Applications of Electrical Machines in Modern Electric Vehicles: Current Developments and Future Perspectives
A special issue of Energies (ISSN 1996-1073). This special issue belongs to the section "E: Electric Vehicles".
Deadline for manuscript submissions: closed (26 April 2022) | Viewed by 16200
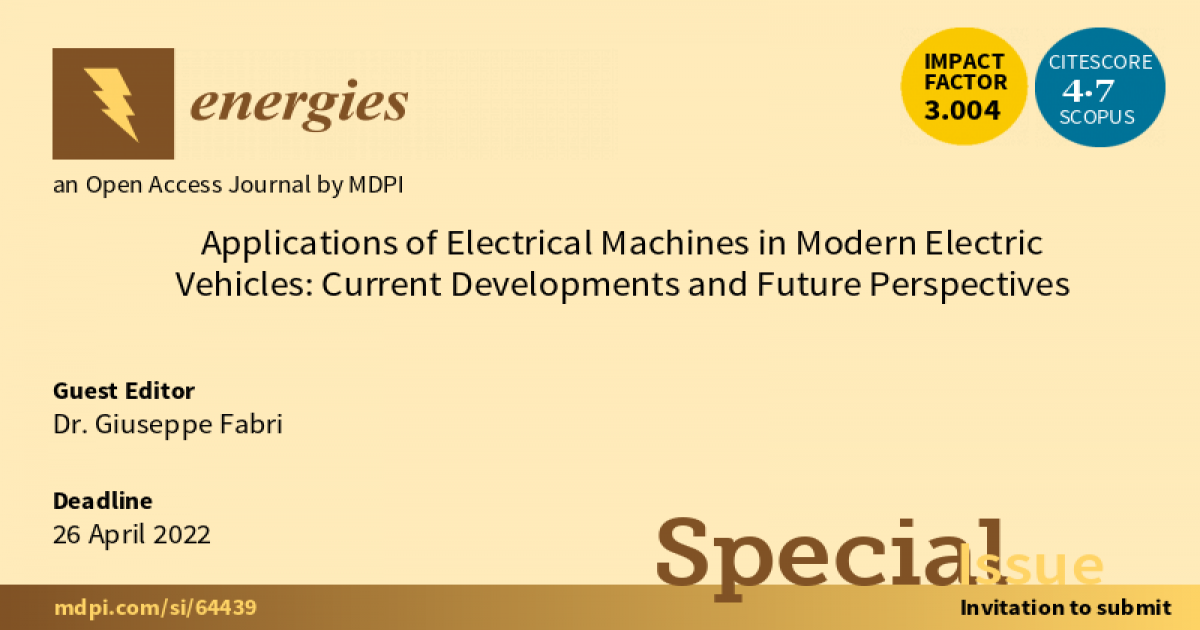
Special Issue Editor
Interests: electrical machines; electrical drives; reluctance motors; machine control; permanent magnet motors; induction motors; automotive; aerospace
Special Issue Information
Dear Colleagues,
Electrical machines are the key technology in the forthcoming revolution of the transportation system, and the electric powertrain remains the final energy user and is responsible for vehicle performance and efficiency.
Modern EV powertrains are complex systems where the electrical machine is highly integrated with power electronics, transmission, and cooling systems, and where the control algorithm is essential to exploit the performance of the powertrain in terms of handling, acceleration capabilities, and efficiency. Vehicle level requirements and characteristics need to be accurately investigated and broken down to powertrain and e-drive specifications in motoring and braking mode operations.
High-speed machines are being investigated to enhance the specific power of the powertrain, mainly where critical raw material such as rare earths are avoided due to costs and supply chain concerns. Design for high speed requires specific design steps and demands for high strength materials (electrical steels) and high-frequency operations in power converters.
In this scope, the topics of interest for this Special Issue, but are not limited to:
- Electrical machine design and control for EV application
- Powertrain integration and high speed operations
- Electrical machine cooling aspects
- Electric motor with reduced critical materials
- New materials for electrical machines
- Application of multiphase motors in EV
- Electrical machines under regenerative braking operation
- Designing for mass production
Guest Editor
Manuscript Submission Information
Manuscripts should be submitted online at www.mdpi.com by registering and logging in to this website. Once you are registered, click here to go to the submission form. Manuscripts can be submitted until the deadline. All submissions that pass pre-check are peer-reviewed. Accepted papers will be published continuously in the journal (as soon as accepted) and will be listed together on the special issue website. Research articles, review articles as well as short communications are invited. For planned papers, a title and short abstract (about 100 words) can be sent to the Editorial Office for announcement on this website.
Submitted manuscripts should not have been published previously, nor be under consideration for publication elsewhere (except conference proceedings papers). All manuscripts are thoroughly refereed through a single-blind peer-review process. A guide for authors and other relevant information for submission of manuscripts is available on the Instructions for Authors page. Energies is an international peer-reviewed open access semimonthly journal published by MDPI.
Please visit the Instructions for Authors page before submitting a manuscript. The Article Processing Charge (APC) for publication in this open access journal is 2600 CHF (Swiss Francs). Submitted papers should be well formatted and use good English. Authors may use MDPI's English editing service prior to publication or during author revisions.
Keywords
- electric vehicles
- electrical machines
- electrical drives
- electric powertrain
- motor cooling
- mass production
- reduced rare earth
- regenerative braking