alloys and more and more often composites are used due to their specific mechanical properties, useful especially in the conditions of fatigue loads. Fatigue and fracture of engineering materials have a complex nature and their course depend on various factors such as material state, loading conditions, environment and their combinations.
The aim of this Special Issue is to collect and share with a wide community of researchers the results of scientific research, addressing the recent advances in fatigue and fracture of materials. It will cover a wide range of topics including: the phenomena accompanying the process of crack initiation and propagation, the influence of different factors on fatigue life, development of approaches in fatigue life estimation, description of failure mechanisms, description and analysis of fracture surfaces, the influence of residual stresses on cracking, effect of microstructure, texture, and grain boundaries on fatigue life, and others.
Thus, we invite the researchers working in the described area to present their latest results in the form of original research and review articles. Papers that present experimental results are highly appreciated, as well as those that focus on numerical techniques for fatigue life assessment.
Dr. Tomasz Ślęzak
Dr. Robert Kosturek
Dr. Krzysztof Grzelak
Guest Editors
Manuscript Submission Information
Manuscripts should be submitted online at www.mdpi.com by registering and logging in to this website. Once you are registered, click here to go to the submission form. Manuscripts can be submitted until the deadline. All submissions that pass pre-check are peer-reviewed. Accepted papers will be published continuously in the journal (as soon as accepted) and will be listed together on the special issue website. Research articles, review articles as well as short communications are invited. For planned papers, a title and short abstract (about 100 words) can be sent to the Editorial Office for announcement on this website.
Submitted manuscripts should not have been published previously, nor be under consideration for publication elsewhere (except conference proceedings papers). All manuscripts are thoroughly refereed through a single-blind peer-review process. A guide for authors and other relevant information for submission of manuscripts is available on the Instructions for Authors page. Applied Sciences is an international peer-reviewed open access semimonthly journal published by MDPI.
Please visit the Instructions for Authors page before submitting a manuscript. The Article Processing Charge (APC) for publication in this open access journal is 2400 CHF (Swiss Francs). Submitted papers should be well formatted and use good English. Authors may use MDPI's English editing service prior to publication or during author revisions.
Keywords
- metals
- composite materials
- mechanical properties
- fatigue behaviour
- failure mechanisms description
- fatigue life prediction
- residual stresses
- fracture analysis
Benefits of Publishing in a Special Issue
- Ease of navigation: Grouping papers by topic helps scholars navigate broad scope journals more efficiently.
- Greater discoverability: Special Issues support the reach and impact of scientific research. Articles in Special Issues are more discoverable and cited more frequently.
- Expansion of research network: Special Issues facilitate connections among authors, fostering scientific collaborations.
- External promotion: Articles in Special Issues are often promoted through the journal's social media, increasing their visibility.
- e-Book format: Special Issues with more than 10 articles can be published as dedicated e-books, ensuring wide and rapid dissemination.
Further information on MDPI's Special Issue polices can be found here.