Special Issue of the Manufacturing Engineering Society 2019 (SIMES-2019)
A special issue of Applied Sciences (ISSN 2076-3417).
Deadline for manuscript submissions: closed (30 November 2019) | Viewed by 53603
Special Issue Editors
Interests: machining; lightweight materials (magnesium alloys, aluminum alloys, titanium alloys); metal forming technology and processing; sustainable manufacturing; industrial metrology; virtual reality; virtual labs; e-learning; innovation in distance teaching
Special Issues, Collections and Topics in MDPI journals
Interests: metal forming (lightweight alloys, advanced high strength steels); additive manufacturing; fused deposition modeling; WAAM; finite element simulation; methodologies for materials selection in manufacturing; virtual labs
Special Issues, Collections and Topics in MDPI journals
Special Issue Information
Dear Colleagues,
Due to the success of the first Special Edition, and encouraged by the Manufacturing Engineering Society (MES), a new Special Edition called “The Special Issue of the Manufacturing Engineering Society 2019 (SIMES-2019)” is launched as a joint issue of the journals Materials and Applied Sciences.
The first edition collected 48 contributions on emerging methods and technologies, such as those related to additive manufacturing and 3D printing, advances and innovations in manufacturing processes in different areas (machining, forming, molding, welding, and nontraditional manufacturing processes), manufacturing systems (machines, equipment and tooling), metrology and quality in manufacturing, product lifecycle management (PLM) technologies, and risks in manufacturing engineering and society.
This second edition involves the aforementioned journals with the aim of covering the wide range of research lines developed by the members and collaborators of the MES and other researchers within the field of Manufacturing Engineering.
Similarly to the first one, the main objective of “The Special Issue of the Manufacturing Engineering Society 2019” is to publish outstanding papers presenting cutting-edge advances in the field of Manufacturing Engineering, focusing on materials processing, as well as on experimental and theoretical results within applied sciences.
The Special Issue aims to explore the evolution of traditional manufacturing models towards the new requirements of the Manufacturing Industry 4.0 and how manufacturing professionals should face the resulting competitive challenges in the context of an ever-increasing use of digital information systems and communication technologies.
Contributions on emerging methods and technologies such as those related to additive manufacturing will have special relevance within this Special Issue, as well as those ones where sustainability and environmental issues play a fundamental role in manufacturing.
The main topics covered by this Special Issue are scientific contributions on the following manufacturing research topics:
- Additive manufacturing and 3D printing
- Advances and innovations in manufacturing processes
- Sustainable and green manufacturing
- Micro and nanomanufacturing
- Manufacturing of new materials
- Manufacturing systems: machines, equipment and tooling
- Robotics, mechatronics and manufacturing automation
- Metrology and quality in manufacturing
- Industry 4.0
- Product lifecycle management (PLM) technologies
- Design, modeling, and simulation in manufacturing engineering
- Production planning
- Manufacturing engineering and society
The above list is not exhaustive, and papers on other topics associated with advances in manufacturing engineering are also welcome.
Excellent papers selected from the Manufacturing Engineering Society International Conference 2019 can also be part of this Special Issue, provided that the degree of novelty of the contribution is guaranteed and the paper has been not published elsewhere.
Especially welcome are all the works with a clear application to the manufacturing field related to nanotechnology and applied nanoscience; optics and lasers; energy savings in manufacturing systems and processes; mechanical engineering; computer science and manufacturing engineering; applied biosciences and bioengineering; applied industrial technologies.
It is our pleasure to invite professionals from Industry, Academic Institutions and Research Centers from around the world to submit their contributions to this Special Issue.
We hope this second edition of the Special Issue is as successful as the first one.
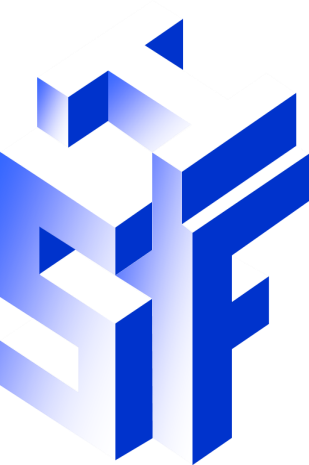
You may choose our Joint Special Issue in Materials.
Prof. Eva M. Rubio
Prof. Ana M. Camacho
Guest Editors
- Members of the Manufacturing Engineering Society will benefit from a 15% discount (approx. 200 €) on the article processing charges. If you are not a member yet, please find more information on how to join the society (here). Regular individual member fee 75 €/year, student fee 35 €/year.
Manuscript Submission Information
Manuscripts should be submitted online at www.mdpi.com by registering and logging in to this website. Once you are registered, click here to go to the submission form. Manuscripts can be submitted until the deadline. All submissions that pass pre-check are peer-reviewed. Accepted papers will be published continuously in the journal (as soon as accepted) and will be listed together on the special issue website. Research articles, review articles as well as short communications are invited. For planned papers, a title and short abstract (about 100 words) can be sent to the Editorial Office for announcement on this website.
Submitted manuscripts should not have been published previously, nor be under consideration for publication elsewhere (except conference proceedings papers). All manuscripts are thoroughly refereed through a single-blind peer-review process. A guide for authors and other relevant information for submission of manuscripts is available on the Instructions for Authors page. Applied Sciences is an international peer-reviewed open access semimonthly journal published by MDPI.
Please visit the Instructions for Authors page before submitting a manuscript. The Article Processing Charge (APC) for publication in this open access journal is 2400 CHF (Swiss Francs). Submitted papers should be well formatted and use good English. Authors may use MDPI's English editing service prior to publication or during author revisions.
Keywords
- 3D printing
- Additive manufacturing
- Assembly processes
- Bioengineering
- Computer science
- Digital manufacturing
- Energy savings
- Ergonomy
- Forming
- Friction
- Green manufacturing
- Industrial technologies
- Industry 4.0
- Joining
- Machining
- Manufacturing automation
- Manufacturing systems
- Mechatronics
- Metrology
- Micro-manufacturing
- Modeling and simulation
- Moulding
- Nano-manufacturing
- Non-traditional manufacturing processes
- Optics and lasers
- Processing of materials
- Product Lifecycle Management
- Production planning
- Quality in manufacturing
- Robotics
- Safety and risks
- Smart manufacturing
- Sustainable manufacturing
- Technological and Industrial Heritage
- Virtual manufacturing
- Wear
- Welding