Friction and Wear Behaviors in Mechanical Engineering
A special issue of Coatings (ISSN 2079-6412). This special issue belongs to the section "Tribology".
Deadline for manuscript submissions: closed (30 April 2025) | Viewed by 16077
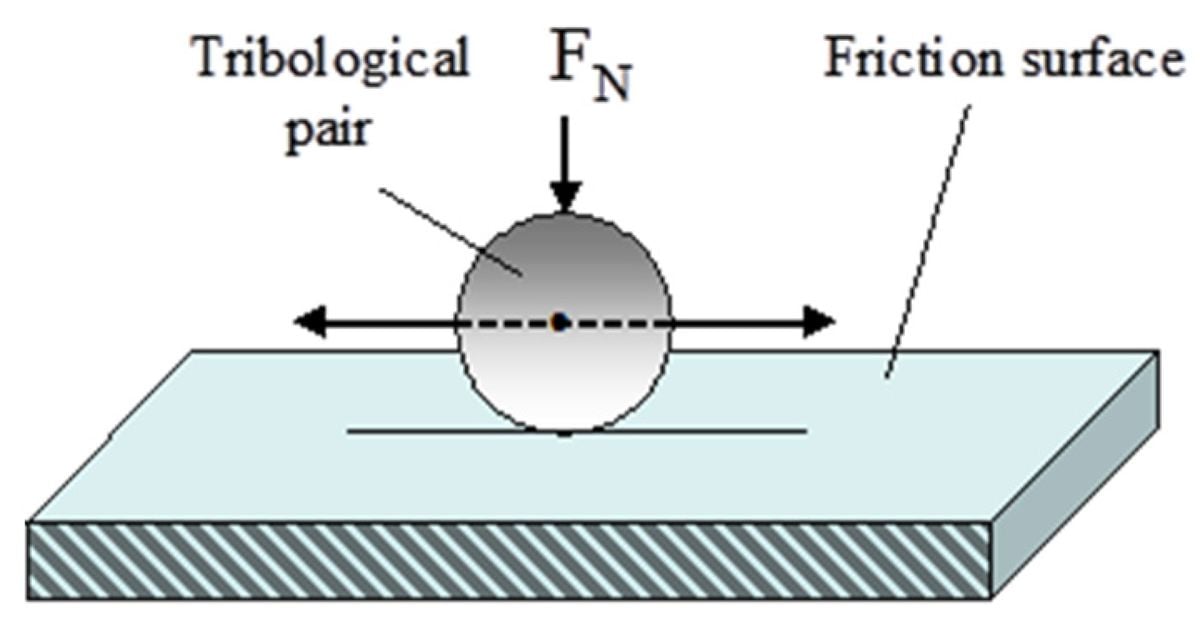
Special Issue Editors
Interests: green tribology; biotribology; nanoparticles in lubricants; biodegradable oils; monitoring of tribosystems
Special Issues, Collections and Topics in MDPI journals
Interests: friction and wear reducing coatings; green tribology materials; bio-degradable oils; nano-particles in lubricants; self-regulation in tribo systems
Special Issues, Collections and Topics in MDPI journals
Special Issue Information
Dear Colleagues,
We would like to invite you to submit your work for the Special Issue “Friction and Wear Behaviours in Mechanical Engineering”. The friction and wear problems in mechanical systems have always been particularly important, but recently, with the worsening of energy problems, the relevance of these issues has increased even more. When solving this question, special attention should be focused on the systematicity of the solution, i.e., analysis of the entire tribological system. We invite articles that deal with the properties of friction surfaces; their change using various technological methods, both when forming coatings and applying other surface modification methods; and tribological system lubrication. We also seek articles dedicated to the loss of and increase in tribological system efficiency, mechanisms of surface wear and degradation, and the monitoring of tribological systems. The most important highlights of this publication are new and combined surface coating and processing methods; self-lubricating coatings; tribological properties of lubricants; their improvement and assessment of changes in properties during the operation; green, i.e., environmentally friendly technologies; and biodegradable lubricants. We welcome contributions that evaluate not only the friction and wear parameters of the tribological system, but also friction mechanisms, surface degradation processes, and environmentally friendly materials (i.e., bioscale and structural and lubricating materials made from renewable materials).
Most of the articles in the Special Issue will consist of published reports of the international conference BALTTRIB'2022 (www.balttrib.info).
The topics of interest include, but are not limited to, the following:
- New and combined methods of coating formation and surface modification;
- Influence of surface treatment on its wear and degradation mechanisms and intensity;
- Structural and lubricating materials of biological origin;
- Self-lubrication coatings and self-regulation processes in friction pairs;
- Green surface treatment technologies;
- Green tribology.
Prof. Dr. Juozas Padgurskas
Dr. Raimundas Rukuiža
Guest Editors
Manuscript Submission Information
Manuscripts should be submitted online at www.mdpi.com by registering and logging in to this website. Once you are registered, click here to go to the submission form. Manuscripts can be submitted until the deadline. All submissions that pass pre-check are peer-reviewed. Accepted papers will be published continuously in the journal (as soon as accepted) and will be listed together on the special issue website. Research articles, review articles as well as short communications are invited. For planned papers, a title and short abstract (about 100 words) can be sent to the Editorial Office for announcement on this website.
Submitted manuscripts should not have been published previously, nor be under consideration for publication elsewhere (except conference proceedings papers). All manuscripts are thoroughly refereed through a single-blind peer-review process. A guide for authors and other relevant information for submission of manuscripts is available on the Instructions for Authors page. Coatings is an international peer-reviewed open access monthly journal published by MDPI.
Please visit the Instructions for Authors page before submitting a manuscript. The Article Processing Charge (APC) for publication in this open access journal is 2600 CHF (Swiss Francs). Submitted papers should be well formatted and use good English. Authors may use MDPI's English editing service prior to publication or during author revisions.
Keywords
- surface modification
- tribosystem
- friction and wear mechanisms
- biolubricants
- biodegradable materials
- green tribology
Benefits of Publishing in a Special Issue
- Ease of navigation: Grouping papers by topic helps scholars navigate broad scope journals more efficiently.
- Greater discoverability: Special Issues support the reach and impact of scientific research. Articles in Special Issues are more discoverable and cited more frequently.
- Expansion of research network: Special Issues facilitate connections among authors, fostering scientific collaborations.
- External promotion: Articles in Special Issues are often promoted through the journal's social media, increasing their visibility.
- e-Book format: Special Issues with more than 10 articles can be published as dedicated e-books, ensuring wide and rapid dissemination.
Further information on MDPI's Special Issue policies can be found here.