Acoustic and Mechanical Metamaterials: Recent Advances
A special issue of Materials (ISSN 1996-1944). This special issue belongs to the section "Mechanics of Materials".
Deadline for manuscript submissions: closed (20 February 2025) | Viewed by 15090
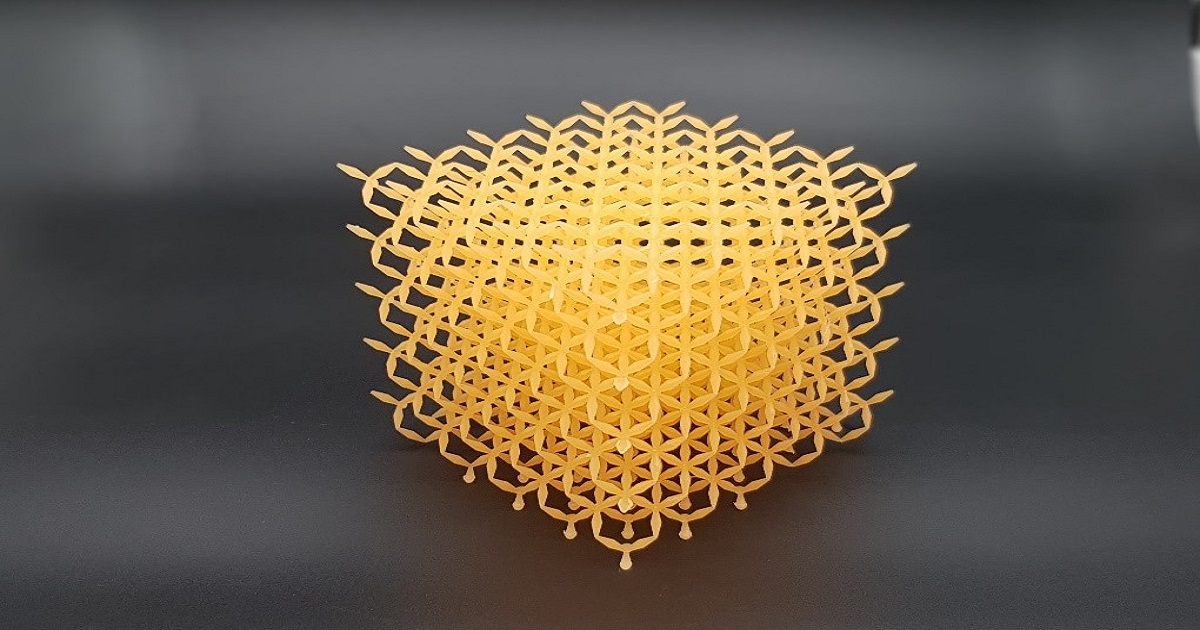
Special Issue Editor
Interests: mechanical properties; mechanical behavior of materials; mechanical testing; mechanics of materials; finite element analysis; acoustics; solid mechanics; finite element modeling; biomechanics; biomaterials
Special Issues, Collections and Topics in MDPI journals
Special Issue Information
Dear Colleagues,
Metamaterials, artificially architectured materials with abnormal physical and mechanical properties, have recently been gaining momentum in research and industrial applications. This is because recent advances in advanced manufacturing technologies, such as additive manufacturing, have made fabricating these intricate materials feasible. It is well known that acoustic metamaterials are usually designed to effectively manipulate acoustic waves. On the other hand, mechanical metamaterials are used not only for their mechanical aspects such as auxeticity, shape morphing, and energy absorption, but in many cases, they are used for their excellent capability to manipulate acoustic wavs. This is why there is a relatively broad overlap of research in the fields of acoustic and mechanical metamaterials.
In this Special Issue, we aim to explore the latest advances in the design and manufacture of acoustic and mechanical metamaterials.
This Special Issue welcomes original research papers and review articles covering all relevant topics, including but not limited to:
- Pentamodes;
- Double-negative acoustic metamaterial;
- Auxetic metamaterials;
- Cosserat metamaterials;
- Split-ring resonators;
- Phononic crystals;
- Superlenses;
- Metamaterials with negative compressibility;
- Willis materials.
Dr. Reza Hedayati
Guest Editor
Manuscript Submission Information
Manuscripts should be submitted online at www.mdpi.com by registering and logging in to this website. Once you are registered, click here to go to the submission form. Manuscripts can be submitted until the deadline. All submissions that pass pre-check are peer-reviewed. Accepted papers will be published continuously in the journal (as soon as accepted) and will be listed together on the special issue website. Research articles, review articles as well as short communications are invited. For planned papers, a title and short abstract (about 100 words) can be sent to the Editorial Office for announcement on this website.
Submitted manuscripts should not have been published previously, nor be under consideration for publication elsewhere (except conference proceedings papers). All manuscripts are thoroughly refereed through a single-blind peer-review process. A guide for authors and other relevant information for submission of manuscripts is available on the Instructions for Authors page. Materials is an international peer-reviewed open access semimonthly journal published by MDPI.
Please visit the Instructions for Authors page before submitting a manuscript. The Article Processing Charge (APC) for publication in this open access journal is 2600 CHF (Swiss Francs). Submitted papers should be well formatted and use good English. Authors may use MDPI's English editing service prior to publication or during author revisions.
Keywords
- acoustic metamaterial
- mechanical metamaterials
- auxetics
- resonators
- pentamodes
Benefits of Publishing in a Special Issue
- Ease of navigation: Grouping papers by topic helps scholars navigate broad scope journals more efficiently.
- Greater discoverability: Special Issues support the reach and impact of scientific research. Articles in Special Issues are more discoverable and cited more frequently.
- Expansion of research network: Special Issues facilitate connections among authors, fostering scientific collaborations.
- External promotion: Articles in Special Issues are often promoted through the journal's social media, increasing their visibility.
- e-Book format: Special Issues with more than 10 articles can be published as dedicated e-books, ensuring wide and rapid dissemination.
Further information on MDPI's Special Issue policies can be found here.